表面処理
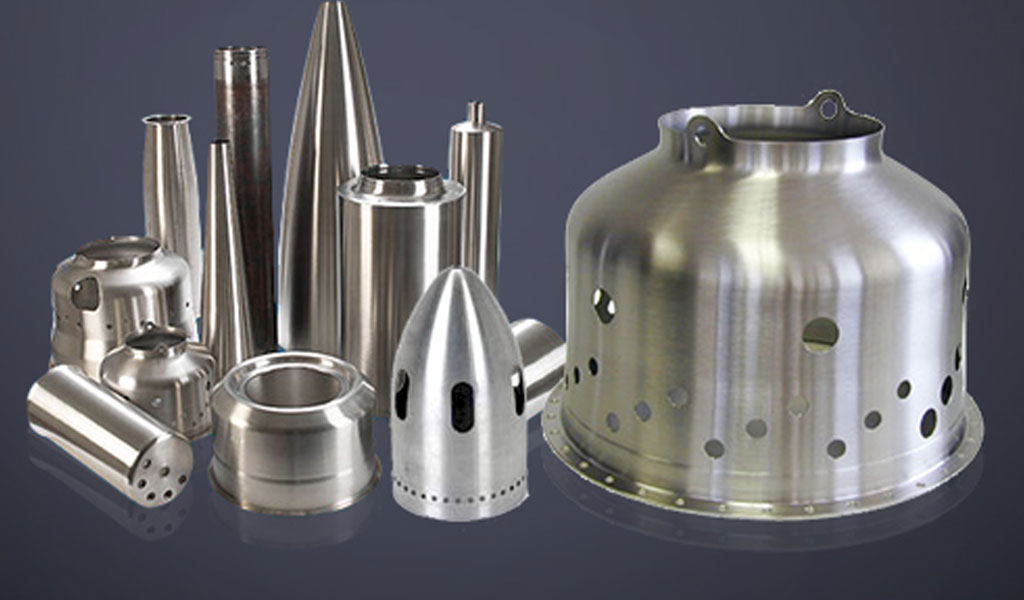
機械加工部品の表面品質は、機能性、耐久性、美観の観点から製造において非常に重要です。機械加工された表面には工具跡、バリ、欠け、その他の欠陥が含まれることが多いため、ほとんどの部品や製品では、望ましい仕上がりを得るために表面処理手順が必要です。
適切な後処理を施すことで、あらゆる表面欠陥に対処し、製品寿命を延ばすことができます。そのため、自動車、航空宇宙、医療など、精度と信頼性が不可欠なさまざまな業界では、後処理は製造の重要な側面となっています。
この記事では、表面処理の重要性、さまざまな仕上げ技術、機械加工部品に適した表面仕上げを選択する手順について説明します。
表面仕上げとは何ですか?
表面仕上げとは、製造後の表面の質感、粗さ、全体的な品質を指します。さらに、研磨、研削、サンドブラスト、コーティングなどのさまざまな表面処理プロセスを受けた後の表面の状態として定義することもできます。
表面仕上げは、粗さ、波状度、平坦度など、さまざまな数学的パラメータで表現できます。これらのパラメータは、さまざまな計測機器や測定原理で測定されることがよくあります。
以下は表面仕上げの測定で一般的に使用される手法です。
- 形状測定
- 干渉法
- スタイラスベースの楽器
- 視覚的な比較
これらの技術は、表面の特徴(波状度や平坦度など)の高さと間隔を測定します。
表面仕上げの価値:なぜ見逃してはいけないのか
表面仕上げの品質は、製品の性能に大きな影響を与える可能性があります。たとえば、表面が粗いと、可動部品の摩擦、磨耗、裂傷の原因になりますが、表面が滑らかであれば、製品の耐久性が向上し、磨耗を防ぐことができます。
それでは、製造業において表面仕上げがなぜ無視できないのか、そのポイントについて解説します。
- 最終製品の機能に影響します。
機械加工部品の表面品質は、測定精度、摩擦、摩耗、および個々の部品や製品の機能に関連するその他の要因に影響します。たとえば、表面仕上げが悪いと、時間の経過とともに劣化し、摩擦が大きくなり、機能が低下します。
- 製品の耐久性
製品の表面仕上げも耐久性に影響します。表面が粗い製品は、水分、汚れ、その他の不純物が溜まる微細な亀裂や細孔があるため、時間の経過とともに腐食、ひび割れ、劣化が起こりやすくなります。一方、表面が滑らかな製品は耐腐食性が高く、汚染物質が付着しにくいため、製品の寿命が長くなります。
- 外観とブランドイメージ
製品の表面仕上げは製品の外観に影響を与え、自動車、航空宇宙、消費財などの業界では特に重要です。
高品質の表面仕上げが施された製品はよりプロフェッショナルに見え、ブランドイメージと顧客の認識を高めることができます。さらに、高品質の表面仕上げは製品を顧客にとってより魅力的にすることで売上を伸ばすことができます。
- 業界標準への準拠
多くの業界では、部品や製品が特定の性能および耐久性の基準を満たすことを保証するために、表面仕上げまたは表面粗さ (Ra)の基準が設けられています。たとえば、航空宇宙業界では、航空機部品の安全性と信頼性を保証するために、厳格な表面仕上げ基準が設けられています。
したがって、高品質の表面仕上げは、さまざまな業界にわたるいくつかの特定の基準の基礎となります。
- 製品の費用対効果
高品質の表面仕上げは、摩耗や腐食による修理や交換が必要になる可能性が低くなるため、メンテナンス コストが削減され、製品の寿命が延びます。さらに、高品質の表面仕上げにより、追加のコーティングや仕上げが不要になり、製造コストが削減されます。
表面処理アプローチの分類
部品や製品を機械加工するための表面処理にはいくつかの方法があり、それぞれに利点と欠点があります。しかし、製造業では機械的、化学的、熱処理、コーティングによる表面処理が最も一般的です。それぞれについて詳しく説明しましょう。
機械表面処理
機械的な表面処理プロセスでは、機械的な力を使用して機械加工部品の表面を修正します。金属の仕上げは 、研削、研磨、ショットピーニング、サンドブラスト、ブラッシングなど、さまざまな方法で実行できます。
