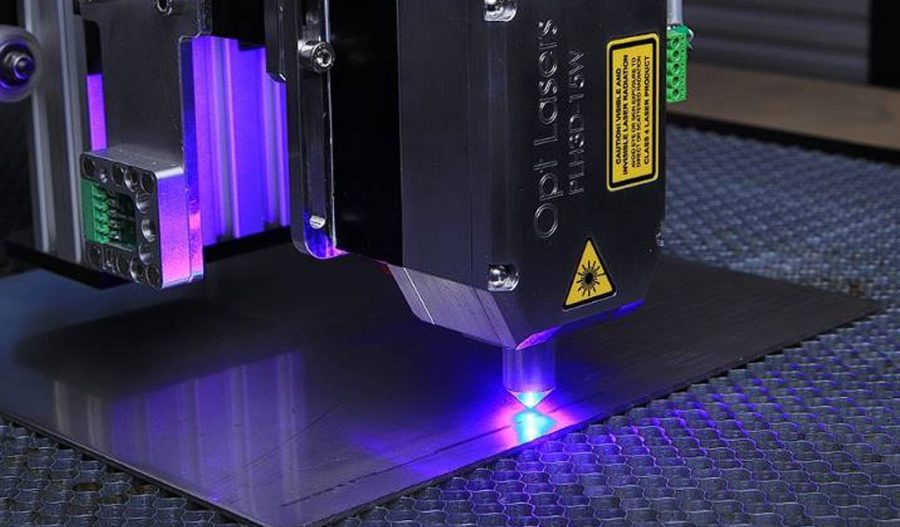
レーザー切断は、精度と効率が何よりも重要となる今日の急速に変化する環境において、画期的なイノベーションです。レーザー切断は、さまざまな材料を正確かつ迅速に切断できるため、さまざまな分野で急速に不可欠な技術となっています。レーザー切断の驚くべき汎用性により、自動車や飛行機から宝石や建築物まで、あらゆるものに使用されています。ここでは、レーザー切断の魅力的な分野に踏み込み、その仕組み、成功の度合い、そして将来性について見ていきます。
レーザー切断はどのように機能し、それは何ですか?
最近では、コンピュータ数値制御装置が製造業で広く使用されています。レーザー切断は、これらの装置で使用される多くの方法の 1 つにすぎません。すべての CNC マシンでは、デジタル化された図面がコンピューター言語に変換された後、ユーザーがマシンにコマンドを入力する必要があります。
この言語は、仕様を実行するために必要なコードをデバイスに提供します。画像をプリンターに送信するのと同様に、言語とマシンの関係はコンピューターと人間の関係に似ています。レーザー切断機も同じように機能するため、設計を迅速に実行できます。
レーザー切断製品の設計により、2D ベクトル ファイルを使用して切断ビームを方向付けることができます。レーザー共振器が主要コンポーネントです。この共振器はガラス繊維で作られ、場合によっては結晶体のガス混合物で作られています。設計者がコンポーネントをどのようにスライスするかによって、共振器の周波数応答が決まります。エネルギーが適用されると、混合物が切断を開始します。一連のミラー レンズを介してアマルガムを通過させた後、レーザーを集中させることができます。
レーザー切断の利点と欠点について議論する前に、レーザー切断の基本を学ぶことが前提条件です。レーザー切断機は、コンピュータ数値制御 (CNC) 機と似た方法で機能しますが、はるかに強力なレーザーを使用します。レーザーは、CNC と光学系を使用して、材料またはビームを目的の方向に向けます。CNC、つまり G コードを使用して、デバイスの動きを制御し、材料を切断します。
レーザー ビームを集中すると、物質は溶解、蒸発、燃焼します。また、ガス ジェットで物質を吹き付けると、高品質のエッジ面が得られます。レーザー ビームを生成するには、ランプまたは放電を使用して、密閉された容器内でレーザー物質を刺激します。
レーザー材料は、ハーフミラーを介して内部反射された後、増幅されます。十分なエネルギーがコヒーレントな単色光ストリームに蓄積されるまで、この現象は持続します。光ファイバーまたはミラーを使用して光を集中させると、光ははるかに明るくなります。
レーザー ビームの最も狭い部分の直径は 0.32 mm 未満です。一方、切断幅は 0.10 mm ほど狭くなることがあります。ただし、これには材料の厚さが関係します。レーザー切断装置が材料の端から切断を開始できない場合は、ピアシング法を使用します。
ピアシング法では、レーザーは強力な力で材料を切断することができます。例えば、厚さ13ミリメートルのステンレス鋼板を焼き切るのに約5〜15秒かかります。
レーザーカッターを使用する利点は何ですか?
