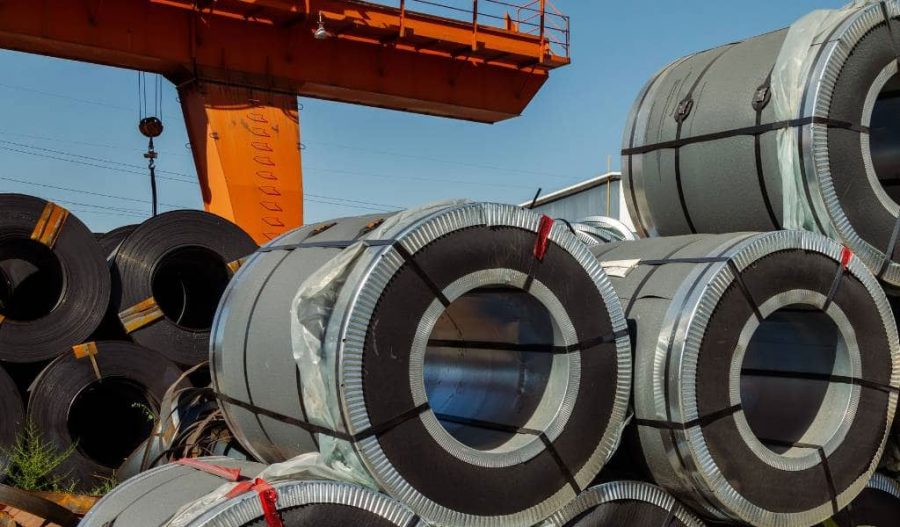
複雑な金属加工の世界では、鋼鉄をシート、プレート、またはさまざまな構造形状に圧延することが不可欠なステップです。このステップは、多くのエンジニアリングおよび建築プロジェクトに不可欠です。 圧延できる鋼鉄の最も厚い厚さは、作業が完了できるかどうかだけでなく、コスト、耐用年数、全体的な外観にも影響を与える重要な要素です。鋼鉄の圧延は、高層ビルや橋の建設から自動車や大型機械の製造まで、生活のあらゆる分野に影響を与えます。
したがって、鋼鉄圧延のこの部分について詳しく学ぶことは、金属加工ビジネスの技術的な側面について学ぶための優れた方法です。 このブログは、鋼鉄をどのくらいの厚さに圧延できるかを決定する要素、さまざまな厚さを実現するために使用するツールと方法、そしてこれらの能力がより重要な金属加工分野にとって何を意味するかを明らかにすることで、鋼鉄圧延の奥深さを探求することを目的としています。
鋼材圧延を理解する方法
鋼の圧延は、溶融金属、ガラス、またはその他の物質をさまざまな形状に変換する基本的な金属加工プロセスであり、主に棒、シート、ロッド、ワイヤなど、長さに比べて断面積が小さい製品に重点が置かれています。この方法は、金属、特に建設業やその他の多くの産業で重要な役割を果たしている鋼を成形するための最も広く使用されている技術です。
このプロセスでは、金属を、同じ速度で反対方向に回転する一対のローラーの間を通過させます。ローラー間の間隔は、金属の厚さよりわずかに小さくなっています。この動作により、金属の全体的な体積は維持しながら、金属の厚さが減ります。
鋼鉄の圧延の真髄
鋼の圧延は、鋼が熱い間(熱間圧延)または冷たい間(冷間圧延)のいずれかで実行できます。それぞれの方法は異なる要件を満たし、異なる結果をもたらします。熱間圧延は鋼の再結晶温度以上で行われるため、鋼が硬化するのを防ぎ、厚さの大幅な変化を可能にします。
一方、冷間圧延は再結晶温度より低い温度で行われ、目的の形状にするためにはローラーを複数回通す必要があることがよくあります。この方法では、熱間圧延よりも優れた機械的特性、より細かい表面仕上げ、より狭い寸法公差を備えた鋼が生産されます。
圧延工程の種類
圧延工程は「万能」なアプローチではなく、さまざまな方法と機械を駆使して、各製品が顧客の特定のニーズを満たすようにします。圧延工程には主に次の 2 つの種類があります。
冷間圧延: このプロセスは室温で実行され、ひずみ硬化によって鋼の強度を高め、表面仕上げを改善します。
熱間圧延は 鋼の再結晶温度以上で行われるため、金属の成形性がさらに向上し、成形が容易になります。
それぞれの圧延プロセスには利点があり、加工する金属の種類と希望する最終製品に基づいて選択されます。圧延プロセスの汎用性により、各プロジェクトの正確な仕様に合わせて、幅広い金属部品や製品を生産できます。
鋼材圧延の重要性
圧延は、板金、ストリップ、ワイヤ、リボンなどの精密材料の製造に不可欠です。そのスピード、精度、効率性により、金属加工業界では欠かせない手法となっています。圧延金属は、建設、自動車、航空宇宙、包装などさまざまな分野でも使用されており、このプロセスの汎用性と重要性が際立っています。
