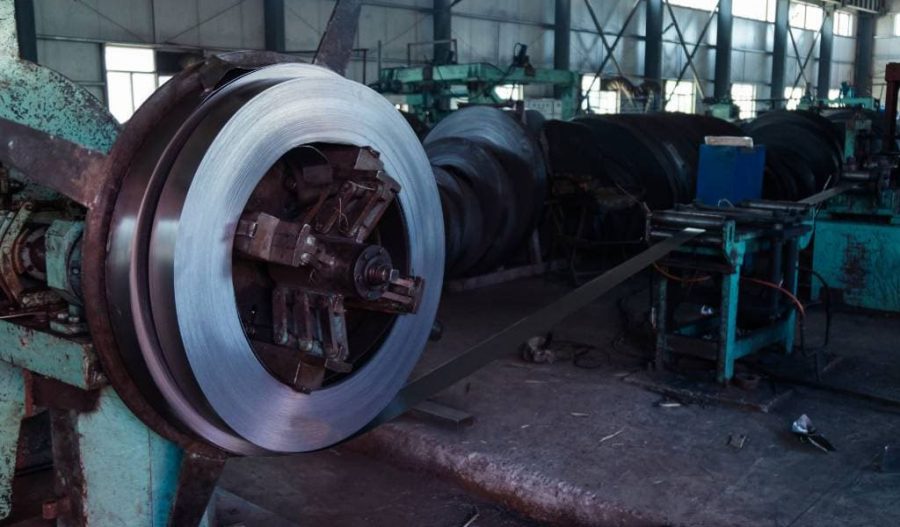
今日のビジネスのやり方を変えた重要な製造プロセスである圧延のエキサイティングな世界を見てみましょう。ローラーは、街並みに並ぶ高層ビルから、私たちをさまざまな場所に連れて行く車、そして私たちが頼りにしている多くのツールや製品まで、私たちが毎日使用する多くのものを作るのに不可欠です。
このブログ投稿の目的は、原材料をより強く、より長持ちし、より多様な用途に使用できる完成品に変えるプロセスである圧延の多くの利点を示すことです。熟練した冶金の専門家、製造プロセスの基礎を学びたい学生、または日常の物の背後にあるテクノロジーに関心のある人など、この圧延の利点のツアーは、この重要な製造方法をより理解し、高く評価するのに役立ちます。圧延プロセスのスピード、コスト効率、新しいアイデアにつながる能力を調べながら、圧延プロセスが工業生産に依然として不可欠である理由を見つけてください。
ローリングプロセスの説明
圧延工程は金属加工の基礎であり、 現代文明の基盤となる材料を形作る上で極めて重要な役割を果たしています 。この技術では、一対の回転ロールに金属を通すことで金属を変形させます。これは単に金属の厚さを変えることではなく、製造における精度、効率、および汎用性に関するものです。
ローリングの真髄
圧延は最も重要な金属成形プロセスであり、使用可能な形状に加工される鉄および非鉄金属と合金の 95% 以上を占めています。これらの形状には、プレート、シート、ストリップ、フォイル、およびレール、ビーム、チャネル、アングル、バー、ロッド、シームレス パイプなどのさまざまなセクションが含まれます。このプロセスでは、材料に高い圧縮応力をかけ、2 つの回転する円筒形ロール間の隙間を通過できるようにすることで、永久変形を実現します。
プロセスの説明
圧延では、生地を伸ばすのと同じように、金属のストックを圧縮して伸ばし、希望の形状とサイズを実現します。平らなロールまたは溝付きのロールは、一定の距離を保ち、反対方向に回転します。この動作により、金属の断面積が縮小し、ロールの隙間を通過させることで形状が変化します。この隙間は、 入力材料の断面積よりも小さく保たれます。
ローリングの段階
ローリングプロセスには主に 3 つの段階があります。
- 一次圧延: この最初の段階では、インゴットの厚さを減らし、ブルームやスラブなどのより単純なストック形状に変換します。これにより、材料の構造が洗練され、機械的特性が向上し、内部欠陥が排除されます。
- 熱間圧延: 一次圧延で得られたブルームとスラブは、熱間圧延によってさらに加工され、プレート、シート、ロッド、その他の二次部材が製造されます。この段階では、高温で材料を成形できます。
- 冷間圧延は最終段階であり、熱間圧延された製品は仕上げ処理を受け、優れた表面仕上げ、正確な許容差、さらに強化された機械的特性が実現されます。
圧延機の種類
圧延機は、ロールの回転を容易にし、圧延工程に不可欠です。圧延機は、ロールの数と配置によって次のように異なります。
- 2 段式圧延機: ロールが上下に重ねられた 2 つの高さのあるスタンドを備えています。
