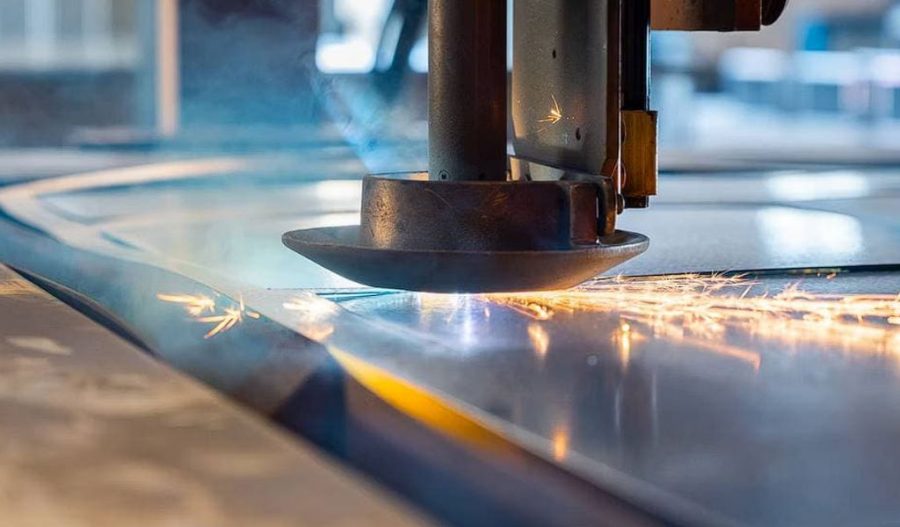
材料の表面微細構造を変化させるには、切断プロセスが必要です。レーザー切断は、機械加工業界でさまざまな材料を切断するために広く使用されています。計画や希望する結果に沿ったパターンを作成するのに役立ちます。この方法では、強力なレーザービームを使用して物質を溶かし、燃焼させ、蒸発させます。レーザー切断には多くの利点がありますが、考慮しなければならない欠点もいくつかあります。
レーザー カッターは、焦点を絞った狭いレーザー ビームを使用して、さまざまな材料をきれいに切断します。デザインやパターンから決定できる明確な目標があって初めて、切断を開始できます。材料によっては、非常に硬くて製造が難しいものもあります。しかし、レーザー カッターの登場により、これは簡単になりました。
このブログでは、レーザー切断について知っておきたいことすべてを説明します。レーザー切断の利点と欠点、およびその動作方法について説明します。
レーザー切断のプロセスとは何ですか?
レーザー切断の基礎を学ぶことは、その利点と欠点について議論する前提条件です。レーザー切断機は、コンピュータ数値制御 (CNC) 機と似た方法で機能しますが、代わりに高出力レーザーを使用します。レーザーは CNC と光学系を使用して、材料またはビームを目的の方向に向けます。提供された CNC または G コードによって材料が切断され、装置の動きが制御されます。
レーザービームを集束させると、溶融、気化、燃焼が起こります。また、材料にガスジェットを吹き付けると、高品質の仕上げエッジ面が得られます。レーザービームは、レーザー材料がランプまたは放電によって励起されると、真空チャンバー内で生成されます。
レーザー材料は、部分的なミラーによって内部反射された後、増幅されます。このプロセスは、十分なエネルギーがコヒーレントな単色光ストリームに蓄積され、放出されるまで続きます。光ファイバーまたはミラーを使用して光を作業スペースに集中させることで、効率が向上します。
レーザー ビームの最も狭いポイントの直径は 0.32 mm 未満です。一方、切り込み幅は 0.10 mm ほど狭くなることがあります。ただし、ここでは物質の厚さが要因となります。レーザー カッターで切断する材料に、切断を開始するためのきれいなエッジがない場合は、ピアシング法を使用します。
レーザーは、ピアシング方式により、強力な力で材料に穴を開けることができます。例えば、13 mm のステンレス鋼板を完全に溶かすのに 5 ~ 15 秒かかります。
レーザー切断の利点は何ですか?