圧延工程で使用される材料と機械
圧延工程の材料は重要です。すべての金属が適しているわけではないからです。効果的に圧延するには、材料は延性や展性などの特定の特性を備えている必要があります。圧延に使用される機械は圧延機と呼ばれ、高度に発達しており、さまざまな種類の金属や合金を処理できるため、高品質の圧延製品を確実に生産できます。
圧延における鋼板の厚さに影響を与える要因
鋼をさまざまな厚さに圧延することは、多くの要因の影響を受ける機械的および材料科学原理の複雑な相互作用です。これらの要因を理解することは、圧延鋼製品の望ましい厚さと品質を実現するために不可欠です。ここでは、圧延プロセス中に鋼の厚さに影響を与える主な要素を包括的に説明します。
ワークピースと圧延機のダイナミクス
圧延製品の厚さの変動は、ワークピースと圧延機の両方に関連する要因によって影響を受けます。主な要因は次のとおりです。
支持ロールの偏心: これにより、ロールギャップに周期的な変動が生じ、ロール製品の厚さの均一性に影響します。
圧延機の作業スタンドの弾性変形:圧延中にかかる力により、圧延機がわずかに変形し、ロール間の隙間が変化することがあります。
熱膨張と摩耗: 圧延プロセス中にロールとワークピースが熱くなると、熱膨張によってロールのギャップが変化することがあります。時間の経過によるロールの摩耗によってもギャップのサイズが変わり、厚さに影響します。
鋼板の張力の変動: 鋼板が圧延機に入るときと出るときに張力が異なると、厚さにばらつきが生じる可能性があります。
スラブの厚さと変形抵抗: 鋼スラブの初期の厚さと圧力下での変形抵抗は、ロールの最終的な厚さに影響を与える可能性があります。
弾性曲線による理論分析
主に弾性曲線と圧延機のバウンス方程式による圧延プロセスの理論的分析では、圧延中のワークピースの厚さを決定する 4 つの主な要因が強調されています。
圧延圧力: ロールが鋼材に及ぼす力は、厚さの減少度合いに直接影響します。
アイドルロールギャップ: 圧延開始前のロール間の初期ギャップは、厚さ減少の基準を設定します。
圧延機の縦方向剛性係数: この係数は、圧延機のフレームが圧延圧力下でどれだけ曲がるかを決定し、間接的にロールギャップ、ひいては鋼板の厚さに影響します。
ベアリング油膜の厚さ: ロールと鋼材の間の潤滑により鋼材がわずかに保護され、最終的な厚さに影響します。
圧延工程における実用上の考慮事項
これらの要因は、実際の圧延プロセスでは個別に作用するのではなく、同時に作用することがよくあります。これらの変数の複合的な影響により、圧延における鋼板の厚さを制御するための総合的なアプローチが必要になります。観察された厚さの変化に応じて圧延プロセスを調整する場合でも、初期設定の一部として調整する場合でも、望ましい製品仕様を達成するには、これらすべての要因を考慮する必要があります。
鉄鋼圧延における技術の進歩
