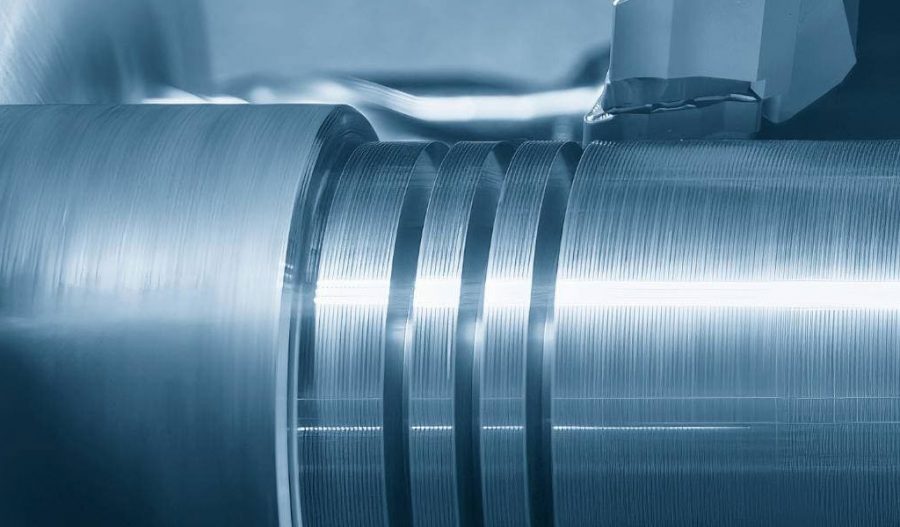
金属成形の重要な部分である金属スピニングは、当社の最新のブログ記事のテーマです。あらゆる製造プロセスの重要な側面は金属成形であり、特に板金成形は薄い金属板をさまざまな形に切断して成形することです。産業革命に始まったこの方法は、今も開発が進められており、昔ながらの方法論と最先端の科学が融合されています。
金属成形
板金成形では、薄い金属を切断し、シート、ストリップ、コイルなどのさまざまな形状に成形します。
板金成形とは何ですか?
メーカーは、薄い金属板、ストリップ、またはコイルを切断して特定の形状に成形する際に、板金加工 (板金成形または板金製造とも呼ばれる) に従事します。これらのプロセスの一般的な業界用語には、プレス加工やプレス成形が含まれます。これは、ほとんどのメーカーが一連の金型を使用してプレスでそれらを実行することに由来しています。
飲料缶、自動車のボディ、飛行機の胴体、家電製品、ファイリングキャビネット、金属製家具などは、厚さが通常 0.4 (1/64″) mm ~ 6 mm (1/4″) の標準金属板の消費者向けおよび商業向けの用途のほんの一部です。
プレスは機械加工ツールであり、金型を使用して金属板を成形するために使用されます。この手順は通常、室温で行われます。「スタンピング」は、このコンポーネントに付けられた名前です。
板金加工で使用される主な 3 つの技術は、引き抜き、せん断、曲げです。
共有
せん断加工は、名前の通り、パンチとダイを使用して板金をスライスし、せん断張力を生み出します。
曲げ
金属は直線軸の周囲に引き伸ばされます。これは曲げ加工の一般的な成形手順です。設計に応じて、曲げは短くなったり長くなったりします。
描画
板金加工業者は、カップや箱など、複雑な曲線や凹面のある部品を作るために、深絞りと呼ばれることもある絞り加工を使用します。この効果を得るために、金属板を金型の空洞に打ち込みます。
材料
低炭素鋼は、価格が安く、強度と展性に優れているため、最も人気があり、広く使用されているタイプの鋼板です。
- アルミナ材料
- 耐久性のあるステンレススチール
- 炭素鋼板
- ハイブリッド鋼
- 工具用ステンレス鋼
- 保護された金属
板金成形の長所と短所
板金加工の利点
金属成形は製造業者の間で非常に人気があります。金属成形には次のような利点があります。
- 材料の形状: チューブや板金など、さまざまな材料の形状に対応します。
- 原材料が適切に使用されているため、スクラップの量は通常、あったとしても非常に少量です。
- 効率的でわかりやすい: 数え切れない世代にわたって、実績のある技術が使用され、手順が完成しました。生産性、効率性、製品品質の向上はすべて、ロボット工学と自動化の成果です。
- 成形された製品は、成形プロセスにより強度が増し、一般的に機械的特性が向上します。
- ツールは通常、安価で使いやすく、さまざまな形にすることができます。
- 適応性 – これらの手順を採用することで、さまざまな形状を実現できます。
- 金属板は耐久性があり丈夫です。
- 強度や構造的完全性を損なうことなく、さまざまな形に簡単に成形できるのは、その可鍛性によるものです。
- さまざまな素材
- 他の押し出し、鋳造、鍛造方法よりも安価です。
- 鋳造や鍛造などの他の製造方法に比べて比較的安価です。
- 形状と機能の両面で非常に適応性があります。さまざまな金属を使用して、金属板を曲げたり、巻いたり、さまざまな形状やサイズに加工したりできます。
- 板金部品は、環境に対する耐性と高い引張強度を備えているため、長持ちします。
- 小ロット生産が可能なので、迅速なプロトタイピングに適しています。
