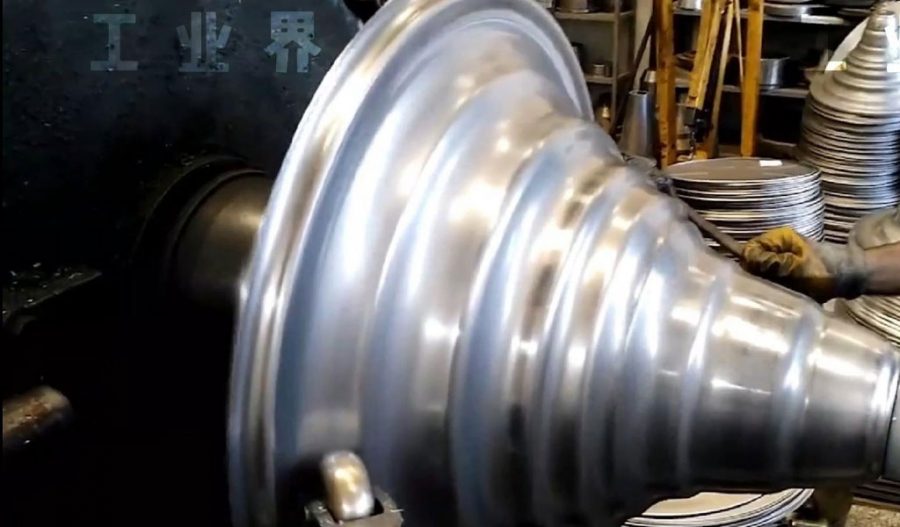
金属成形は、あらゆる工業プロセスに不可欠な要素です。コスト効率、機械的品質の向上、柔軟な操作、生産性の向上、材料の大幅な節約などの利点により、金属成形は多くの製造プロセスにおいて重要な工業コンポーネントとなっています。
- 原材料を最終製品に変えるには、さまざまな製造技術が使用されます。製造プロセスの例としては、鋳造、成形、成型、接続、コーティング、分割、機械加工、材料特性の変更などがあります。
- 成形は最も一般的な製造プロセスの 1 つであり、航空宇宙、自動車、防衛産業など、さまざまな分野で幅広く使用されています。
- バルクまたはシート成形プロセスは、鍛造材料の形状を作成するために使用されます。成形、成型、および鋳造は、鋳造品を作成するために使用されます。
- 自動車業界では、ホイールリム、ボディ、バルブ、シャーシフォーム(ロールまたはスタンプ)、オイルパンなどの部品の成形が一般的です。
- 私たちは毎日、鍋、フライパン、歯磨き粉のチューブ、自転車のフレーム、チェーン、チューブ継手、ファンブレードなど、数え切れないほど多くの形状の物体に遭遇します。
- 引張、圧縮、曲げ、せん断応力、またはこれらの組み合わせを使用して塑性変形を適用し、原材料を必要なサイズと形状に成形します。
分類の形成:
金属成形技術は通常、2 つの主要なカテゴリに分類されます。
バルク成形プロセス
金属成形には、板金成形とバルク成形の 2 種類があります。表面積と体積の比率が低い原材料を成形すると、バルク変形が発生します。バルク成形には、圧延、鍛造、押し出し、および引き抜きが含まれます。バルク変形処理手順では、圧縮、圧縮、引張、せん断、およびそれらの組み合わせなど、さまざまな力を利用できます。
成形プレスは、金型と一連のツールを使用してバルク成形を行います。バルク成形で製造されるアイテムには、ギア、ブッシュバルブ、およびコネクティングロッド、バルブ、油圧バルブなどのその他のエンジン部品が含まれます。
板金加工
板金鍛造では、張力とせん断力が最も一般的に使用されます。板金成形は、主にシート、プレート、ストリップの加工を指します。板金加工の大部分は、油圧または空気圧プレスを使用して行われます。板金加工手順では、ダイとパンチと呼ばれる一連の器具を使用します。多くの板金加工の中には、引き抜き、せん断、打ち抜き、打ち抜きなどがあります。
粉末金属成形
粉末成形と呼ばれる比較的新しいタイプの成形プロセスは、その独特の特性により、注目を集めています。材料の無駄を最小限に抑え、ほぼ最終寸法の部品を作成できることが、粉末成形の主な強みです。このプロセスは、ニアネットシェイプ成形と呼ばれています。材料の化学組成を調整して、特定の機械的特性を実現できます。従来の鍛造金属と比較すると、焼結金属は成形性に優れています。しかし、粉末成形では、気孔率をゼロまたはほぼゼロにすることが依然として大きな障害となっています。気孔のある部品は強度が低く、柔軟性が低く、耐腐食性も劣るため、想定寿命が切れる前に破損する可能性が高くなります。
金属成形方法はどのように分類されますか?
