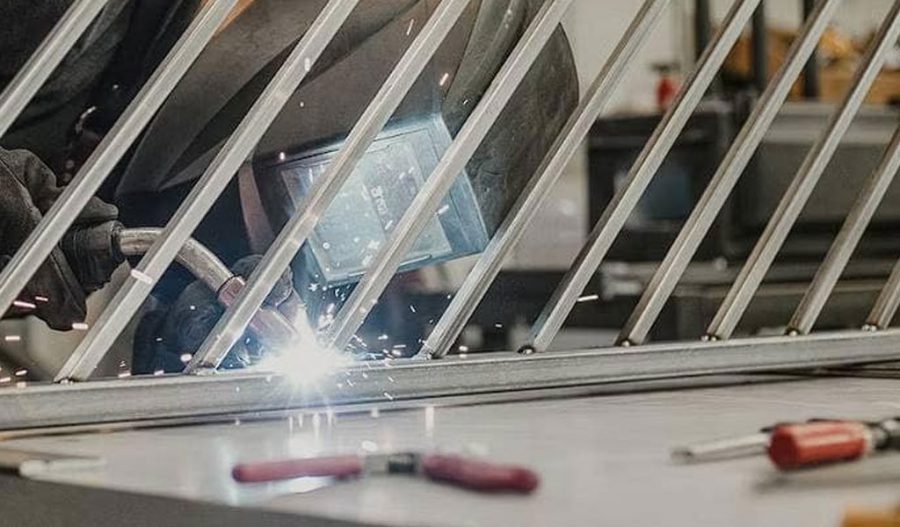
アルミニウムの MIG 溶接は難しいとよく言われます。しかし、これは真実ではなく、アルミニウムの状態と溶接のセットアップに大きく依存します。適切な準備に時間と労力をかけないと、期待通りの結果は得られません。
アルミニウムの MIG 溶接と TIG 溶接を比較すると、前者の方が簡単で時間がかかりません。ただし、正しい手順に従い、適切な準備を行えば、結果として得られる溶接接合部の品質は同じです。
そのため、このブログでは、この一般的な金属を適切に準備する方法、アルミニウムの溶接が難しい理由、使用するシールドガス、MIG 溶接機を適切に設定する方法、適切な溶接技術について説明します。
アルミニウムのMIG溶接はなぜ難しいのでしょうか?
アルミニウムには、鋼とはまったく異なる MIG 溶接手順が必要です。アルミニウムの独特の化学的および物理的特性により、溶融アルミニウムは溶接欠陥に対して特に脆弱であり、溶接が弱くなる可能性があります。適切な機器とノウハウがあれば、強力で長持ちする溶接を回避し、実現することができます。これらの特徴は次のとおりです。
金属の厚さ
炭素鋼などの他の溶融物と比較すると、アルミニウム金属片は一般的に薄くなります。この金属を MIG 溶接する場合、溶け落ちはよくある問題です。これはアルミニウムを溶接する場合によくある問題であり、注意を怠るとすぐに問題が悪化する可能性があります。
高レベルの不純物に敏感
水、汚れ、その他の汚染物質は、アルミニウムの溶接部に簡単に入り込む可能性があります。したがって、アルミニウムを MIG 溶接する際には、金属が汚染されて溶接部が弱くなることがないように、特別な注意を払う必要があります。汚染を避けるには、適切なシールド ガスと充填材を使用してください。
低融点
アルミニウムの融点は華氏約 1,220 度です。酸化されたアルミニウムは華氏 3,700 度でしか溶けません。アルミニウムの融点が低いため、融点が華氏 2,600 度から 2,800 度の鋼鉄と比較すると、扱いが困難です。
アルミニウムを溶接するには、シールドとして機能する酸化物を除去する必要があるため、最初に部品を徹底的に洗浄する必要があります。
高い多孔性
アルミニウムは加熱されて液体状態になると水素を吸収するため、汚染に対して非常に脆弱になります。溶融物に水素が含まれると、冷却時に結晶化する傾向があります。その結果、アルミニウムは気泡の形成により多孔質になります。他の金属合金で溶接すると、耐久性が不十分になります。
アルミニウム用にMIG溶接機を正しく設定する
スプレー転送の正しい電圧は、アルミニウムの MIG 溶接を成功させるために調整する必要がある多くの変数のうちの 1 つにすぎません。
一般的な問題を回避するために、MIG 溶接機の各設定を確認し、シールド ガスの流量について説明します。
ワイヤ送り設定
アルミニウムの MIG 溶接には、軟鋼よりもはるかに高いワイヤ送り速度が必要です。MIG 設定は溶接機のマニュアルに記載されています。
マシンの収納部にチャートがない場合は、ユーザー マニュアルを参照してください。また、会社が承認したアルミニウム溶接手順を確認することもできます。
ただし、MIG 溶接機に設定チャートがない場合は、経験則として、軟鋼の場合よりも 30 ~ 100% 速いワイヤ送り速度を使用できます。