- 薄い金属板で作られているため、金属板コンポーネントは軽量かつ頑丈です。強度要件は高いが重量制限は低い場合、この方法が適しています。
板金加工の欠点
金属成形の潜在的な欠点は次のとおりです。
- 不許容範囲 — 特に厚さに関しては、不許容範囲が大きく異なる可能性があります。
- 厚さの制限 — これらの手順では厚さに制限があります。
- 製造コストに寄与する要因としては、サイクルタイムが遅くなること、機器の電力要件が高いこと、ツールや機器が高価であることなどが挙げられます。
- 高額な設備・工具費
- アドバンスプランの価格
- 生産率の低下
- 肉体的な魅力
- 板金成形による製造を開始するために必要なツールと工具には、多額の初期投資が必要です。
- 製造時間とコストが増加するだけでなく、非常に複雑な設計は板金成形に適さない可能性があります。
- 多くの手作業が必要な板金成形は簡単ではありません。スタンピングなどの他の作業よりも結果が出るまでに時間がかかる場合があります。
金属トリミング
金属の切断は、原材料の加工における最も基本的なステップの 1 つです。金属はあらゆる製造プロセスに不可欠な要素です。したがって、金属切断プロセスは、直接的または間接的に製造部門全体を支えています。
金属切削加工には無数の用途があり、それぞれに独自の仕様があるため、多種多様な金属切削技術が開発されています。
このエッセイのテーマは、ニーズに合った適切な金属切断手順を見つける方法です。
金属切削とは何ですか?
金属切削は、金属加工物を複数の部品に分割する侵食プロセスまたは力を伴う減算型金属加工の一種です。放電とウォーター ジェットは、切削動作を行う方法の 2 つの例です。
さまざまな種類の金属切削方法
金属切削技術は、さまざまなカテゴリに大まかに分類できます。以下にいくつかの例を示します。
機械切断
機械的な切断手順では、鋭利な切削工具を金属に押し付けて材料を除去します。金属は通常、次の 4 つの方法のいずれかを使用して機械的に切断されます。
旋回
円筒形の金属棒やロッドは、通常、非回転切削工具を使用して旋削されます。この技術では、金属を外側から内側に切削します。内側から旋削する場合は、ボーリング技術が使用されます。
利点
- 速い切断速度
- 高精度
- 所要時間が短い
- さまざまな合金や金属と互換性があります
- 特別なトレーニングを受けなくても誰でも操作できます。
デメリット
- 球面セグメントにのみ適用可能
- 高価な機械
- 頻繁に使用するツール
- 大量の材料の堆積 非常に高い熱出力
フライス加工
回転切削工具は、フライス加工でワークピースから静止した材料を除去するために使用されます。さまざまなツールを利用することで、目的を達成することができます。
利点
- 最高の精度
- 合理化された切断手順
- さまざまな素材に使用可能
デメリット
- 大量の余剰材料
- 経験のあるオペレーターが必要
掘削
穴あけは、金属加工において小径の穴を開ける一般的な手順です。複雑な完成品、金属板、ブロックなどはすべてこの方法で加工できます。
利点
- 最高の精度
- 小さな直径の穴を開けるのに最適な選択肢
- あらゆる表面で効果的
デメリット
- 工具の摩耗、発熱が大きく、穴あけ以外の用途がほとんどない
- 用途
- 部品のその後の組み立てのための入口
- ネジ穴
- 見た目が魅力的
研削
研削では、研磨ホイールを使用してワークピースからごくわずかな材料を除去します。主に金属の二次仕上げ工程で使用されます。この工程では、ごくわずかな材料しか除去されません。切断にはより適している可能性があります。
利点
- 良好な表面仕上げもその能力の範囲内です。
- 材料研磨の減少