- 3 段圧延機: 生産性を向上させるために、同じ垂直面に 3 つのスタンドを配置します。
- 4 段圧延機: 2 つのバックアップ ローラーを組み込むことで、曲がりを減らし、均一な圧縮を保証します。
- クラスターミル: このミルは、2 つ以上のバックアップ ローラーでサポートされた 2 つの作業ローラーを使用し、主に冷間圧延に使用されます。
- マルチハイロールミル:小径の作業ローラーを 2 つ採用し、優れた剛性を実現。
- ユニバーサル圧延機: この圧延機は 2 つの垂直ローラーと 2 つの水平ローラーで構成され、幅広フランジの H 型断面梁の製造に使用されます。
- ローリングの利点
- 圧延プロセスには、速度と時間の効率、大量生産への適合性、高い材料効率とエネルギー効率、複雑なプロファイルを生成する能力、正確な許容差、さまざまな業界への応用など、数多くの利点があります。
課題
圧延には利点があるものの、初期コストが高く、表面仕上げが粗くなる可能性があり、大量生産の環境では最も効率的です。
効率と生産性
圧延工程と板金加工は製造業に不可欠な要素であり、現代の生産ラインを支える効率性と生産性の融合を実現します。これらの工程は、自動化と戦略的なシステムバランスを通じて、製造業者が業務を最適化し、生産量を大幅に増加することを可能にします。
圧延効率の核心
圧延は製鉄に不可欠なプロセスで 、 一連のローラーに金属を通すことで金属を変形させ、厚さを減らしたり、断面を変えたりします。この方法は、さまざまな形状やサイズを効率的に製造できる点で優れているため、さまざまな鉄鋼製品の製造に適しています。圧延の効率性は、大量の材料を扱い、驚くべき速度と一貫性で目的の形状に変形できる能力に表れています。
板金加工における生産性
板金加工には、切断、成形、組み立てなどの段階が含まれ、正確な順序で完了します。生産サイクルの特定の部分専用の一連の機械またはモジュールを備えた生産システムの自動化により、生産性が大幅に向上します。これらのシステムの生産性と効率を計算することは、ラインのパフォーマンスを最適化し、生産量を増やすために不可欠です。
生産性と効率性の計算
生産システムの生産性と効率性を評価するには、ライン内の各マシンまたはモジュールのパフォーマンスを把握することが不可欠です。 これには、 各モジュールのサイクル タイム、生産性、可用性などのパラメータの分析が含まれます。生産性は部品あたりの秒数で表され、モジュールがロード、処理、アンロードなどのプロセスを完了するのにかかる時間を反映します。
可用性は、A = MTBF / (MTBF + MTTR) という式で定義されます。ここで、MTBF は平均故障間隔、MTTR は平均修復時間であり、モジュールが動作可能であると予想される時間の割合を示します。
ライン生産性の最大化
生産性を最大化するための戦略には、モジュール間にバッファを実装して同時処理を可能にし、ボトルネックを回避し、生産ライン全体のスループットを向上させることが含まれます。同時処理とシリアル処理の選択は、ラインの生産性に大きな影響を与える可能性があり、同時処理はシステムのボトルネックの影響を軽減して、多くの場合、より高い出力につながります。
