へら 絞り と は
金属へら絞りは、スピンフォーミングとも呼ばれる金属加工技術で、平らな円形のブランクやディスク状の素材を、軸対称の丸い形状に変形させます。このプロセスは、ディスクブランクの表面に対して配置されたローラーによる横方向の力と、軸上で高速に回転するマンドレルの適用によって達成されます。マンドレルは、ワークピースを支持し、その最終形状を与える役割を果たします。
金属へら絞りのプロセスでは、円形の金属シートが変形され、ワークピースから材料を取り除くことなくさまざまな形状を作り出します。へら絞りの間、ディスクブランクは引張および圧縮力を受けながら、マンドレルの周りに包み込まれます。使用される金属へら絞りの種類に応じて、元の金属シートの厚さが減少する場合があります。この特性は、加工された金属が所定の仕様に達するように精密に制御されます。
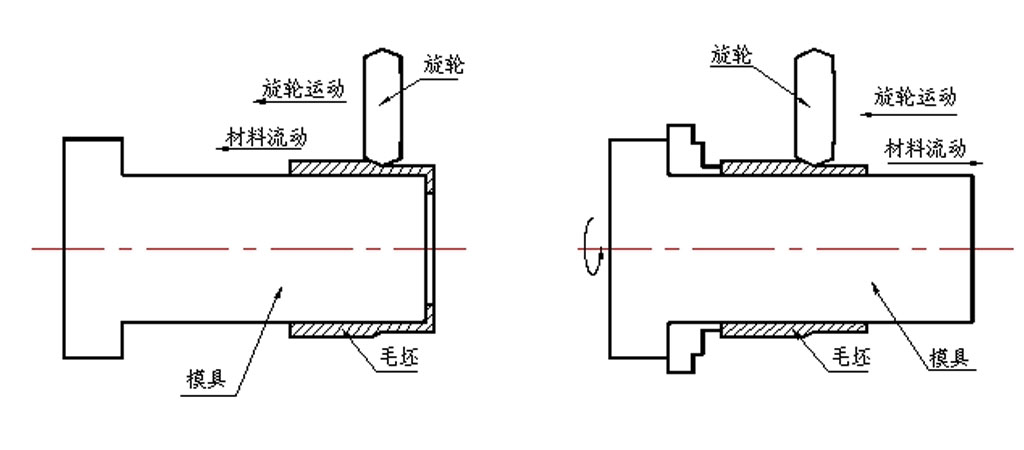
金属へら絞りは、古代から伝わる金属加工技術であり、芸術と科学の融合です。エジプト時代にまで遡るこの技術は、何千年もの間にわたり進化し、手作業の工程からコンピュータと数値制御(CNC)を使用した技術的な製造方法へと進化してきました。
金属へら絞りには大幅な進化があったにもかかわらず、高精度で高品質な仕上がりを必要とする製品を製造するために、手作業による金属へら絞りも依然として使用されています。手作業で金属へら絞り機を操作するためには、長い期間の見習いや特別な能力が求められ、手と目の協調性が必要です。
金属へら絞りは、最も古い素材成形方法の一つです。この技術は、手作業で操作される陶芸のろくろを使用した古代エジプトの陶器製造の技術に由来します。紀元前3000年にはすでに使用されていたとされるこの急速に回転するろくろは、金属へら絞りプロセスの基礎を提供しました。当時は、木材や粘土を成形するために金属へら絞りが使用されており、この技術は今日でも芸術の一形態として存在しています。紀元前25年には、円形の鉄の盾が金属へら絞りを使用して作られていました。
中世の時代には、金属へら絞りは非常に重要な技術となりました。花瓶やティーケトル、トロフィーなどが、このプロセスを使用して製造されました。それらは、職人の助手が手動で操作する大きなフライホイールを用いた回転駆動で木製のへら絞り旋盤を使用して作られていました。
へら絞り機械
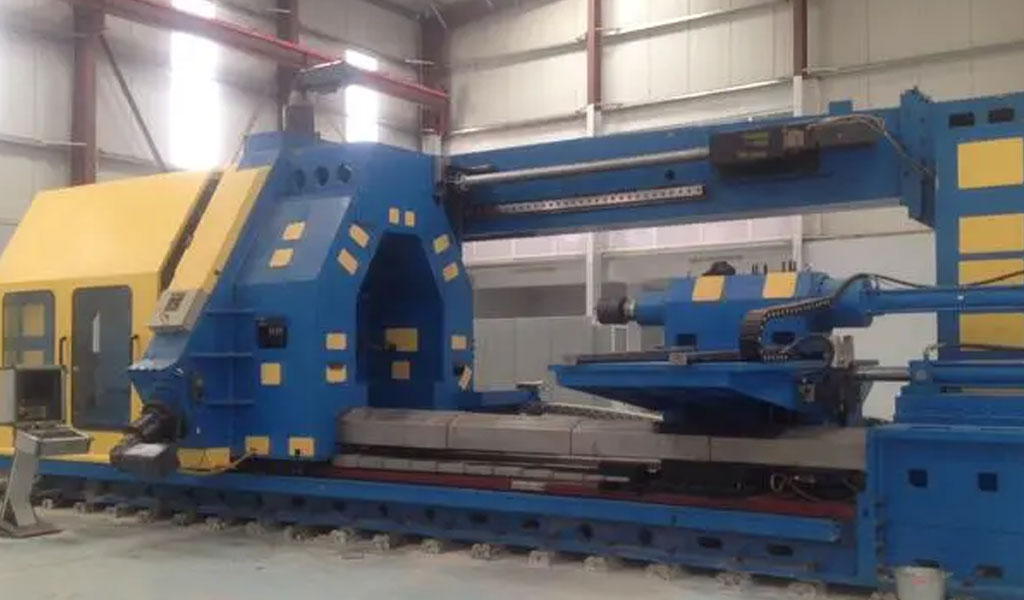
へら絞り操作は、旋盤とローラーを使用して行われます。旋盤は、工作物を軸に沿って高速で回転させる機械であり、切削、穴あけ、研磨などの他の金属加工操作にも使用されます。へら絞り用に適応された旋盤には、マンドレルが含まれます。へら絞り旋盤の基本的なコンポーネントは以下の通りです。
マンドレル
マンドレルは、金属ディスクに体積や形状を与える成形ダイであり、完成品の内形を持っています。工作物を急速に回転させながらサポートし、均一に変形させ、しわや歪みを防ぎます。
