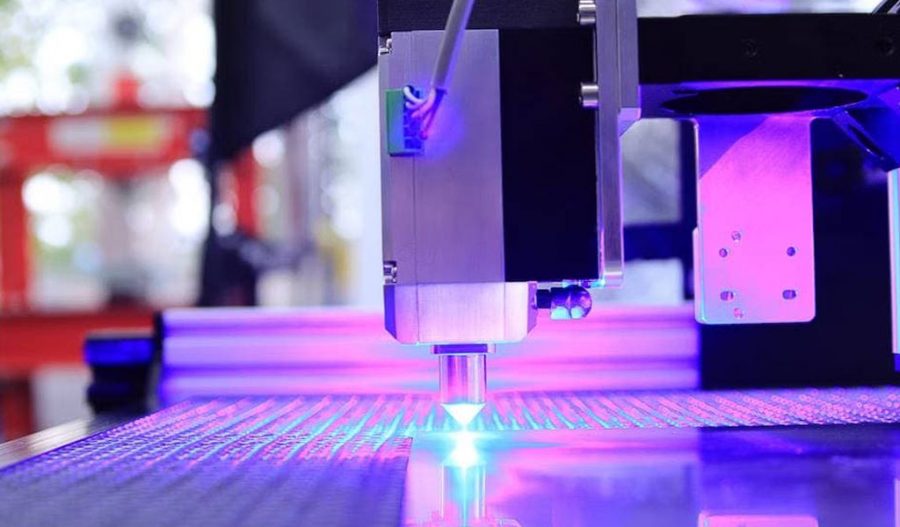
レーザー切断の人気はここ数十年で急上昇し、今では国際貿易に欠かせないものとなっています。レーザー切断は、製造業から医療まで、無限とも思える分野で使用されています。レーザー切断製品は、考えられるあらゆる店で入手できます。マイクロチップのシリコンはレーザーで切断され、矯正眼科手術はレーザーで行われ、ロケット船の貨物はレーザーで製造されています。
しかし、レーザー切断については、一般の人々にまだ知られていない情報が数多くあります。そのメカニズムと機能とはどのようなものでしょうか。どのような用途に使用できるのでしょうか。個人または企業として、レーザー切断法からどのようなメリットが得られるのでしょうか。
ここでは、レーザー切断について知りたいことすべてを学ぶことができます。レーザーカッターの仕組みの基本から、さまざまな用途まで、学ぶべきことはたくさんあります。幸いなことに、この技術は、手で操作するのと同じくらい、脳でも簡単に理解できます。
レーザー切断はどのように機能しますか?
レーザー切断機は、コンピューターの代わりに高出力レーザーを使用して、CNC マシンと同じ機能を実行できます。レーザーは、CNC および光学機械を通過する材料またはビームのレールとして機能します。CNC または G コードは、材料を切断するときにマシンを誘導します。
レーザーを物体に照射すると、レーザーは溶け、蒸発し、燃えます。ガスジェットを使用して材料を吹き付けると、滑らかで仕上げられたエッジが作られます。レーザー光は密閉された容器内で生成され、ランプまたは放電によって活性化されます。
発光物質から発せられる光は、その一部を反射することで増幅されます。このプロセスを繰り返すことで、単一色のコヒーレント光線が出現します。鏡や光ファイバーは光を集中させ、小さな点を非常に明るくすることができます。
レーザー ビームの最も狭い部分の直径は 0.32 ミリメートル未満です。逆に、必要に応じて、切開幅は 0.10 ミリメートルというさらに小さな幅で済みます。ただし、答えは材料の厚さによって異なります。レーザー カッターを使用して材料を端からではなく中心から外側に向かって切断する場合は、穿孔手順が使用されます。
レーザー切断の技術と方法
レーザーカッターは、集中した熱や光を使用して対象材料を蒸発させたり溶かしたりする切断ツールです。ただし、このパワーを伝達する方法はさまざまです。
レーザー切断の一般的な用途は次のとおりです。
火炎切断
レーザー炎切断は、酸素アセチレン切断とは異なり、切断プロセスを助けるために酸素を使用します。発熱酸化反応を発生させることで、レーザーエネルギーの必要性を低減します。溶融した材料は、酸素を使用して切断部から物理的に吹き飛ばされます。この方法は、「反応性レーザー切断」と呼ばれます。
熱応力骨折
ベース材料に応力を発生させて切断する方法は、熱応力破壊です。窒化アルミニウムを切断するために使用される技術の 1 つは、アイテムの表面で非常に薄い層の材料を溶かして酸化アルミニウムを生成することです。熱膨張率が異なるため、酸化アルミニウムとベース窒化アルミニウムは応力場を引き起こし、異なる速度で冷却すると、レーザー ラインに沿って部品に亀裂が生じます。
レーザーラスタリング
さまざまな素材に画像を彫刻する場合、レーザー ラスタリングが最適な方法です。この方法では、ビットマップを取得し、それをレーザー カッターが実行できる指示に変換します。次に、レーザーが画像を素材の表面に永久的に焼き付けます。
