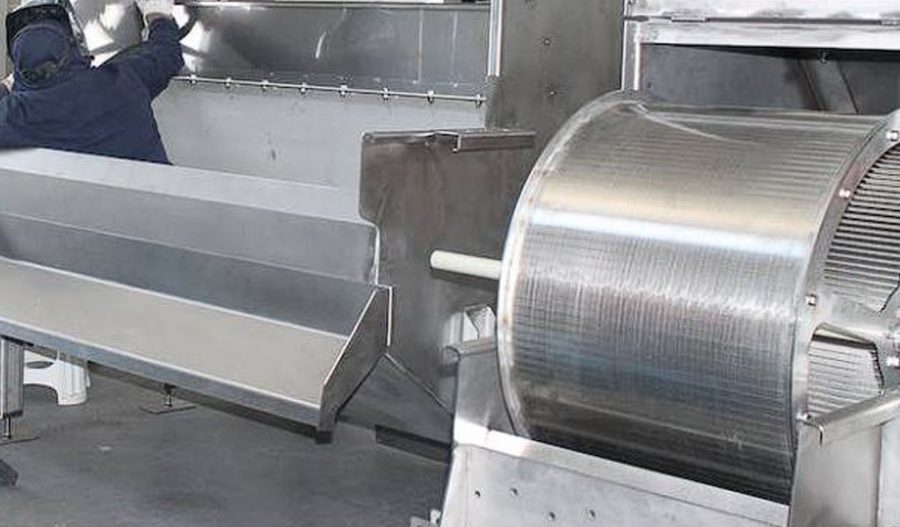
金属の圧延は、さまざまな状況での使用のために金属の可鍛性と適応性を大幅に向上させた興味深い手順です。金属の圧延は、インゴットを精密なシートに変えたり、さまざまな金属部品に複雑な形状を与えたりできるため、製造、自動車、航空宇宙、建設など、多くの分野で不可欠です。
この記事で、金属圧延の歴史、現在の実践、そして将来の可能性について興味深い旅に皆さんをお連れしたいと思います。金属に驚くべき強度、柔軟性、美しさを与える方法がこれから明らかにされるので、その詳細を理解する準備をしてください。
金属圧延とは何ですか?
金属加工において、圧延は金属成形工程の一種で、材料の厚さを減らし、材料全体に均一に厚さを分散させるために使用されます。1 組以上のロールを使用して金属ストックを減らします。熱間圧延は、プロセス中の金属の温度が圧延される金属の再結晶化温度よりも高い場合に発生します。冷間圧延は、金属の温度が再結晶化温度よりも低いプロセスを指します。
今日は、圧延の目的、利点、欠点、定義、方法、動作原理、種類、用途、熱間圧延と冷間圧延、潤滑剤の目的などについて説明します。
金属を成形する方法の 1 つは、圧延と呼ばれるプロセスです。このプロセスでは、材料を 2 組のローラーの間に通して、厚さを減らしたり均一にしたりします。このプロセスには、熱間圧延と冷間圧延の 2 つの技術があります。純粋な量に関して言えば、熱間圧延はアプリケーション内の他のすべての操作を圧倒し、冷間加工技術の中では冷間圧延が主流です。
ロールスタンドは、それぞれ 1 組のロールを保持し、簡単な金属加工用のロールミルに組み合わされています。構造用鋼、棒鋼、レールは、1 枚の鋼板から圧延できる製品のほんの一部です。圧延ミルと呼ばれる一部の製鉄所では、半完成の鋳造品を加工して完成品に変えます。
ローリングプロセスの実際の仕組み
圧延工程では、材料のストックを 2 つ以上のローラーの間で移動させて薄くし、厚さを均一に保ちます。この方法ではインゴットの断面に重点が置かれるため、プレスされた金属またはインゴットの厚さは減少します。材料を圧延すると、長さは長くなり、厚さは薄くなりますが、幅は同じままです。
熱間圧延と冷間圧延
熱間圧延
熱間圧延は金属加工で使用される方法で、材料を再結晶点よりも高い温度に加熱します。ただし、再結晶化のため、金属は強く加工できません。
冷間圧延
高温で行われる熱間圧延とは異なり、冷間圧延は低温、通常は室温で行われます。その結果、ひずみ硬化、表面品質の向上、および安定した許容誤差により、強度が 20% 向上します。
ローリングアプリケーション
熱間圧延は、通常、平らな金属板や、線路のような単純な断面の製造に使用されます。熱間圧延金属は、一般的に次のようなさまざまな目的で使用されます。