金属ディスクは、マンドレルに配置されローラーで加工される前に、グリースやワックスで潤滑され、取り外しを容易にします。潤滑プロセスの二次的な機能は、工作物の表面仕上げを改善し、強化することです。
マンドレルは、鋼、アルミニウム、プラスチック、木材から機械加工されることがあります。プロトタイピングや短期間の生産には、より安価な材料を使用することができます。金属は、ローラーが加える力に耐えるのに十分な剛性を持たなければなりません。
ローラー
へら絞り機のローラーは、部分作業ゾーンと呼ばれる局所的な力を加える剛性のあるツールです。力が加わることで、工作物がマンドレルに沿って流動し、望ましい形状に変形します。
回転する工作物への圧力による摩擦を減らし、熱や早期の摩耗を防ぐために、ローラーツールの設計にはボールローラーが含まれており、プロセス全体で回転します。
ローラーはオペレーターによって手動で操作されることがあり、完璧な部品を生産するためには高度な技術と多くの訓練が必要です。手動生産方法に関連する危険を避けるため、CNC(コンピュータ数値制御)加工がへら絞りプロセスとして人気を博しています。
へら絞りのローラーからの局所的な力は、他の金属加工プロセスと比較して低いです。高強度の厚手の金属を、低い力とエネルギーで大径に成形することができ、コストを削減できます。
作業ゾーンは、工作物の回転とローラーの前進運動によって作られるわずかに螺旋状の経路であり、材料に切片的な流れを生み出し、部品にわずかなねじれを生じさせます。
テールストック
テールストックは、ヘッドストックと一致して反対側に位置し、急速な回転中に工作物をマンドレルに固定しサポートします。必要な圧力を加えて工作物を固定する機構が含まれています。
フォロワー
フォロワーは、テールストックスピンドルの端に取り付けられ、工作物を固定する圧力パッドです。フォロワーの面積は、完成品の底部の面積に対応します。
スピンドル
ヘッドストックのスピンドルは、マンドレルが取り付けられる軸です。成形中にマンドレルと工作物を回転させる役割を果たします。テールストックには、フォロワーが取り付けられている別の回転スピンドルがあります。
ヘッドストック
ヘッドストックは、スピンドルを駆動するために必要な電力を伝達する機構を含むフレームです。この機構は、回転速度(RPM)を制御します。ヘッドストックは、スピンドルと取り付けられたマンドレルをサポートします。
旋盤ベッド
旋盤ベッドは、ヘッドストック、テールストック、その他のへら絞り機械コンポーネントをサポートします。
コンピュータ数値制御(CNC)へら絞り
CNCへら絞りは、旋盤を使用してへら絞りプロセスを制御および自動化します。CNCへら絞りの初期段階は、手動旋盤と似ています。オペレーターは、工作物をCNC旋盤ドライブに配置し、圧力パッドを使用して固定します。
CNCマシンは、成形プロセスのパラメータでプログラムされます。CNC旋盤が作動すると、工作物を型に押し付けながら回転します。手動旋盤と同様に、CNC旋盤の回転力は、金属片を型の形状に変形させます。
CNCへら絞りは、その低コスト、製品の優れた引張強度、優れた仕上げ、洗練された結晶粒構造で推奨されます。寸法安定性は、1000分の1インチまたは100分の1ミリメートル以内です。
