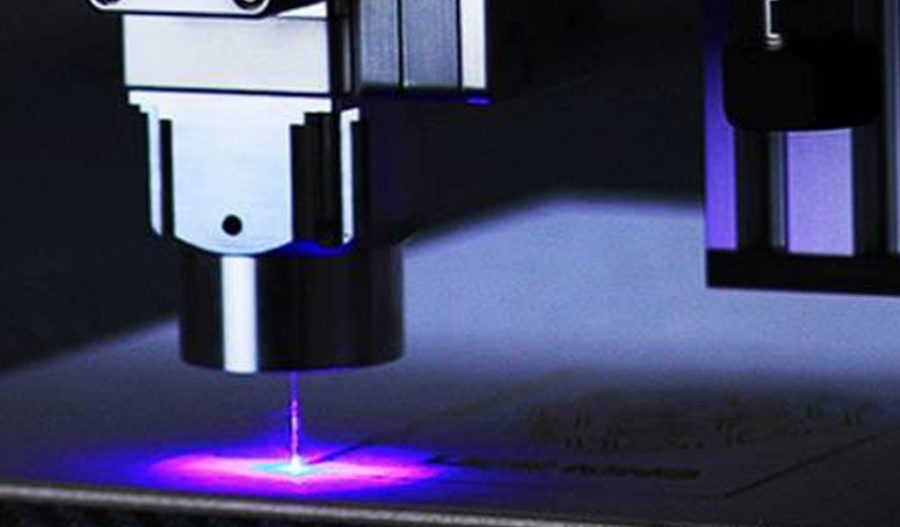
レーザー切断とプラズマ切断は、精密な切断を実現するためにさまざまな業界で使用されている 2 つの一般的な技術です。方法によって長所と短所が異なるため、その違いを理解することが重要です。
企業は、レーザー切断とプラズマ切断の利点を比較し、ニーズに合った最適な方法を決定することで、知識に基づいた決定を下すことができます。この情報を使用して、切断プロセスを微調整し、さまざまな産業環境で精度、効率、成功を向上させることができます。
このブログでは、レーザー切断とプラズマ切断を比較し、それぞれの利点、欠点、用途について説明します。これにより、十分な情報に基づいた決定を下すことができます。
レーザー切断とは何ですか?
レーザー切断は、集中した強力な光線を利用して金属を切断する方法です。この切断方法では、レーザー光学系とコンピュータ数値制御 (CNC) で金属を加熱して部分的に蒸発させます。強力なガス ジェットにより、浮遊した金属粒子を除去し、滑らかな表面を残すこともできます。
レーザー切断を使用すれば、さまざまな金属をきれいで正確に切断できます。多くの現代の製造業では、このコンピューター制御の方法を使用して、細かい部分を彫刻したり、複雑な切り込みを入れたり、正確な形状を切断したりすることが一般的です。部品が単純なものでも複雑なものでも、製品の成功に精度が不可欠な場合は、レーザー切断が非常に役立ちます。
レーザー切断の利点
スピード
レーザー切断と比較すると、従来の機械切断に必要な時間は、特に難しい切断の場合、はるかに長くなります。
切断速度の点では、厚さ約 10 mm までであれば、レーザーはプラズマ切断や火炎切断などの他の熱切断方法よりも優れています。ただし、利点の正確な点はレーザー カッターの強度によって異なります。
物質汚染なし
ロータリーカッターを使用して材料を加工する場合、冷却剤を使用するのが一般的です。切断された部品は冷却剤で汚染される可能性があり、脱脂が必要になります。研削プロセス中に冷却剤または潤滑剤が必要になる場合があります。研削ホイールのアブレーションは自然に発生しますが、多くの製品に危険な炭化粒子が残ります。ウォーターカッターを使用すると、ガーネットの粉塵も残ります。レーザー切断ではエネルギーとガスのみが使用されるため、材料が汚染されることはありません。
柔軟性
レーザー切断では、切断の合間にツールを切り替える必要がないため、生産が高速化され、ダウンタイムが短縮されます。同じセットアップで同じ厚さの材料からさまざまな形状を切断できるため、生産性が向上し、セットアップ時間が短縮されます。
レーザー切断は、直線、曲線、複雑なパターンのいずれにも同様に有効です。レーザー ビームの精度の高さにより、最も複雑な切断も簡単に行うことができます。レーザー切断は適応性に優れているため、特に精密な切断やデザインが求められる作業によく使用されます。
多様な素材
アクリルやその他のポリマー、チタン、軟鋼、ステンレス鋼、タングステンは、レーザー切断を使用して効率的に切断できる多くの材料のほんの一部です。この汎用性の高い技術は、さまざまな材料の切断に適応できます。技術の進化により、この適応性は高まっています。
たとえば、炭素繊維強化複合材を切断するには、繊維と接着剤の両方に適合した周波数のレーザーが必要です。