- トラック用車両シャーシ
- チューブと配管
- 自動車用ホイール、リム、クラッチプレート
- 水ヒーター
- 農作業用具
- ストラップ
- 鉄骨構造
- スタンピング
- 鉄道ホッパ車の材料および部品
- 高速道路や道路の装甲板
- 棚とクローゼットの扉
- ディスク
冷間圧延鋼は、建築資材、スチールドラム、給湯器、ヒンジ、チューブ、棚、照明器具、金属容器、給湯器、フライパン、ファンブレード、芝刈り機、電子機器キャビネット、家具など、さまざまな製品に使用されています。
私たちが日常的に使用するほとんどすべてのものは、この圧延金属の用途のリストに示されているように、冷間圧延または熱間圧延を使用して製造されています。
ローリングプロセス
ローリングには次のような多くの種類があります。
- ロールを形成する
- 成形ロール
- 平らに巻く
- 指輪を巻く
- 圧延による構造の形成
- ピッチングの調整と
- 鍛冶場を転がす
圧延機の種類
圧延工場の主な5つのカテゴリーは次のとおりです。
- 2段式圧延機
- 3段に積み重ねられた圧延機
- ローラーミルを4段に積み重ねる
- 平行圧延機
- 圧延機クラスター
転がり潤滑
ロールと金属は、圧延プロセス全体にわたって摩擦を生じます。そのため、潤滑は非常に重要です。さらに、摩擦はロール間の作業を促進するため有益です。このため、圧延作業には適切な潤滑剤を選択することが重要になります。潤滑剤の存在がなくなるか、適切なレベル以下に減少することが時々あるためです。
鋼の冷間圧延時には、パラフィンなどの低粘度の流体潤滑剤が必要です。アルミニウム、銅、およびそれらの合金などの非鉄金属は、表面を損傷する恐れなく、熱処理前にパラフィンで洗浄できます。
熱間圧延では潤滑は不要ですが、堆積したスケールを除去するために、噴出する水によって発生する蒸気が必要です。ただし、油の代わりにグラファイトグリースを塗布します。
ローリングで最も頻繁に起こる問題とその解決方法
金属圧延は、古代の手作業から最先端の工場機械へと進化を遂げてきました。これは複雑で要求の厳しいプロセスであり、細心の注意が必要です。製造方法に関係なく、いくつかの典型的な圧延欠陥が発生する可能性があります。
圧延とは、金属材料をローラーの間に通して厚さを減らし、均一にすることです。温度が再結晶点よりも低い場合、このプロセスは「冷間圧延」と呼ばれます。熱間圧延は、材料を再結晶点を超える温度にさらすプロセスを指します。
ローリングで最も頻繁に発生する欠陥とその修正方法を以下に示します。
エッジのひび割れ
熱間圧延と冷間圧延の両方で金属の端が割れることがあります。これは、ワークピースの表面が二次的な引張応力を受けるために発生します。不均一な加熱、圧延、または過度の焼入れはすべて、これらの亀裂の形成に寄与する可能性があります。
エッジのひび割れを修復するにはどうすればいいですか?