レーザー切断技術を使用すると、さまざまな利点が得られます。次に、これらの利点のいくつかについて説明します。
高精度と精密
レーザーの集中光線により、極めて正確な材料除去が可能になります。レーザーはコンパクトで強力ですが、材料の溶解と蒸発の精度は他に類を見ません。レーザーの許容誤差は通常 0.003 ~ 0.006 mm です。
プラズマ カッターの許容誤差はレーザー カッターよりも大きく (約 0.02 mm) なっています。他の切断ツールでも、同様の 1 ~ 3 mm の許容誤差レベルが見られます。
工場では、非常に精密で正確な機械が必要です。このようなシナリオでは、レーザーカッターが頻繁に使用されます。その結果、レーザー切断は、厳しい許容誤差要件を持つ航空宇宙産業で使用されています。
物質汚染なし
ロータリーカッターを使用して材料を加工する場合、冷却剤を使用するのが一般的です。切断された部品は冷却剤で汚染される可能性があり、脱脂が必要になります。研削作業では、冷却剤または潤滑剤の使用が必要になる場合があります。研削ホイールの摩耗後に残る炭化物の粒子は、多くの完成品に危険をもたらします。ウォーターカッターを使用すると、ガーネットの粉塵も残ります。レーザー切断ではエネルギーとガスのみが使用されるため、材料が汚染されることはありません。
柔軟性
他の切断技術と比較すると、レーザー切断には多くの利点があります。切断の合間にツールを切り替える必要がなくなるため、大きな利点があります。調整後、レーザー カッターは同じ厚さの 1 枚のシートからさまざまな形状を迅速かつ正確に切断できます。これは、複数の切断や複雑なデザインがある場合に役立ちます。
レーザー切断は、精密で細かい切断にも使用できます。レーザー ビームの正確さと精度により、品質を犠牲にすることなく複雑なデザインを切断できます。このようなデザインは手作業で切断するのが難しいため、レーザー切断は優れたオプションです。
手頃な価格と低コスト
レーザー技術の利点の 1 つは、同様の機能を持つ CNC マシンに比べてコストを節約できることです。レーザー切断により、独自のデバイスを作成する必要がなくなります。追加の切断ツールは不要なので、プロジェクトに合わせてデバイスを変更する必要がありません。
直接接触がないため、表面の劣化も防げます。レーザーカッターは可動部品が比較的少ないため、他の加工技術に比べてメンテナンスの手間が少なく済みます。機械の運用コストも、従来の製造方法よりも低くなります。
高速
レーザー切断は、現在利用可能な製造技術の中で最も高速なものの 1 つです。12 kW の酸素補助レーザーは 40 mm の鋼板を素早く切断できるため、レーザー切断は実に驚くべきプロセスです。レーザーを使用した切断は、有線による方法よりも 50 ~ 100 倍、バンドソーよりも 10 倍も高速です。
レーザー切断は作業を非常に迅速に完了できるため、短時間で高い生産性が求められる産業環境に最適です。レーザー切断は比類のない速度と生産性を提供するため、大規模なプロジェクトや大量生産に最適です。
オートメーション
現代のレーザー切断装置は機械化が進んでいるため、作業を完了するのに必要な人数はごくわずかです。熟練した機械オペレーターは、最終的な品質を決定する上で依然として重要な役割を果たします。それでも、手作業の必要性が減り、切断速度が速くなるため、他の切断方法に比べて大幅なコスト削減につながります。多くの機械には、送りシステムとそれに続くコンベアが組み込まれています。当然、このような構成ではレーザー カッターはより高価になります。
非常に複雑な作業に使用される
他の切断技術と比較すると、レーザー カッターを使用すると、通常は難しい多くの作業を簡単に行うことができます。レーザー技術は、最も繊細なエッジにも使用できます。レーザー カッターを使用すると、複雑な形状をすばやく作成できますが、切断領域に歪みや反りが生じる可能性があります。レーザー切断は、許容される材料の範囲が広く、許容範囲も広いです。
多様な素材
アクリルやその他のポリマー、軟鋼、チタン、ステンレス鋼、ハステロイ、タングステンは、技術の適応性のおかげで、レーザー切断を使用して効率的に切断できる多くの材料のほんの一部です。技術が進歩するにつれて、この適応性は高まるばかりです。繊維用に別の周波数でカーボンを切断し、接着剤用に別の周波数を使用できます。
品質
炭素繊維強化複合材が適切に調整されていれば、レーザーカッターで切断するとバリがごくわずかしか残りません。多くの場合、バリを取り除く必要はありません。すべては、材料の厚さや種類などの詳細によって異なります。
さらなる利点は、熱の影響を受ける領域が限定されていることです。HAZ サイズを最小限に抑えると、HAZ に沿った微細構造の変化が少なくなるため、予測可能性と信頼性が向上します。
被害防止
レーザー切断のもう 1 つの利点は、最も薄い材料にも跡が残らないことです。この装置を使用すると、材料が必然的に変形したり、損傷したりするという誤解が広まっています。従来の考え方では、レーザー切断には極度の熱が必要であると考えられています。
熱は材料の特定の領域にのみ影響し、許容範囲には影響しないことに注意してください。レーザーの超高速切断速度により、厚いシートも短時間で切断できます。そのため、製造中に反りや歪みを簡単に回避できます。
レーザー切断の欠点は何ですか?