低消費電力
今日の競争の激しい市場では、企業は常に効率性を向上させる方法を模索しています。この点で、レーザー切断は非常に有用です。レーザー切断機は、従来の切断方法で使用される約 50 キロワットから大幅に削減された約 10 キロワットの電力しか使用しません。このエネルギー使用量の削減は、持続可能性の目標と一致しており、関連コストと環境への影響を削減するという追加の利点があります。
レーザー切断は、企業の効率性を高め、運用コストを削減し、環境に良い影響を与えることができるため、よりスマートで持続可能な製造方法を追求する上で有望な選択肢です。
レーザー切断の欠点
エネルギー
レーザー切断の主な欠点は、レーザー ビームを生成するために大量のエネルギーが必要になることです。電力要件と効率は、切断の性質と使用するレーザーによって大きく異なります。
一方、レーザー技術の急速な進歩を考えると、この欠点は近い将来に修正される可能性が高いでしょう。
危険なガス
プラズマ切断などの熱的方法を使用して材料を切断すると、材料が溶けてガスが放出され、有毒な臭いが発生する場合があります。これは、プラスチックを扱う場合に特に当てはまります。作業中の従業員の安全を確保するには、しっかりとした換気システムが不可欠です。
切断作業では大量の煙や悪臭が発生します。優れた換気システムは高価ですが、それを取り除くことは不可欠です。切断作業による労働者の健康への危険を減らすために、企業は労働者の安全を最優先し、作業場に適切な換気システムを設置する必要があります。
材料の厚さの制限
レーザー カッターの一般的な出力は約 6 キロワットです。最大約 12 mm の厚さの金属しか切断できず、切断速度も非常に遅い (約 10 mm/秒) です。切断の物理的限界に達するには、最大で最も強力な機械が必要です。ただし、ウォータージェット切断とワイヤ放電切断にはどちらも限界があります。これら 3 つの方法はすべて、他の方法よりも速く、より深い切断を実現します。
生産率が一定しない
レーザー切断は柔軟性のある切断方法ですが、すべての金属に使用できるわけではありません。たとえば、銅やアルミニウムなどの金属は反射率と熱伝導率が高いため、レーザー切断には適していません。
レーザー切断の生産速度も、状況によって大きく変動することがあります。レーザーで切断する材料の種類によって、切断速度、ワークピースの厚さ、使用するパラメータが変わります。生産性を最大限に高め、望ましい切断結果を得るには、これらの要因とその影響をしっかりと把握することが重要です。
専門知識が必要
レーザー カッターの機能を最大限に活用するには、資格を持った専門のオペレーターが不可欠です。レーザー カッティング マシンを最大限に活用するには、何をすべきかを知っておく必要があります。熟練したオペレーターは、マシンのパラメータを微調整して、最先端の機器を購入した人が設定した基準を満たすカッティングを実現できます。
正確で高品質なカットは、まずレーザーカッターを正しく設定して初めて可能になります。設定には、出力、速度、焦点の調整が含まれます。企業は、この革新的な機器を最大限に活用する方法を知っている熟練したオペレーターに任せることで、この機器を最大限に活用できます。
プラズマ切断とは何ですか?