エッジの破損はトリミングによって修復できます。さらに、張力による伸張とローラーによる水平調整によってエッジのひび割れを防ぐことができます。最後に、エッジ ロールを使用すると、不均一なロールを滑らかにすることができます。
ワニのひび割れ
金属材料を圧延すると層が分離し、ワニ皮のようなひび割れのある板が形成される可能性があります。そのため、圧延面に貼り付けて個々のロールの経路をたどるのではなく、平面で金属シートが製造されます。
シートの厚さ全体にわたる応力と歪みの不均一な分布が、ワニ口割れの主な原因です。材料の中央部分は他の部分よりも広がる傾向があり、冶金学的に弱い部分になります。
ワニ口のひび割れは修復できますか?
ワニ割れを防止する一般的な方法の 1 つは、ローラーにキャンバーを付けることです。ローラーに反対方向のキャンバーが適用されるため、たわみ後、シートと接触する表面は平らになります。
波状のエッジ
端の繊維が中央の繊維より著しく長いのは、よくある圧延不良です。これは、凹型ローラーが曲げによって弾性変形を起こしたときに発生します。中央が厚いため、側面を長くする必要があります。
端が曲がらないようにするにはどうすればいいですか?
波状のエッジがある場合には、油圧ジャッキの使用が効果的です。油圧ジャッキはロールの弾性変形を制御できるためです。また、より細い直径のロールを使用することで生産性が向上します。
ジッパーのひび割れ
これは、金属シートの中央に微細な亀裂が形成されるためです。ジッパーの亀裂は、通常、圧延工程の強い圧力でロールが座屈したときに発生します。その結果、中央に引張張力が生じ、端に圧縮応力が生じます。ジッパーの亀裂は、均質な変形によってワークピースに生じる引張応力によって発生します。
壊れたジッパーはどうすればいいですか?
ロールは、キャンバー加工することでジッパー破損から保護されます。キャンバー加工とは、内径が外径よりも若干大きくなるように加工することです。
センターバックリング
圧延工程で残留張力が残り、最終的にバランスが取れて、この欠陥につながります。金属が中央で座屈すると、中央の繊維が端の繊維よりも長くなります。熱間圧延機または冷間圧延機のクラウンが高すぎると、圧延機は中央で外側に転がります。中央座屈は、構造要素が横方向にたわんだ結果であると理解できます。
センターバックルの挑戦
中心の座屈を防ぐには、クラウン ロールを使用します。ロールの放物線曲線により、温度、材質、変形の問題が解消されます。
金属ロール成形の利点
金属ロール成形には、他の金属加工方法に比べていくつかの大きな利点があります。
生産における最大限の効率
ロール成形は、軽量の金属部品を大量生産するための高速かつ効率的な方法です。コンピューター支援設計 (CAD) ソフトウェアが構造構成と設計パターンを管理するため、人的介入の必要性が減ります。溶接とパンチングは、効率性を向上させるためにロール成形機械に統合できるインライン サービスのほんの一例です。このプロセスは、仕上げが少なくて済み、廃棄物もほとんど発生しないため、非常に効率的です。
一貫した精度
ロール成形は、コンポーネントを段階的に曲げて正確な結果と厳密な許容差を実現する増分プロセスです。さらに、CAD ソフトウェアは金属成形プロセス全体を管理して、高品質で均一な最終結果を保証します。