曲げ
この金属鍛造法は非常に適応性があります。ブレーキ プレスで最も一般的に行われますが、同様の装置でも行うことができます。金属シートは、ダイ ブロックの上に置いてパンチ プレスされます。ダイ成形では、シートに穴を開けるのではなく、金属に曲げ力を加えます。ダイの種類に応じて、曲げは、プレス ブレーキ、回転曲げ、ロール曲げなどのいくつかの手順にさらに分類できます。
ストレッチ
「ストレッチング」と呼ばれる金属加工プロセスの一環として、金型を使用して金属片を同時に曲げたり伸ばしたりします。これを使用すると、複雑な形状の金属部品を作成できます。また、正確な半径曲げを必要とする滑らかな表面を持つ大型の金属部品を成形するのにも最適です。
深絞り
金属を成形するもう 1 つの一般的な方法は、深絞りです。深絞りでは、空洞のある金属シートを金型に固定します。パンチダウンした後、穴を通して「引き抜かれます」(これが名前の由来です)。金属シートは金型に従って曲げられたり、カップや箱のように成形されます。細部にこだわった金属部品やデザインは、深絞りで作るのが最適です。
ロール成形
ロール成形形状は、多数のローラー セットで使用される金属部品です。ロール成形機は、金属片が通されるときに、複数のローラー ペアで金属片の表面を常に押し付けます。これらを使用して、金属を想像できるあらゆる形状に成形できます。ロール成形は、金属部品を徐々に成形して目的の断面に達するまで繰り返すプロセスです。大量生産に適しており、通常は長い部品の製造に使用されます。
押し出し
押し出しは、金属片を金型に押し込むという、異なる種類の金属成形です。この方法で、目的の断面が作られます。ただし、この技術は他の方法と似ています。押し出しでは、金属は金型に押し込まれる前に、十分に高温に加熱されて柔らかくなります。この温度まで加熱されると、金属は事実上液体になります。金型には穴が開いており、プレスされた高温の金属がそこを流れていきます。
金属トリミング
金属トリミングとは、主にワークピースの縁の周りの余分な材料を取り除くことです。成形プロセスの最後のステップとして、これは製品を最終的な形にするために不可欠です。
トリミングが使用される理由は何ですか?
トリミングが重要な製造工程である理由はいくつかあります。原材料に記載されている手順に加えて、このプロセスにより、最終製品の精度と品質が可能な限り最高レベルに保たれます。製品が設計どおりに作られるように、トリミングによって余分な材料が取り除かれます。このプロセスにより、最終製品の品質が向上します。
トリミングは、製品の有用性と寿命を向上させるだけでなく、弱い部分や故障の可能性のある場所を排除するためにも利用できます。トリミングにより、製品の美観が向上し、安全性が高まるだけでなく、作業もしやすくなります。
トリミングでは、すべての部品が同じであり、仕様に適合していることを保証する一貫性が重要であり、これは大量生産に不可欠です。そのため、トリミングは製造に大きな影響を与える重要なステップです。
トリミング作業の本質的な重要性
トリミング手順には多くの利点があるため、板金生産に不可欠な要素となっています。
一貫性と精度
製造の精度と一貫性の重要性は、いくら強調してもし過ぎることはありません。自動車、航空宇宙、医療機器業界は、要件から少しでも逸脱すると悲惨な結果を招く可能性があるため、特に注意が必要です。トリミング手順では、エラーの余地を排除することで、製造されるすべての部品が設計パラメータに正確に従うことを保証します。
外観と品質の向上
コンポーネントの機能性と美観は、その全体的な品質に影響します。コンポーネントは便利であっても、角が粗かったり、形状が不均一だったりするなど、目立った欠陥があると、品質が低い印象を与える可能性があります。トリミングにより、製品の見た目の魅力が高まり、購入者の品質評価に影響します。