プラズマ カッターで金属を切断するには、いくつかの手順が必要です。溶融法を採用したプラズマ切断では、正確な結果が得られます。イオン化されたガス、つまりプラズマが金属を溶かし、放出します。ステンレス鋼、銅、アルミニウム、鋼、真鍮などの金属は、圧縮空気によってプラズマで吹き付けられ、窒素や水素などの不活性ガスがノズルから非常に高速で噴射されます。この切断方法は、自動車の修理や産業建設および製造など、さまざまな用途に使用されています。
プラズマ切断の利点
切断速度
プラズマ切断は、他の切断方法と比べ、切断速度が非常に速いという点で際立っています。プラズマアークは強力なイオン化ガスのジェットを生成し、さまざまな導電性材料を迅速かつ正確に切断できます。プラズマ切断は、鋼鉄、アルミニウム、ステンレス鋼を迅速かつ容易に切断するのに特に効果的です。プラズマ切断は、その超高速切断速度により、迅速かつ効率的な切断を必要とする作業に最適なオプションであり、企業の生産性向上、ターンアラウンド時間の短縮、最も厳しい納期の遵守にも役立ちます。
厚物切断
厚い材料を切断する場合、プラズマ切断が明らかに勝者です。プラズマ切断は、高速プラズマジェットを生成するため、他の切断方法では難しいかもしれない厚い金属板を切断することができます。プラズマ切断は、厚い金属を正確に切断できるため、工業用途に最適です。
プラズマ切断の精度とスピードは、硬い材料を切断することが日常的に行われる建設、造船、金属加工に最適です。信頼性が高く多用途の切断ソリューションを必要とする業界にとって、厚い金属を処理できるプラズマ切断は優れた選択肢です。
熱衝撃
プラズマ切断は、他の熱ベースの切断方法と同様に、熱を発生させます。ただし、他の熱ベースの切断方法と比較すると、プラズマ切断は周囲の材料への熱の影響が大幅に小さく、これは明らかな利点です。
熱による変形が起こりやすい薄い材料を切断する場合、熱の影響が軽減されるため、歪みや反りが発生する可能性が低くなります。プラズマ切断は、切断プロセス中に材料が損傷したり反ったりする可能性が大幅に軽減されるため、薄い材料をきれいかつ正確に切断する必要がある作業に強く推奨されます。
使いやすさ
プラズマ切断機は、オペレーターのことを考えて作られているため、操作が簡単です。この使いやすさにより、さまざまなスキルレベルの人が効果的に機械を操作できます。
切断工程の自動化により、毎回きれいで正確な切断が可能になります。
自動化により、オペレーターは一貫した切断を実現できます。これにより生産性が向上し、新しい切断方法の習得期間が短縮されます。このユーザーフレンドリーな操作性により、生産性が向上するだけでなく、変動する生産需要への対応や新入社員のトレーニングも容易になります。プラズマ切断機は、オペレーターにわかりやすいインターフェイスと自動化機能を提供し、切断プロセスの標準化と効率化を促進します。
プラズマ切断の欠点
高価な機器が必要
プラズマ切断にはいくつかの欠点がありますが、最も顕著なのは必要な機器のコストが高いことです。プラズマ切断に必要な主な機器は、プラズマトーチ、エアコンプレッサー、電源です。エアコンプレッサーがすぐに手に入らない場合は、これらの部品は比較的安価です。プラズマトーチの先端や電極などの消耗品のコストを考慮することも重要です。
