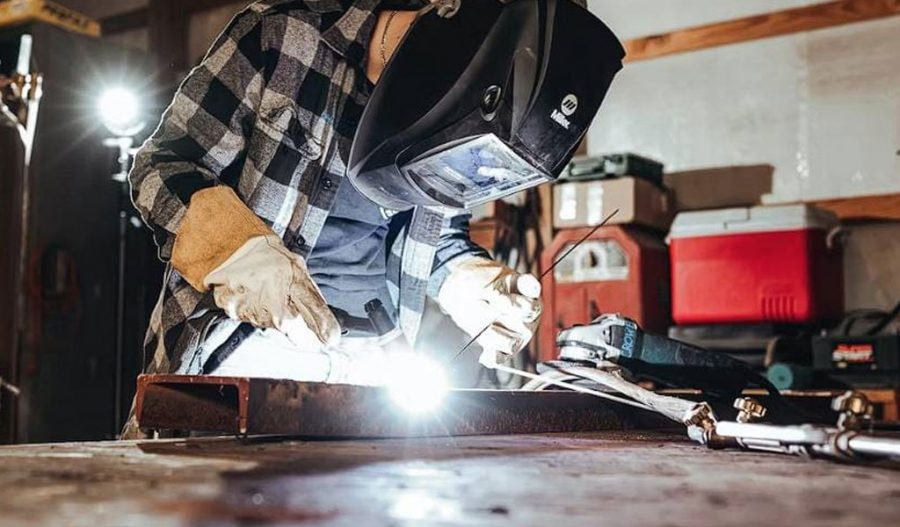
さまざまな分野で広く利用されているプロセスである金属不活性ガス (MIG) 溶接の基礎を学びます。MIG 溶接は、柔軟性が高く安価な溶接方法で、高品質の溶接を実現し、後片付けがほとんどまたはまったく必要ありません。この記事では、MIG 溶接の利点と用途、必要な機器、さまざまな材料を溶接するためのプロセス、注意すべき点、一般的な問題とその解決策などについて説明します。
MIG溶接(金属不活性ガス溶接)とは何ですか?
MIG 溶接では、消耗性フィラー金属電極とワークピースの間にアークを発生させて融合させます。保護はすべて、外部から配管されるガスまたはガスの組み合わせによって行われます。MIG 溶接には、不活性シールド ガスが必要です。
不活性ガスの例には以下のものがあります。
- 元素: ヘリウム、アルゴン、二酸化炭素。
ヘリウムは、他の不活性ガスと比較して、最も速い溶接速度と最大の溶接堆積速度を提供します。
アルミニウム、ステンレス鋼、炭素鋼などの材料はすべて MIG 溶接に適しています。これは、さまざまなプロジェクトに利用できる柔軟な溶接技術です。
適切な安全対策を講じれば、MIG 溶接はリスクがありません。ただし、他の溶接手順と同様に、高温や電気を扱う際には事故が発生する可能性があります。
MIG溶接のセットアップ
金属の準備は、溶接機を始動する前の最初のステップです。錆、汚れ、油、その他の不純物と戦うために必要な特定の化学物質をより多く含むスティック電極やフラックス入り電極とは対照的に、ソリッド MIG ワイヤはあまり効果的ではありません。アークを点火する前に、金属ブラシまたはグラインダーを使用して表面を金属が露出するまで清掃します。また、作業クランプが取り付けられている金属に汚れがないことを確認してください。電気抵抗があると、ワイヤの供給効率に影響します。
接続部を面取りすると、溶接が母材に完全に浸透することが保証されます。これは、厚い金属に強力な溶接を施すために不可欠です。突き合わせ接合では、これが最も必要になります。
次のステップは、ギアを使用する準備をすることです。
- ケーブルを確認します。アークを発生させる前に、溶接機器のケーブル接続が安全で損傷がないことを確認します。
- 電極の極性を選択する必要があります。MIG 溶接には、正極性または逆極性の DC 電極が必要です。通常、極性接続はデバイスの内部にあります。
- ガスの流れを調節します。シールド ガスの流量を 1 時間あたり 20 ~ 25 立方フィートに設定し、電源を入れます。ガス ホースの漏れが疑われる場合は、石鹸水に泡がないか調べます。ホースに漏れが生じた場合は、交換する必要があります。
- ストレスを軽減します。ドライブ ロールまたはワイヤ スプール ハブの張力が不十分だと、ワイヤの供給効率が低下する可能性があります。マニュアルの指示に従って変更を行ってください。
- 消耗品を確認します。接触チューブから余分な飛散物を取り除いて、摩耗した接触チップまたはライナーを交換し、錆びたワイヤーを捨てます。
溶接技術と位置
MIG 溶接技術に関する、拘束力のない一般的な推奨事項を以下に示します。
MIG溶接にフラットポジションを使用する
