
アーク溶接は、電気アークを使用して 2 つ以上の金属片を接合する一般的な溶接方法です。自動車、建設、製造など、さまざまな業界で広く使用されています。アーク溶接は、金属部品間の結合を強力かつ長持ちさせる効率性と適応性でよく知られている技術です。
このブログでは、アーク溶接の仕組みと、この方法を使用することによる利点と欠点について説明します。
アーク溶接とは何ですか?
アーク溶接では、接合する金属を溶かすのに十分な熱を電気で生成し、金属が冷えると接合部が硬化します。溶接電源を使用して金属棒 (「電極」と呼ばれる) と母材の間にアークを発生させ、接触点で金属を溶かします。溶接アークは、使い捨てまたは永久電極と直流または交流で作動します。
溶接エリアは通常、ガス、蒸気、スラグによって飛散する火花、スパッタ、その他の破片から保護されます。アーク溶接には、手動、半自動、全自動の3つの方法があります。アーク溶接は19世紀後半に始まり、第二次世界大戦中に造船業界で広く使用されるようになりました。現在でも、鉄鋼の建物や車両の生産に重要な役割を果たしています。
アーク溶接のプロセスとは何ですか?
アーク溶接は、電気アークによって加工対象の材料を溶かす技術です。このプロセスは、まずアース線を基板に固定することから始まります。次に、溶接工が電極のリード線を加工対象の金属に接触させます。
溶接機は、電極を材料から引き離すときにガスを電気的に分解して、アークまたは連続プラズマ放電を生成します。直流 (DC) または交流 (AC) アーク溶接機は、特定の場所にピンポイント溶接を生成します。
アーク溶接技術を使用すると、金属を溶かすことができます。AC または DC 電源によって生成される電気アークは、約 6500 度 (華氏) に達し、2 つのワークピースの接合部で金属を溶かすのに十分な温度になります。
電極は、電流を流すか、または電流を伝導して同時に溶接プールに溶かし、手または機械によってアークが接合ラインに沿って誘導されるときに接合部にフィラー材料を供給します。
アークによって金属が過熱されると、金属は空気中の酸素や窒素と化学反応を起こします。これを防ぐために、保護ガスまたはスラグを使用して、溶融金属が空気と接触する時間を制限します。溶融金属が冷却されると、冶金結合が形成されます。
アーク溶接の利点
アーク溶接は多くの利点があるため、さまざまな種類の溶接で使用されています。
アプリケーションの多様性
アーク溶接は適応性に優れているため、さまざまな状況で役立ちます。アーク溶接は、さまざまな厚さの金属を接合できるため、幅広い溶接用途に適応できます。
高い生産性
アーク溶接は高品質の溶接を迅速に行うことができるため、生産性を大幅に向上させることができます。アーク溶接機の技術開発により、溶接速度が上がり、出力が向上しました。このため、時間的制約のあるプロジェクトにはアーク溶接が強く推奨されます。
金属の互換性は広い
アーク溶接機を使用すると、炭素鋼、ステンレス鋼、アルミニウム、その他の金属を溶接できます。アーク溶接は適応性に優れているため、さまざまなプロジェクトで頻繁に使用されます。
溶接のためのさまざまな姿勢
アーク溶接の位置は、平面、水平、垂直、頭上まで多岐にわたります。この汎用性により、複雑な形状や対照的な金属を含む溶接プロジェクトでの設計の自由度が向上します。
幅広いアーク溶接プロセス
アーク溶接にはさまざまな技術があり、それぞれに利点があります。フラックス入りアーク溶接、ガスメタルアーク溶接、シールドメタルアーク溶接など、すべて定期的に使用されるアーク溶接の種類です (FCAW)。この多様性により、溶接工はニーズに最も合った手順を選択できます。
コスト効率が高い
アーク溶接は、最も経済的な技術の 1 つです。アーク溶接は、必要な機器が安価で入手しやすいため、DIY 愛好家や中小企業の間で人気があります。アーク溶接は、セットアップが最小限で済み、電極などの消耗品が安価であるため、コスト効率に優れています。
屋外溶接に最適
アーク溶接は、さまざまな気象条件で作業できるため、建設現場や現場で好まれています。アーク溶接の電気アークは気象の影響を受けないため、過酷な条件でも強力な溶接を実現できます。