レーザー切断は、ほぼすべての分野で部品の製造に使用されていますが、欠点もあります。レーザー切断プロセスには多くの利点がありますが、最初に考慮すべき欠点がいくつかあります。
特定の物質が蒸発する
プラスチックなどの一部の材料は、切断時に蒸発する傾向があります。これはレーザー カッターを使用する際の大きな欠点です。ただし、プロの機械オペレーターであれば、この欠点を簡単に回避できます。
専門家はこの問題を回避するためにデバイスの構成を調整しますが、現在、これらの変更を実装するためのコストが高いことが大きな欠点です。
材料の厚さの制限
レーザー カッターの一般的な出力は約 6 キロワットです。最大 12 mm の厚さの金属しか切断できません (速度 10 mm/秒)。最も大型の装置でも、切断限界までしか切断できません。ただし、ウォータージェット切断とワイヤー放電切断には同じ制約があります。これら 3 つの方法により、他のどの方法よりも速く、より深い切断が可能になります。
専門知識が必要
レーザー切断機を最大限に活用するには、その機能に精通し、問題をすぐに見つけることができるプロのオペレーターが必要です。機械が適切にセットアップされていないと、レーザー切断装置と切断された材料が深刻な損傷を受ける可能性があります。最高の効率を達成し、コストのかかるミスを防ぐためには、経験豊富なオペレーターを雇うことが不可欠です。
しかし、有能な専門家はより多くの供給を必要とし、サービス価格が上昇する可能性があります。それにもかかわらず、生産性を最大化し、無駄を減らし、レーザー切断機の寿命を延ばすには、熟練したオペレーターにお金をかけることが重要です。
高いエネルギー消費
他の種類の切削工具と比較すると、レーザー切断機のエネルギー消費率ははるかに高くなります。3 軸 CNC マシンが 40 mm の鋼板からブランクを取り除くのに使用するエネルギーは、機械に必要なエネルギーの約 10 分の 1 です。ただし、処理時間が半分 (1 分対 20 分) であれば、必要なレーザー カッターは CNC の半分のエネルギーしか使用しません。この点で、各コンポーネントは独自のプロファイルを持ち、違いを分析することは困難です。
危険なガスや煙の発生
レーザー切断は、処理できる材料の範囲が広いため、さまざまな用途に使用されています。ただし、このような柔軟性を扱う際には、いくつか留意すべき点があります。プラスチックのように溶けやすい材料をレーザー切断すると、有毒な煙やガスが放出される可能性があります。レーザーの熱切断作用によりこれらの材料が切断されると、有毒な化合物が放出されます。
これらの材料を扱う作業には、十分な換気と適切な安全対策が必要です。作業者に健康上のリスクをもたらす煙を封じ込めて除去するための適切な対策を講じれば、さまざまな材料に対してレーザー切断を安全かつ効率的に行うことができます。
初期費用
レーザー切断機の購入には、かなりの出費が必要になる場合があります。レーザー切断機は、通常、プラズマ切断などの他の切断技術よりも高価で、価格はプラズマ切断機の約 2 倍です。レーザー カッターの購入にかかる費用は高額になることがよくあります。しかし、長期的に見れば、利益とメリットについて考えるのが一番です。