機械的な表面処理は、表面の傷を除去し、滑らかな表面を作り、材料の耐摩耗性を向上させるのに最適です。この方法により、特定の表面テクスチャや仕上げを生成し、材料の美観を向上させることができます。
化学表面処理
名前が示すように、化学表面処理では、適切な化学溶液を使用して機械加工された部品の表面を変更します。化学溶液は部品と反応し、腐食、酸化、摩耗に対する耐性を向上させる保護層を形成します。
化学表面処理を実現するための標準的な技術には、エッチング、陽極酸化、電気メッキ、不動態化などがあります。
コーティング表面処理
コーティング処理プロセスでは、材料の表面に薄い保護層を形成して、耐腐食性と耐摩耗性を高めます。この処理は、粉体塗装、電気メッキ、アロジンコーティング、化学蒸着、塗装などのさまざまな技術で実行できます。
熱処理
熱処理プロセスでは、熱を使用して材料の微細構造をカスタマイズすることで材料の特性を変更します。これは、焼鈍、焼入れ、焼き戻し、表面硬化などの技術によって実現できます。
熱処理仕上げは、材料の強度、靭性、延性などの機械的特性を改善し、特定の用途における性能を向上させるのに適しています。
利用できる表面仕上げにはどのような種類がありますか?
CNC 加工やその他の製造において、表面仕上げは高品質の最終製品を作成する上で重要な役割を果たします。望ましい表面品質を実現するために、メッキ、粉体塗装、亜鉛メッキ、陽極酸化、レーザークラッディングなど、さまざまな技術が利用できます。さまざまなCNC 表面仕上げの種類について、さらに詳しく説明しましょう。
メッキ仕上げ
基板上に金属の薄い層を堆積させて、魅力的で耐腐食性のある表面を作成するプロセスは、メッキ仕上げとして知られています。メッキ金属は、金からニッケル、亜鉛まで何でもかまいません。
金属メッキは装飾品や宝飾品に使用されるだけでなく、電子機器、自動車、航空宇宙部品の保護カバーとしても使用されます。
粉体塗装
粉体塗装は、製造業でよく使われる塗装方法で、乾燥して細かく粉砕した粉末を静電塗装で金属表面に塗布します。まず、機械加工した部品を染料粉末に浸します。次に、部品をオーブンで焼くと染料が溶けて耐久性のある保護層が形成されます。その結果、欠け、ひび割れ、色あせに強い、滑らかで均一な仕上がりになります。
粉体塗装仕上げは金属部品にも非金属部品にも使用できますが、金属表面仕上げには最適です。
亜鉛メッキ仕上げ
亜鉛メッキ仕上げとは、錆や腐食を防ぐために金属部品を亜鉛層でコーティングするプロセスを指します。金属が過酷な環境にさらされ、構造的完全性を維持するために保護が必要な建設、自動車、海洋などのさまざまな業界で使用されています。
亜鉛メッキ処理には、金属表面の洗浄と、さまざまな技術 (溶融亜鉛メッキ、電気亜鉛メッキ、スプレー亜鉛メッキ) によるコーティングという 2 つの主要なステップがあります。また、コーティングの厚さは用途によって異なり、数ミクロンから数ミリメートルの範囲になります。
陽極酸化仕上げ
陽極酸化処理は、機械加工された部品や製品、特に工業および航空宇宙用途で使用される製品の耐久性と外観を最適化するために使用されるもう 1 つの表面仕上げプロセスです。
このプロセスでは、電気化学堆積法を使用して金属表面に保護酸化物層を作成します。陽極酸化仕上げは特にアルミニウムに適用されますが、チタン、亜鉛、マグネシウムなどの他の金属にも使用できます。
複雑な形状の機械加工部品の表面仕上げには、粉体塗装に代わる陽極酸化処理が最適です。陽極酸化処理により、完成部品の色が長期間にわたって優れた状態で保持されます。
レーザークラッディング仕上げ
レーザークラッディングとは、レーザービームを使用して金属粉末を溶融して融合し、材料表面にコーティング層を作成することを指します。レーザークラッディング法によって形成されたコーティングは、基材の耐摩耗性、耐腐食性、強度、表面硬度を向上させます。
レーザークラッディングプロセスでは、レーザー出力、粉末供給速度、ビームサイズ、スキャン速度、層の厚さなど、いくつかの要因によって表面仕上げの品質が影響を受けます。たとえば、レーザー出力が高く、スキャン速度が遅いと、表面仕上げはより滑らかになります。
機械加工部品に最適な表面仕上げを選択するにはどうすればよいでしょうか?