プレイバック数値制御(PNC)へら絞り
PNCへら絞りでは、オペレーターがジョイスティックを使用して手動で工作物を成形します。設計された形状が達成されると、プログラムされた変更が保存され、オペレーターの動きを繰り返す形で複数回使用されます。正確な結果を達成するためには、プログラムの非効率な側面を削除し、より効率的なものに置き換えるなど、小さな変更や調整が必要です。
PNCへら絞りは、大量生産に効果的です。プレイバックモードでは、旋盤が成形プロセスを必要に応じて何度でも繰り返し、オリジナルの部品の正確な複製を作成します。オペレーターはブランクを旋盤に置き、プレイバックサイクルを起動します。
主要なへら絞り機械
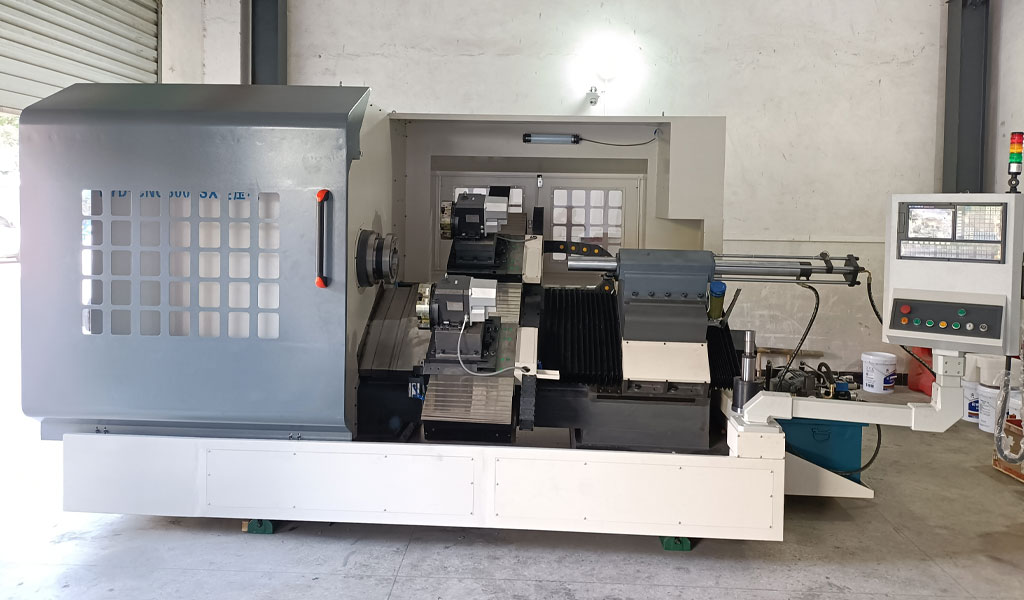
米国およびカナダには、さまざまなへら絞り機械が存在します。これらの機械は、今日の社会において非常に重要です。なぜなら、航空宇宙、自動車、電子機器などの産業で使用されるさまざまな金属部品のコスト効率の良い生産を可能にし、技術の進歩と経済成長に寄与しているからです。以下では、これらの主要な機械とその能力について詳しく説明します。
Leifeld PNC350-800(製造元: Leifeld へら絞り AG)
Leifeld PNC350-800は、非常に評価の高いCNCへら絞り機です。この機械は、高度な自動化能力、精度、信頼性で知られています。大きな工作物を扱うように設計されており、航空宇宙、自動車、その他の産業で使用されるさまざまな金属部品の生産に適しています。CNC制御により、プログラム可能なセットアップが可能で、効率的で多用途に使用できます。
MJC Engineering E-400(製造元: MJC Engineering & Technology, Inc.)
MJC Engineering E-400も、へら絞り用途において人気のある選択肢です。ユーザーフレンドリーなインターフェースとCNC制御が特徴で、プログラムと操作が簡単です。この機械の剛性とパワーにより、高精度かつ再現性の高い重作業のへら絞りタスクに対応できます。
Baileigh R-M10(製造元: Baileigh Industrial, Inc.)
Baileigh R-M10は、手動操作のへら絞り機で、小規模な作業場やホビーストに最適です。CNCオプションほど自動化されていないものの、その手頃な価格、コンパクトなサイズ、使いやすさから人気があります。小規模なプロジェクトやプロトタイプ開発に適しています。
PNC-CNC へら絞り機械シリーズ(製造元: PNC Engineering)
PNC-CNCシリーズは、さまざまなへら絞りニーズに対応するためのCNC制御を備えたモデルを提供しています。これらの機械は、堅牢な構造、ユーザーフレンドリーなインターフェース、優れた性能で知られています。PNC-CNCシリーズは、金属成形の精度と生産性の両方を追求しています。
LNSpin LS-250(製造元: LNS America, Inc.)