レーザー切断は、効率、精度、適応性、速度に優れているため、従来の方法よりも優れています。長期的には、レーザー切断機は、コストの節約、効率の向上、新しい可能性をもたらすため、企業にとって有益な投資となります。
結論
レーザー切断は、さまざまな材料にパターンを作成し、表面の微細構造を変化させるために広く使用されている加工プロセスです。強力なレーザー ビームを使用して物質を溶解、燃焼、蒸発させ、さまざまな材料をきれいに切断します。このプロセスには高出力レーザーが使用され、CNC と光学系を使用して材料またはビームを目的の方向に向けます。レーザー ビームは、レーザー材料がランプまたは放電によって励起されると、真空チャンバー内で生成されます。レーザー ビームの最も狭いポイントの直径は 0.32 mm 未満で、切り口の幅は 0.10 mm ほど狭くなることがあります。
レーザー切断の利点には、高精度、材料汚染なし、柔軟性、手頃な価格、低コスト、高速、自動化、多用途性などがあります。レーザー切断では、独自のデバイスを作成する必要がなくなり、従来の製造方法に比べて保守と運用コストが少なくて済みます。また、これは現在利用可能な製造技術の中で最も高速な技術の 1 つで、12 kW の酸素支援レーザーで 40 mm の鋼板を有線方式の 50 ~ 100 倍、バンドソーの 10 倍の速度で切断できます。
レーザー切断は、比類のない速度と生産性を提供するため、大規模なプロジェクトや大量生産に最適です。非常に複雑な形状の作業に使用され、切断領域に歪みや反りを生じさせることなく複雑な形状を作成できます。レーザー切断を使用して効率的に切断できる材料の種類は多岐にわたり、アクリル、ポリマー、軟鋼、チタン、ステンレス鋼、ハステロイ、タングステンなどの材料を簡単に切断できます。
結論として、レーザー切断には、高精度、精密、柔軟性、手頃な価格、多用途性など、数多くの利点があります。ただし、各材料の詳細と作業の特定のニーズを考慮することが重要です。レーザー切断には、熱暴露の低減、損傷の防止、切断速度の高速化など、いくつかの利点があります。また、最も薄い材料にも跡が残らず、反りや歪みを防ぐことでも知られています。ただし、切断中に特定の材料が蒸発する可能性、材料の厚さの制限、熟練したオペレーターの必要性など、考慮すべき欠点もあります。
最適な効率と、コストのかかるミスの防止には、専門のオペレーターが不可欠です。レーザー切断機は他の切断ツールよりもエネルギー消費率が高いですが、CNC マシンの半分のエネルギーしか消費しません。さらに、プラスチックのように溶けやすいレーザー切断材料は、有毒な煙やガスを放出する可能性があります。これらの材料を安全に扱うには、適切な換気と安全対策が必要です。