鉄鋼圧延業界では、過去数十年にわたって大幅な技術進歩が見られ、鉄鋼の加工方法に革命をもたらし、最終製品の品質を向上させてきました。これらの革新は、新しい圧延機技術の導入からプロセス制御や材料処理の進歩まで、圧延プロセスのさまざまな側面に及びます。ここでは、現代の鉄鋼圧延業界を形作った基本的な技術進歩について探ります。
圧延技術のアップグレード
最近の圧延工場の改良は、生産コストの削減と鋼板製品の品質向上に極めて重要な役割を果たしています。業界では、熱間圧延と冷間圧延の両方で新しい技術と製造の進歩が導入されています。鉄鋼業界の統合により、工場間での技術革新の共有が促進され、これらの進歩を実行するための最適な環境が整いました。
よりスマートな制御システムと計測機器
現代の圧延工場は、高度に自動化されたサイバーフィジカルシステムへと進化しました。現在では、ゲージと形状の測定機能が改良された産業用コンピューターとスマートセンサーによって監視および制御されています。適応制御モデルによって圧延力が リアルタイムで調整され、高精度のサーボ電気モーターが油圧システムに取って代わり、圧延プロセスの精度と効率が向上しています。
高度なシミュレーションおよび設計ソフトウェア
有限要素解析や熱機械モデリングなどのソフトウェア ツールにより、圧延力、温度の影響、製品特性の予測精度が向上しました。これらのシミュレーションにより、エンジニアは実際の試運転前に最適なロール パス スケジュールと制御戦略を設計でき、圧延プロセスにおける試行錯誤を大幅に削減できます。
より安全でクリーンな工場
職場の安全性と環境の持続可能性の向上に重点を置くことで、高度な煙抽出システムと防音材が開発されました。これらのアップグレードにより、空気の質が向上し、騒音公害が軽減され、挟み込み防止装置、ライトカーテン、人間工学に基づいたハンドリング装置によって作業員が保護されます。
新しいミル構成
圧延機の設計における革新により、特殊な製品向けに最適化された独自の圧延機構成が生まれました。協調型せん断機、スリッター、ローラーを備えたインライン圧延機により、シングルパス生産が可能になり、小径ロール クラスター圧延機により、これまで実現不可能だった形状にも対応できます。連続圧延プロセスと新しい合金向けに設計された圧延機により、ロールの品質とスループットが向上します。
革新的な金属の移送と取り扱い
自動化されたストックリール、コンベア、およびコイラーにより、ミルスタンド間のダウンタイムをゼロにして、バランスの取れた材料フローが実現します。インテリジェントな転送システムが同期して連続圧延を行い、自動調整コイラーと張力制御により、最終ロールが過度に伸びることなく適切に巻き取られます。
電力と効率の改善
アップグレードされた AC 可変周波数モーター ドライブにより、速度制御とエネルギー効率が向上します。潤滑フローの最適化により摩擦と無駄が削減され、現場での熱の捕捉と断熱により熱エネルギーが節約されます。これらのアップグレードは、圧延電力消費の削減とグリーン製造原則の採用に重点を置いています。
ビッグデータ分析の活用