平らな表面での溶接は簡単です。状況に応じて、MIG ガンは溶接方向に対して垂直に 36 度まで傾けることができます。高電圧、高速、高温の設定を使用してください。実際、一定の動きではありますが、浸透溶接であればどのようなものでも理想的です。
水平姿勢でのMIG溶接のテクニック
水平位置での溶接には、より多くの労力が必要です。MIG は、わずかに角度を付ける必要があります。溶接方向に対して 15° ~ 35° の角度で、上空に向けて 36° ~ 46° の角度で向けます。融合シームとロールオーバー溶接に注意してください。ジョイントを常にストリンガーのタイトさまでビードします。最も効果的な動きは、ホイップとサークルです。機械の設定を上げることで、無能さを補うことはできません。溶接を均等に分散して制御するには、スキルとテクニックが必要です。
垂直姿勢でのMIG溶接のテクニック
垂直下方向も簡単です。最も高い位置から始めて、下方向に進みます。MIG ガンを 35 ~ 45 度上向きに傾ける必要があります。逆さまに溶接するにはコツがあります。電極を左右に一定に動かし続けると、溶接が十分に深く浸透しません。溶接が溜まらないようにできる限り、パターンは関係ありません。
垂直上向きMIGガンによる溶接
MIG 溶接機を最も難しい作業に配置するのは、垂直上向きの位置です。MIG ガンのハンドルを握る最適な角度は、上向き 35 ~ 45 度です。垂直上向きに溶接する場合は、作業用の溶接棚を作ることが不可欠です。MIG 溶接では、垂直上向きの非常に凸状の溶接が頻繁に発生します。ちょっとしたヒントとして、表面に小さな溝を削って溶接すると、溶接中に直立姿勢を保つことができます。この作業にどれだけ努力しても、溶接の見た目は必ずひどいものになります。溶接の幅が十分であれば見栄えの良い溶接が実現できますが、そうでない場合は、溶接は非常に凸状の外観になります。
オーバーヘッドMIG溶接
上記の MIG 溶接を行う場合、MIG ガンを溶接方向に対して 5 ~ 35 度の角度で傾ける必要があります。内部温度を高くしておくと効果的であり、その温度を維持することは最終的には自動的になります。
多少の飛散は起こるので、火花が自分に当たらないように注意する必要があります。身を守るために袖をまくりましょう。そうしないと、熱い金属が袖から漏れて肘を火傷してしまいます。
MIG溶接用パターン
MIG 溶接パターンをお探しなら、ここがぴったりの場所です。溶接品質は、機械のセットアップ、溶接ジョイントの清潔さ、人間工学など、自分では制御できない要因に大きく関係します。パターンは、無能さを補う役割を果たします。熟練の溶接工は、通常、溶接ジョイントが何であっても、溶接方法を「理解」しており、知っています。パターンは、流れに沿って動く方法を理解する際に、安定感をもたらします。トーストに塗ったピーナッツバターのように、溶接を広げることは、パターンを使用すると簡単になります。均一性と滑らかさをもたらします。最も頻繁に発生するパターンは次の 4 つです。
- 鞭打ち
- 安定した動き
- 織り
- サークル
定常溶接法による溶接パターン
最も基本的なアプローチは、安定した動きで、微調整された MIG 溶接機が必要です。ほとんどのロボットはこの方法を使用しており、どの方向でも完璧な溶接が可能です。電極の角度、移動速度、その他の機械変数が役割を果たします。一般的に、溶接が良ければ良いほど、一定の動作のためには温度を高くする必要があります。この方法を適切に設定するだけで十分です。これは、希望の位置以外の位置からアルミニウムを MIG 溶接するための標準的な方法です。それ以外は、指示がすべてを物語っています。