レーザー ラスタリングの精度と適応性により、非常に精細な芸術作品を作成できます。この方法では、木材、金属、ガラス、石など、あらゆる素材に優れた彫刻を施すことができます。レーザー ラスタリングは複雑な画像を複製できるため、彫刻プロジェクトに最適な方法として登場し、芸術的表現と最先端の精度の理想的な融合を実現しています。
フュージョンカット
レーザー光線で材料に切断を行う際、アルゴンや窒素などの不活性ガスの高圧ジェットを使用して溶融材料を吹き飛ばし、きれいな切断面を作ります。ガスは溶融金属に注入されるため、不活性でなければなりません。不活性ガスはシールドガスとしても機能し、溶融端を外部の力から保護します。
リモートカット
リモート カッターを使用して薄い素材や繊細な素材を切断する方法は、昇華または蒸発とも呼ばれ、一般的です。レーザーによる切断ではガスが不要で、最も一般的にはガルボ スキャナーを使用して、ミラー セットを介してレーザーを目的の方向に移動させます。ガスの代わりに、レーザーが素材を蒸発またはアブレーションします。薄い素材のリモート切断は非常に高速です。
ベクターカット
「ベクター切断」形式のレーザー切断は、直線の幾何学的線を持つコンポーネントに対して実行されます。商業広告看板がその良い例です。レーザーは通常、きれいな直線の切断を行います。
レーザー切断の種類
切断に使用されるレーザーには主に 3 種類あります。これらのレーザーには、二酸化炭素 (CO2)、ネオジム イットリウム アルミニウム ガーネット (Nd:YAG)、ファイバーがあります。これらは、レーザー光が放射される材料によって区別されます。
二酸化炭素レーザー
このタイプのレーザーは、ヘリウム、水素、キセノン、および少量の二酸化炭素 (10 ~ 20%) で構成されるガス放電媒体を使用します。レーザーを「ポンピング」するために、光ではなく放電電流が使用されます。
放電が光源を通過すると、そこにある窒素分子のエネルギー レベルが上昇します。前述のように、励起された窒素分子は光子の放出によるエネルギー損失を受けません。
代わりに、振動モードを使用して CO2 分子にエネルギーを与えます。この手順は、CO2 分子の大部分が輸送可能な段階に入るまで繰り返されます。二酸化炭素分子は 10.6 または 9.6 ミクロンの赤外線を放射し、エネルギーを減らします。
このため、共振ミラーは、これらの特定の波長の光を適切に反射するように作られています。ミラーは、材料を切断するために使用された赤外線ビームを逃がす部分反射器の一種です。
赤外線が消散すると、エネルギーはドープされたヘリウム原子に伝達され、CO2 分子は基底状態に戻ります。その後、レーザーの冷却システムにより、冷えたヘリウム原子は元の温度に戻ります。他のレーザーと比較すると、CO2 レーザーの効率は約 30% と大幅に高くなっています。
ファイバーレーザー
ファイバーレーザーは、レーザー業界における比較的最近のイノベーションであり、ガス(CO2 レーザー)や結晶ではなく光ファイバーを介して光が放射されます。ファイバーレーザーは、結晶レーザーと同様に、光ファイバーを使用して光を放射する固体デバイスです。
エルビウムとイッテルビウムは光ファイバーに添加される元素の 1 つです。エルビウムが放出する光の波長は 1528 ~ 1620 nm です。イッテルビウムが放出する光の波長は 1064 nm、1030 nm、1080 nm です。
