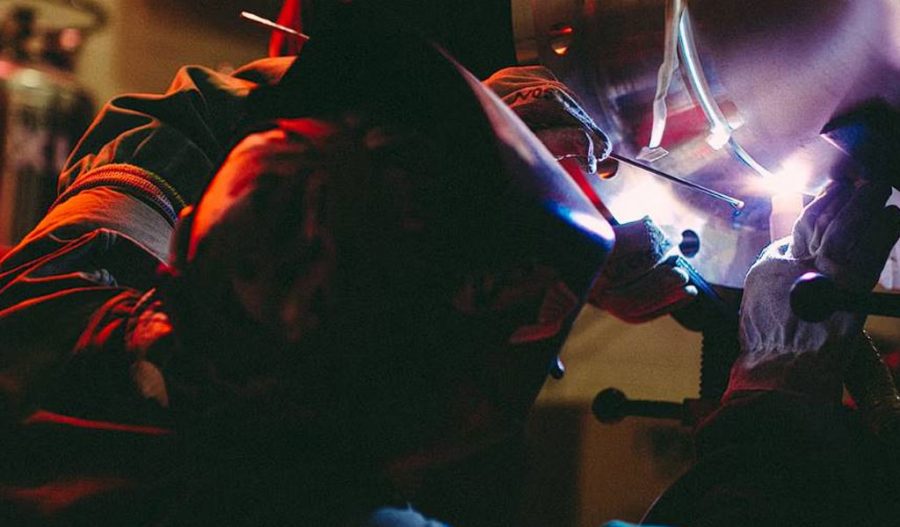
MIG 溶接は、溶接業界やアマチュア溶接工の間で広く使用されています。これは、この溶接技術が効果的で、実装が簡単だからです。不活性ガスを使用することで溶接品質が保証され、2 つの頑丈な材料とソリッド ワイヤの組み合わせにより、非常に頑丈な接合部が実現します。
MIG 溶接とは正確には何でしょうか? MIG 溶接は、母材に固体ワイヤを挿入することで、非常に頑丈な溶接を実現します。不活性ガスは、汚染物質が溶接プロセスに入り込むのを防ぐシールドとして使用されます。金属不活性ガス (略して MIG) は、この手順で使用される金属と不活性ガスを指します。
MIG 溶接は、単純な作業場の雑用から複雑な金属加工まで、さまざまな作業に役立ちます。さまざまな目的で使用すると、メリットとデメリットがあります。MIG 溶接の利点、適切な用途と不適切な用途について説明します。
MIG溶接の目的は何ですか?
MIG 溶接はさまざまなプロジェクトに使用できますが、その強みはより複雑で小規模な作業にあります。溶接に必要な機器が小さく、使用する金属が非常に強いため、品質を維持し、高い出力を達成するのに最適です。MIG 溶接にはさまざまな用途があり、その一部を以下に示します。
さまざまな金属と合金を活用:
MIG 溶接は、事実上あらゆる金属や合金に効果的に使用できます。この手順で使用されるシールド ガスは、すべてのコンポーネントを損傷から保護します。コンポーネントは、どれほど劇的に変化しても、常にきれいで損傷がありません。そのため、この溶接技術は幅広い用途に使用できます。
詳細な作業:
MIG 溶接は小型のハンドガンで行われ、強力な溶接を行うのにそれほど技術は必要ありません。これにより、溶接工は溶接プロセスの細かい点に集中できるようになり、より複雑で洗練された溶接が実現します。MIG 溶接はカスタマイズが豊富なため、趣味で溶接をする人の間で人気があります。
小さな構造物の製造:
MIG 溶接は、小型構造物の製造時に構造の完全性を損なうことなく高品質の溶接を作成するために使用されます。環境に優しい溶接方法であるだけでなく、化学廃棄物の量も削減します。
溶接初心者:
MIG 溶接は特に複雑な手順ではなく、比較的低いレベルの技能でも良好な溶接ができるため、初心者や趣味の溶接者に最適です。特別な教育や訓練を必要とせず、非常に簡単なのが魅力です。溶接の技能が向上しても、より複雑なプロジェクトに MIG 溶接を使い続けることができます。
MIG 溶接で使用される一般的な材料は何ですか?