LNSpin LS-250は、多用途な自動へら絞り機で、大量生産に適しています。自動ローディングとアンローディング機能を備えており、手動介入を減らし、生産効率を向上させます。LS-250はその信頼性と高速なサイクルタイムで知られており、多くのメーカーにとって優れた選択肢となっています。
特定のモデルの入手可能性や人気は、この最新情報以降に変化している可能性があります。へら絞り機械を調査する際には、メーカーからの最新の製品情報を確認し、特定の機能、生産能力、自動化レベル、予算などの要因を考慮して、要件に最適な機械を選定することが重要です。
へら絞りの種類
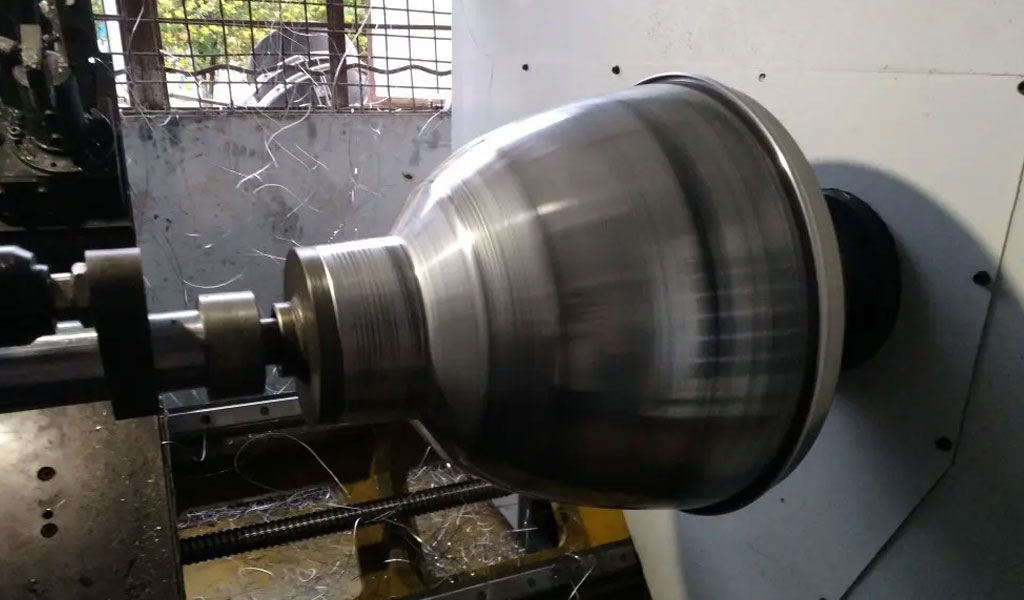
スピニングは、圧縮引き伸ばし成形として分類されます。これは、ローラーが局所的な作業ゾーンおよびその隣接する領域で金属の流れに影響を与えるための放射状、引張、および圧縮応力のためです。引張応力は、ローラーがワークピースに接触し、ローラーの軸方向の送りが増加することで発生し、マンドレルに対して放射状の平面内での体積変位を生じさせます。
金属の体積が中心に近づくほど減少するため、その間に圧縮応力が発生します。これらの応力は、開口端での厚さの増加や、座屈およびしわの可能性に寄与します。これを補正するためには、送り方向を調整する必要があります。
従来のへら絞り
従来のスピニングでは、ローラーがワークピースをマンドレルの輪郭に沿って押し出します。このプロセス全体を通して、ワークピースの材料厚さは一定に保たれます。成形後、ワークピースの深さは増加し、その直径は減少します。これは最も単純な種類のへら絞りと考えられ、シンプルな工具と機械を必要とします。
剪断スピニング
剪断スピニングでは、ローラーがマンドレルの輪郭に沿って移動する際に、ワークピースに下方の力を加えます。完成した部品の材料厚さは元のブランク形状よりも薄くなりますが、その直径は一定です。ワークピースの深さも増加します。ワークピースに大きな圧縮力がかかるため、その機械的特性(例:強度と硬度の向上)も強化されます。
剪断スピニングでは、工具の設計がより頑丈であり、精密な機械制御が必要です。これにより、部品の寸法精度や表面仕上げに影響を与えます。このプロセスは多くの熱を生成し、ワークピースに摩擦を与え、マンドレルの摩耗を引き起こします。冷却剤が必要です。
サイン法則
剪断スピニングプロセスで得られる材料の厚さは、理論的にはサイン法則により決定されます。サイン法則によると、部品の最終厚さは、元の平板金属の厚さに円錐の半頂角のサインを掛けた値に等しくなります。これは、単一パスの剪断スピニングで形成された円錐形のプロファイルにのみ適用されます。スピニング軸に垂直な未形成の金属は、元の厚さを保持します。
熱間スピニング
熱間スピニングでは、トーチを使用してワークピースを鍛造温度まで加熱します。トーチは、ワークピースがマンドレルに押し付けられる間に向けられます。この技術は、材料の延性と可鍛性が低い場合や、金属板が厚すぎて室温で変形しにくい場合に使用されます。室温で行われるスピニング(冷間スピニング)は、あらゆる種類の金属に適しています。