出力アンペア数の選択
MIG 溶接の場合、生成されるアンペア数は、ワイヤが機械に送られる速さによって決まります。金属の溶接には、金属の移動速度が速いほど、より多くのアンペア数とより深い溶け込みが必要になります。
溶接機のアンペア出力は、特定のワイヤ送り速度のモデルによって異なります。そのため、ある機械ではワイヤ送り速度 400 IPM で 200A を出力できますが、別の機械では同じ速度で 180A を出力できます。
アンペア出力はワイヤの直径によっても影響を受けます。ワイヤの太さは、ワイヤが流せる電流に直接関係します。したがって、太いワイヤで細いワイヤと同じアンペア出力を得るには、ワイヤ送り速度を速くする必要があります。
スプールまたはプッシュプルガンアタッチメント
製造元の Web サイトをチェックして、溶接機がスプール ガンまたはプッシュ プル ガンと互換性があるかどうかを確認してください。MIG 溶接機とアルミニウム溶接ガンをすでにお持ちの場合は、製造元の指示に従ってすべてを接続できます。
常にそうであるとは限りませんが、現在では標準の MIG ガンの代わりにスプール ガンまたはプッシュ プル ガンが一般的に使用されています。また、スプール ガンの電源ケーブルを溶接機のフロント パネルに接続する必要があります。
ただし、製造元によっては、シールドガスも供給する溶接リードを使用してスプールガンに電力を供給するところもあるため、絶対的なガイドラインはありません。
シールドガスの流量
アルミニウムの MIG 溶接では、トーチを素早く動かす必要があるため、高いシールド ガス流量が必要です。
アルミニウムの MIG 溶接には、純粋なアルゴンを使用する場合、最低でも 1 時間あたり 20 立方フィート (「CFH」) が必要ですが、炭素鋼の溶接には 15 CFH で十分です。ただし、溶接部分が多孔質の場合は、流量を 1 時間あたり約 30 立方フィートに増やしてみてください。
ただし、アルゴンとヘリウムの混合では、シールド ガスの流量をさらに大きくする必要があります。ヘリウムは空気やアルゴンに比べて密度が低いため、最大 50 CFH の流量が必要になる場合があります。ただし、アルゴンとヘリウムの混合では、シールド ガスの流量をさらに大きくする必要があります。ヘリウムは空気やアルゴンに比べて密度が低いため、最大 50 CFH の流量が必要になる場合があります。
アルミミグ溶接手順
アルミニウム表面洗浄
金属表面の洗浄は、アルミニウムの MIG 溶接における最初のステップです。この手順は、ほこりや湿気などの環境汚染物質を大幅に削減できるため、不可欠です。これらの汚染物質を除去しないと、溶接に問題が生じます。アルミニウムを洗浄するには、溶剤が最も効果的です。
溶剤アセトンはその一例です。この液体は、水蒸気を除去し、アルミニウムの表面からグリースや油を洗浄するのに最適です。アセトンを作業用タオルまたは濡れた布につけてアルミニウムを洗浄し、表面をこすります。
オイルイーターやその他の脱脂剤は、この目的に適した強力な石鹸の 2 つの例です。手順が終了し、アルミニウム片がきれいで乾燥したら、溶接を開始できます。
酸化層を除去する
酸化アルミニウムの融点は、純アルミニウムの融点よりも高くなります。酸化層が溶けるには、華氏 3,700 度が必要です。MIG 溶接用にアルミニウムを準備するには、まず保護コーティングを剥がします。アルミニウムの表面の酸化物は、ステンレス スチールのワイヤー ブラシで簡単にこすり落とすことができます。