強力で長持ちする溶接
アーク溶接は、強力で長持ちする溶接部を作り、接合された金属片の品質と耐久性を保証します。電気アークの融合により、優れた機械的特性を持つ溶接部が作られるため、この溶接方法は、構造的完全性が最も重要な用途に最適です。
アーク溶接の欠点
アーク溶接には多くの利点がありますが、欠点もあります。
限定的なアプリケーション
アーク溶接の主な欠点は、その潜在的な用途の範囲が狭いことです。プラスチックやその他の非導電性材料は電気を通さないため、アーク溶接機を使用して溶接することはできません。また、アーク溶接は、アークからの高熱によって材料が簡単に変形するため、薄い金属の溶接には適していません。
溶接スパッタと煙
アーク溶接中に電極が溶けると、溶接煙とスパッタが発生します。これらの廃棄物がもたらす潜在的な危険性を考慮すると、十分な予防措置を講じる必要があります。溶接煙とスパッタは深刻な健康問題を引き起こす可能性があるため、適切な換気と個人用保護具で身を守ることが重要です。
時間がかかる
アーク溶接は、各接合部に特別な注意を払う必要があるため、完了するまでに多くの時間がかかります。時間が重要な場合、溶接プロセスだけで数時間を費やす必要があるのは非常にイライラすることがあります。
専門的なトレーニングが必要です。
専門的な訓練が必要なことも、アーク溶接のもう 1 つの欠点です。アーク溶接に習熟するには、長時間の訓練と経験が必要です。溶接を安全かつ効果的に行うには、溶接工は基礎となる科学をしっかりと理解している必要があります。
アーク溶接による高品質の溶接には、訓練と経験が必要です。溶接工は、関連するすべての溶接理論と安全手順に精通している必要があります。溶接プロセスが適切に実行されていない場合、または溶接工が必要なスキルを習得する必要がある場合、溶接が弱いと溶接部品の構造的完全性が損なわれる可能性があります。
表面の洗浄と準備
アーク溶接による溶接を成功させるには、溶接面を徹底的に洗浄し、準備する必要があります。錆、汚れ、油、その他の汚染物質は溶接の品質を低下させる可能性があるため、溶接前に金属表面がきれいであることを確認することが重要です。表面の洗浄と準備が不適切だと、溶接欠陥や溶接強度の低下が生じる可能性があります。
危険になることもある
適切な安全装置を使用すれば、アーク溶接も安全です。アークの高温により火傷を負う可能性があり、目は紫外線の影響を受けやすいです。アーク溶接では有毒な煙が発生するため、それを吸い込むと危険です。
アーク溶接プロセスのさまざまな種類
アーク溶接にはさまざまな形式があります。アーク溶接の技術は、溶接する金属によって大きく異なります。ここでは、さまざまなアーク溶接方法の概要を説明します。
ガスメタルアーク溶接(MIG溶接)
ガスメタルアーク溶接 (GMAW) は MIG 溶接とも呼ばれ、電極は溶接ガンを通して連続的に供給されるワイヤです。シールドガスは通常アルゴンと二酸化炭素の組み合わせで構成され、溶融した溶接プールを保護する役割を果たし、大気中の酸素と窒素の存在から溶接プールを保護します。
この保護ガス クロークは、大切な宝物を危害から守る用心深い守護者のように、溶接の完全性と品質を保証します。MIG 溶接では、ワイヤをワークピースに押し付けて引き出すことでアークを発生させます。アークが確立されると、ワイヤを溶接ガンから徐々に送り出すことで、隣接する材料を効果的に接合します。
MIG 溶接の利点としては、溶接速度が速く、溶接品質が高く、溶接プロセスを容易に制御できることなどが挙げられます。オンデマンド溶接は、ガスボンベや溶接装置などの溶接装置がかさばるため、より困難です。
MIG 溶接のもう 1 つの欠点は、限られた設定でしか実行できず、厚さ 1/16 インチ以下の材料を簡単に焼き切ってしまうことです。MIG 溶接は、サイクル タイムが速く、溶接品質が高いため、航空宇宙業界ではよく選ばれています。
サブマージアーク溶接
サブマージアーク溶接 (SAW) は、アークをフラックス粒子の覆いの下に沈めておくという点で、アーク溶接のさまざまな方法の中でも独特なものです。SAW では、電極とワークピースの間に形成される電気アークを固体フラックス材料で常に覆います。