ワークピースが塑性状態で変形するため、熱間スピニングは大きな変形を引き起こし、粒構造が精緻化されるため、強度の向上などの物理的特性が改善されます。しかし、加熱された金属は急速に酸化します。このプロセス全体は制御が難しく、費用も高くなります。
チューブスピニング
チューブスピニングは、円筒状の中空チューブの壁厚を延長および減少させるための剪断スピニングの一形態です。チューブはまずマンドレルに取り付けてクランプされます。チューブをマンドレルの長さに沿って引き伸ばすのは、チューブの周囲に等間隔に配置された3つ以上のローラーによって行われます。材料の軸方向の流れの方向は、ローラーの動きの方向と一致します。
チューブスピニングは、マンドレルの外側または内側で行うことができます。外部チューブスピニングでは、チューブがマンドレルの外表面に伸ばされます。内部チューブスピニングでは、チューブが中空のマンドレル内でスピニングされて伸ばされます。
チューブスピニングは、壁厚が問題でない限り、複数の直径を持つチューブの製造に使用できます。剪断スピニングと同様に、より精巧な工具設計が必要であり、チューブの機械的特性も向上します。
調整
ワークピースの厚さや仕上げは、回転速度(RPM)、ローラーの形状や直径、圧力、アタックアングルを変更することで調整する必要があるかもしれません。また、ワークピースの端の外径を減少させるために2回目のパスが必要な場合もあります。
ワークピースの端を調整するのは難しく、トリムが必要な端や非常に鋭い端ができる可能性があります。調整は慎重に行う必要があります。ローラーが材料の上を通過するたびに、材料は硬くなり、工具から弾みます。
ネッキングや拡張もへら絞りで可能です。ネッキングは、部品の特定の部分の直径が徐々に縮小することを指します。拡張は、部品の特定の部分の直径が増加することを指します。
へら絞りの後処理としては、プラニッシングとトリミングがあります。プラニッシングは、工具によって仕上げ部品に残されたしわやマークを取り除くために行われる仕上げ工程です。この工程では、プラニッシング工具が、低速で回転しているワークピースに力を加えます。トリミングは、仕上げ部品の端にある余分な材料を切断する作業です。
へら絞りに使用される金属
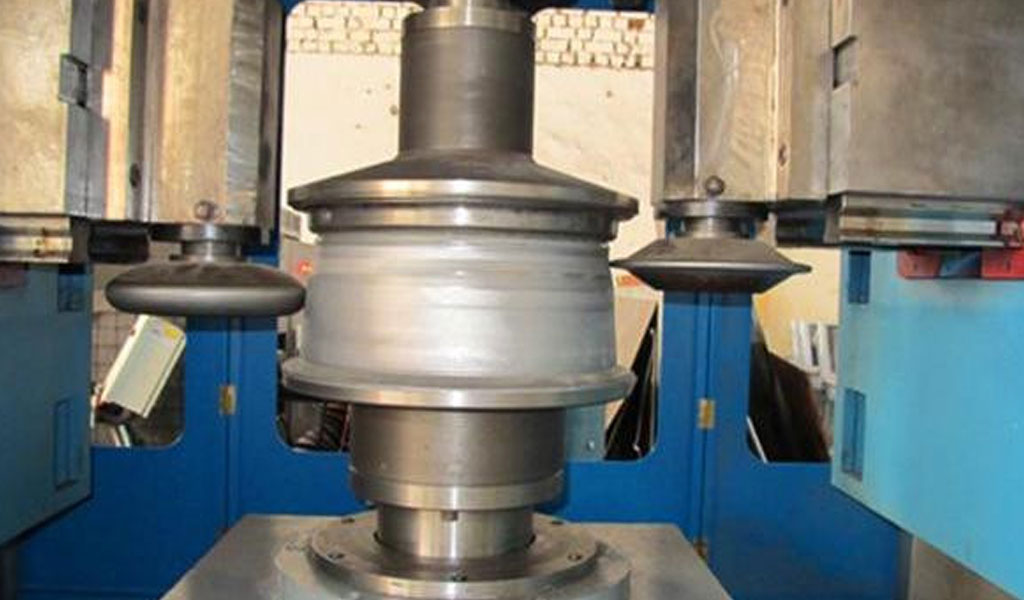
へら絞りは、あらゆる種類の金属に対して行うことができます。金属プレスによって成形可能な金属であれば、へら絞りで加工することができます。場合によっては、プレスでは成形できない金属がへら絞りで加工されることもあります。へら絞り用の旋盤は15,000 psiで動作し、炭素鋼や工具鋼を除くあらゆる金属を変形させることができます。
アルミニウム
アルミニウムは豊富な金属で、高い強度対重量比、延性、および可鍛性を持っています。これらの特性により、へら絞りに理想的な金属となっています。アルミニウムは、へら絞りで最も人気のある材料です。高い耐食性と化学抵抗性、そして優れた熱安定性を持っています。アルミニウムは、鉄鋼に対するコスト効果の高い軽量な代替品です。