ただし、酸化層をこすり落とす前に、脱脂剤を使用して不純物を取り除く必要があります。脱脂剤を使用せずにこすり落とすと、炭化水素やその他の不純物が金属に混入する危険があります。また、初心者の溶接工には、ワイヤーブラシで酸化層を落とすこともお勧めしません。
アルミニウムから酸化物を除去するための代替技術としては、酸化物除去溶液の使用があります。化学溶液を使いすぎるとアルミニウムが損傷する恐れがあるので、注意してください。
最適なMIG溶接フィラー材料を選択する
市販されている溶接ワイヤ電極には、いくつかの異なるタイプがあります。特定の種類に決める前に、溶接の要件と好みを慎重に検討することが重要です。アルミニウムの MIG 溶接用に作られた特別なタイプのワイヤ電極があります。アルミニウム金属の溶接では多孔性などの欠陥が生じる可能性がありますが、この独自の設計により、そのようなことが起こる心配はありません。
ER4043、ER5183、ER4047、ER5356 のフィラー金属は、アルミニウムの MIG 溶接に非常に優れた性能を発揮します。最も人気があり、広く販売されている電極は、ER4043 と ER5356 です。
ただし、ER4043 は ER5356 電極よりもはるかに柔らかいため、自動車のボディ修理に最適な材料です。フィラー材料を決定するときは、溶接するベース材料を考慮する必要があります。
シールドガスを選択
アルミニウムを MIG 溶接する場合、溶接を保護するために適切なシールド ガスを選択することが重要です。これらのガスは、大気中の水素、酸素、窒素による溶接の汚染を防ぎます。溶接部の気泡によって生じる高い多孔性は、不適切なシールド ガスの使用によって生じます。
フラックス コア MIG ワイヤやその他の特殊な MIG 電極はシールド ガスなしでも使用できますが、ほとんどの場合、溶接中にアルミニウムの表面に不純物が形成されるのを防ぐためにガスが必要です。
アルゴンとアルゴン・ヘリウム混合ガスは、アルミニウムの金属不活性ガス溶接 (MIG) に最もよく使用されるシールドガスです。アルミニウムの厚い部分には、ヘリウムとアルゴンを混合して使用します。ただし、酸素と二酸化炭素ガスは、溶融溶接部を酸化させて損傷を引き起こすため、適切な代替ガスではありません。
金属を予熱する
接合部の歪みをなくすために、溶接前にアルミニウムを予熱することができます。この手順は必ずしも必要ではありませんが、アルミニウムの溶接部のひび割れを防ぐのに役立ちます。ただし、熱は華氏 230 度未満に保つのが最適です。
溶接ゾーンの前後にトラック溶接を配置すると、予熱手順が速くなります。厚いアルミニウム板を扱う場合、予熱は不可欠です。一般的な溶接機では、厚いアルミニウム板をうまく溶接するために、より多くの熱が必要になる可能性があります。このため、予熱には誘導加熱器を使用できます。
アルミニウム金属板を予熱する場合、誘導加熱システムは最も安全で信頼性の高い機械の 1 つです。これらのヒーターはコイルベースの設計を特徴としています。これらのシステムは直火に頼らないため、トーチよりも温度調節が優れています。
アルミニウム MIG 溶接のヒントとコツ
アルミニウムの MIG 溶接に関する役立つヒントを以下に示します。