- ワークピースの正確な測定に最適
デメリット
- 最低限の能力
- 滑らかにする必要があるエッジとサーフェスにのみ作用します。
熱切断
熱切断法では、金属を切断するために正確な場所で材料を溶かします。熱切断手順の精度は高いですが、一方で、ワークピースの材料の強度を損なう可能性のあるホットスポットが生成されます。
熱切断には次のようないくつかの種類があります。
レーザー切断
レーザーを使用して切断するには、高周波光線で材料を溶かします。レーザービームは非常に小さいため、非常に正確な切断が可能で、最も好まれる方法の 1 つとなっています。レーザーで可能な形状は直線切断だけではありません。レーザーカッターを使用して多軸切断を行うことはできません。
利点
- レーザー切断はあらゆる素材に対応します。
- 精巧な精度
- レーザー切断により複雑な形状も切断可能です。
デメリット
- 高熱地帯
- 材料の厚さに関しては、レーザー切断にはかなり制限があります。
- 溶融中の金属の酸化によるゴミの形成
プラズマ切断
プラズマ切断は、イオン化されたプラズマ流を使用して材料を溶かす金属切断方法です。金属が溶けると、高圧の空気流によって排出されます。イオン化されたジェットの非常に狭い幅によって、正確な切断が実現します。この技術は、高い電気伝導性を持つ材料に限定されることに注意してください。したがって、プラズマ切断は、導電性のないすべての金属合金には適合しません。
利点
- プラズマ切断に適した材料にはステンレス鋼が含まれます。
- 消耗品は安価
- 精巧な精度
デメリット
- 熱の影響を受ける地域の発展
- より実質的な材料の場合、より効果的である可能性があります。
- 有害ガスの排出
- アークグレアを発生させる
酸素燃料切断
火炎切断と酸素燃料切断は同義語です。酸素と他のガスの爆発混合物を燃料源として加熱します。材料が高温で溶けることで切断が行われます。
利点
- この切り方は驚くほど持ち運びに便利です。
- 電力は不要です。
- 手続きは簡単で、費用もかかりません。
デメリット
- 精度はもっと向上する可能性があります。
- 危険なガスが空気中に放出されます。
- セキュリティの欠如
- より実質的な材料の場合、より効果的である可能性があります。
放電加工(EDM)
放電加工では、電気アークによって金属が溶解されます。ワークピースは、実際に触れることなく電極の近くに近づきます。ワークピースを変形させることで、新しい電極が作成されます。印加電圧により、2 つの接点間に電流が流れます。これらの放電によって温度が上昇し、材料が溶解します。
利点
- 自然な曲線に沿わないカットを行うスキル
- 精巧な精度
- 困難な物質を扱う
デメリット
- 消費電力が高いです。
- トリミング率が低い
- 導電性物質のみで機能します。
- 熱の影響を受ける地域の発展
電気化学加工
電気化学加工では、電気と化学反応を組み合わせて加工物から材料を除去します。このプロセスは電気メッキの逆で、金属部品を迅速に製造できます。
利点
- 高硬度の金属と効果的に結合します
- ホットスポットの形成を回避します。
- ツールの摩耗は問題ではありません。
- 急加速
デメリット
- 金属を切断するための高価な手順
- 金属錆の可能性
- 導電性材料のみに使用可能
金属仕上げ
金属部品の製造において最も重要な工程の 1 つは表面研磨です。完成した部品はどれも、高品質の金属表面処理によってその美観が向上し、さらに重要なことに、耐久性も向上します。
さまざまな種類の金属仕上げが利用可能です。効率を最大限に高め、無駄を最小限に抑えるには、それぞれの仕上げを徹底的に理解することが不可欠です。
金属仕上げとは何ですか?