へら絞りに最適なアルミニウム合金には、1100、2024、3003、5052、6061、および7075があります。
アルミニウムのへら絞り製品の例としては、調理器具、キッチン用品、ドラム、じょうご、装飾部品、電子機器の部品、電化製品、および家具などがあります。
鋼
鋼は、鉄、炭素、その他の元素を含む合金です。鋼の特性とへら絞り中の加工性は、その組成と製造プロセスに依存します。
ステンレス鋼
ステンレス鋼は、最低でも10.5%のクロムと、ニッケル、モリブデン、マンガンなどの添加剤を含む鋼です。優れた化学抵抗性と耐食性で知られており、高い強度、靭性、剛性を持ち、これらの特性は高圧および高温下でも維持されます。
炭素鋼
炭素鋼は、主に鉄と炭素から成る鋼です。炭素含有量は2%未満です。炭素含有量が多いほど、炭素鋼は強度が高く剛性も増しますが、硬く脆くなり、延性や可鍛性が低下します。また、炭素含有量が増えると、耐食性や化学抵抗性が低下します。それにもかかわらず、炭素鋼はコスト効果の高い代替品として利用されます。
炭素鋼のグレードには、低炭素鋼または軟鋼(炭素含有量3%未満)、中炭素鋼(炭素含有量0.3 – 0.6%)、および高炭素鋼(炭素含有量0.6%以上)があります。
鋼のブランクの製造プロセスも、へら絞り中の加工性に影響を与えます。熱間圧延鋼は、再結晶温度よりも高い非常に高温で圧延されます。一方、冷間圧延鋼は室温で圧延されます。熱間圧延鋼は冷間圧延鋼よりも延性が高く、可鍛性および柔軟性があります。しかし、鋼の熱間圧延は酸化しやすく、強度が低下します。それでも、両方のタイプがへら絞りに適しています。
すべての種類の鋼は、重作業に適しています。鋼のへら絞り部品は、自動車、建設、製造、航空宇宙産業で一般的に使用されます。鋼は、圧力容器、タンク、および加工機器の製造材料として人気があります。
真鍮
真鍮は銅と亜鉛の合金です。優れた熱伝導性と電気伝導性、および銅含有量に起因する良好な耐食性、微生物耐性、及び防汚性を持っています。また、黄色味から赤味を帯びた魅力的な外観を持っており、装飾用途に適しています。
真鍮は良好な延性と可鍛性を持っています。へら絞りで成形された場合、その加工性は優れています。真鍮のへら絞り部品の例としては、楽器、パイプやフィッティング、構造部品、家具、電子機器などがあります。
青銅
青銅は、銅、錫(主要な合金元素)、マンガン、リンの合金です。黄色味を帯びた茶色の魅力的な外観が特徴です。真鍮よりも強度と剛性が高く、重量は真鍮やステンレス鋼よりも重いです。青銅は他の真鍮の特性、例えば良好な溶接性も持っています。
青銅のへら絞り部品は、耐久性があり、強度が高いです。例としては、彫刻、楽器、トロフィー、エンジン部品、構造部品などがあります。しかし、真鍮よりも硬く、可鍛性が低いです。
ハステロイ
ハステロイは、ニッケル、クロム、モリブデンの合金です。この特殊な合金は、優れた化学抵抗性、酸化抵抗性、耐食性で人気があります。ハステロイのへら絞り部品は、石油精製所、発電所、化学製造サイトでの圧力容器のタンクヘッドとして、また自動車や航空機器の部品として広く使用されています。ハステロイは、高温高圧下でも強度と靭性を維持します。