光ファイバーはエネルギーの損失が無視できるほど少ない状態で光を伝送できることはよく知られています。そのため、光ファイバーは、正確な位置決めを必要とする他の素材よりも信頼性が高いのです。
クリスタル(ルビー、ND、ND-YAG)レーザー
CO2 レーザーとは対照的に、このレーザーは合成結晶が発光媒体として機能する固体デバイスです。1% のイオン化ネオジム (Nd3+) を含む YAG (Y3Al5O12) 結晶が最もよく使用されます。
結晶構造では、Y イオンが Nd イオンに置き換えられています。各ロッドの直径は 6 ~ 9 センチメートル、長さは 10 センチメートルです。共振器システムは、端に高反射コーティングが施された YAG ロッドで構成されています。
レーザー ポンピングは、クリプトン フラッシュまたはレーザー ダイオードを使用して実行できます。ネオジム イオンは、レーザー ポンピングによって高エネルギー レベルに励起されます。励起されたネオジム イオンは、最終的により低く安定した状態に戻り、光の放射を停止します。このプロセスは、励起された Nd イオンが媒体全体に広がるまで続きます。劣化した Nd イオンからは、1064 nm の赤外線波長が放射されます。
レーザー切断の利点
より手頃な価格で低コスト
レーザー技術の利点の 1 つは、レーザー切断が同等の CNC マシンよりもコスト効率が高いことです。レーザー切断技術のおかげで、特殊なツールは不要になりました。特殊な切断ツールは不要なので、特定のプロジェクトで使用するために機器を適応させる必要がありません。
また、直接接触がないため、摩耗もありません。レーザー切断機は他の加工技術に比べて可動部品が少ないため、メンテナンスの手間が少なくて済みます。また、従来の製造方法に比べて、機械の運用コストも低くなります。
シートの使用率が高く、無駄が最小限
レーザー切断では、厚い材料を切断する際に発生する廃材が最小限に抑えられます。このため、大量の材料を切断する場合、レーザー切断は他の方法よりも優れています。レーザー カッターを使用すると、工場は原材料を最大限に活用できます。材料の無駄が減り、リソースをより効率的に使用することで生産コストが削減されます。
低消費電力
実際にカットしたい場合は、パワーが大きければ大きいほど便利です。一方、レーザー切断機には他の可動部品がないため、消費電力は大幅に少なくなります。ただし、可動部品のある機械は通常、エネルギー要件が高くなります。さらに、レーザー カッターはあらゆる材料を素早く切断できます。エネルギーと時間の両方の必要性が減ります。エネルギー使用量が減ると、運用コストも削減されます。
正確さと高精度
材料を正確に切断するために、レーザーは光線を集中させます。レーザーのパワーと小型さは、材料を正確に溶かしたり蒸発させたりするのに理想的です。レーザーの許容範囲は通常、0.003 mm ~ 0.006 mm です。
プラズマ カッターの許容レベルはレーザー カッターよりも高く、約 0.02 mm です。他の切断ツールの許容レベルも最大 3 mm です。工場では、非常に高い精度と精密さを備えた機械が必要です。
この目的にはレーザーカッターが一般的に使用されます。レーザー切断では精密な測定が必要となるため、航空宇宙産業で広く使用されています。
非常に困難な仕事の場合
レーザー切断機は材料の最も小さなエッジでも加工できるため、他の切断技術では難しい多くの作業を簡素化できます。レーザー カッターを使用すると、複雑な形状を素早く製造できます。ただし、切断領域がわずかに歪んだりねじれたりする場合があります。レーザー切断は許容範囲が柔軟で、多くの材料に使用できます。