金属製造では、切断が基本的なプロセスとして大きく依存しています。切断は、大きな金属板をより小さく複雑な部品に切り分ける上で重要な役割を果たします。製造業者は金属を扱う際にさまざまな切断プロセスを採用していますが、レーザー切断は多くの利点があるため、最も最先端のオプションの 1 つとして際立っています。レーザー切断が金属加工に適した選択肢である理由と、それをどのように実装できるかについては、読み進めてください。
柔軟性
レーザー カッターを使用すると、追加のツールやツールの変更なしで個別のカットを行うことができます。硬い器具は必要ないため、カットの合間にツールを切り替えたり、研いだりする必要はありません。さらに、初期構成を再利用して、同じ厚さの材料からさまざまな形状をカットできます。レーザー切断機は適応性が高く、大量の材料を処理する場合でも、コストのかかるダウンタイムや非効率性なしで繊細なカットを行うことができます。
精度
レーザー切断には、精度という利点もあります。レーザー切断は、他の切断技術と比較して、精度が高くなります (精度 +/- 0.1 mm)。このため、工場では外注に頼ることなく精密部品を製造できます。精度が高いため、多くの場合、追加の許容差は必要ありません。
汎用性
レーザー カッターの中には、複数の軸を備えたものがあります。この技術を使用して、想像できるあらゆるユニークな形状やパターンを彫刻できます。また、他の金属や合金を含むあらゆる素材を、その組成や厚さに関係なく切断できます。これらの機械なら、最も複雑なデザインでも簡単に切断できます。
レーザーカットでは、さまざまな素材から複雑なデザインを切り出すことができ、モデルによっては複数の素材を一度に処理できるものもあります。これらの特徴により、レーザーカットで実現できるデザインの多様性は事実上無限です。
一貫性
レーザー カッターは幅広い材料に対応できるため、一貫性があり信頼性の高い部品やアセンブリを生産できます。機械から出た最初のピースは、1000 番目と同じ正確なカットが施されます。これにより、生産施設は標準化された方法で複数の同一製品を製造できます。
スピード
レーザー切断は、他の切断技術(特に従来の機械式切断)とは異なり、大幅に短い時間で完了できます。この利点は、より複雑な切断を行うときに特に役立ちます。
プラズマ切断や火炎切断などの代替技術による切断では、複雑な金属部品や大きな金属部品を製造するときに長い時間がかかります。速度だけでも、レーザー切断は 10 mm の厚さの材料でも可能になります。
オートメーション
レーザー切断では、オペレーターの入力も最小限で済みます。最新のレーザー切断装置は、技術の進歩により、高度に自動化されています。最新の機械のほとんどは、CNC CAD/CAM ソフトウェア、供給機、および後続のコンベアと通信できるため、スループット、精度、信頼性が大幅に向上しています。プロセスのどの段階でも肉体労働は不要になりましたが、安全性、正確な切断、品質を保証するには、熟練したオペレーターが必要です。そのため、他のプロセスと比較して、レーザー切断はコスト効率に優れています。
仕上げの必要性の低減