チタン
チタンは、高い強度対重量比、化学抵抗性、耐食性を持つ金属です。軽量で柔らかく延性があるため、へら絞りに適しています。しかし、チタンは非常に高価であり、他の金属ほど頻繁にはへら絞りされません。
へら絞りの応用
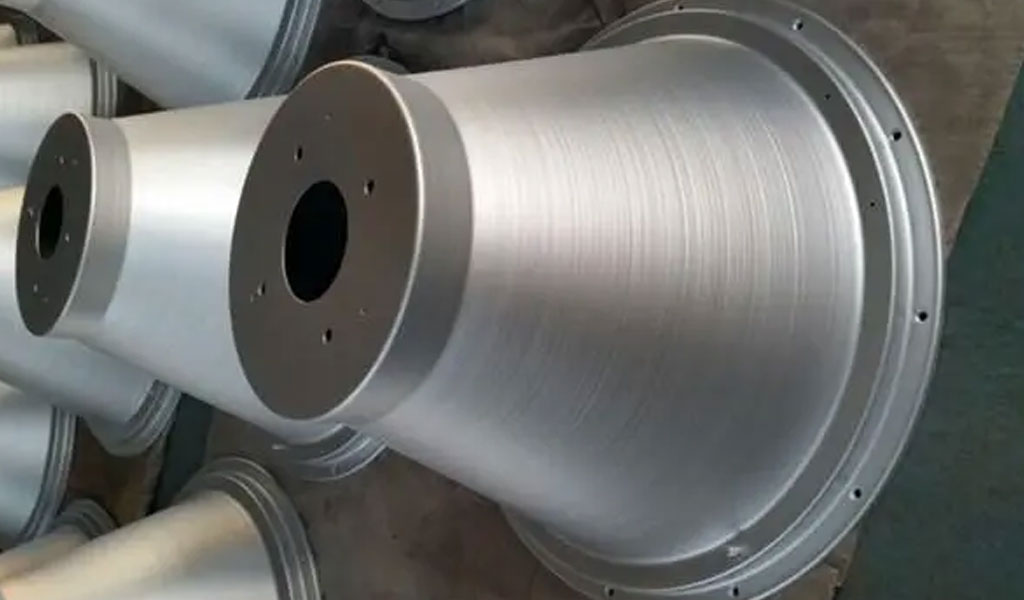
へら絞りは、同心円状の対称部品の中・小ロットの生産や、金属プレス用の金型コストが高額な場合に使用されます。へら絞り形状の生産量が一定のレベルを超えると、金属プレスの方が生産速度が速く、コストも安いため、金属プレスが使用されます。
一部の金属形状は非常に独特で、金属プレスでの生産が不可能であり、へら絞りが最適な製造方法となります。
半球
金属半球は、照明器具、反射板、ミキシングボウル、衛星アンテナ、タンクヘッド、カバー、キャップ、ドームに使用され、直壁ありと直壁なしのデザインが可能です。冷間圧延鋼、ステンレス鋼(304および316グレード)、アルミニウム、銅、および真鍮から作られています。
円錐
漏斗、ホッパー、コーンペンダントなど。
ベンチュリ
集塵機、ファン、ブロワー、スクラバー用のベンチュリ管。
放物面
ベル、アンテナリフレクター、衛星アンテナ、照明器具、柱やスタンドのベースなど。
円筒
パイプ、容器およびタンクの外殻、ガスシリンダー、缶など。
ホッパーの蓋と底
ホッパーの蓋と底は、様々な材料を分配するために手作業で絞られます。これらは、高品質のアルミニウムから作られ、顧客の仕様に合わせて絞られ、トリミングされます。場合によっては、穴やスロットの追加などの二次加工が必要となることもあります。
タンクヘッド
へら絞りは、圧力容器、貯蔵タンク、およびその他の処理装置のタンクヘッドを製造する際に使用される製造プロセスの1つです。容器は高圧や過酷な環境にさらされることが多いため、メーカーはシームレスで耐久性があり、強度の高いタンクヘッドを製造したいと考えています。これを達成するためにへら絞りが使用されます。ただし、タンクヘッドのへら絞りには、規制がその寸法、強度、組成を管理しているため、プロセスの正確な制御が求められます。
タンクヘッドの一般的な形状は以下の通りです:
- フランジのみ
- ディッシュのみ
- フランジとディッシュ
- 半球形
- 高クラウン
- トリスフェリカル
- 2:1 セミエリプティカル
へら絞りの利点と欠点
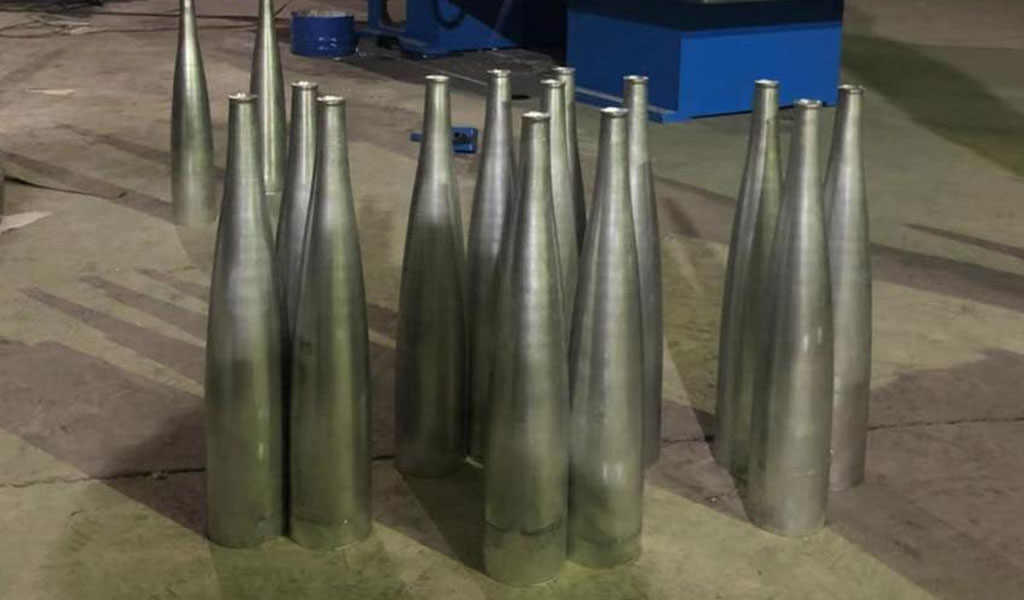
へら絞りの利点
- 信頼性の高い部品が得られる
へら絞りでは、シームレスな部品が製造され、高い内部圧力や外部力に耐える耐久性を持つ部品が得られます。シームは完成品の弱点となり、強度と一体性を低下させることがあります。また、へら絞りは金属の結晶構造を精緻化し、引張強度、靭性、硬度といった機械的特性を向上させます。この特性により、軽量かつ高強度の材料が必要とされる用途において、より軽い材料でも同じ圧力や外部負荷に耐えることが可能になります。 - 工具のコスト効率が高い