ホイップパターン法を用いた溶接手順
ストリンガービードとフィレット溶接ジョイントは、ホイップ溶接によって大きな恩恵を受けます。ホイップ溶接は、溶接液の溜まりを小さな領域に限定し、金属を流し込む前にジョイントを予熱します。溶接工としてキャリアをスタートしたばかりの人は、この方法によって移動速度の管理方法を学ぶことができます。これは、2 回の前進と 1 回の後退の単純なシーケンスです。歩くのと同じくらい簡単です。
サークル溶接技法のパターン
ウィップとウィーブはどちらも円を描くように作業することで簡素化できます。さまざまな関節に効果的で、実質的にどこにでも使用できます。きつい円を描き、前進しながらこのプロセスを繰り返します。
織り込み溶接技術のパターン
幅の広い溶接に使用される織り目は、ストリンガー ビードほど小さいものから、1 回のパスで可能な限り広く大きなものまであります。変形しにくい大きな接合部では、織り目を使用することでメリットが得られます。原則として、船上での織り目は禁止されています。設定速度での熱量を制限する計算のため、重要な接合部の近くでは織り目は許可されません。
MIG溶接はどの業界で使用されていますか?
製造業
MIG 溶接は、生産のあらゆる分野で利用されています。たとえば、家庭用の小さな装飾品や、巨大なプレハブ建築部品は、MIG 装置を使用して製造されています。
MIG マシンの典型的な用途は、大量生産の組立ライン生産です。ただし、MIG 溶接は、手作業で大量生産される製品によく使用されます。
工事
多くの人が目にする建物を建てる場合、鋼鉄がよく使われます。建設現場で MIG 溶接機を見かけることはあまりありません。しかし、新しい建物は MIG 溶接で作られた部品に大きく依存しています。
当店にはMIGマシンがあり、階段、手すり、はしごなどを作るのに使用しています。また、工業用MIGマシンを使用して、さまざまなサイズのバージョイストも製造しています。
工場で溶接されるコンポーネントは、通常、現場でスティック溶接機を使用して設置されます。複数の階にわたってバージョイストや梁を溶接するには、より長い MIG 溶接機のリードが必要になります。
自動車
自動車部門の溶接は、技術の進歩によりますます機械化されています。最近の進歩により、新車の組み立てにおいて手作業による溶接は不要になる可能性があります。
しかし、MIG 溶接は多くの場合、修理に最も効果的な方法です。たとえば、手作業による MIG 溶接で、ほとんどの自動車ボディの損傷を修理できます。排気システムの損傷も修理できます。
MIG 溶接は、車の修理において最適な選択肢となる場合があります。たとえば、アルミ合金ホイールの場合、溶接には TIG 溶接機が最適なツールです。
ロボット工学
MIG 溶接の自動化は、技術の進歩とともに向上しています。その結果、自動溶接システムのロボット化により、これまで以上に高い生産性を実現しています。
ロボット工学では、さまざまな溶接技術が利用されています。MIG 溶接は、迅速で簡単な作業に最も効果的です。MIG 溶接の速度は、自動化によって向上します。