金属仕上げ
金属の仕上げは生産の最終段階であり、環境を保護し、美しさを向上させます。接合または密封が必要な部品も、機械加工するには粗すぎる表面を滑らかにするために仕上げを使用すると効果的です。金属の洗浄、バリ取り、スケール除去などのプロセスも仕上げの一部です。簡単に言えば、多くの金属仕上げ手順には幅広い用途があります。この記事では、いくつかの重要な仕上げプロセスについて、その用途と金属仕上げ手順を選択する際に考慮すべき事項とともに説明します。
さまざまな金属仕上げ
仕上げ工程の例は以下のとおりです。
メッキ
基板は、化学薬品の浴を伴う金属めっきによって、亜鉛、カドミウム、ニッケル、クロムなどの金属の薄い層でコーティングまたは変更することができます。無電解めっきでは、電流を使用して基板を覆う電気めっきとは異なり、基板が反応を触媒する自己触媒技術を使用します。このプロセスは化学的に集約的で大規模に行われるため、めっきサービス プロバイダーが必要になることがよくあります。
金属メッキにより、製品の寿命、耐腐食性、表面摩擦、美観などを向上させることができます。亜鉛メッキは亜鉛メッキ金属の犠牲陽極として機能し、腐食しながら同時にその下の基板を保護します。ただし、ほとんどの場合、メッキ機は表面の欠陥を修正するための最適な選択肢ではありません。
ボルト、ワッシャー、その他の小さな鋼製部品は、シェラダイジング処理によって、腐食に強い亜鉛鉄合金でコーティングできます。亜鉛ダストコーティングを施すには、加熱されたドラム内で部品をタンブリングします。この仕上げは腐食に非常に強いです。バレル仕上げ機は、大規模な製造工程で迅速かつ効果的なコーティング オプションを提供します。
清掃/ブラッシング
ブラシを使用した金属仕上げは、メッキよりも表面の傷を取り除くのに効果的です。これらの仕上げ機は、木目のパターンをより均一かつ平行に見せ、製品をより磨き上げたように見せます。通常、この効果は研磨ベルトまたはワイヤー ブラシを使用して実現されます。木目に対して垂直に、ベルトまたはブラシを単独で向けると、エッジが多少丸くなります。金属写真印刷や看板に使用されるアルミニウム パネルは、この仕上げ処理を受けます。
洗浄前に金属表面を準備するには、ワイヤーブラシを使用してスケールや砂を取り除くこともできます。また、同じ方法を使用して、特定の溶接作業からスラグを取り除くこともできます。
メッキやコーティングの前に、化学薬品や酸の浴槽を利用して、成形、機械加工、その他の手順の後に残る油の残留物を除去します。
振動仕上げ
バリ取り、スプルー、鋭利なエッジ、その他の破片の除去は、振動仕上げ装置でよく行われます。研磨ペレットが入ったドラム内に部品を配置した後、タンブル振動を使用して均一でランダムなテクスチャを生成します。この機械は、サイクル速度と振動の強さが通常調整可能なため、非常に小さいものから大きいものまでさまざまなサイズのアイテムを効果的に処理できます。
爆破
一貫したマット仕上げが必要な場合、通常はサンドブラスト機やその他のブラスト装置が使用されます。サンドブラストはビーズブラストとも呼ばれ、砂、鋼鉄の弾丸、金属ペレット、またはこれらの組み合わせなどの研磨剤を表面に急速に吹き付けます。これにより、それほど硬くない金属でも磨かれた仕上がりになります。
疲労、応力腐食割れ、フレッティングなどに対する耐性の向上など、さまざまな金属表面処理に用いられるショットピーニングは、圧縮応力を与えるブラスト技術です。冷間加工技術では、製造中に表面が受ける引張応力に対する解毒剤として圧縮張力を適用します。疲労耐性のために圧縮応力を適用することは、冷間加工による表面改質の別の技術であるバニシングによっても実現できます。
結論
