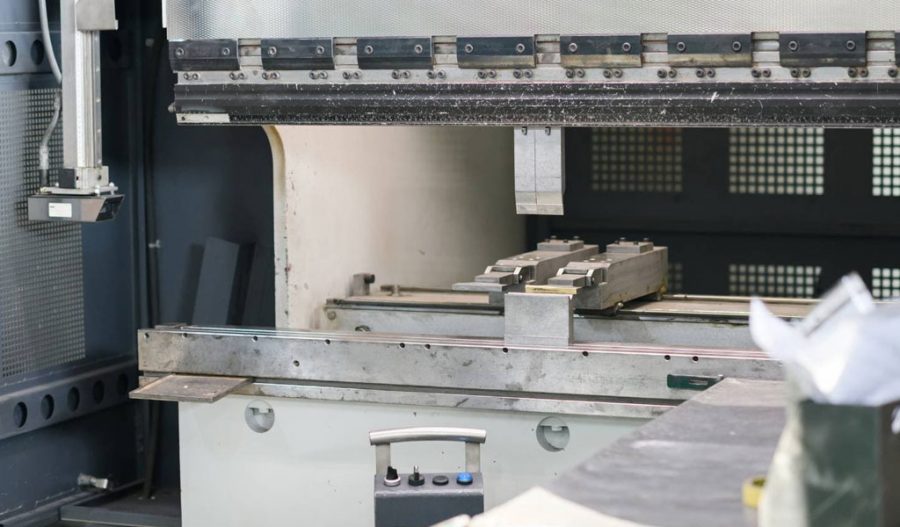
一見単純な質問ですが、金属部品の設計や製造に携わる人にとっては、この質問は非常に重要です。なぜなら、この質問は、製造プロセス中に使用される機械、材料、方法の選択に直接影響を与えるからです。
金属シートや金属板を正確に曲げる能力は、単純なブラケットから複雑な機械部品まであらゆるものを製造する上で非常に重要であるため、プレスブレーキの曲げ能力をしっかりと理解しておくことが不可欠です。次のブログ投稿では、プレスブレーキの曲げ能力に影響を与えるいくつかの側面について見ていきます。これらの考慮事項には、金属の種類、曲げの長さ、プレスブレーキの特定の特性が含まれます。
このレッスンでは、鋼、アルミニウム、銅など、さまざまな金属を曲げる複雑な作業と、これらの金属の特性が曲げ加工に及ぼす影響について説明します。さらに、現代のプレスブレーキの性能を向上させ、金属曲げ加工をより正確かつ効率的に実行できるようにした技術的な改善についても説明します。
曲げ能力に影響を与える要因
プレスブレーキの曲げ能力は、 達成できる曲げの精度と品質を決定する多くの要因の影響を受けます。 これらの要因は、材料特性や工具から機械の技術仕様やオペレーターのスキルまで多岐にわたります。これらの重要な要因について詳しく見てみましょう。
材料特性:
- シート材料: 材料の種類と、厚さ、硬度、木目方向などの特性は、曲げ加工に大きく影響します。引張強度の高い材料はより大きな曲げ力を必要とし、機械の能力に影響します。
- 応力とプレートの厚さ: 応力の分布が不均一であったり、プレートの厚さが一定でなかったりすると、曲げ精度にばらつきが生じる可能性があります。応力が均一でプレートの厚さが一定であれば、曲げ精度は高くなります。
プレスブレーキ工具:
- ツールの精度: ツール自体の精度が最も重要です。ツールが不正確な場合、曲げ精度が低下します。上部の金型のエッジと角度が下部の金型のノッチと一致することを確認することが重要です。
- 金型補正装置: プレスブレーキの金型補正装置の精度は、曲げ精度に直接影響します。CNC 制御の補正装置では、手動調整よりも、さまざまなプレート位置でより正確な調整が可能です。
機械仕様:
- 機械製造精度: クランプ開口部の真直度、Y1 軸と Y2 軸の繰り返しおよび任意の位置決め精度、スライダーとガイド レール間のクリアランスなど、プレス ブレーキの各部品の製造精度はすべて、全体的な曲げ精度に影響します。
- フレームとスライダー: フレームとスライダーの強度と精度、およびオイルシリンダーとスライダー間の接続の一貫性は、正確な曲げを実現するために不可欠です。
ヒューマンファクター:
- オペレーターのスキル: オペレーターのスキルと経験は重要な役割を果たします。自動化されたシステムであっても、オペレーターが機械を正しくセットアップして調整する能力が結果に影響します。
- 自動化: ロボットプレスブレーキを導入すると、人為的エラーの影響を最小限に抑え、曲げ作業の一貫性と精度を高めることができます。
追加の考慮事項:
- クランプ精度: トップパンチを保持するクランプの精度は、全体的な曲げ精度に影響します。高精度のクランプにより、曲げが一貫して正確になります。