レーザー切断機の初期費用は高額かもしれませんが、長期的なメリットを考慮する価値はあります。レーザー切断は、効率、精度、適応性、速度に優れているため、従来の方法よりも優れています。長期的には、レーザー切断機は、コストの節約、効率の向上、新しい可能性をもたらすため、企業にとって有益な投資になる可能性があります。
ツーリングとCNCの絞り加工能力を最大化する
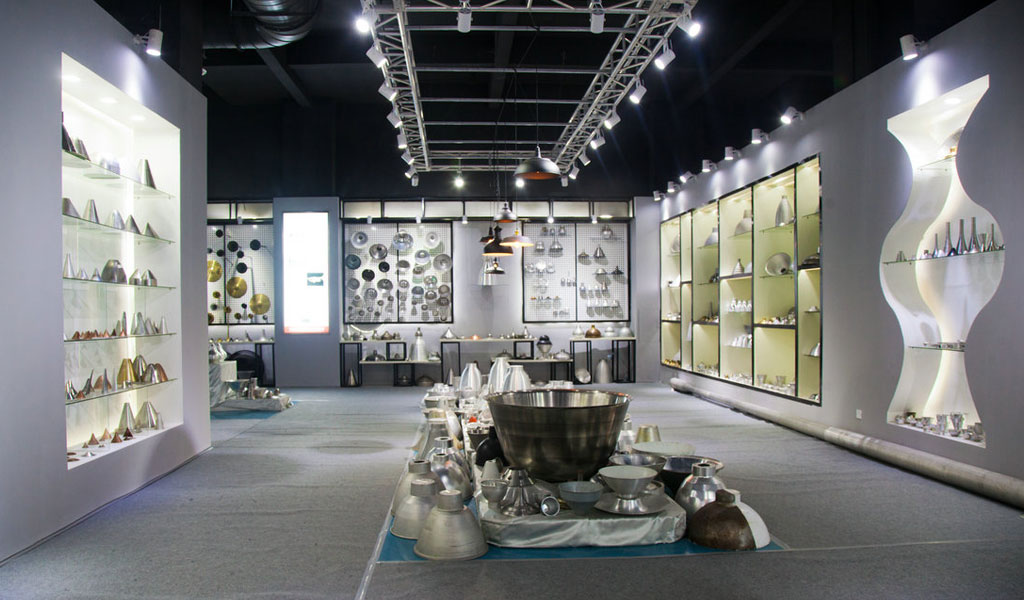
BE-CU 中華のへら 絞り 会社では、過度の摩耗やストレスの兆候を監視しながら、設備を最大限に活用しています。さらに、より新しい最新の設備を検討し、製造能力をサポートまたは向上できる設備に投資しています。当社のチームは機械やツールに細心の注意を払っているため、部品の品質と生産性に悪影響を与えないように定期的にメンテナンスも行っています。
BE-CUの設計とエンジニアリングサポート
BE-CUは、社内の設計およびエンジニアリングチームを活用して、部品生産の初期コンセプトからお客様を支援することができます(提供された設計に対して広範な設計サポートも提供可能です)。私たちのチームは、プロジェクトの開始から終了まで、お客様と定期的かつ透明なコミュニケーションを取りながら、望ましい最終目標に向かって作業を進め、明確な進行方向を提供します。
BE-CUの設計およびエンジニアリングサポートプロセスの一例:
- クライアントがBE-CUチームに部品図面を提供します。
- 当社のエンジニアリングチームが図面をレビューし、ベストプラクティスに基づいて調整を行います。お客様のニーズに応じて、成形または絞り部品を最も効果的に達成する方法を推奨します。
- 図面と設計は必要に応じて改訂され、完璧な形に仕上げられます。財務的な実行可能性も最優先事項として考慮されます。
- 主要な目標は、全ての部品の適合性、形状、機能性を実現することです。
- 研究開発は製造プロセスの重要なステップであり、BE-CUは概念実証や様々な検証要件のためにプロトタイピングサービスを提供しています。研究開発プロセスにおける金属成形については、当社のeBookをご覧ください。
BE-CUが提供する広範な社内サービス
この金属加工プロセスは、軸対称の高性能部品を製造します。スピン成形とも呼ばれ、材料を望ましい形状に切削するのではなく、金属ディスクまたはチューブを円錐形やその他の円形に変形させます。
へら絞りは、手動の手作業によるスピニングプロセスまたは自動CNCスピニングを使用します。BE-CUのへら絞り機能の利点には以下が含まれます:
- コスト削減
- 短いリードタイム
- 最大の設計柔軟性
- シームレスで高品質な構造
対応可能な金属には、ステンレス鋼、炭素鋼、アルミニウム、銅、インコネル、ハステロイ、チタン、ブロンズ、真鍮が含まれます。BE-CUは、センター間60インチから直径100インチまでのカスタム金属絞り部品を製造でき、材料の厚さは0.018インチから2.00インチまで対応可能です。
当社の CNC へら 絞り サービスで迅速なプロトタイプの作成について、今すぐお問い合わせください。こちらでチャットして直接見積もりを取得するか、無料のプロジェクトレビューをリクエストしてください。