汎用性
ロール成形を使用して、鉄または非鉄金属で作られたさまざまな厚さのシートをプロファイル曲げすることができます。コンポーネントは、単一の曲げから複雑な形状パターンまで何でも可能で、どちらも簡単に設計できます。この方法は、U チャネル、C チャネル、その他の開いた形状や閉じた形状を作成するのに最適です。
分数次元の機能
ロール成形技術では、1 セットの装置だけでさまざまな長さの金属部品を作成できるため、継ぎ目が不要になります。たとえば、スタッドとトラックの技術では、必要な長さのフレームを作成できます。さらに、ロール成形装置は、ブレーキ プレスやスタンピング手順よりも長いシート状の材料を処理できます。
コスト効率
ロール成形後の完成品はより精密になるため、原材料の無駄が少なくなります。部品の品質が高く、一貫性があるため、トリミング、溶接、廃棄が少なくなります。ロール成形ビジネスでは、規模の経済により、より低い単価を消費者に還元できます。
結論
金属の圧延は、材料の厚さを減らすと同時に、その減少を材料全体に均等に広げる金属成形技術です。材料のストックを 2 つ以上のローラー間で移動させると、材料は薄くなり、厚さが均一になります。「熱間圧延」という用語は、金属の温度が再結晶温度を超える技術を指します。再結晶温度より低い温度で金属を圧延することは、冷間圧延として知られています。議論のトピックには、圧延の目的、利点、欠点、定義、方法、動作原理、タイプ、用途、熱間圧延と冷間圧延、および潤滑剤の機能が含まれます。
熱間圧延は、材料を再結晶点以上に加熱して圧延する金属加工プロセスです。低温圧延は「冷間圧延」とも呼ばれ、強度を最大 20% 向上させることができます。自動車のシャーシ、チューブ、パイプ、ホイール、リム、クラッチ プレート、給湯器、農具、ストラップ、鉄骨構造、スタンピング、鉄道ホッパー車の材料と部品、高速道路や街路の装甲板、棚やクローゼットのドア、ディスクなど、数多くの製品が熱間圧延金属に依存しています。モジュレーテッド ピッチング、鍛造圧延、リング圧延、フラット圧延、鍛造圧延はすべて圧延プロセスの例です。蒸気は、蓄積したスケールを除去し、圧延に十分な潤滑を維持するために使用されます。
ローリングに関する最も一般的な問題は、どの技術でも発生する可能性があります。ローリングとは、金属材料をローラー間で移動させて厚さを減らし、均質化するプロセスです。エッジのひび割れ、ワニのひび割れ、波状のエッジ、ジッパーのひび割れは、ローリング不良の典型的な例です。トリミング、張力による伸張、ローラーの水平調整、エッジ ロールの使用はすべて、ひび割れたエッジを修復するための実行可能なオプションです。ローラーのキャンバーを調整すると、ワニのひび割れがなくなります。
油圧ジャッキを使用すると、波状のエッジが丸まるのを防止できます。反り加工は、ジッパーの裂け目を修復する効果的な方法です。ロール成形金属により、軽量金属部品を大規模に迅速かつ効率的に生産できます。この方法では、部品を 1 つずつ曲げて、許容誤差を徐々に狭めていくため、段階的なプロセスになります。最大限の効率、一貫した精度、多様性、小寸法での対応、コスト効率、規模の経済、単位コストの低減は、金属ロール成形の利点のほんの一部にすぎません。