- 材料サポート: 高い繰り返し位置決め精度を備えたフロント材料サポートとバックゲージ システムの使用により、曲げの精度がさらに向上します。
曲げ強度の計算
プレスブレーキの曲げ能力は、曲げる材料の種類、曲げの長さ、プレスブレーキ自体の特性など、いくつかの要因によって決まります。ここでは、さまざまな情報源から得た知見を基に、プレスブレーキの曲げ能力を計算する方法の概要を示します。
素材の厚さと種類:
曲げ能力を計算する際、材料の厚さと種類が主な要素となります。材料によって引張強度のレベルが異なり、曲げに必要な力に直接影響します。たとえば、高張力鋼の厚い板を曲げるには、薄いアルミニウム板を曲げるよりも大きな力が必要です。
曲げの長さ:
曲げの長さも、必要な曲げ力を決定する上で重要な役割を果たします。曲げが長いほど、曲げの長さ全体にわたってより大きな力が必要になります。プレスブレーキの曲げ能力は、多くの場合、特定の長さの軟鋼を特定の厚さに曲げることに基づいて評価されます。
プレスブレーキ仕様:
プレスブレーキの仕様、たとえばトン数、タイプ (油圧、機械、電気)、機能 (CNC 制御、ツール オプション) は、曲げ能力に影響します。トン数が高いプレスブレーキは、より厚く、より頑丈な材料を扱うことができます。
Vダイ開口部:
曲げる材料の厚さに対する V ダイ開口部のサイズは、曲げ能力に影響します。一般的な目安としては、V ダイ開口部の幅は材料の厚さの約 8 倍にする必要があります。
曲げ力の計算:
曲げ力は次の式で計算できます: 曲げ力 = (材料の引張強度 x 材料の厚さ² x 曲げ長さ) / (V ダイ開口部 x 定数)。定数は測定単位と曲げる材料によって異なります。
安全マージン:
プレスブレーキの過負荷を防ぐために、曲げ能力を計算する際には安全マージンを考慮することが重要です。プレスブレーキは、最大定格能力の 80% 以下で動作させるのが一般的です。
技術の進歩とその影響
プレスブレーキ技術の進化により、金属加工業界は大きく変わり、効率、精度、安全性の新しい時代が到来しました。この変革は主に、CNC 技術、自動化、高度なソフトウェアとハードウェアの統合の進歩によるものです。これらの技術の進歩がプレスブレーキの運用をどのように変えたかを以下に概説します。
CNC テクノロジーと自動化:
CNC (コンピュータ数値制御) 技術の導入は、プレスブレーキ操作に革命をもたらしました。CNC プレスブレーキは、オペレーターが機械に詳細な曲げ指示をプログラムできるようにすることで、比類のない精度を提供します。これにより、エラーの余地が減るだけでなく、複数の操作にわたって一貫した結果が保証されます。自動化により、曲げプロセスが合理化され、手作業が減り、スループットが向上するため、これがさらに強化されます。
ソフトウェアの適応:
最新のプレスブレーキには、材料の挙動に リアルタイムで適応する高度なソフトウェアが搭載されています。このソフトウェアは、レーザー測定システムなどの内部および外部のセンシングを利用して、クラウニングやたわみの変化などの材料特性を考慮します。この適応性により、一貫性のない特性を示す材料でも、曲げ操作の高精度が保証されます。
アダプティブベンディング:
新しいプレスブレーキは、曲げ加工中にスプリングバック、たわみ、およびさまざまな引張強度を事前に計算して調整できます。これは、下部ビームの機械的または油圧的な調整によって実現され、材料の不一致に関係なく、各曲げが正確であることを保証します。一部のシステムでは、サイクル全体にわたってトン数を監視し、精度を維持するためにリアルタイムで調整を行います。