メンテナンスは必要ですが、ロボットアームは人間のように消耗しません。また、精密で均一な溶接が可能で、全体的にはるかに信頼性が高いです。これは、ロボットアームは作成者から与えられた指示のみを実行するため、人間のようなエラーが発生する可能性が極めて低いためです。
MIG溶接の長所と短所
MIG 溶接は、その適応性と生産速度の速さにより、大量生産が優先される産業環境にとって貴重なツールとなります。
MIG の汎用性、スピード、使いやすさは他に類を見ません。これらの利点により、TIG 溶接の方が見た目が美しく、建設現場での TIG の適用が制限されるという欠点を補うことができます。
長所
- 大量生産でも高速溶接が可能です。
- 習得が簡単 さまざまな金属に対応
- しっかりとした完璧な溶接
- 効率を犠牲にすることなく、より少ないパスでより多くのフィラーメタルを転送します。
短所
- スティック溶接に比べて柔軟性に欠ける
- 使えるポジションは限られているので、
- 初期投資額が高額になる可能性あり
- TIG 溶接ほど魅力的ではありません。
結論
MIG 溶接は、高品質の溶接部が得られ、後片付けがほとんどまたはまったく必要ない、柔軟で安価な溶接方法です。ヘリウム、アルゴン、二酸化炭素などの不活性シールド ガスが必要で、アルミニウム、ステンレス鋼、炭素鋼などの材料はすべて MIG 溶接に適しています。MIG 溶接のセットアップには、表面をむき出しの金属まで清掃し、接続部を面取りし、ケーブルを確認し、正または逆極性の DC 電極を選択し、シールド ガスの流量を設定し、溶接機をオンにすることが含まれます。このテキストで最も重要な詳細は、MIG 溶接のテクニックと位置です。これらのテクニックには、MIG 溶接の平らな位置、MIG 溶接の水平位置、MIG 溶接の垂直位置、MIG 溶接の垂直位置、および MIG 溶接の垂直上向き位置の使用が含まれます。
平らな表面での溶接は簡単ですが、水平位置での溶接にはより多くの労力が必要です。垂直位置での溶接では、電極を常に左右に動かす必要があります。垂直上向きの MIG ガンで溶接するには、電極を常に左右に動かす必要があります。このテキストで最も重要な詳細は、見栄えの良い溶接を実現するために使用できる 4 つの MIG 溶接パターンです。オーバーヘッド MIG 溶接では、MIG ガンを溶接の方向に 5 ~ 35 度の角度で傾ける必要があります。
パターンは、流れに沿って動く方法を見つけ出し、均一性と滑らかさをもたらす際に安定感をもたらします。 ホイップ パターン テクニックを使用した溶接手順 ストリンガー ビードと隅肉溶接ジョイントは、ホイップすることで大きなメリットが得られます。 サークル溶接テクニックの溶接パターン ホイップとウィーブは、どちらも円形で作業することで簡素化できます。 MIG 溶接は、製造、建設、自動車など、多くの業界で使用されています。 ウィーブは幅の広い溶接に使用されますが、船舶では禁止されています。
MIG 溶接は、小さな装飾品から大型のプレハブ建築部品まで、あらゆる生産分野で使用されています。また、手作業で大量生産される製品にも使用されています。自動車の溶接は、技術の進歩によりますます機械化されています。MIG 溶接は自動車を修理する最も効果的な方法ですが、最善の選択肢となるのはごくまれです。ロボット工学により MIG 溶接の自動化が進み、より高い出力とより信頼性の高い溶接が可能になりました。