金属仕上げには、単純な研磨から金属の分子構造のより複雑な操作まで、幅広い手順が含まれます。「金属仕上げ」という用語は、洗浄や研磨などのさまざまなプロセスによって金属製品の表面を強化することを指します。
金属仕上げの利点と欠点
金属仕上げ技術の利点
上記の仕上げプロセスには多くの利点があります。
耐腐食性、美観の向上、機能性の向上は、それぞれの基本的な利点です。より微妙な点としては、金属コーティングにより、軟鋼などの加工しやすく、安価で、広く入手可能な材料が使用できるようになることがよくあります。さらに、導電性と耐摩耗性が向上する場合もあります。
金属仕上げの欠点
あらゆる製造プロセスに関連するコストは、製造プロセスの計画に費やされる時間と労力、および最終製品の価格上昇です。
塗装や研磨などの仕上げを施すには、加工後に部品を慎重に取り扱わなければなりません。仕上げ工程を完了するには追加の時間と労力が必要となり、リードタイムが長くなります。
代替の仕上げ方法により、最終製品の使用可能範囲が制限される場合があります。たとえば、特殊な高温塗料を使用しない限り、通常の塗料では対応できない温度範囲があります。
結論
板金成形は、物作りの重要な部分です。薄い金属板をさまざまな形に切断して成形します。産業革命によってこの方法が生まれ、現在も改良が続けられています。昔ながらの方法と最新の科学的発見が融合されています。薄い金属板、ストリップ、またはコイルを切断して特定の形状に成形するのが、板金加工のすべてです。板金加工には、引き抜き、切断、曲げの 3 つの主な方法があります。
パンチとダイを使用して板金を切断すると、せん断張力が生じます。一方、曲げは、直線軸の周りに伸ばされた金属を成形する一般的な方法です。引き抜きは、湾曲した凹面の形状を作成するために使用されます。工具用のステンレス鋼、炭素鋼板、アルミニウム、低炭素鋼、低炭素鋼は、板金の製造に使用できる材料の一部です。
板金加工には、さまざまな形状の金属を扱える、廃棄物が少ない、高速、理解しやすいなど、多くの利点があります。また、押し出し、鋳造、成形などの他の方法よりもコストがかからず、さまざまな用途に使用できます。板金部品は強度があり、長持ちするため、少量で製造できるため、迅速な試作に適しています。
しかし、板金加工では、エラー、厚さの制限、製造コストの高さ、複雑な設計の必要性、高価なツールや設備の必要性など、いくつかの問題が発生する可能性があります。また、板金加工は手作業で行う必要があるため、スタンピングなどの他の方法よりも時間がかかります。
金属を切断する方法には、機械切断、フライス加工、穴あけ、研削、熱切断、プラズマ切断、酸素燃料切断、放電加工 (EDM)、電気化学加工などがあります。旋削、フライス加工、穴あけ、研削、回転切断はすべて、鋭利な切削工具を使用して金属から材料を除去する機械的切断の種類です。
機械切削では、さまざまな金属や材料を素早く正確に切断できます。回転切削工具は、フライス加工でワークピースから動かない材料を取り除くために使用されます。この方法は正確で迅速です。ドリル加工は小径の穴を開ける一般的な方法ですが、多くの練習が必要で、工具がすぐに摩耗します。研磨ホイールは、ワークピースからごく少量の材料を取り除くために研削加工で使用されます。
これにより、表面の仕上がりが良好になり、材料の研磨の必要性が減ります。熱切断を使用すると、適切な場所で材料が溶かされます。これにより、非常に正確な結果が得られますが、材料を弱めるホットスポットが残ることもあります。レーザー切断は、高周波光線で材料を溶かします。非常に正確ですが、材料の厚さが制限され、廃棄物が発生する可能性があります。