以下は、MIG 溶接で最も頻繁に使用される材料のリストです。
- アルミニウム
アルミニウムは、柔らかく銀色の外観を持つ非鉄金属です。アルミニウムを溶接する場合は、純粋なアルゴンガスのみを使用する必要があります。アルミニウムを溶接する際には、溶融池が部品を焼き切って反対側に落ちやすいため、問題が発生します。
- 銅
銅は展性と汎用性があるため、配管や電気配線に最適です。銅を溶接する場合、MIG 溶接が最適な方法です。ただし、銅をうまく溶接するために必要な熱は、鋼鉄を溶接する場合の約 2 倍です。
- ニッケル合金
ニッケル合金には通常、クロム、モリブデン、鉄、銅の少なくとも 1 つの元素が含まれます。ニッケル合金は通常、100% アルゴンのガス混合物を使用して溶接されます。ただし、追加の電力が必要な場合は、最大 40% のヘリウム濃度を使用できます。
- スチール
鋼は、鉄と炭素を主成分とし、硫黄やリンなどの他の元素も含む金属合金です。鋼を溶接する際は、シールドとして 75% のアルゴンガスと 25% の二酸化炭素を使用することをお勧めします。純粋なアルゴンガスで溶接すると、接合部の柔軟性が低下するためです。
実際のMIG溶接プロセス
MIG 溶接ではワイヤ電極が使用されるため、このプロセスは一般にワイヤ溶接と呼ばれます。電極として、細いワイヤがリールから溶接機に連続的に供給されます。ソリッド ワイヤとコア ワイヤの両方の供給が可能です。
芯線は、ソリッドワイヤとは対照的に、別の金属または粉末フラックスが充填された金属シースの複合材です。
溶接機のトリガーが押されると、ワイヤ電極の端と接合される金属(加工される金属)の間にアークが発生します。溶接プールを作成するには、ワイヤと加工物の間にアークを発生させ、両方を溶かす必要があります。
MIG 溶接では、ワイヤは 1 つの目的ではなく 2 つの目的で使用されます。ワイヤ溶接という名前は、金属ワイヤが熱源であると同時に接合部のフィラー金属でもあることから付けられました。
電流は、銅製の接触チューブ(接触先端)を通して連続的に供給されることにより、ワイヤに伝導されます。
MIG 溶接では、充填材、ワークピース、および周囲の環境間の反応を防ぐためにシールドガスが使用されます。
ワイヤはシールドガスを導入するノズルに囲まれています。溶接される材料とその用途の両方が、使用するシールドガスを決定する上で重要な役割を果たします。
MIG 溶接は、外部電源がワイヤ送り速度とアーク長を管理し、溶接機が移動速度とワイヤ位置を管理するため、半自動と呼ばれます。
金属転送モード
金属をワイヤ電極から溶接プールへ移送するために、4 つの異なる金属移送モードを利用できます。
スプレーモード
有芯電極またはソリッドワイヤ電極を比較的高いエネルギーレベルで連続的に堆積させることにより、高エネルギー金属転送モードであるスプレーモードが構成されます。
さまざまなサイズと形状の液滴を生成する球状移行法とは対照的に、この方法では均一な形状の溶融金属液滴が安定して流れます。
スプレー モードには、高い堆積速度、溶接スパッタなし、溶接後の簡単なクリーニング、ハード オートメーション、ロボット工学、半オートメーションへの適応性など、多くの利点があります。また、最大 98% の高い電極効率、優れた使いやすさ、優れた溶接ビード外観も備えています。
球状モード
金属は、連続的に供給される金属芯電極またはソリッドワイヤ電極上に、短絡と重力による大きな滴を交互に繰り返すことによって、球状モードで堆積されます。
大きな液滴の形状は均一ではありません。これは、短絡移行段階と球状移行段階の間の切り替えであり、前段階が終了したときに始まります。
この技術では、電極は基板と物理的に接触しません。
極めて高速で溶接を行うこと、シールドガスとして安価な二酸化炭素ガスを使用すること、安価な金属芯電極または固体電極を使用することは、球状モードの金属転送の多くの利点のほんの一部にすぎません。
パルスモード
この技術は、スプレー モードを厳密に制御したバリエーションです。溶接は高電流レベルと低電流レベルの両方で実行されます。
電流が強い場合、金属は一滴の液体として移送されます。MIG 溶接における他の金属移送方法と比較すると、パルス方式には最も多くの利点があります。
スパッタは最小限、抵抗は高い、溶融欠陥は存在せず、溶接ビードは優れた外観で形成され、作業者の魅力は高く、熱による歪みは最小限に抑えられ、ワークピースが不自然な位置にある場合でも溶接が可能で、電極効率は 98% であり、ロボットや自動化アプリケーションに役立ちます。
短絡モード
繰り返しの電気短絡により、短絡モード(ディップ モードとも呼ばれる)で金属芯電極またはソリッド ワイヤ電極から金属が堆積します。この技術は熱量が低いため、金属の転送に最適です。
金属を移送するには、電極が溶融金属のプールまたは基板と直接接触する必要があります。
金属は、上下逆さま、正面向き、平面上、上方など、あらゆる方向で短絡により移動する可能性があります。
低入熱モード、溶接歪みの低減、使いやすさの向上、電極効率 93% 以上などの特長により、パイプ用途に最適です。フィットアップ不良にも比較的容易に対応できます。
MIG 溶接の利点は何ですか?