これらの消耗品は定期的に交換する必要があり、全体的な運用コストが増加します。したがって、プラズマ切断機の購入とメンテナンスのコストについて考えることが重要です。これらのコストを考慮しても、速度と厚さの容量を重視する業界では、プラズマ切断が価値のある選択肢となるでしょう。
有害廃棄物を生産する
プラズマ切断では危険な廃棄物が発生することも欠点の 1 つです。プラズマ切断で使用されるイオン化ガスには、オゾンや一酸化炭素などの有毒ガスが含まれています。適切な換気が行われないと、これらの化学物質が空気中に放出され、付近の人々に健康被害をもたらす可能性があります。使用済みのプラズマ トーチ消耗品にも化学物質が含まれており、安全に処分する必要があります。
薄い素材に限定
プラズマ切断は薄い材料にしか使用できないのが主な欠点の 1 つです。プラズマ切断では、イオン化されたガスの細く高速な流れを使用するため、厚い材料の切断は困難です。たとえば、厚い金属を切断する必要がある場合は、酸素燃料切断を使用します。
各方法を比較する際に考慮すべき要素
プラズマ切断とレーザー切断のどちらを選択するかを決める際には、次の要素を考慮することが重要です。
切断能力
プラズマ カッターは、厚い金属板を切断する能力に優れているため、工業用途に適しています。一方、レーザー マシンは、精度が高く、複雑なデザインを作成できるため、薄い金属の加工に最適です。レーザー切断は、小さくて正確な切断が必要な場合に優れており、プラズマ切断は、大きくて単純な切断が必要な場合に優れています。
企業が各切断方法の利点を把握していれば、材料の厚さと希望する切断要件に基づいて、作業に最適な方法を選択できます。
効率とスピード
レーザー切断は、薄い材料を扱うときに、迅速かつ正確な切断を実現することで、速度面で有利です。一方、プラズマ切断は、材料の厚さに関係なく切断速度が安定しているため便利です。コンピュータ数値制御 (CNC) システムにより、レーザー切断およびプラズマ切断プロセスの精度と生産性が向上します。
CNC 技術により、オペレーターはより高速で一貫性のある切断を行えるようになり、生産速度が上がり、生産性が向上します。企業は、レーザーおよびプラズマ切断オプションを備えた CNC システムを組み込むことで、さまざまな切断アプリケーションで正確で効率的、かつ信頼性の高い結果を達成できるようになります。
適切な材料
プラズマ カッターは鋼鉄、アルミニウム、銅などの導電性材料にしか使用できませんが、レーザー カッターは木材、ガラス、プラスチックなどにも使用できます。CO2 レーザーで反射性材料を切断すると、レーザー ビームが反射するため、悲惨な結果になる可能性があることを覚えておくことが重要です。
レーザーでさまざまな材料を切断できる能力は、多くの分野で新しい使用の可能性を切り開きます。作業に適した切断技術を選択するには、両方のアプローチの長所と短所を知る必要があります。
予算の制約
プラズマ切断とレーザー切断のどちらを選ぶか決める際は、コストを考慮することが重要です。レーザー切断装置の初期投資は、通常、プラズマ切断機よりも高額です。初期投資は高額ですが、レーザー切断の精密さにより、材料の無駄が少なくなり、生産性が向上します。初期費用が低いため、予算が限られている業界では、プラズマ切断への切り替えを検討する必要があります。