被害防止
レーザー切断は、最も薄い材料でも損傷のリスクを最小限に抑えられるという利点があります。多くの人は、この装置を使用すると材料が変形したり劣化したりすることが避けられないという誤った印象を持っています。
レーザー切断プロセスには高熱が必要であるという誤解がよくあります。熱は許容範囲には影響せず、材料のごく一部にしか影響しません。シートは記録的な速さでレーザー切断できるため、製造時間が短縮されます。そのため、製造中の反りや歪みは簡単に回避できます。
レーザー切断の欠点
火災の危険性
レーザーカッターは、放出する光によって近くの可燃物が危険なレベルまで加熱される可能性があるため、火災の危険があります。
危険な粉塵や煙を発生させる
作業者と産業機器の安全を確保するには、これらを作業スペースから適切に除去する必要があります。
マスター、少し時間がかかるかもしれません。
レーザーカッターは、さまざまな設定とそれがカットに与える影響について学ぶべき情報が膨大であり、設定の数も非常に多いため、使いこなせるようになるまでには時間がかかるかもしれません。
高価になるかもしれない
レーザーカッターへの初期投資は多額になる可能性があり、運用コスト(消費電力など)も急速に増加する可能性があります。
かなりのメンテナンスが必要
ミラーとレンズは清潔に保ち、調整し、専門家によって定期的に調整する必要があります。
レーザー切断の応用
すでに述べたように、レーザー切断の分野は絶えず発展している魅力的な分野です。
レーザー切断の最も一般的な現在の用途のいくつかを以下に示します。
自動車産業
レーザー切断は、複製部品を製造する際のスピードと精度に優れているため、自動車分野でも利用されています。自動車業界では、さまざまな形状やサイズの部品を正確に複製することが不可欠です。レーザーで金属やプラスチックを切断して、自動車のパネル、ボタン、電子部品を製造します。
レーザー切断機は、車内のボタンに彫刻を施して光を取り入れたり、シリアル番号や部品番号を永久に記録したりすることもできます。レーザーは、さまざまな部品の製造に使用する金型を切断することもできます。
ハイドロフォーム部品はレーザーカッターで切断できます。これらは通常、車両の構造的サポートを提供する固体チューブです。これらの部品は、エンジン フレームや計器パネルによく使用されます。
シリコン製造
シリコンには多くの用途があり、レーザー切断に適した材料の 1 つです。エンジニアは精密切断を使用して、他の切断方法で製造されたものよりもサイズの小さいシリコン部品を作成できます。
シリコンは高温に耐えることができ、時間が経っても劣化しません。さらに、非常に柔軟性があります。シリコンが最もよく使われるのは、電子機器、コンピューター、繊維、家庭用品、車両、建築資材などです。
金型および工具業界
前述のように、レーザー切断を使用して複製部品の金型を作成できます。レーザーはさまざまな深さで金属を切断できるため、信頼性の高いダイカットプロセスで、打ち抜き部品の正確な金型を作成し、繰り返し再利用できます。
レーザーカットによる金型コピーは、高速かつ正確な複製方法です。射出成形金型の精度は、レーザーカットで作られた金型の精度に匹敵します。
これにより、金型製作プロセスが合理化され、より迅速かつ低コストで、より正確に金型を複製できるようになります。
レーザー カッターは、自動車部門のマーキングや彫刻から単純な手工具の製造まで、工具業界で幅広い用途に使用されています。レーザー カッターは効率性が高いため、硬い金属の打ち抜きよりも優れている場合があります。ゴムは非常に適応性が高いため、ほとんどの工具のハンドルに会社のロゴやレーザーで刻印された情報を入れることができます。