適切な充填材を使用してください。
アルミニウムの MIG 溶接では、優れた性能を発揮するフィラー材料が数多くあります。銅ろう、洋白シート、青銅線、真鍮シム ストックはすべて優れた選択肢です。これらのコンポーネントは、消耗ワイヤ電極と組み合わせて使用すると、特にバッキング バーなしで T ジョイントを形成する場合に優れた性能を発揮します。
軟鋼よりも優れた耐久性を備えているため、ひび割れなどの欠陥から保護するのに最適です。これらの充填材は、アルミニウム溶接の難しさを克服するために必要な特性を備えているため、溶接工は完璧な溶接を行うことができます。その頑丈な特性により、溶接接合部の全体的な信頼性と寿命が向上します。
清潔さは不可欠です。
アルミニウムを溶接する場合は、金属の自然な酸化傾向を考慮する必要があります。最良の結果を得るには、溶接前に表面を徹底的に洗浄することが不可欠です。ステンレススチールのワイヤーブラシは、アルミニウムの表面を洗浄し、酸化層を除去するのに効果的な方法です。
溶接工は、金属の準備に細心の注意を払うことで、溶接の品質を大幅に向上させ、気孔を減らすことができます。溶接前に慎重に洗浄すると、母材と充填材の融合が改善されるだけでなく、アルミニウム溶接の耐久性も向上します。
適切なジョイント設計方法を使用します。
異なる品質の金属を接合する場合、接合設計方法を慎重に選択する必要があります。この選択により、酸化や腐食の可能性が減り、さまざまな金属部品間の接続が安全かつ長持ちします。接続された金属の完全性を維持し、将来の問題を回避するには、接合設計に大きく依存するため、慎重に検討する必要があります。
アルミ線で作られたブラシを使用してください。
溶接前にアルミニウムワイヤーブラシを使用して金属表面から錆や腐食を除去するのが最善の選択肢です。鉄分を多く含むフィラー材料を扱う場合は特に、この作業が重要です。
アルミワイヤーブラシを使用すると、溶接工は錆や酸化層を徹底的に除去して、滑らかで傷のない表面を残すことができます。この入念な準備は、ベースメタルがフィラー材に付着して融合する能力を向上させるため、高品質の溶接を行うために不可欠です。錆を取り除くことで、溶接工は接合部を長持ちさせ、構造上の弱点による故障の可能性を減らすことができます。
より大きな浸透を実現するために電圧を上げます。
溶接中に高い電圧を使用すると、材料のより深い浸透が可能になり、その結果、気孔の可能性が減少します。浸透は、標準的な方法よりも最大 50% 深くなります。ただし、金属シートが意図せず燃え尽きないように注意し、電圧を適切に調整する必要があります。
溶接工は電圧を調整することで、最適な溶け込みとワークピースの保護の間の最適な点を見つけることができます。この微調整により溶接が保護され、連結された金属シートの耐久性と構造的安定性が保証されます。
短時間の溶接
アルミニウムは溶接中に熱くなりすぎることが多いため、1 回の長い溶接よりも、断続的に短い溶接を行うのが最適です。溶接の合間に金属を休ませて冷却することで、この技術により金属が過熱して変形する可能性が低くなります。
この方法は、溶接部とアルミニウム部品を弱める可能性のある過度の熱の蓄積を防ぎます。アルミニウムの過熱によって生じる問題を回避するために、溶接工は加える熱量を制限し、短い冷却間隔を設けることで溶接プロセスの制御を改善できます。
溶接後、ワイヤーを取り外します。