オフラインプログラミング:
オフライン プログラミング機能により、プレス ブレーキのセットアップ プロセスが一変しました。ブランクのサイズを決定する前に 3D 図面から直接プレス ブレーキ プログラムを作成することで、オペレーターはプレス ブレーキの特性をすばやく入力して精度を確保できます。これにより、工場の現場での手動プログラミングが不要になり、プレス ブレーキの生産を安定的に維持できます。
安全性と効率性の向上:
技術の進歩により、安全性と効率性も大幅に向上しました。最新のプレスブレーキには、統合された安全システムが標準装備されており、操作がより安全になり、プレス関連の負傷の発生率が減ります。さらに、精密研磨されたセグメント化された曲げツールとアクティブ角度補正テクノロジーにより、プレスブレーキのセットアップがより速く、より人間工学的で、より正確になりました。
環境への配慮:
エネルギー効率と持続可能な製造方法はますます重要になっています。最新のプレスブレーキはエネルギー効率に優れた設計になっており、運用コストの削減と環境への影響の低減に貢献しています。これは、より持続可能な製造プロセスに向かう業界の動向と一致しています。
厚い金属を曲げる際の実際的な考慮事項
プレスブレーキで厚い金属を曲げるには、精度、効率、安全性を確保するためにいくつかの実用的な考慮事項があります。これらの考慮事項は、プレスブレーキの機能を最大限に活用しながら、望ましい曲げ品質を実現するために不可欠です。さまざまな情報源からの洞察に基づいて、これらの考慮事項を包括的に説明します。
材料特性と準備:
- 材料の挙動を理解する: 金属の種類によって、引張強度、硬度、弾性など、曲げ方に影響する独自の特性があります。これらの特性を理解することで、適切な曲げ技術とツールを選択するのに役立ちます。
- 表面処理: 金属表面が清潔で、曲げ精度に影響を与えたり工具を損傷したりする可能性のある汚染物質やコーティングがないことを確認することが重要です。
ツールの選択と注意:
- 適切なツール: 金属の厚さ、種類、希望する曲げ角度に基づいて、適切なパンチとダイを選択することが重要です。厚い金属に適していないツールを使用すると、曲げが不正確になったり、ツールが損傷したりする可能性があります。
- ツールのメンテナンス: 曲げの欠陥を防ぐために、曲げツールを定期的に検査してメンテナンスします。ツールが摩耗または損傷すると、曲げの品質と精度が損なわれる可能性があります。
マシンの容量と設定:
- 機械の限界を理解する: プレスブレーキの最大曲げ能力を知ることは、機械の過負荷を避けるために重要です。機械の能力を超える厚さの金属を曲げると、プレスブレーキが損傷する可能性があります。
- 正確な機械設定: 特定の曲げ作業に応じて、曲げ力、速度、バックゲージの位置などのプレスブレーキ設定を調整することで、最適な曲げ性能が確保されます。
曲げ技術:
- エアベンディング、ボトムベンディング、コイニング: 材料の厚さと必要な曲げ精度に基づいて適切な曲げ技術を選択します。エアベンディングは柔軟性があるため一般的に使用されますが、厚い金属や高精度が必要な場合は、ボトムベンディングまたはコイニングが必要になる場合があります。