セラミック製造
エンジニアは、さまざまな状況でセラミックの幅広い特性を活用できます。セラミックは熱伝導率と電気伝導率が低いため、優れた絶縁体になります。融点が高く、非常に丈夫で、他の化学物質と反応しません。
レーザーは、切断品質を損なうことなくセラミックを素早く切断するために頻繁に使用されます。セラミック部品は、ジェットエンジンモーター、電気モーター、スピーカー、発電機、ヘッドフォン、炊飯器、さらには白熱電球など、さまざまな機械や機器に使用されています。
結論
レーザー切断は国際貿易に不可欠な要素となり、製造、医療、ロケット船の貨物などさまざまな分野で使用されています。レーザー切断の人気はここ数十年で急上昇し、マイクロチップ シリコン、矯正眼科手術、ロケット船の貨物に使用されています。レーザー切断は、さまざまな技術と方法で、集中した熱または光を使用して対象材料を蒸発または溶解することで機能します。一般的な用途には、火炎切断、熱応力破壊、レーザー ラスタリング、融合切断、リモート切断、ベクター切断などがあります。
切断に使用されるレーザーには、二酸化炭素 (CO2)、ネオジム イットリウム アルミニウム ガーネット (Nd: YAG)、ファイバーの 3 つの主な種類があります。二酸化炭素レーザーは、ヘリウム、水素、キセノン、少量の二酸化炭素 (10 ~ 20%) で構成されるガス放電媒体を使用します。レーザーは振動モードを使用して CO2 分子にエネルギーを与え、そのエネルギーを減らします。ファイバー レーザーは、エルビウムとイッテルビウムが光ファイバーにドープされた光ファイバーを介して光を放射します。
結晶レーザーは、合成結晶を使用して光を発する固体デバイスであり、イオン化されたネオジム (Nd3+) を 1% 含む YAG (Y3Al5O12) 結晶が最もよく使用されます。これらのレーザーはエネルギー損失がごくわずかであるため、正確な位置決めが必要な他の材料よりも信頼性が高くなります。
要約すると、レーザー切断は、製造、医療、ロケット船の貨物など、さまざまな分野で使用できる多用途で多機能なツールです。レーザー切断のメカニズム、技術、およびアプリケーションを理解することは、個人にとっても企業にとっても不可欠です。レーザー切断は、結晶構造内の Y イオンをネオジムイオンで置き換える切断技術です。これらのネオジムイオンはより高いエネルギーレベルに励起され、融点が高くなり、摩耗が減少します。レーザー切断機は可動部品が少なく、従来の製造方法よりもメンテナンスが少なく、運用コストが低くなります。
レーザー切断は、同等の CNC マシンよりも手頃で低コストであるため、特殊なツールが不要になり、摩耗が軽減されます。また、シートの使用率が高く、廃棄物が最小限に抑えられるため、大量の材料を切断する場合、他の方法よりも優れています。レーザー切断機は消費電力が低いため、より効率的でコスト効率に優れています。
レーザー切断は、許容範囲が 0.003 mm から 0.006 mm の範囲で、材料の溶解と蒸発に最適です。航空宇宙産業では精密測定に広く使用されており、非常に困難な作業に適しています。複雑な形状の製造にも使用できますが、切断領域がわずかに歪んだりねじれたりすることがあります。
しかし、レーザー切断には、火災の危険性、危険な粉塵や煙の発生、熟練するまでに時間がかかる、費用がかかる、定期的なメンテナンスが必要であるなどの欠点があります。