改良されたセンサーとクラウドベースの分析を統合することで、製品の寸法、機器の振動、温度変化に関する膨大なデータセットをキャプチャして分析できるようになりました。機械学習アルゴリズムは、リアルタイム データと履歴パターンを組み合わせて圧延プロセスを改良し、人間の能力を超えたパフォーマンスの一貫性を実現します。
インテリジェントローリングの未来
今後、圧延工場では、より包括的なプロセス制御、組み込みの欠陥検出、予知保全アラート、自律最適化が統合されることが期待されています。冶金科学とデジタル化されたシステムを組み合わせることで、効率と精度の新たな領域が開かれ、運用プロセスを超えて分子レベルでの戦略的な材料エンジニアリングへと進むことになります。
結論
鋼の圧延は金属加工において極めて重要であり、溶融金属をさまざまな形状に変形します。このプロセスでは、金属を、同じ速度で反対方向に回転する一対のローラーの間を通過させます。ローラー間の間隔は、金属の厚さよりわずかに小さくなっています。鋼の厚さは、作業の完了、コスト、寿命、外観に影響を与える重要な要素です。
鋼の圧延は、熱間圧延(熱間圧延)または冷間圧延(冷間圧延)で実行できます。それぞれ異なる要件に対応し、異なる結果をもたらします。圧延プロセスには、室温で実行される冷間圧延と、鋼の再結晶温度を超える温度で実行される熱間圧延の 2 つの主な種類があり、これにより優れた成形性と簡単な成形が可能になります。
すべての金属が圧延に適しているわけではないため、圧延工程で使用する材料は非常に重要です。圧延に使用される機械は圧延機と呼ばれ、高度に発達しており、さまざまな種類の金属や合金を処理できるため、高品質の圧延製品を確実に生産できます。
圧延中に鋼板の厚さに影響を与える要因には、支持ロールの偏心、圧延機の作業スタンドの弾性変形、熱膨張と摩耗、鋼板張力の変化、スラブの厚さと変形抵抗などがあります。これらの要因を理解することは、圧延鋼製品の望ましい厚さと品質を実現するために重要です。
鉄鋼圧延業界では、過去数十年にわたって大幅な技術進歩が見られ、鉄鋼の加工方法に革命が起こり、最終製品の品質が向上しました。これらの進歩は、新しい圧延機技術の導入からプロセス制御や材料処理まで、圧延プロセスのさまざまな側面に及びます。
圧延機の技術がアップグレードされたことで、生産コストが削減され、鋼板製品の品質が向上しました。鉄鋼業界の統合により、工場間での技術革新の共有が促進され、これらの進歩を実装するための最適な環境が整いました。現代の圧延機は、産業用コンピューターとスマートセンサーによって監視および制御される、高度に自動化されたサイバーフィジカルシステムへと進化しました。高度なシミュレーションおよび設計ソフトウェアにより、圧延力、温度の影響、および製品特性の予測が向上し、圧延プロセスにおける試行錯誤が削減されました。
より安全でクリーンな工場が開発され、先進的な煙抽出システムと防音材により空気の質が向上し、騒音公害が軽減されました。新しい工場構成が登場し、材料の流れが最適化され、電力消費が削減されました。 ビッグデータ分析 により、製品の寸法、機器の振動、温度変化に関する膨大なデータセットを収集して分析できるようになりました 。