レーザー カッターは極めて精密であるため、切断後に残る破片 (バリなど) は通常少なくなります。レーザー カッターは、バリを最小限に抑え、扱いやすい、きれいで鋭いエッジを生成します。
精度の高さもさらなる利点です。カッターからの集中レーザービームは、きれいで正確な切断に不可欠です。HAZ が減少すると、熱暴露による内部欠陥の可能性が減り、金属部品の一貫性、堅牢性、信頼性が向上します。
非接触切断
レーザーカッターからの細いビームだけが、実際に切断される材料に接触します。このため、レーザー切断ツールは、機械で使用されるものよりも摩擦や力によって損傷を受ける可能性が低くなります。また、機械的な手順とは異なり、この方法では、ワークピースに通常の変形、反り、裂け目などが生じません。
エネルギーの使用
レーザー切断は、従来の切断方法よりも効率的で高速であるため、エネルギー消費量が少なくて済みます。平均的なレーザー切断セッションでは、約 10 キロワットの電力を消費します。50 キロワットの電力を必要とする従来の切断装置と比較すると、レーザー切断の効率は驚異的です。レーザー切断装置に切り替えることで、次の製造プロジェクトでコストと時間を節約できます。
レーザー切断の欠点
レーザー切断には多くの利点がありますが、知っておくべき欠点もいくつかあります。そのいくつかについて、後ほど説明します。
特定の物質の蒸発
蒸発は、プラスチックやその他の熱可塑性プラスチックを切断する際によく起こる副作用です。実際、これはレーザー切断法の大きな欠点です。これは欠点ですが、経験豊富な機械オペレーターなら回避策を知っています。この問題を回避するために、専門家はデバイスの構成を調整します。ただし、現時点では、これらの調整にかかるコストはかなり高額です。
現場の専門知識が必要
マシンの機能を最大限に活用し、不具合を迅速に検出するには、訓練を受けたオペレーターが不可欠です。デバイスが適切に構成されていないと、材料とレーザー切断プロセスの両方に悪影響が及びます。市場には適切なスキルを持つ作業員が不足しているため、オペレーターの雇用コストは高くなります。ビデオ インタビュー ソフトウェアを使用すると、オンラインで会議を開催できるため、移動時間が不要になります。
金属の厚さの制限
レーザー切断は、薄いシートを含むさまざまな材料に使用できますが、重金属は別の方法で処理するのが最適です。専門のオペレーターの存在も必要ですが、アクセス可能な機器を使用して、最も厚いシートを判別できます。工場で使用される最も一般的な測定範囲は、15〜20 mm です。
初期費用
レーザー切断装置を購入するには、多額の費用がかかる場合があります。たとえば、プラズマ切断とレーザー切断を比較すると、後者は約 2 倍の費用がかかります。機械への初期投資は高額ですが、長期的な利益はそれを補って余りあるものです。
有害ガスと煙
先ほど、レーザー切断はさまざまな材料で実行できることを述べました。レーザー切断の欠点は、ほぼすべての材料で使用できることです。熱切断プロセスでは、溶けるすべての物質からガスや潜在的に危険な煙が放出されます。プラスチックを扱う場合、これらの危険な煙が放出されるのは当たり前のことです。
レーザー切断はなぜそれほど正確なのでしょうか?