レーザー切断の分野は絶えず発展しており、自動車産業、半導体製造、金型およびツール、セラミック製造などの分野で応用されています。自動車産業では、レーザー切断はさまざまな形状とサイズの複製部品の製造に使用され、金型およびツール産業では、レーザーカッターは打ち抜き部品の精密な金型を作成するために使用されます。
セラミック製造業界では、レーザーカッターを使用して、切断品質を損なうことなくセラミックを迅速に切断しています。これらの材料は、ジェットエンジンモーター、電気モーター、スピーカー、発電機、ヘッドフォン、炊飯器、白熱電球など、さまざまな機械や機器に使用されています。
ツーリングとCNCの絞り加工能力を最大化する
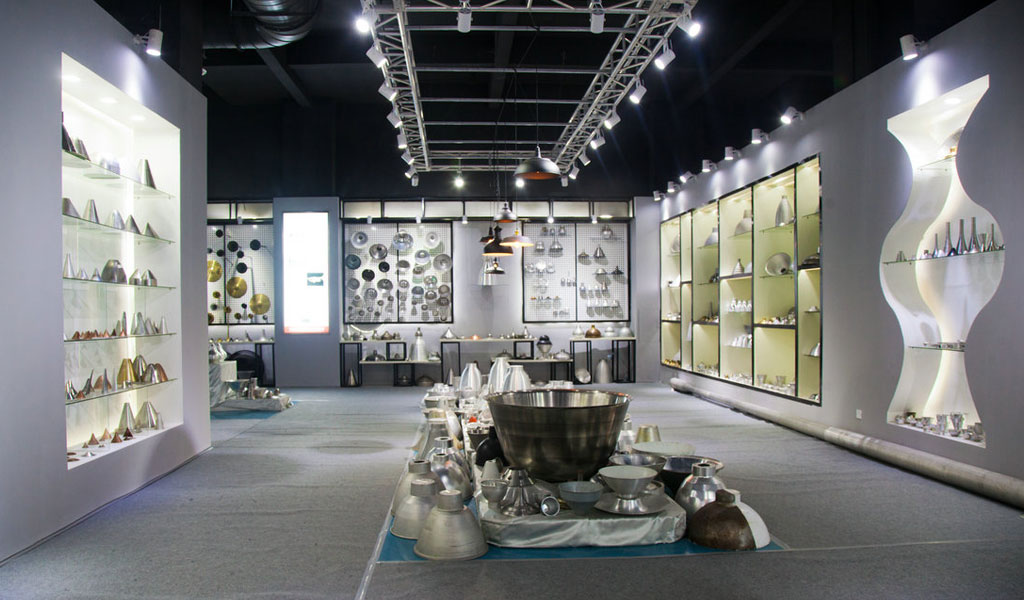
BE-CU 中華のへら 絞り 会社では、過度の摩耗やストレスの兆候を監視しながら、設備を最大限に活用しています。さらに、より新しい最新の設備を検討し、製造能力をサポートまたは向上できる設備に投資しています。当社のチームは機械やツールに細心の注意を払っているため、部品の品質と生産性に悪影響を与えないように定期的にメンテナンスも行っています。
BE-CUの設計とエンジニアリングサポート
BE-CUは、社内の設計およびエンジニアリングチームを活用して、部品生産の初期コンセプトからお客様を支援することができます(提供された設計に対して広範な設計サポートも提供可能です)。私たちのチームは、プロジェクトの開始から終了まで、お客様と定期的かつ透明なコミュニケーションを取りながら、望ましい最終目標に向かって作業を進め、明確な進行方向を提供します。
BE-CUの設計およびエンジニアリングサポートプロセスの一例:
- クライアントがBE-CUチームに部品図面を提供します。
- 当社のエンジニアリングチームが図面をレビューし、ベストプラクティスに基づいて調整を行います。お客様のニーズに応じて、成形または絞り部品を最も効果的に達成する方法を推奨します。
- 図面と設計は必要に応じて改訂され、完璧な形に仕上げられます。財務的な実行可能性も最優先事項として考慮されます。
- 主要な目標は、全ての部品の適合性、形状、機能性を実現することです。
- 研究開発は製造プロセスの重要なステップであり、BE-CUは概念実証や様々な検証要件のためにプロトタイピングサービスを提供しています。研究開発プロセスにおける金属成形については、当社のeBookをご覧ください。
BE-CUが提供する広範な社内サービス
この金属加工プロセスは、軸対称の高性能部品を製造します。スピン成形とも呼ばれ、材料を望ましい形状に切削するのではなく、金属ディスクまたはチューブを円錐形やその他の円形に変形させます。
へら絞りは、手動の手作業によるスピニングプロセスまたは自動CNCスピニングを使用します。BE-CUのへら絞り機能の利点には以下が含まれます:
- コスト削減
- 短いリードタイム
- 最大の設計柔軟性
- シームレスで高品質な構造
対応可能な金属には、ステンレス鋼、炭素鋼、アルミニウム、銅、インコネル、ハステロイ、チタン、ブロンズ、真鍮が含まれます。BE-CUは、センター間60インチから直径100インチまでのカスタム金属絞り部品を製造でき、材料の厚さは0.018インチから2.00インチまで対応可能です。
当社の CNC へら 絞り サービスで迅速なプロトタイプの作成について、今すぐお問い合わせください。こちらでチャットして直接見積もりを取得するか、無料のプロジェクトレビューをリクエストしてください。