効率の役割
効率は、E = N * P / (N * P + ST) * A として計算され、ST はセットアップ時間を表します。効率は、生産ラインの全体的な有効性を決定する上で重要な役割を果たします。効率は、材料の変更、ツールの変更、メンテナンスなどの非生産時間を考慮し、長期間にわたるラインの運用生産性の現実的な見積もりを提供します。
材料特性の強化
圧延プロセスは、変形と制御された冷却によって微細構造を操作することで、材料、特に鋼の機械的特性を大幅に向上させます。この変換は、強度と柔軟性のバランスが取れた鋼を生産するために不可欠であり、自動車、建設、製造のさまざまな用途に適しています。
結晶粒微細化と相転移
圧延により結晶粒が微細化され、表面硬度が向上し、表面粗さが減少します。また、このプロセスにより、材料表面の残留応力が引張から圧縮に変化し、極限引張強度、降伏強度、曲げ性、靭性などの機械的特性が向上します。これらの向上の程度は、接触応力や圧延サイクル数などの特定の圧延パラメータによって異なります。
制御された圧延と冷却
制御された圧延と冷却技術の開発により、鋼の精密な微細構造設計が可能になります。このアプローチにより、相変態を制御して望ましい微細構造を生成し、必要な材料特性を実現できます。たとえば、熱間圧延と超高速冷却および焼入れおよび分割 (Q&P) プロセスを組み合わせると、Fe-Si-Mn-Nb 鋼の結晶構造が洗練され、残留オーステナイト粒子が埋め込まれたマルテンサイトマトリックスが生成されます。この微細構造により鋼の強度が向上し、残留オーステナイトは変態誘起塑性 (TRIP) 効果を通じて可塑性と加工硬化能力を高めます。
高強度鋼に対するQ&Pプロセスの影響
先進の高強度鋼の Q&P プロセスにより、強度と柔軟性が大幅に向上します。このプロセスでは、マルテンサイト開始温度より低く、マルテンサイト終了温度より高い温度に急冷し、その後、等温処理を行って過飽和マルテンサイトから残留オーステナイトへの炭素拡散を可能にします。その結果、TRIP 効果により延性と靭性が向上した高強度鋼が生まれ、従来の熱処理サンプルよりも優れたものになります。
環境と安全に関する考慮事項
圧延とそれに関連するプロセスは、材料特性の向上に大きな利点をもたらしますが、環境と安全上の課題も伴います。製鉄は最も炭素集約的なプロセスの 1 つであり、世界の温室効果ガス排出の一因となっています。ヒサルナ製鉄プロセスや鉄鋼生産における再生可能水素の使用などのイノベーションは、これらの排出量を削減し、製鉄をより持続可能なものにするために研究されています。
表面仕上げと寸法精度の向上
プロジェクトに適したタイプの鋼板を選択する際には、冷間圧延鋼板と熱間圧延鋼板の違いを理解することが重要です。各タイプにはそれぞれ異なる特性、利点、欠点があり、特定の要件に基づいてプロジェクトの結果に影響を与えます。
冷間圧延鋼板:精度と美観