レーザー切断はコンピューター制御のため、優れた精度と高い安全性を備えています。このような機能により、レーザー切断は非常に正確になります。
- コヒーレント光子: レーザー切断メカニズムは、1 つの安定した強力なエネルギー ビームと同期した光子の一定の流れを利用して、精度を向上させます。一定の光線は、さまざまな材料を楽々と切断します。
- レーザー切断機構は、元の設計図と比較して、誤差がほとんどない結果を生み出すことがよくあります。手作業による切断と比較すると、レーザーは常にわずかな時間で、きれいで正確な切断を実現します。
- 最新の光ファイバーレンズを搭載したレーザーカッターのレーザーヘッドにより、正確なレーザーの配置が管理されます。その結果、レーザービームの焦点はより明確かつ直接的になります。
- レーザー切断は、レーザービームが材料に直接接触することがないため、他の方法よりも付随的な被害が少なくなります。理想的な状況では、熱によって切断が行われます。機器の摩耗が少ないということは、出力がより信頼できることを意味します。
- 複雑な作業: レーザー切断装置は、その精度、正確性、一貫性により、非常に複雑な作業に最適です。
レーザー切断精度に影響を与える要因
レーザー切断の精度を向上させるには、次の点を考慮する必要があります。
- より薄い、またはより滑らかな素材を使用すると、より正確なカットが可能になります。素材とその構成ごとに、独自の機械設定が必要です。
- レーザーによって生成されるスポットのサイズ: ビームスポットが狭いほど、広いスポットよりもきれいなカットが得られます。
- 厚い材料をきれいかつ均一に切断するには、より高いレーザー出力設定を検討する必要があります。
- 作業場の精度: ワークピースの材料を作業台上にどのように配置するかも、切断の精度に影響します。不安定な作業台からの振動により、測定が狂い、作業の精度が損なわれる可能性があります。
結論
レーザー切断は、さまざまな材料を正確かつ迅速に切断できるため、今日のペースの速い環境において画期的なイノベーションです。自動車、飛行機、宝飾品、建築など、さまざまな分野で使用されています。レーザー切断は、コンピュータ数値制御 (CNC) マシンを使用して行われます。このマシンでは、デジタル化された図面がコンピュータ言語に変換された後、ユーザーがマシンにコマンドを入力する必要があります。レーザー共振器は、ガラス繊維と結晶体のガス混合物で構成されており、エネルギーが加えられると、混合物が切断を開始します。その利点と欠点について説明する前に、レーザー切断の基礎を学ぶことが前提条件となります。
レーザー切断は金属製造に不可欠なプロセスで、大きな金属板をより小さく複雑な部品に切り分けます。レーザー ビームの直径は 0.32 mm 未満、切り口の幅は 0.10 mm です。ピアシング方式により、レーザーは強力な力で材料を切断できます。レーザー カッターを使用する利点には、大きな金属板をより小さく複雑な部品に切り分けられることが挙げられます。レーザー切断は、柔軟性、精度、汎用性など、多くの利点があるため、金属加工に最適です。
レーザー切断は、材料の組成や厚さに関係なく、あらゆる形状やパターンを彫刻したり、あらゆる材料を切断したりするために使用できます。また、他の切断技術よりも精度が高く、工場では外注せずに精密部品を生産できます。レーザー切断では、さまざまな材料から複雑なデザインを切断することができ、モデルによっては一度に複数の材料を処理できるものもあります。これにより、生産施設では標準化された方法で複数の同一製品を製造できます。レーザー切断は他の切断技術よりも高速で、10mmの厚さの材料でも切断できます。