- クラウニング システムの使用: クラウニング システムは、機械のたわみを補正し、長い曲げや厚い金属を曲げる場合に、全長にわたって均一な曲げを保証します。
オペレーターのスキルと安全性:
- 経験豊富なオペレーター: 厚い金属をうまく曲げるには、プレスブレーキの操作、材料の挙動、安全プロトコルに関する知識を持つ熟練したオペレーターが不可欠です。
- 安全対策: 曲げ作業中の事故を防ぐためには、ライトガードや安全マットの使用、適切な操作手順の遵守などの安全対策を実施することが重要です。
曲げ後の考慮事項:
- 検査と品質管理: 曲げ加工後は、ワークピースの精度、一貫性、欠陥の有無を検査することが重要です。これにより、曲げ加工が必要な仕様と品質基準を満たしていることが保証されます。
- スプリングバック補正: 厚い金属を扱う場合、曲げた後に金属が部分的に元の形状に戻る傾向であるスプリングバックを考慮することが重要です。曲げ角度を調整してスプリングバックを補正すると、最終製品が希望の寸法を満たすことが保証されます。
結論
プレスブレーキの曲げ能力は、ブラケットや複雑な機械部品など、さまざまな金属部品を製造するために非常に重要です。
曲げの長さとプレスブレーキの特定の特性、シート材料、応力とプレートの厚さ、ツールの精度、ダイ補正装置の精度、機械の仕様、フレームとスライダーの強度、オペレーターのスキル、自動化、クランプ精度、材料のサポートなどの材料特性はすべて、プレスブレーキの曲げ能力を決定する上で重要な役割を果たします。
プレスブレーキの曲げ能力は、曲げる材料の種類、曲げの長さ、プレスブレーキ自体の特性など、いくつかの要因によって決まります。材料の厚さと種類は主な要因です。材料によって引張強度のレベルが異なり、これが曲げに必要な力に直接影響します。
プレスブレーキの仕様、たとえばトン数、タイプ、機能も曲げ能力に影響します。材料の厚さに対する V ダイ開口部のサイズは曲げ能力に影響します。曲げ力は、次の式を使用して計算できます: 曲げ力 = (材料の引張強度 x 材料の厚さ² x 曲げの長さ) / (V ダイ開口部 x 定数)。
プレスブレーキ技術は金属加工業界を大きく変革し、効率、精度、安全性の新時代をもたらしました。CNC 技術、自動化、および高度なソフトウェアとハードウェアの統合の進歩により、プレスブレーキの運用が刷新されました。CNC 技術により、オペレーターは詳細な曲げ指示を機械にプログラムできるため、エラーの余地が減り、複数の操作にわたって一貫した結果が得られます。最新のプレスブレーキには、材料の挙動に リアルタイムで適応できる高度なソフトウェアが搭載されており、曲げ操作の高精度が保証されます。
オフライン プログラミング機能により、プレス ブレーキのセットアップ プロセスが一変し、オペレーターはプレス ブレーキの特性を入力して精度を迅速に確保できるようになりました。標準装備、精密研磨、セグメント化された曲げツール、アクティブ角度補正テクノロジーなどの統合された安全システムにより、安全性と効率性が向上しました。
エネルギー効率と持続可能な製造方法はますます重要になってきており、最新のプレスブレーキはエネルギー効率に優れた設計になっており、運用コストの削減と環境への影響の低減に貢献しています。