溶接プールが形成されると、フラックスが溶解し、部分的に蒸発して、溶接部を覆う保護液スラグが形成されます。シールドガスも生成され、ワークピースの材料が酸素や窒素などの大気ガスと反応するのを防ぎます。
フラックスのブランケットは、飛散や火花を防ぐので、作業場を清潔に保つのに最適です。また、フラックス ブランケットは、有毒な空気や紫外線の影響も軽減します。SAW プロセスには、垂直方向や頭上方向で使用できない、鉄以外の材料には使用できない、パス間でスラグを除去する必要があるなどの欠点があります。パイプラインやその他の圧力容器では、突合せ溶接を作成するために SAW がよく使用されます。
フラックス入りアーク溶接(「FCAW」)
MIG 溶接と比較すると、フラックス入りアーク溶接は非常に似ています。機械は自動的にワイヤをガンに送り込み、それが電極として機能します。溶接プロセスではワイヤが消費されますが、これによりワイヤはフィラーとしての使用にも適しています。
ソリッド MIG ワイヤと比較すると、この電極のコアは中空で、フラックスやその他の化学物質が充填されています。フラックスは加熱されるとシールド ガスとスラグを生成し、ボンベ入りガスを必要とする MIG 溶接機とは対照的に、溶接部を汚染から保護します。
プラズマアーク溶接
プラズマアーク溶接 (PAW) を行うには、消耗品であるタングステン電極をトーチ (溶接ガン) 本体内に収納します。プラズマを生成するには、電気アークでガス (シールドガスではない) をイオン化し、トーチから放出させます。溶接ガン内の電極の位置と、プラズマを放出するノズルの形状によって、プラズマが周囲のシールドガスから分離されます。
PAW の利点には、生産性の高さと、深く精密な溶接が可能なため自動化の可能性が挙げられます。また、PAW ではワークピースにどの方向からでもアプローチできるという利点もあります。PAW に使用する機器は非常に高価で、紫外線 (UV) 放射も発生するため、一部のコンポーネントには水冷が必要です。PAW の精度と速度は、エレクトロニクスや医療など、さまざまな分野で役立っています。
ガスタングステンアーク溶接(TIG溶接)
ガス タングステン アーク溶接 (GTAW) と呼ばれる溶接プロセスでは、消耗タングステン電極を使用してアーク内で金属を接合します。溶接中は、シールド ガス (通常はアルゴンまたは窒素) が放出され、トーチはシュラウドで覆われているため、ガスが漏れて溶接部が損傷するのを防ぎます。
TIG 溶接では、溶接プロセスに対するオペレーターのコントロールが向上し、アーク溶接機で可能な最も強力な接合部が作られ、汚染物質のない溶接が実現します。TIG 溶接の欠点としては、速度が遅いこと、オペレーターのスキル レベルが高いこと、自動化できないことが挙げられます。TIG 溶接は、接合部の強度と柔軟性が同等に重要な場合によく使用されます。
エレクトロスラグ溶接(ESW)
厚さが 1 インチ以上の 2 つのピースを接合する場合、ESW は垂直接合にのみ使用できます。ピース間のスペースにフラックスが充填され、ギャップに自動的に送り込まれたワイヤ電極がフラックスに埋め込まれます。
アークは電流が流れると発生します。しかし、フラックスが溶けると、溶融フラックスの電気抵抗によって、約 3,500°F の溶接熱が発生します。
この用途は、フラックスを使用してジョイントを充填し、溶接中に所定の位置に保持する必要があるため、垂直ジョイントに限定されます。さらに、アーク点灯前にフラックスを保持するために、ジョイントのベースにバッカーまたはスターティング プレートを取り付ける必要があります。
シールドメタルアーク溶接(SMAWまたはスティック溶接)
スティック溶接はシールドメタルアーク溶接 (SMAW) とも呼ばれ、フラックスを塗布した消耗電極棒とワークピースの表面を溶かして溶接接合部を作るアーク溶接技術です。スティック溶接では、棒をワークピースに近づけることでアークが生成されます。
次に、溶接工はワークピースに固定された電極棒を慎重に動かしてアークを発生させ、溶接を完了します。フラックスを塗布した棒は使用され、溶接が進むにつれて最終的に交換されます。