冷間圧延鋼板は、優れた表面仕上げと高い寸法精度で知られています。これらの特性は、室温またはそれよりわずかに低い温度で圧延処理することで実現されます。この方法により、より滑らかで均一な鋼板が製造されるため、建築要素や消費者製品など、外観が重要となる用途に最適です。厚さ、幅、長さの測定精度が高いため、冷間圧延鋼板は、正確な仕様が求められるプロジェクトで非常に人気があります。
熱間圧延鋼板:コスト効率と成形性
逆に、熱間圧延鋼板は鋼を高温で圧延して製造されるため、表面は粗く、スケール状になりますが、成形やサイズ調整が容易になります。寸法精度は劣るものの、熱間圧延鋼板は延性と成形性に優れているため、表面仕上げが重要でない構造用途に適しています。また、製造プロセスが簡単なため、熱間圧延鋼板は冷間圧延鋼板よりもコスト効率に優れています。
強度、コスト、美観のバランス
冷間圧延鋼板と熱間圧延鋼板のどちらを選ぶかは、最終的にはプロジェクトの特定のニーズによって決まります。冷間圧延鋼板は、追加処理が必要なため一般的に高価ですが、表面がより滑らかで、精度が高く、強度も高いため、美観と耐久性が求められる用途に適しています。熱間圧延鋼板は、より手頃な価格で扱いやすいため、仕上げや正確な寸法がそれほど重要でない構造プロジェクトに適しています。
結論
圧延鋼は、現代の産業、技術、インフラに欠かせません。その歴史は、中央アジアとヨーロッパで鉄鉱石が採掘されていた鉄器時代にまで遡ります。それ以来、このプロセスは大きく進化し、古代の技術から現代の技術主導の方法へと移行し、世界の 2.9 兆ドルの経済活動を支え、促進しています。
現在、鉄鋼は主に高炉法とアーク炉法で生産されています。高炉法は、銑鉄とスクラップ鋼を溶かし、アーク炉で成分を精製して鉄を生産します。一方、アーク炉法は、高電流のアークを使用してスクラップ鋼または直接還元鉄を溶かし、溶鋼を生産します。
製鉄業は世界的に最も炭素集約的な産業の一つであり、温室効果ガス排出量の約 10% を占めています。HIsarna 製鉄プロセスや水素還元などのイノベーションは、排出量を削減し、化石燃料の代わりに再生可能な水素を使用して鋼鉄を生産することを目指しています。圧延プロセスでは、機械的な変形によって金属ストックをさまざまな形状と厚さに変形します。これは、幅広い金属製品の製造に不可欠です。
熱間圧延では金属が大きく変形し、I ビーム、レール、シートなどの大型断面が製造されます。ただし、金属の機械的特性にはほとんど方向性がないため、高温でミルスケールが形成されるため、表面仕上げが粗くなる可能性があります。冷間圧延では、ひずみ硬化によって金属の強度が高まり、優れた表面仕上げが得られるため、精度と美観が求められる用途に適しています。圧延プロセスには、平圧延、形状圧延、リング圧延、ねじ圧延などがあります。
圧延は、正確な寸法と機械的特性を備えた金属製品を大量生産するために不可欠な、非常に効率的で多用途なプロセスです。建設、自動車、航空宇宙など、さまざまな業界で極めて重要な役割を果たしています。現代の圧延技術により、 正確かつ迅速な金属処理が可能な高度な圧延機が開発されました。