構造部品を横方向に曲げると、中央部分が座屈する可能性があります。クラウン ローラーは中央部分の座屈を防ぐのに効果的です。最大限の効率、一貫した精度、多様性、小寸法での対応、コスト効率、規模の経済、単位コストの低減は、金属ロール成形のメリットのほんの一部にすぎません。
ツーリングとCNCの絞り加工能力を最大化する
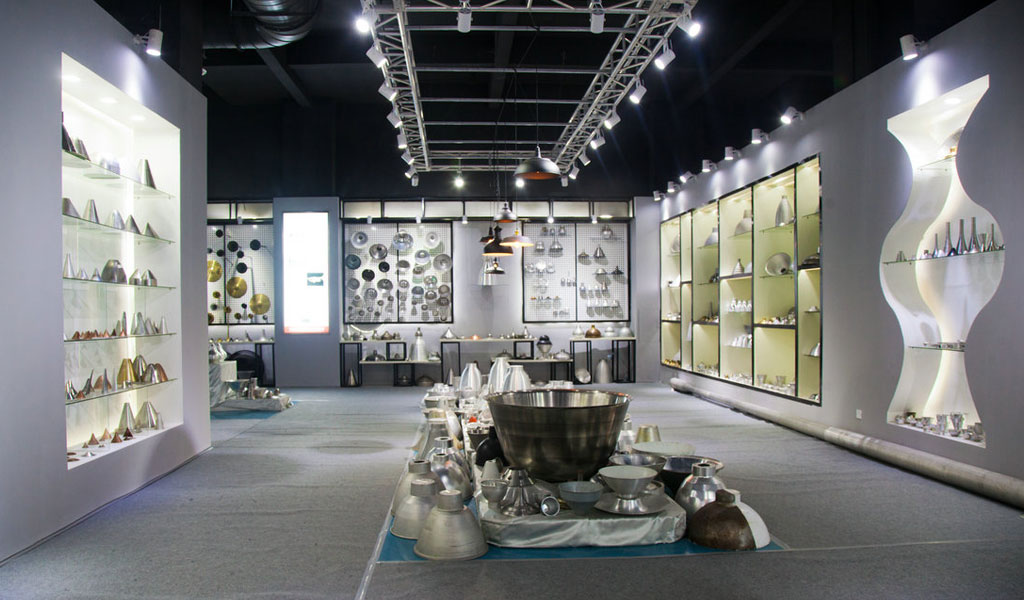
BE-CU 中華のへら 絞り 会社では、過度の摩耗やストレスの兆候を監視しながら、設備を最大限に活用しています。さらに、より新しい最新の設備を検討し、製造能力をサポートまたは向上できる設備に投資しています。当社のチームは機械やツールに細心の注意を払っているため、部品の品質と生産性に悪影響を与えないように定期的にメンテナンスも行っています。
BE-CUの設計とエンジニアリングサポート
BE-CUは、社内の設計およびエンジニアリングチームを活用して、部品生産の初期コンセプトからお客様を支援することができます(提供された設計に対して広範な設計サポートも提供可能です)。私たちのチームは、プロジェクトの開始から終了まで、お客様と定期的かつ透明なコミュニケーションを取りながら、望ましい最終目標に向かって作業を進め、明確な進行方向を提供します。
BE-CUの設計およびエンジニアリングサポートプロセスの一例:
- クライアントがBE-CUチームに部品図面を提供します。
- 当社のエンジニアリングチームが図面をレビューし、ベストプラクティスに基づいて調整を行います。お客様のニーズに応じて、成形または絞り部品を最も効果的に達成する方法を推奨します。
- 図面と設計は必要に応じて改訂され、完璧な形に仕上げられます。財務的な実行可能性も最優先事項として考慮されます。
- 主要な目標は、全ての部品の適合性、形状、機能性を実現することです。
- 研究開発は製造プロセスの重要なステップであり、BE-CUは概念実証や様々な検証要件のためにプロトタイピングサービスを提供しています。研究開発プロセスにおける金属成形については、当社のeBookをご覧ください。
BE-CUが提供する広範な社内サービス
この金属加工プロセスは、軸対称の高性能部品を製造します。スピン成形とも呼ばれ、材料を望ましい形状に切削するのではなく、金属ディスクまたはチューブを円錐形やその他の円形に変形させます。
へら絞りは、手動の手作業によるスピニングプロセスまたは自動CNCスピニングを使用します。BE-CUのへら絞り機能の利点には以下が含まれます:
- コスト削減
- 短いリードタイム
- 最大の設計柔軟性
- シームレスで高品質な構造
対応可能な金属には、ステンレス鋼、炭素鋼、アルミニウム、銅、インコネル、ハステロイ、チタン、ブロンズ、真鍮が含まれます。BE-CUは、センター間60インチから直径100インチまでのカスタム金属絞り部品を製造でき、材料の厚さは0.018インチから2.00インチまで対応可能です。
当社の CNC へら 絞り サービスで迅速なプロトタイプの作成について、今すぐお問い合わせください。こちらでチャットして直接見積もりを取得するか、無料のプロジェクトレビューをリクエストしてください。