へら絞りの工程は、原材料から完成品に至るまで、高度で複雑な行程を網羅しており、対称的な金属部品を作成する際の高度な精度と効率を示しています。この詳細な調査では、曲げ、引き伸ばし、深絞り、押し出しなどのさまざまな方法による最初の成形から、トリミングや高度な金属仕上げ技術などの重要な仕上げまで、へら絞りの重要な段階に焦点を当てています。
各ステップは、最終製品の望ましい品質、機能性、美観を実現するために不可欠です。手作業のスキルと高度な PNC/CNC テクノロジーの両方によって実現される へら絞り の汎用性は、航空宇宙、自動車、防衛など、さまざまな分野で幅広い用途を提供します。
このブログは、へら絞りの包括的な段階と現代の製造業における重要な役割をより明確に理解できるようにすることで、プロセスの神秘性を解き明かし、より多くの専門家にその利点を検討してもらうことを目的としています。へら絞り製品に固有の適応性、費用対効果、優れた機械的特性は、この方法の価値を強調し、他の製造技術と比較して優れた選択肢となっています。
ツーリングとCNCの絞り加工能力を最大化する
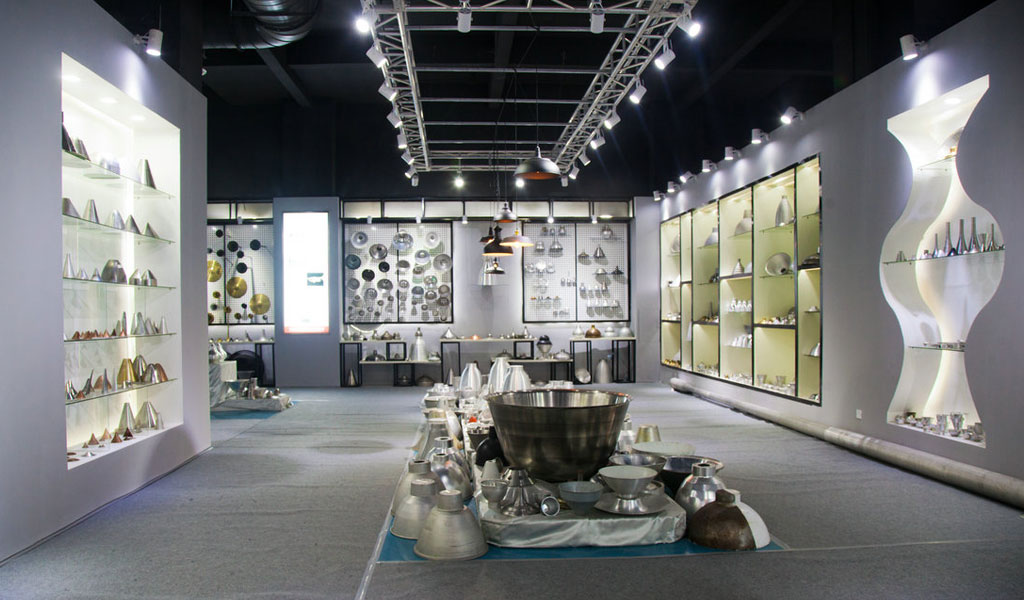
BE-CU 中華のへら 絞り 会社では、過度の摩耗やストレスの兆候を監視しながら、設備を最大限に活用しています。さらに、より新しい最新の設備を検討し、製造能力をサポートまたは向上できる設備に投資しています。当社のチームは機械やツールに細心の注意を払っているため、部品の品質と生産性に悪影響を与えないように定期的にメンテナンスも行っています。
BE-CUの設計とエンジニアリングサポート
BE-CUは、社内の設計およびエンジニアリングチームを活用して、部品生産の初期コンセプトからお客様を支援することができます(提供された設計に対して広範な設計サポートも提供可能です)。私たちのチームは、プロジェクトの開始から終了まで、お客様と定期的かつ透明なコミュニケーションを取りながら、望ましい最終目標に向かって作業を進め、明確な進行方向を提供します。
BE-CUの設計およびエンジニアリングサポートプロセスの一例:
- クライアントがBE-CUチームに部品図面を提供します。
- 当社のエンジニアリングチームが図面をレビューし、ベストプラクティスに基づいて調整を行います。お客様のニーズに応じて、成形または絞り部品を最も効果的に達成する方法を推奨します。
- 図面と設計は必要に応じて改訂され、完璧な形に仕上げられます。財務的な実行可能性も最優先事項として考慮されます。
- 主要な目標は、全ての部品の適合性、形状、機能性を実現することです。
- 研究開発は製造プロセスの重要なステップであり、BE-CUは概念実証や様々な検証要件のためにプロトタイピングサービスを提供しています。研究開発プロセスにおける金属成形については、当社のeBookをご覧ください。
BE-CUが提供する広範な社内サービス
この金属加工プロセスは、軸対称の高性能部品を製造します。スピン成形とも呼ばれ、材料を望ましい形状に切削するのではなく、金属ディスクまたはチューブを円錐形やその他の円形に変形させます。
へら絞りは、手動の手作業によるスピニングプロセスまたは自動CNCスピニングを使用します。BE-CUのへら絞り機能の利点には以下が含まれます:
- コスト削減
- 短いリードタイム
- 最大の設計柔軟性
- シームレスで高品質な構造
対応可能な金属には、ステンレス鋼、炭素鋼、アルミニウム、銅、インコネル、ハステロイ、チタン、ブロンズ、真鍮が含まれます。BE-CUは、センター間60インチから直径100インチまでのカスタム金属絞り部品を製造でき、材料の厚さは0.018インチから2.00インチまで対応可能です。
当社の CNC へら 絞り サービスで迅速なプロトタイプの作成について、今すぐお問い合わせください。こちらでチャットして直接見積もりを取得するか、無料のプロジェクトレビューをリクエストしてください。