プラズマ切断はイオン化されたプラズマ流で材料を溶かしますが、電気伝導性に優れた材料にしか使用できません。酸素燃料切断は、酸素と他のガスの強力な混合物を使用します。非常に正確ですが、多くの電力を消費し、切断があまり速くありません。電気化学加工は、電気と化学プロセスを使用してワークピースから材料を除去します。非常に硬く、ホットスポットを生成しない金属に最適です。
金属仕上げは、金属部品の見た目を良くし、長持ちさせるため、金属部品の製造において重要な部分です。単純な研磨から金属の分子構造の複雑な変更まで、多くのステップが含まれます。利点としては、錆びにくさ、見た目の良さ、有用性、低コストなどが挙げられます。しかし、リードタイムが長くなること、処理後の部品の取り扱いに注意を払わなければならないこと、最終製品の有効範囲が制限される可能性があるなど、問題もあります。効率化して無駄を減らすには、それぞれの仕上げについて知っておく必要があります。
ツーリングとCNCの絞り加工能力を最大化する
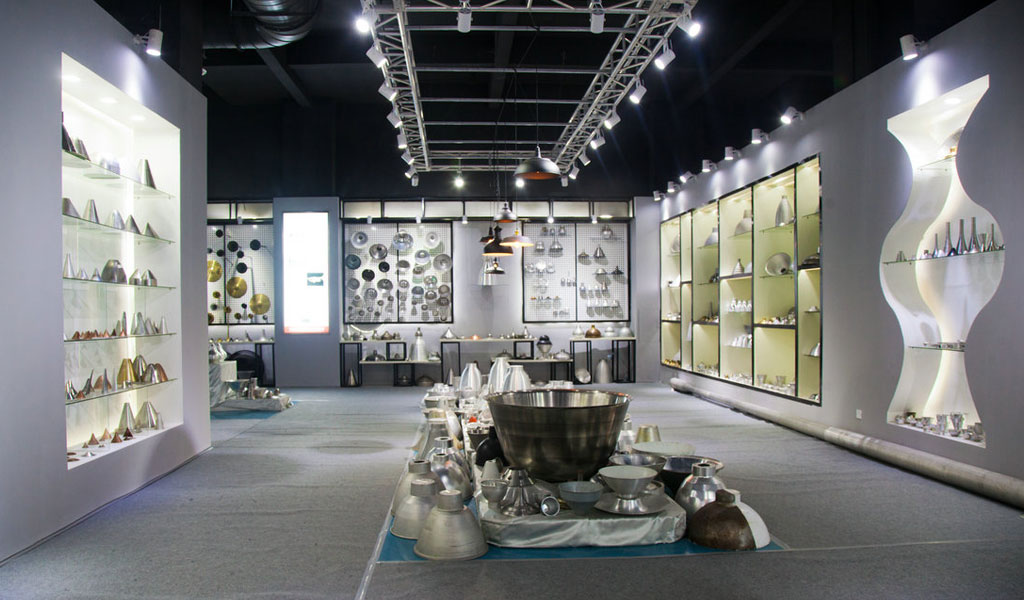
BE-CU 中華のへら 絞り 会社では、過度の摩耗やストレスの兆候を監視しながら、設備を最大限に活用しています。さらに、より新しい最新の設備を検討し、製造能力をサポートまたは向上できる設備に投資しています。当社のチームは機械やツールに細心の注意を払っているため、部品の品質と生産性に悪影響を与えないように定期的にメンテナンスも行っています。
BE-CUの設計とエンジニアリングサポート
BE-CUは、社内の設計およびエンジニアリングチームを活用して、部品生産の初期コンセプトからお客様を支援することができます(提供された設計に対して広範な設計サポートも提供可能です)。私たちのチームは、プロジェクトの開始から終了まで、お客様と定期的かつ透明なコミュニケーションを取りながら、望ましい最終目標に向かって作業を進め、明確な進行方向を提供します。
BE-CUの設計およびエンジニアリングサポートプロセスの一例:
- クライアントがBE-CUチームに部品図面を提供します。
- 当社のエンジニアリングチームが図面をレビューし、ベストプラクティスに基づいて調整を行います。お客様のニーズに応じて、成形または絞り部品を最も効果的に達成する方法を推奨します。
- 図面と設計は必要に応じて改訂され、完璧な形に仕上げられます。財務的な実行可能性も最優先事項として考慮されます。
- 主要な目標は、全ての部品の適合性、形状、機能性を実現することです。
- 研究開発は製造プロセスの重要なステップであり、BE-CUは概念実証や様々な検証要件のためにプロトタイピングサービスを提供しています。研究開発プロセスにおける金属成形については、当社のeBookをご覧ください。
BE-CUが提供する広範な社内サービス
この金属加工プロセスは、軸対称の高性能部品を製造します。スピン成形とも呼ばれ、材料を望ましい形状に切削するのではなく、金属ディスクまたはチューブを円錐形やその他の円形に変形させます。
へら絞りは、手動の手作業によるスピニングプロセスまたは自動CNCスピニングを使用します。BE-CUのへら絞り機能の利点には以下が含まれます:
- コスト削減
- 短いリードタイム
- 最大の設計柔軟性
- シームレスで高品質な構造
対応可能な金属には、ステンレス鋼、炭素鋼、アルミニウム、銅、インコネル、ハステロイ、チタン、ブロンズ、真鍮が含まれます。BE-CUは、センター間60インチから直径100インチまでのカスタム金属絞り部品を製造でき、材料の厚さは0.018インチから2.00インチまで対応可能です。
当社の CNC へら 絞り サービスで迅速なプロトタイプの作成について、今すぐお問い合わせください。こちらでチャットして直接見積もりを取得するか、無料のプロジェクトレビューをリクエストしてください。