MIG 溶接は、その汎用性、スピード、使いやすさから、大量生産が優先される産業環境にとって貴重なツールとなっています。利点: 大量の溶接を高速に実行でき、習得が簡単で、さまざまな金属に対応し、堅牢で完璧な溶接が可能で、効率を犠牲にすることなく、少ないパスでより多くのフィラー メタルを移動できます。欠点: スティック溶接に比べて柔軟性が低く、初期投資が高く、TIG 溶接ほど魅力的ではありません。
ツーリングとCNCの絞り加工能力を最大化する
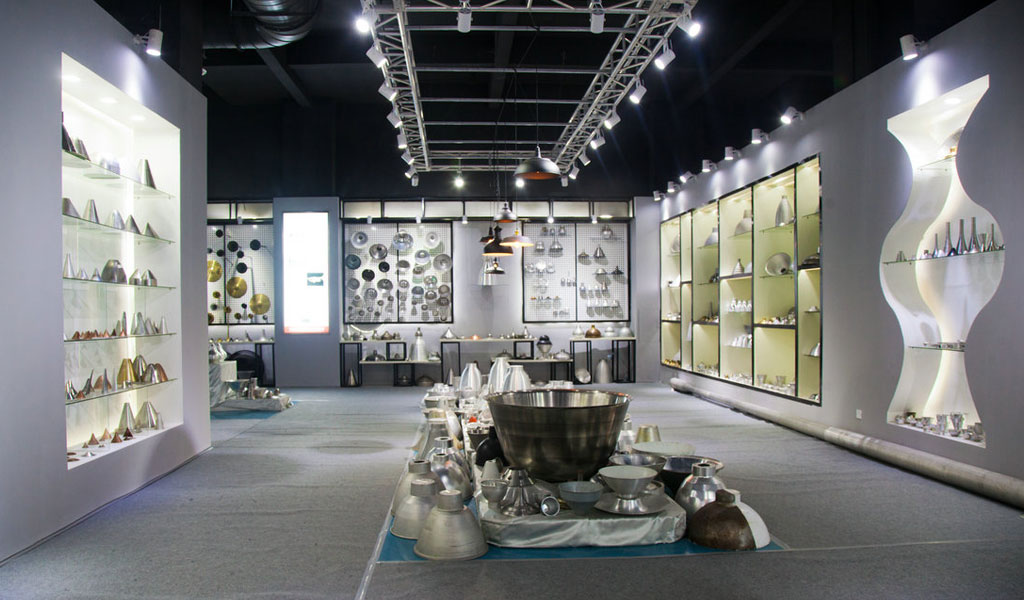
BE-CU 中華のへら 絞り 会社では、過度の摩耗やストレスの兆候を監視しながら、設備を最大限に活用しています。さらに、より新しい最新の設備を検討し、製造能力をサポートまたは向上できる設備に投資しています。当社のチームは機械やツールに細心の注意を払っているため、部品の品質と生産性に悪影響を与えないように定期的にメンテナンスも行っています。
BE-CUの設計とエンジニアリングサポート
BE-CUは、社内の設計およびエンジニアリングチームを活用して、部品生産の初期コンセプトからお客様を支援することができます(提供された設計に対して広範な設計サポートも提供可能です)。私たちのチームは、プロジェクトの開始から終了まで、お客様と定期的かつ透明なコミュニケーションを取りながら、望ましい最終目標に向かって作業を進め、明確な進行方向を提供します。
BE-CUの設計およびエンジニアリングサポートプロセスの一例:
- クライアントがBE-CUチームに部品図面を提供します。
- 当社のエンジニアリングチームが図面をレビューし、ベストプラクティスに基づいて調整を行います。お客様のニーズに応じて、成形または絞り部品を最も効果的に達成する方法を推奨します。
- 図面と設計は必要に応じて改訂され、完璧な形に仕上げられます。財務的な実行可能性も最優先事項として考慮されます。
- 主要な目標は、全ての部品の適合性、形状、機能性を実現することです。
- 研究開発は製造プロセスの重要なステップであり、BE-CUは概念実証や様々な検証要件のためにプロトタイピングサービスを提供しています。研究開発プロセスにおける金属成形については、当社のeBookをご覧ください。
BE-CUが提供する広範な社内サービス
この金属加工プロセスは、軸対称の高性能部品を製造します。スピン成形とも呼ばれ、材料を望ましい形状に切削するのではなく、金属ディスクまたはチューブを円錐形やその他の円形に変形させます。
へら絞りは、手動の手作業によるスピニングプロセスまたは自動CNCスピニングを使用します。BE-CUのへら絞り機能の利点には以下が含まれます:
- コスト削減
- 短いリードタイム
- 最大の設計柔軟性
- シームレスで高品質な構造
対応可能な金属には、ステンレス鋼、炭素鋼、アルミニウム、銅、インコネル、ハステロイ、チタン、ブロンズ、真鍮が含まれます。BE-CUは、センター間60インチから直径100インチまでのカスタム金属絞り部品を製造でき、材料の厚さは0.018インチから2.00インチまで対応可能です。
当社の CNC へら 絞り サービスで迅速なプロトタイプの作成について、今すぐお問い合わせください。こちらでチャットして直接見積もりを取得するか、無料のプロジェクトレビューをリクエストしてください。