機械加工部品に適した表面仕上げを選択することは、部品の望ましい機能と外観を実現するために不可欠です。ただし、表面仕上げは特定の部品または製品の仕様に完全に依存するため、機械加工プロジェクトに最適な表面仕上げ技術は存在しません。
機械加工部品や製品の表面仕上げ技術を選択するための手順を段階的に説明します。
ステップ1: 部品の機能を決定する
表面仕上げを選択する最初のステップは、部品の機能を決定することです。異なる用途では、望ましいパフォーマンスを実現するために異なる表面仕上げが必要です。たとえば、摩耗の激しい環境で使用される部品 (ベアリングやギアなど) には、摩擦を減らすために滑らかな表面仕上げが必要です。一方、海洋産業や化学産業などの腐食性の高い環境で使用される部品には、耐腐食性の高い表面仕上げが必要です。
考慮事項:部品の機能によって表面仕上げの要件が決まり、間違った表面仕上げを選択すると、製品が早期に故障したり、パフォーマンスが低下したりする可能性があります。
ステップ2: 部品の材質を特定する
2 番目のステップは、部品の材質を特定することです。表面仕上げの要件は、硬度、延性、熱伝導率などの特性にも左右されるからです。たとえば、アルミニウムなどの柔らかい材料には、鋼鉄などの硬い材料よりも滑らかな表面仕上げが必要です。
考慮事項:部品の材質によって表面仕上げの要件が決まり、不適切な表面仕上げを選択すると、部品が損傷したり、パフォーマンスが低下したりする可能性があります。
ステップ3: 加工プロセスを決定する
従来のフライス加工、CNC 加工、EDM など、部品の製造に使用される加工プロセスを決定します。加工後の表面仕上げは、部品の作成に使用される加工プロセスによって異なります。さらに、希望する仕上げを実現するのに適した表面仕上げ方法を分析するのに役立ちます。
考慮事項:製造プロセスによって表面仕上げの要件が決まり、間違った表面仕上げを選択すると、品質が低下したり、パフォーマンスが不安定になったりする可能性があります。
ステップ4: 表面仕上げの要件を指定する
表面仕上げは、通常、表面粗さ、つまり完全な平面からの表面偏差で指定されます。粗さは、マイクロメートル (µm) またはマイクロインチ (µin) 単位で測定されます。表面仕上げの要件は、通常、エンジニアリング図面または仕様で指定されます。
考慮事項:表面の粗さを避ける ために、仕上げ要件は、選択された製造プロセス、材料、および意図された用途で現実的かつ達成可能なものでなければなりません。
ステップ5: 表面仕上げ方法を選択する
最後のステップは、表面仕上げ方法を選択することです。希望する表面仕上げを実現するには、研削、研磨、サンドブラスト、化学処理など、いくつかの方法があります。方法の選択は、表面仕上げの要件、部品の材質、および使用する製造プロセスによって異なります。
考慮事項:表面仕上げ方法は、部品の仕様に応じて、再現性、コスト効率、一貫性が保たれている必要があります。
まとめ
表面処理は、あらゆる機械加工部品の機能性、性能、耐久性、美観の点で不可欠です。ただし、機械加工部品に適した表面仕上げを選択するには、部品の機能材料、機械加工方法、および仕上げ要件を十分に理解する必要があります。
BE-CUでは、お客様のニーズと専門エンジニアのコンサルティングに基づいて、さまざまな表面仕上げサービスを提供しています。当社にご連絡いただければ、部品の最適な性能と美観を実現する適切な仕上げを提供いたします。