ガンのトリガーを放すときは、フィーダー ワイヤをベースから素早く取り外す必要があります。溶接後にワイヤをガン内に残しておくのは得策ではありません。ワイヤは溶接溜まり内で冷却されるため、溶接品質が低下します。
溶接工は、ワイヤーをガンから素早く引き抜くことで、ワイヤーが内部で冷えるのを防ぎ、スパッタを減らします。この予防措置により、溶接プロセス中に発生するスパッタの量が減り、完成した溶接の品質と外観が向上します。溶接品質の向上と溶接後の清掃時間の短縮は、どちらもこの余分な努力によるメリットです。
結論
アルミニウムの MIG 溶接は、その独特の化学的および物理的特性のため、難しいとよく考えられています。アルミニウムの融点は華氏約 1,220 度であるため、溶接欠陥が発生しやすくなります。汚染や溶接の弱化を防ぐために、適切なシールド ガスと充填材を使用することが不可欠です。
アルミニウムの融点が低いため、融点が華氏 2,600 ~ 2,800 度の鋼鉄に比べて扱いが困難です。強力で長持ちする溶接を実現するには、適切な機器とノウハウを準備することが重要です。アルミニウムの MIG 溶接を成功させるには、スプレー転送の適切な電圧とシールド ガスの流量が不可欠です。
アルミニウムの MIG 溶接では、軟鋼よりも高いワイヤ送り設定が必要です。アンペア出力は、機械に送られるワイヤの速度とワイヤの直径によって異なります。スプールまたはプッシュプルガンのアタッチメントも重要であり、電源ケーブルは溶接機のフロントパネルに接続する必要があります。
アルミニウムの MIG 溶接では、トーチを素早く動かす必要があるため、シールド ガスの流量を高くする必要があります。純粋なアルゴンの場合は最低 20 立方フィート/時 (CFH) が必要ですが、炭素鋼の溶接の場合は 15 CFH で十分です。ただし、アルゴンとヘリウムの混合ガスの場合は、さらに高い流量が必要になります。
アルミニウムの MIG 溶接の最初のステップは、アルミニウムの表面を洗浄することです。これにより、ほこりや湿気などの環境汚染物質が除去されます。アセトンやオイルイーターなどの溶剤は、アルミニウムの洗浄に効果的です。酸化アルミニウムの融点は純粋なアルミニウムよりも高く、酸化層が溶けるには華氏 3,700 度かかります。酸化層をこすり落とすことは不可欠ですが、脱脂剤または酸化物除去溶液の使用をお勧めします。
最適な MIG 溶接フィラー材の選択は、溶接の要件と好みによって異なります。アルミニウムの MIG 溶接には特殊なタイプのワイヤ電極が作られており、これにより気孔などの欠陥がなくなります。アルミニウムの MIG 溶接は非常に効果的なプロセスで、ER4043、ER5183、ER4047、ER5356 などのフィラー金属が最も人気があります。自動車のボディ修理に使用されるベース材料は ER5356 電極よりも柔らかいため、溶接に適した材料となっています。シールド ガスは、溶接部を大気中の水素、酸素、窒素から保護するために不可欠です。一般的なシールド ガスには、アルゴンとアルゴン ヘリウムの混合物があります。
アルミニウム溶接部の溶接割れを防ぐためには金属の予熱が重要ですが、熱を華氏 230 度未満に保つのが最適です。予熱には誘導加熱器を使用できますが、必ずしも必要ではありません。