将来的には、圧延工場には、より包括的なプロセス制御、組み込みの欠陥検出、予測メンテナンスアラート、自律最適化が統合されることが期待されています。
ツーリングとCNCの絞り加工能力を最大化する
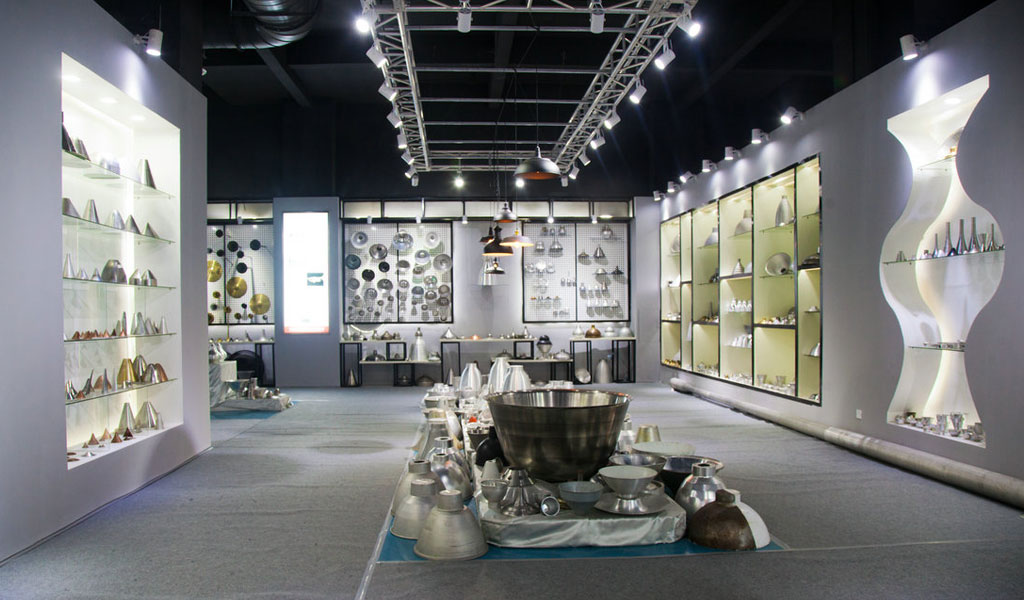
BE-CU 中華のへら 絞り 会社では、過度の摩耗やストレスの兆候を監視しながら、設備を最大限に活用しています。さらに、より新しい最新の設備を検討し、製造能力をサポートまたは向上できる設備に投資しています。当社のチームは機械やツールに細心の注意を払っているため、部品の品質と生産性に悪影響を与えないように定期的にメンテナンスも行っています。
BE-CUの設計とエンジニアリングサポート
BE-CUは、社内の設計およびエンジニアリングチームを活用して、部品生産の初期コンセプトからお客様を支援することができます(提供された設計に対して広範な設計サポートも提供可能です)。私たちのチームは、プロジェクトの開始から終了まで、お客様と定期的かつ透明なコミュニケーションを取りながら、望ましい最終目標に向かって作業を進め、明確な進行方向を提供します。
BE-CUの設計およびエンジニアリングサポートプロセスの一例:
- クライアントがBE-CUチームに部品図面を提供します。
- 当社のエンジニアリングチームが図面をレビューし、ベストプラクティスに基づいて調整を行います。お客様のニーズに応じて、成形または絞り部品を最も効果的に達成する方法を推奨します。
- 図面と設計は必要に応じて改訂され、完璧な形に仕上げられます。財務的な実行可能性も最優先事項として考慮されます。
- 主要な目標は、全ての部品の適合性、形状、機能性を実現することです。
- 研究開発は製造プロセスの重要なステップであり、BE-CUは概念実証や様々な検証要件のためにプロトタイピングサービスを提供しています。研究開発プロセスにおける金属成形については、当社のeBookをご覧ください。
BE-CUが提供する広範な社内サービス
この金属加工プロセスは、軸対称の高性能部品を製造します。スピン成形とも呼ばれ、材料を望ましい形状に切削するのではなく、金属ディスクまたはチューブを円錐形やその他の円形に変形させます。
へら絞りは、手動の手作業によるスピニングプロセスまたは自動CNCスピニングを使用します。BE-CUのへら絞り機能の利点には以下が含まれます:
- コスト削減
- 短いリードタイム
- 最大の設計柔軟性
- シームレスで高品質な構造
対応可能な金属には、ステンレス鋼、炭素鋼、アルミニウム、銅、インコネル、ハステロイ、チタン、ブロンズ、真鍮が含まれます。BE-CUは、センター間60インチから直径100インチまでのカスタム金属絞り部品を製造でき、材料の厚さは0.018インチから2.00インチまで対応可能です。
当社の CNC へら 絞り サービスで迅速なプロトタイプの作成について、今すぐお問い合わせください。こちらでチャットして直接見積もりを取得するか、無料のプロジェクトレビューをリクエストしてください。