また、オペレーターの入力が最小限で済むため、コスト効率も高くなります。さらに、レーザー カッターは、バリが最小限で、きれいで鋭い切断面を生成します。レーザー切断には、精度、HAZ の低減、非接触切断、エネルギー効率、切断の高速化など、多くの利点があります。ただし、特定の材料の蒸発、この分野の専門知識、金属の厚さの制限、初期費用、有害なガスや煙など、考慮すべき欠点がいくつかあります。さらに、レーザー切断は、コンピューター ガイド機能により非常に正確で安全性も向上し、非常に正確です。ただし、特定の材料の蒸発、この分野の専門知識、金属の厚さの制限、初期費用、有害なガスや煙など、考慮すべき欠点がいくつかあります。
ツーリングとCNCの絞り加工能力を最大化する
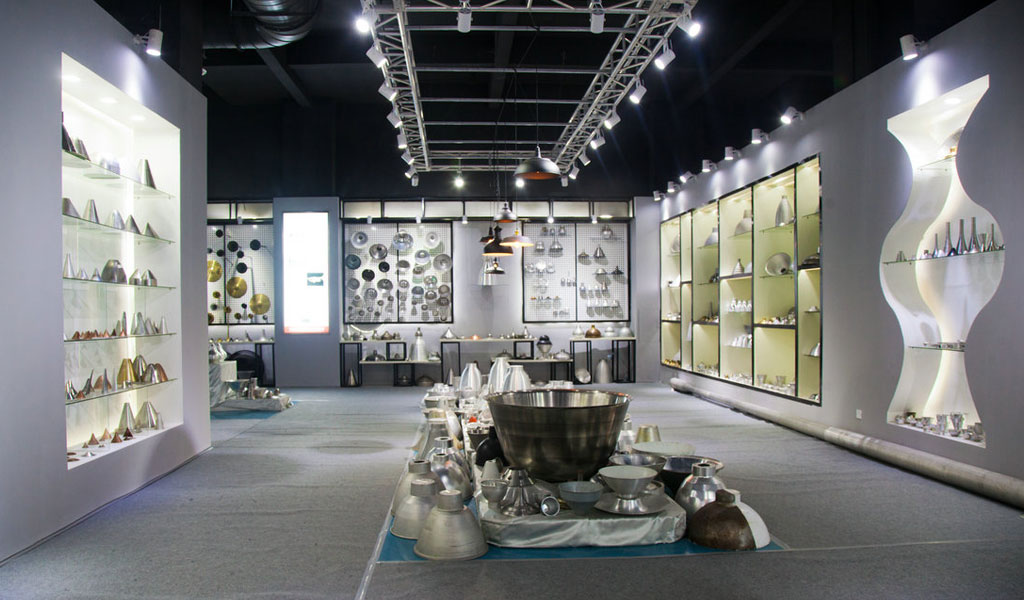
BE-CU 中華のへら 絞り 会社では、過度の摩耗やストレスの兆候を監視しながら、設備を最大限に活用しています。さらに、より新しい最新の設備を検討し、製造能力をサポートまたは向上できる設備に投資しています。当社のチームは機械やツールに細心の注意を払っているため、部品の品質と生産性に悪影響を与えないように定期的にメンテナンスも行っています。
BE-CUの設計とエンジニアリングサポート
BE-CUは、社内の設計およびエンジニアリングチームを活用して、部品生産の初期コンセプトからお客様を支援することができます(提供された設計に対して広範な設計サポートも提供可能です)。私たちのチームは、プロジェクトの開始から終了まで、お客様と定期的かつ透明なコミュニケーションを取りながら、望ましい最終目標に向かって作業を進め、明確な進行方向を提供します。
BE-CUの設計およびエンジニアリングサポートプロセスの一例:
- クライアントがBE-CUチームに部品図面を提供します。
- 当社のエンジニアリングチームが図面をレビューし、ベストプラクティスに基づいて調整を行います。お客様のニーズに応じて、成形または絞り部品を最も効果的に達成する方法を推奨します。
- 図面と設計は必要に応じて改訂され、完璧な形に仕上げられます。財務的な実行可能性も最優先事項として考慮されます。
- 主要な目標は、全ての部品の適合性、形状、機能性を実現することです。
- 研究開発は製造プロセスの重要なステップであり、BE-CUは概念実証や様々な検証要件のためにプロトタイピングサービスを提供しています。研究開発プロセスにおける金属成形については、当社のeBookをご覧ください。
BE-CUが提供する広範な社内サービス
この金属加工プロセスは、軸対称の高性能部品を製造します。スピン成形とも呼ばれ、材料を望ましい形状に切削するのではなく、金属ディスクまたはチューブを円錐形やその他の円形に変形させます。
へら絞りは、手動の手作業によるスピニングプロセスまたは自動CNCスピニングを使用します。BE-CUのへら絞り機能の利点には以下が含まれます:
- コスト削減
- 短いリードタイム
- 最大の設計柔軟性
- シームレスで高品質な構造
対応可能な金属には、ステンレス鋼、炭素鋼、アルミニウム、銅、インコネル、ハステロイ、チタン、ブロンズ、真鍮が含まれます。BE-CUは、センター間60インチから直径100インチまでのカスタム金属絞り部品を製造でき、材料の厚さは0.018インチから2.00インチまで対応可能です。
当社の CNC へら 絞り サービスで迅速なプロトタイプの作成について、今すぐお問い合わせください。こちらでチャットして直接見積もりを取得するか、無料のプロジェクトレビューをリクエストしてください。