最良の結果を得るには、適切な充填材を使用し、表面を徹底的に洗浄し、適切な接合設計方法を使用します。溶接前にアルミワイヤーブラシを使用して金属表面の錆や腐食を除去すると、接合部の耐久性が向上します。溶接中に電圧を上げると、浸透が大きくなり、気孔が発生する可能性が低くなります。
過熱や歪みを防ぐために、短時間で溶接してください。この技術により、溶接の間に金属を休ませて冷却できるため、過熱の可能性が減り、過度の熱の蓄積が減ります。溶接後は、飛散を防ぎ溶接品質を向上させるために、フィーダー ワイヤをベースから取り外してください。
ツーリングとCNCの絞り加工能力を最大化する
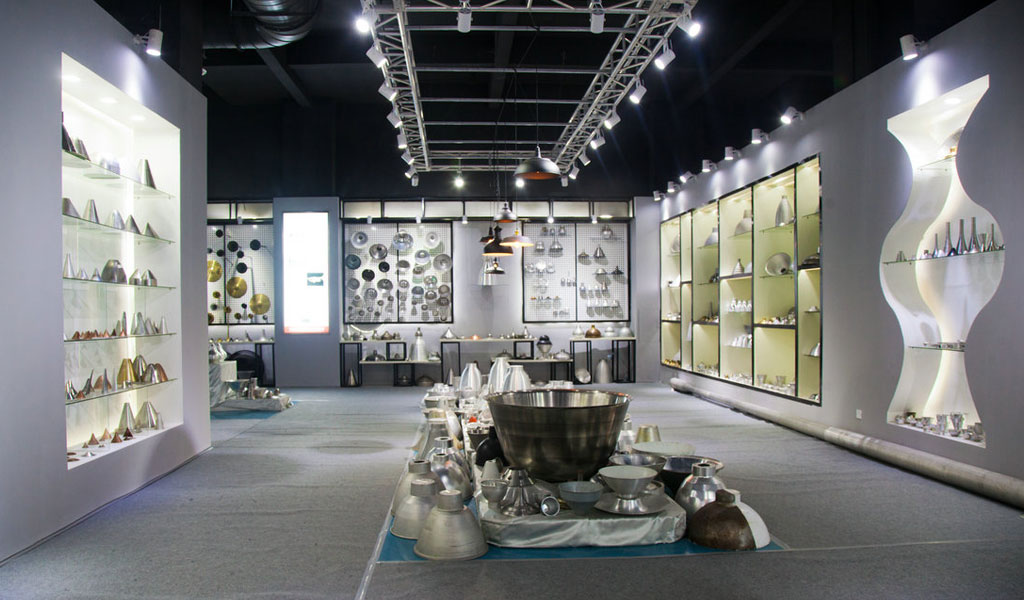
BE-CU 中華のへら 絞り 会社では、過度の摩耗やストレスの兆候を監視しながら、設備を最大限に活用しています。さらに、より新しい最新の設備を検討し、製造能力をサポートまたは向上できる設備に投資しています。当社のチームは機械やツールに細心の注意を払っているため、部品の品質と生産性に悪影響を与えないように定期的にメンテナンスも行っています。
BE-CUの設計とエンジニアリングサポート
BE-CUは、社内の設計およびエンジニアリングチームを活用して、部品生産の初期コンセプトからお客様を支援することができます(提供された設計に対して広範な設計サポートも提供可能です)。私たちのチームは、プロジェクトの開始から終了まで、お客様と定期的かつ透明なコミュニケーションを取りながら、望ましい最終目標に向かって作業を進め、明確な進行方向を提供します。
BE-CUの設計およびエンジニアリングサポートプロセスの一例:
- クライアントがBE-CUチームに部品図面を提供します。
- 当社のエンジニアリングチームが図面をレビューし、ベストプラクティスに基づいて調整を行います。お客様のニーズに応じて、成形または絞り部品を最も効果的に達成する方法を推奨します。
- 図面と設計は必要に応じて改訂され、完璧な形に仕上げられます。財務的な実行可能性も最優先事項として考慮されます。
- 主要な目標は、全ての部品の適合性、形状、機能性を実現することです。
- 研究開発は製造プロセスの重要なステップであり、BE-CUは概念実証や様々な検証要件のためにプロトタイピングサービスを提供しています。研究開発プロセスにおける金属成形については、当社のeBookをご覧ください。
BE-CUが提供する広範な社内サービス
この金属加工プロセスは、軸対称の高性能部品を製造します。スピン成形とも呼ばれ、材料を望ましい形状に切削するのではなく、金属ディスクまたはチューブを円錐形やその他の円形に変形させます。
へら絞りは、手動の手作業によるスピニングプロセスまたは自動CNCスピニングを使用します。BE-CUのへら絞り機能の利点には以下が含まれます:
- コスト削減
- 短いリードタイム
- 最大の設計柔軟性
- シームレスで高品質な構造
対応可能な金属には、ステンレス鋼、炭素鋼、アルミニウム、銅、インコネル、ハステロイ、チタン、ブロンズ、真鍮が含まれます。BE-CUは、センター間60インチから直径100インチまでのカスタム金属絞り部品を製造でき、材料の厚さは0.018インチから2.00インチまで対応可能です。
当社の CNC へら 絞り サービスで迅速なプロトタイプの作成について、今すぐお問い合わせください。こちらでチャットして直接見積もりを取得するか、無料のプロジェクトレビューをリクエストしてください。