スティック溶接は、特殊な設備に投資することなく、風の強い日の屋外など、さまざまな環境で実行できるという利点があります。ただし、電極がすぐに摩耗するため、薄い材料にはスティック溶接はお勧めできません。スティック溶接は、建設から鉱業、重機、石油・ガス産業など、さまざまな分野で広く使用されています。
アークスタッド溶接(「SW」)
この特殊な方法は、アンカー(または「スタッド」)の溶接用に作られています。電極としても機能する独自の留め具が使用されます。
スタッドの取り付けポイントにアーチを形成するように設計された特殊なガンを使用して、スタッドを溶融プールに押し下げます。これにより、その下の金属にしっかりと溶接されたボルトが生成されます。
熱を集中させて溶融金属を囲むために、シールドガスの有無にかかわらず、特殊なフェルールが溶接部の周囲に配置されます。溶接が完了すると、フェルールは取り外されて廃棄されます。
結論
アーク溶接は、建築、製造、自動車産業など、多くの分野で一般的に行われています。溶接とは、電気アークを使用して金属部品を接合し、強力で長持ちする接続を作成するプロセスです。溶接工は、基板にアース線を取り付け、電極のリード線を接合する金属に接触させます。アークの温度は約 6500 度に達することがあり、これは 2 つの作業部品の継ぎ目の金属を溶かすのに十分な熱です。
炭素鋼、ステンレス鋼、アルミニウムのいずれを扱う場合でも、アーク溶接はお客様のニーズに適応できます。この方法を使用して行う溶接は、耐久性があり、長持ちし、非常に強力で、しかも価格も手頃です。使用が制限されること、溶接ガスと排出物、時間の浪費、専門的なトレーニングなど、欠点はほんの一部にすぎません。
アーク溶接では高温になるため、薄い金属は特に変形しやすくなります。溶接ガスやスパッタの危険性があるため、保護具の使用と適切な換気が必要です。
錆、汚れ、油、その他の不純物はアーク溶接の品質を低下させる可能性があるため、作業を始める前に表面を慎重に洗浄し、準備する必要があります。火傷、紫外線、有毒ガスはすべて潜在的な危険であるため、適切な保護具を用意しておくことが重要です。
結論として、アーク溶接は多くの利点と欠点を備えた柔軟で効果的な溶接方法です。ただし、溶接部品の安全性を保証するには、正しい安全装置を使用し、適切なプロトコルに従うことが重要です。一般に MIG 溶接として知られるガス金属アーク溶接 (GMAW) の溶融池は、溶接ガンから絶えず供給されるシールド ガスによって周囲の酸素と窒素から保護されます。この方法は、溶接の耐久性と品質を保証します。ただし、溶接装置が非常に大きく重いため、より困難で、特定の場所に限られます。
サブマージアーク溶接 (SAW) は、アークがフラックス粒子のブランケットの下に沈んだままになるユニークな技術です。この方法では、スパッタや火花から保護し、有害なガスや日光の影響を軽減するシールド液体スラグが生成されます。ただし、パス間でスラグを除去する必要がある、垂直方向または上方向で使用できない、鉄以外の材料には使用できないなどの欠点があります。
MIG 溶接と同様に、フラックス入りアーク溶接 (FCAW) では、フラックスと化学物質を充填した中空電極コアを使用します。高速で精密な溶接方法である PAW では、ワークピースのどの側からでも溶接が可能です。ただし、コストが高く、一部の部品は水冷する必要があります。
ガス タングステン アーク溶接 (TIG) では、アーク内で金属を融合するために、使い捨てのタングステン電極を使用します。TIG 溶接では、溶接工によるより正確な操作が可能になり、最も強力な溶接部が作られ、汚染の可能性が排除されます。フラックスがコンポーネント間のスペースを満たし、ワイヤ電極がフラックス内に埋め込まれるため、ESW は垂直ジョイントにのみ適用できます。
シールドメタルアーク溶接はスティック溶接とも呼ばれ、フラックスを塗布した電極棒とワークピースの表面を溶かすアーク溶接法です。さまざまな状況で役立ちますが、電極の摩耗のため薄い材料には使用しないでください。
アークスタッド溶接 (SW) は、電極としても機能する特定の留め具を使用して、アンカーを溶接するための特殊な技術です.