プレスブレーキで厚い金属を曲げる場合の実際的な考慮事項には、材料の特性と準備の理解、適切なツールの選択、ツールの保守、機械の容量と設定の理解、曲げ技術の選択、クラウニングシステムの使用、熟練したオペレーターの配置などがあります。 曲げ工程中の事故を防ぐためには、ライトガードや安全マットの使用などの安全対策が不可欠です。曲げ後の考慮事項には、検査、品質管理、スプリングバック補正などがあり、最終製品が希望の寸法を満たしていることを確認します。
ツーリングとCNCの絞り加工能力を最大化する
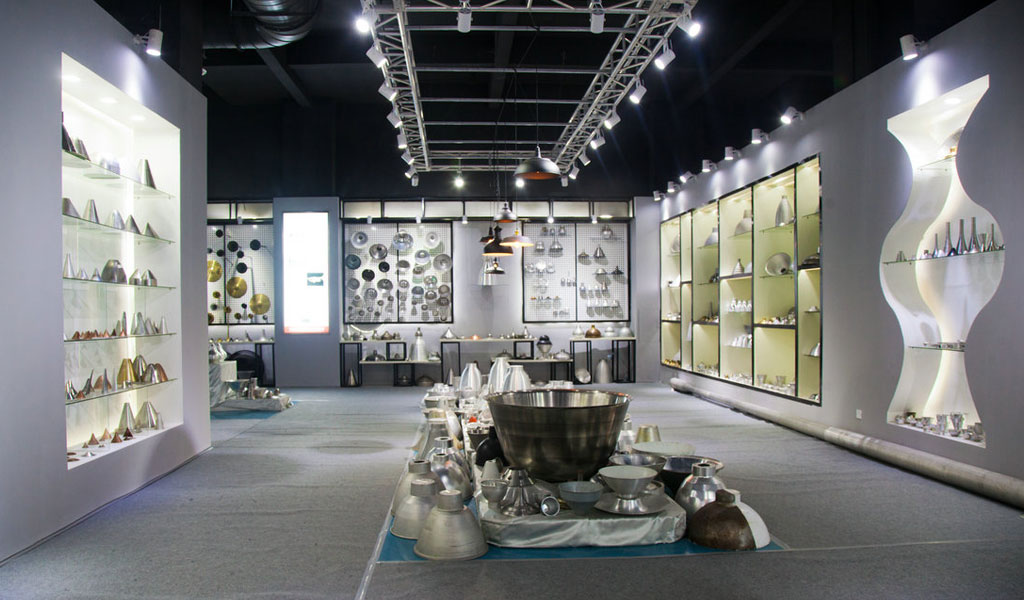
BE-CU 中華のへら 絞り 会社では、過度の摩耗やストレスの兆候を監視しながら、設備を最大限に活用しています。さらに、より新しい最新の設備を検討し、製造能力をサポートまたは向上できる設備に投資しています。当社のチームは機械やツールに細心の注意を払っているため、部品の品質と生産性に悪影響を与えないように定期的にメンテナンスも行っています。
BE-CUの設計とエンジニアリングサポート
BE-CUは、社内の設計およびエンジニアリングチームを活用して、部品生産の初期コンセプトからお客様を支援することができます(提供された設計に対して広範な設計サポートも提供可能です)。私たちのチームは、プロジェクトの開始から終了まで、お客様と定期的かつ透明なコミュニケーションを取りながら、望ましい最終目標に向かって作業を進め、明確な進行方向を提供します。
BE-CUの設計およびエンジニアリングサポートプロセスの一例:
- クライアントがBE-CUチームに部品図面を提供します。
- 当社のエンジニアリングチームが図面をレビューし、ベストプラクティスに基づいて調整を行います。お客様のニーズに応じて、成形または絞り部品を最も効果的に達成する方法を推奨します。
- 図面と設計は必要に応じて改訂され、完璧な形に仕上げられます。財務的な実行可能性も最優先事項として考慮されます。
- 主要な目標は、全ての部品の適合性、形状、機能性を実現することです。
- 研究開発は製造プロセスの重要なステップであり、BE-CUは概念実証や様々な検証要件のためにプロトタイピングサービスを提供しています。研究開発プロセスにおける金属成形については、当社のeBookをご覧ください。
BE-CUが提供する広範な社内サービス
この金属加工プロセスは、軸対称の高性能部品を製造します。スピン成形とも呼ばれ、材料を望ましい形状に切削するのではなく、金属ディスクまたはチューブを円錐形やその他の円形に変形させます。
へら絞りは、手動の手作業によるスピニングプロセスまたは自動CNCスピニングを使用します。BE-CUのへら絞り機能の利点には以下が含まれます:
- コスト削減
- 短いリードタイム
- 最大の設計柔軟性
- シームレスで高品質な構造
対応可能な金属には、ステンレス鋼、炭素鋼、アルミニウム、銅、インコネル、ハステロイ、チタン、ブロンズ、真鍮が含まれます。BE-CUは、センター間60インチから直径100インチまでのカスタム金属絞り部品を製造でき、材料の厚さは0.018インチから2.00インチまで対応可能です。
当社の CNC へら 絞り サービスで迅速なプロトタイプの作成について、今すぐお問い合わせください。こちらでチャットして直接見積もりを取得するか、無料のプロジェクトレビューをリクエストしてください。