切断品質
カットの精度について考えてください。レーザーカットでは、通常、きれいなバリのないカットと磨かれたエッジが得られます。プラズマカットでは、エッジが少し不均一になる場合があります。方法を決定するときは、カットピースの仕上げとエッジの品質に関して、望ましい結果について考えることが重要です。
結論
レーザー切断とプラズマ切断は、さまざまな業界で精密切断によく使用される 2 つの技術です。レーザー切断は、集中した強力な光線を使用して金属を切断する方法ですが、プラズマ切断は溶解法を使用します。金属を溶かして排出することで、正確な結果が得られます。プラズマ切断は、ステンレス鋼、銅、アルミニウム、鋼、真鍮などの導電性材料を切断するのに特に効果的です。
レーザー切断は従来の機械切断よりも高速で、厚さ約 10 mm まで切断できます。また、切断の合間にツールを切り替える必要がないため柔軟性が高く、生産性が向上し、セットアップ時間が短縮されます。直線、曲線、複雑なパターンにも同様に機能するため、正確な切断やデザインが求められる作業に最適です。
レーザー切断は、切断の合間にツールを切り替える必要がないため柔軟性が高く、生産速度が速くなり、ダウンタイムが短縮されます。直線、曲線、複雑なパターンにも同様に機能するため、正確な切断やデザインが求められる作業に最適です。
しかし、レーザー切断には、エネルギー消費、危険な煙、材料の厚さの制限、生産速度のばらつきなど、いくつかの欠点があります。レーザー カッターを正しくセットアップし、出力、速度、焦点を調整するには、熟練したオペレーターが不可欠です。熟練したオペレーターは、切断する材料に影響を与える要因と使用するパラメータを理解することで、正確で高品質の切断を保証できます。
結論として、レーザー切断とプラズマ切断は、さまざまな業界の企業にとって欠かせない 2 つの技術です。レーザー切断は切断速度が速く柔軟性に優れていますが、生産性を最大化し、望ましい結果を得るには、それぞれの方法の特定のニーズと要件を考慮することが不可欠です。プラズマ切断は、非常に効率的で多用途な切断方法で、厚い材料を扱う必要がある業界に最適です。その超高速切断速度により、企業は生産量を増やし、ターンアラウンド タイムを短縮し、厳しい納期に間に合わせることができます。プラズマ切断は周囲の材料への熱影響が少ないため、建設、造船、金属加工に適しています。その使いやすさと自動化により、オペレーターはきれいで正確な切断を簡単に行うことができます。
しかし、プラズマ切断には、機器や消耗品のコストが高いこと、有害廃棄物が発生することなど、いくつかの欠点があります。プラズマ切断で使用されるイオン化ガスにはオゾンや一酸化炭素などの有毒ガスが含まれており、適切に処分しないと健康に害を及ぼす可能性があります。さらに、プラズマ切断は薄い材料に限られているため、厚い材料を切断するのは困難です。
プラズマ切断とレーザー切断を比較する場合、企業は切断能力、効率と速度、適切な材料、予算の制約、切断品質などの要素を考慮する必要があります。プラズマ切断は小さくて正確な切断に適しており、レーザー切断は大きくて単純な切断に優れています。どちらの方法にも長所と短所があるため、企業が特定のニーズに適した切断技術を選択することが重要です。