へら絞りは、プレス加工、鋳造、鍛造、ハイドロフォーミングなどに比べ、工具が簡素で保守が容易であり、コスト効率が高いです。小規模生産や一度限りの生産には、柔らかく安価な工具が使用できます。ただし、大量生産にはより硬く堅牢な工具が必要です。へら絞りの工具は、セットアップ時間が短く済みます。 - 最終部品の微調整が容易
へら絞りでは、特に部品のサイズを縮小する変更が簡単かつ迅速に行えます。工具の調整だけで済むことが多く、他の金属加工や鋳造プロセスでは費用がかかる修正も、へら絞りでは簡単に対応可能です。 - 廃材が比較的少ない
へら絞りは、比較的少量の廃材しか発生しません。
へら絞りの欠点と制限
- 加工時間が長い
へら絞りは、他の成形および鋳造プロセスに比べ、加工時間が長くなります。通常、中・小規模の生産に限定され、大量生産には時間がかかります。 - 部品の一貫性が維持しにくい
手作業での操作では、部品の一貫性や品質がオペレーターの技能に依存します。 - 形状に制限がある
へら絞りは、円錐、放物線、半球といった軸対称形状の製品の製造に限られます。 - 生産中の誤差が許されにくい
生産中に欠陥(例:ひび割れ、へこみ)が生じた場合、その修正は難しく、部品の品質や信頼性が損なわれる可能性があります。そのため、欠陥のある部品は廃棄しなければなりません。 - 安全リスクが高い
手作業による回転加工では、回転する部品が高速で動くため、多くの安全リスクが伴います。作業開始前にワークピースがテールストックとマンドレルの間にしっかりと固定されていることを確認する必要があります。作業中にワークピースが飛ばされることがあるため、操作中は注意を怠らないことが重要です。
結論
へら絞りは、回転するワークピースにローラーで力を加え、マンドレルの形状に従わせる金属加工技術です。このプロセスでは、平らな金属板や事前に成形された金属板を軸対称形状に変形させます。
へら絞りに使用される旋盤機は、マンドレル、ローラー、テールストック、ヘッドストック、スピンドル、フォロワーなどの部品から構成されています。
従来のへら絞りは、ワークピースの厚みを一定に保ちながら、深さを増します。
剪断絞りでは、ワークピースの直径を一定に保ちながら、厚みを減らします。ワークピースの深さも増加します。
高温絞りは、室温で変形しにくい材料に使用されます。延性や可鍛性が低い材料に適しています。
多重通過絞りは、鋭く複雑な形状の部品を製造する際に使用され、均一な厚みを確保します。
チューブスピニングは、円筒状のチューブを伸ばす剪断絞りの一種です。
へら絞りに最適な材料は、旋盤とマンドレルで変形可能な金属、またはプレス成形可能な金属です。へら絞りでよく使用される金属には、アルミニウム、鋼、真鍮、青銅、ハステロイ、チタンなどがあります。
へら絞りは、半球、円錐、円筒、放物面、ベンチュリなどの製造に特化しています。また、タンクヘッドの製造にも最適です。
シームレスな部品は耐久性が高く、へら絞りによって金属の結晶構造が精緻化され、機械的特性が向上します。