圧延鋼の歴史は金属加工の初期の時代にまで遡り、何世紀にもわたる革新と技術の進歩を経て進化してきました。産業革命と鉄の圧延の台頭により、鉄と鋼の製造に革命が起こり、機械、鉄道、蒸気船で広く使用されるようになりました。現代の圧延技術の進化は、レール圧延機、魚腹型錬鉄レール、および重いセクションを圧延するための 3 段圧延機の導入によって特徴づけられています。
ツーリングとCNCの絞り加工能力を最大化する
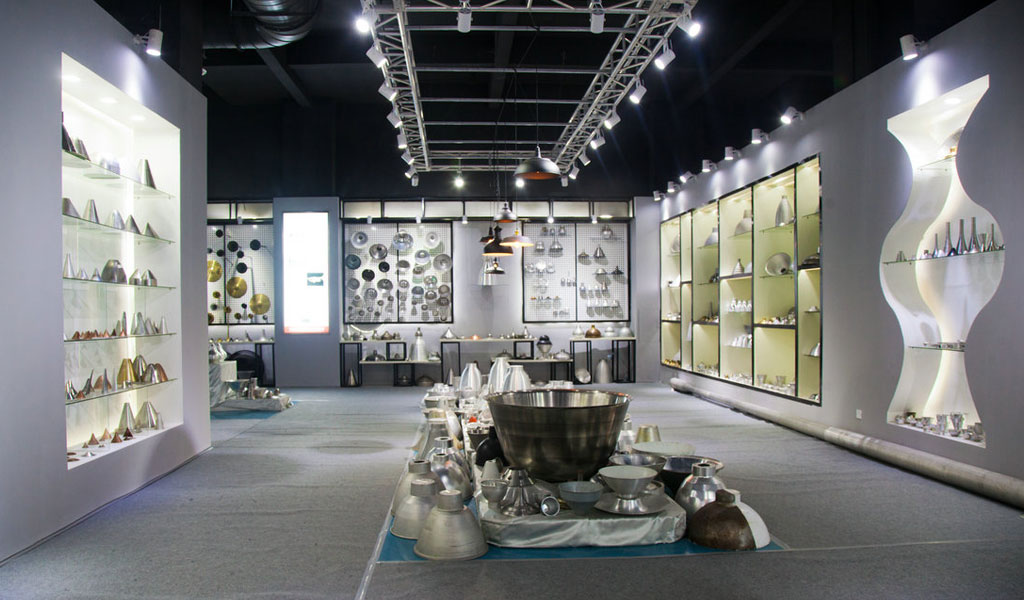
BE-CU 中華のへら 絞り 会社では、過度の摩耗やストレスの兆候を監視しながら、設備を最大限に活用しています。さらに、より新しい最新の設備を検討し、製造能力をサポートまたは向上できる設備に投資しています。当社のチームは機械やツールに細心の注意を払っているため、部品の品質と生産性に悪影響を与えないように定期的にメンテナンスも行っています。
BE-CUの設計とエンジニアリングサポート
BE-CUは、社内の設計およびエンジニアリングチームを活用して、部品生産の初期コンセプトからお客様を支援することができます(提供された設計に対して広範な設計サポートも提供可能です)。私たちのチームは、プロジェクトの開始から終了まで、お客様と定期的かつ透明なコミュニケーションを取りながら、望ましい最終目標に向かって作業を進め、明確な進行方向を提供します。
BE-CUの設計およびエンジニアリングサポートプロセスの一例:
- クライアントがBE-CUチームに部品図面を提供します。
- 当社のエンジニアリングチームが図面をレビューし、ベストプラクティスに基づいて調整を行います。お客様のニーズに応じて、成形または絞り部品を最も効果的に達成する方法を推奨します。
- 図面と設計は必要に応じて改訂され、完璧な形に仕上げられます。財務的な実行可能性も最優先事項として考慮されます。
- 主要な目標は、全ての部品の適合性、形状、機能性を実現することです。
- 研究開発は製造プロセスの重要なステップであり、BE-CUは概念実証や様々な検証要件のためにプロトタイピングサービスを提供しています。研究開発プロセスにおける金属成形については、当社のeBookをご覧ください。
BE-CUが提供する広範な社内サービス
この金属加工プロセスは、軸対称の高性能部品を製造します。スピン成形とも呼ばれ、材料を望ましい形状に切削するのではなく、金属ディスクまたはチューブを円錐形やその他の円形に変形させます。
へら絞りは、手動の手作業によるスピニングプロセスまたは自動CNCスピニングを使用します。BE-CUのへら絞り機能の利点には以下が含まれます:
- コスト削減
- 短いリードタイム
- 最大の設計柔軟性
- シームレスで高品質な構造
対応可能な金属には、ステンレス鋼、炭素鋼、アルミニウム、銅、インコネル、ハステロイ、チタン、ブロンズ、真鍮が含まれます。BE-CUは、センター間60インチから直径100インチまでのカスタム金属絞り部品を製造でき、材料の厚さは0.018インチから2.00インチまで対応可能です。
当社の CNC へら 絞り サービスで迅速なプロトタイプの作成について、今すぐお問い合わせください。こちらでチャットして直接見積もりを取得するか、無料のプロジェクトレビューをリクエストしてください。