結論として、プラズマ切断は、建設、造船、金属加工など、さまざまな業界で使用できる多用途で効率的な切断方法です。その使いやすさ、自動化、汎用性により、厳しい納期を守り、生産性を向上させる必要がある業界にとって最適な選択肢となります。
ツーリングとCNCの絞り加工能力を最大化する
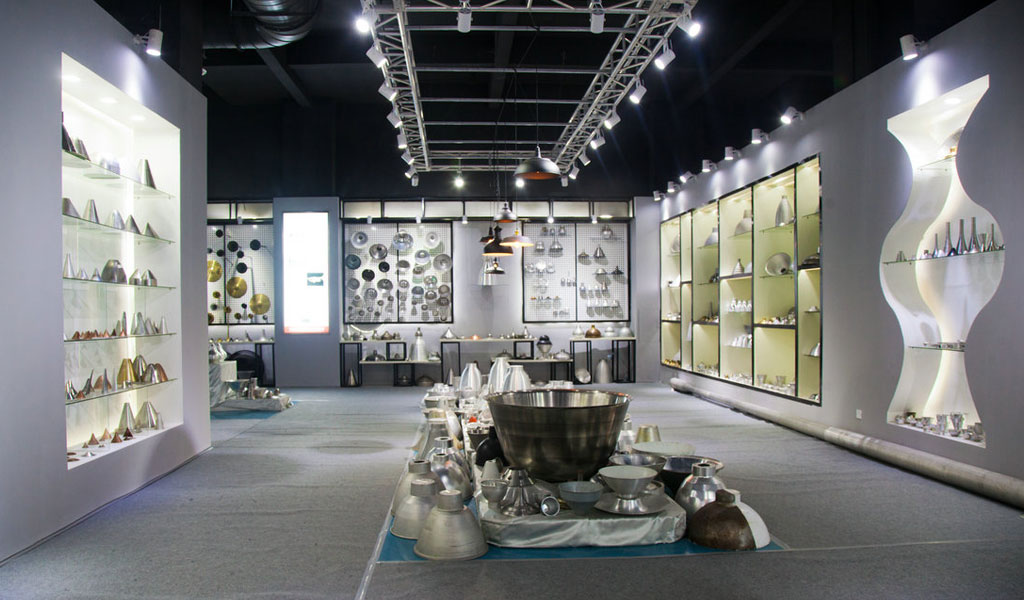
BE-CU 中華のへら 絞り 会社では、過度の摩耗やストレスの兆候を監視しながら、設備を最大限に活用しています。さらに、より新しい最新の設備を検討し、製造能力をサポートまたは向上できる設備に投資しています。当社のチームは機械やツールに細心の注意を払っているため、部品の品質と生産性に悪影響を与えないように定期的にメンテナンスも行っています。
BE-CUの設計とエンジニアリングサポート
BE-CUは、社内の設計およびエンジニアリングチームを活用して、部品生産の初期コンセプトからお客様を支援することができます(提供された設計に対して広範な設計サポートも提供可能です)。私たちのチームは、プロジェクトの開始から終了まで、お客様と定期的かつ透明なコミュニケーションを取りながら、望ましい最終目標に向かって作業を進め、明確な進行方向を提供します。
BE-CUの設計およびエンジニアリングサポートプロセスの一例:
- クライアントがBE-CUチームに部品図面を提供します。
- 当社のエンジニアリングチームが図面をレビューし、ベストプラクティスに基づいて調整を行います。お客様のニーズに応じて、成形または絞り部品を最も効果的に達成する方法を推奨します。
- 図面と設計は必要に応じて改訂され、完璧な形に仕上げられます。財務的な実行可能性も最優先事項として考慮されます。
- 主要な目標は、全ての部品の適合性、形状、機能性を実現することです。
- 研究開発は製造プロセスの重要なステップであり、BE-CUは概念実証や様々な検証要件のためにプロトタイピングサービスを提供しています。研究開発プロセスにおける金属成形については、当社のeBookをご覧ください。
BE-CUが提供する広範な社内サービス
この金属加工プロセスは、軸対称の高性能部品を製造します。スピン成形とも呼ばれ、材料を望ましい形状に切削するのではなく、金属ディスクまたはチューブを円錐形やその他の円形に変形させます。
へら絞りは、手動の手作業によるスピニングプロセスまたは自動CNCスピニングを使用します。BE-CUのへら絞り機能の利点には以下が含まれます:
- コスト削減
- 短いリードタイム
- 最大の設計柔軟性
- シームレスで高品質な構造
対応可能な金属には、ステンレス鋼、炭素鋼、アルミニウム、銅、インコネル、ハステロイ、チタン、ブロンズ、真鍮が含まれます。BE-CUは、センター間60インチから直径100インチまでのカスタム金属絞り部品を製造でき、材料の厚さは0.018インチから2.00インチまで対応可能です。
当社の CNC へら 絞り サービスで迅速なプロトタイプの作成について、今すぐお問い合わせください。こちらでチャットして直接見積もりを取得するか、無料のプロジェクトレビューをリクエストしてください。