ツーリングとCNCの絞り加工能力を最大化する
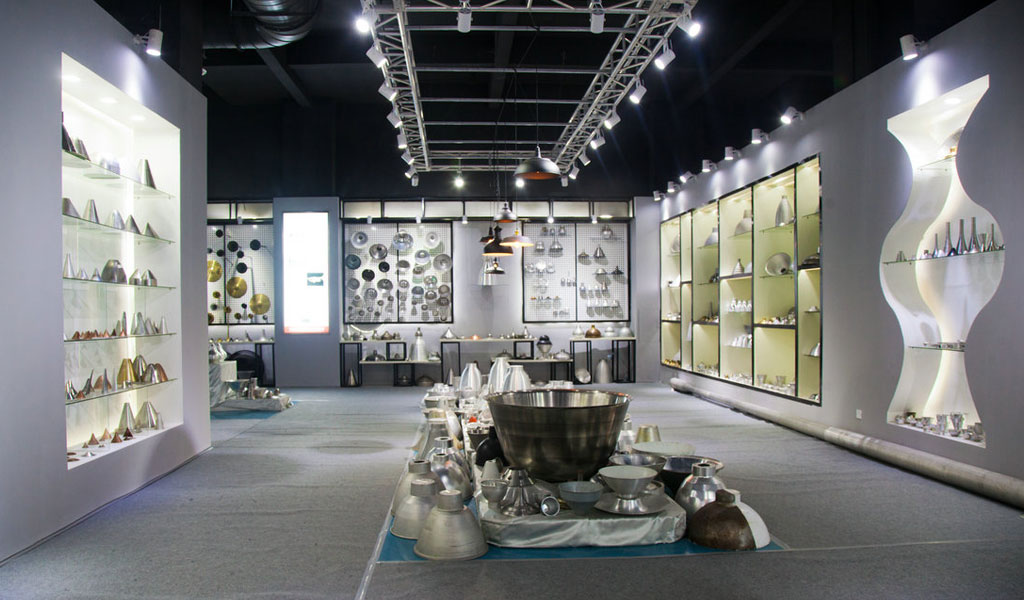
BE-CU 中華のへら 絞り 会社では、過度の摩耗やストレスの兆候を監視しながら、設備を最大限に活用しています。さらに、より新しい最新の設備を検討し、製造能力をサポートまたは向上できる設備に投資しています。当社のチームは機械やツールに細心の注意を払っているため、部品の品質と生産性に悪影響を与えないように定期的にメンテナンスも行っています。
BE-CUの設計とエンジニアリングサポート
BE-CUは、社内の設計およびエンジニアリングチームを活用して、部品生産の初期コンセプトからお客様を支援することができます(提供された設計に対して広範な設計サポートも提供可能です)。私たちのチームは、プロジェクトの開始から終了まで、お客様と定期的かつ透明なコミュニケーションを取りながら、望ましい最終目標に向かって作業を進め、明確な進行方向を提供します。
BE-CUの設計およびエンジニアリングサポートプロセスの一例:
- クライアントがBE-CUチームに部品図面を提供します。
- 当社のエンジニアリングチームが図面をレビューし、ベストプラクティスに基づいて調整を行います。お客様のニーズに応じて、成形または絞り部品を最も効果的に達成する方法を推奨します。
- 図面と設計は必要に応じて改訂され、完璧な形に仕上げられます。財務的な実行可能性も最優先事項として考慮されます。
- 主要な目標は、全ての部品の適合性、形状、機能性を実現することです。
- 研究開発は製造プロセスの重要なステップであり、BE-CUは概念実証や様々な検証要件のためにプロトタイピングサービスを提供しています。研究開発プロセスにおける金属成形については、当社のeBookをご覧ください。
BE-CUが提供する広範な社内サービス
この金属加工プロセスは、軸対称の高性能部品を製造します。スピン成形とも呼ばれ、材料を望ましい形状に切削するのではなく、金属ディスクまたはチューブを円錐形やその他の円形に変形させます。
へら絞りは、手動の手作業によるスピニングプロセスまたは自動CNCスピニングを使用します。BE-CUのへら絞り機能の利点には以下が含まれます:
- コスト削減
- 短いリードタイム
- 最大の設計柔軟性
- シームレスで高品質な構造
対応可能な金属には、ステンレス鋼、炭素鋼、アルミニウム、銅、インコネル、ハステロイ、チタン、ブロンズ、真鍮が含まれます。BE-CUは、センター間60インチから直径100インチまでのカスタム金属絞り部品を製造でき、材料の厚さは0.018インチから2.00インチまで対応可能です。
当社の CNC へら 絞り サービスで迅速なプロトタイプの作成について、今すぐお問い合わせください。こちらでチャットして直接見積もりを取得するか、無料のプロジェクトレビューをリクエストしてください。