MIG 溶接には、他の溶接方法と同様に、利点と欠点があります。これらの利点の多くは、何をしているか、そして最終的な目的によって決まります。ただし、状況によっては最適ではない場合もありますが、多くの理由から MIG 溶接は優れた選択肢です。MIG 溶接には、次のような多くの利点があります。
簡単に学べる
初心者の溶接工は、習得するのに大掛かりな訓練や経験を必要としないため、MIG 溶接を使用することが多いです。ローリング マシン、ガス タンク、基本的な手順書があれば、すぐに作業を開始できます。MIG 溶接のコツをつかめば、基本を超えて使い続けることができます。
見栄えの良い溶接
MIG 溶接は、強度が高く、簡単に実行できるだけでなく、見た目も美しいという利点もあります。適切に行えば、溶接はきれいで見た目も美しく仕上がります。
有毒ガスはそれほど多くない
ほとんどの溶接方法では、溶接中および溶接後に大量の有毒ガスが放出されます。金属とガスの組み合わせ、または材料の加熱だけでも有毒ガスが発生する可能性があります。当然のことながら、有毒ガスを吸い込むのはよくありません。シールドガスタンクを使用するため、MIG 溶接ははるかに安全で、有害な副産物は発生しません。
ほとんどの金属の溶接
MIG 溶接は、事実上あらゆる金属や金属合金に使用できます。このため、初心者も熟練したプロも頻繁に使用しています。この溶接の優れた点は、さまざまな金属や鋼にうまく溶接できることです。
MIG 溶接は、事実上あらゆる材料に使用できます。考慮すべき点は、適切なワイヤ サイズを選択することだけです。溶接機と互換性のあるワイヤ サイズの金属のみを溶接できます。金属によっては、特定のサイズが見つからない場合がありますが、これは非常にまれなことですが、実際に起こることです。
強力な溶接
MIG 溶接では、2 つの母材の間にソリッド ワイヤが供給されます。その結果、頑丈で信頼性の高い溶接が実現します。MIG 溶接では、他の溶接プロセスに比べてサポート力と強度が増すため、やや太めのワイヤが使用されます。
溶接の飛散は最小限に抑えられます。
溶接を行うと、溶接材料がかなり飛び散ることを多くの人が認識する必要があります。しかし、MIG 溶接では、ほとんど飛び散りが発生しないため、プロセスが合理化され、クリーンになります。溶接を損傷する可能性のある飛び散りがないため、良好な溶接ができる可能性が高くなります。
クリーン
MIG 溶接は、他の溶接方法に伴う飛散物、煙、その他の厄介な問題が生じないため、大きな混乱は生じません。通常、溶接機の周囲には金属の汚れや燃料の層が付着します。しかし、MIG 溶接ではそのようなことはありません。MIG 溶接はクリーンなプロセスであるため、汚れのない溶接と整頓された作業エリアが得られます。
MIG 溶接の欠点は何ですか?
MIG 溶接には多くの利点があるにもかかわらず、欠点もあります。機械の不便な設計と必要なコンポーネントが問題の一因となっています。したがって、MIG 溶接には多くの明らかな利点があるにもかかわらず、重大な欠点もあります。MIG 溶接には、次のような欠点があります。
汚染物質に対する感受性
MIG 溶接を不活性ガスで行うと、溶接部はよりきれいになり、接合部はより強くなります。ただし、これにより溶接部は溶接中に不純物の影響を非常に受けやすくなります。短時間でも酸素にさらされると、材料や溶接部が劣化する可能性があります。
そのため、溶接には汚れがなく、湿気やガスのない環境が必要です。そうした環境があれば、溶接の見た目も良くなり、成功率も高くなります。汚染物質にさらされると、材料が錆びたり劣化したりする可能性があります。
ワイヤ供給機構
MIG 溶接のワイヤ供給機構は、もっと扱いやすくする必要があります。2 種類の異なる金属が必要になり、その間に 3 本目のソリッド ワイヤを供給する必要があります。溶接の品質は、ワイヤの状態と適切な供給に依存します。その結果、溶接を開始するのが難しくなります。
設備費
MIG 溶接工として始めるには、高額な費用がかかるため、一部の人にとっては手が出ないかもしれません。数百、数千ボルトを簡単に扱える溶接機を購入する必要があります。さらに、ワイヤー、金属、さまざまなクランプ、そしてそれらすべてを動かすための電気も必要です。営利目的で溶接業界に携わっていない場合、これは高額な費用になる可能性があります。
放射線
MIG 溶接を行うと、溶接アークからさまざまな波長の紫外線 (UV)、可視光線、赤外線 (IR) が発生します。少量であれば大した影響はありませんが、慢性的にさらされると問題になります。白内障、目の痛み、光に対する過敏症など、副作用の可能性があります。慢性的にさらされると、皮膚疾患やがんが発生することもあります。
清潔な材料が必要です。
MIG 溶接には、材料の維持管理の基準が厳しく求められるため、プロセスの複雑さと難しさが増します。溶接には、金属が不純物のないきれいな状態である必要があります。そのため、金属を涼しく乾燥した暗い場所に保管する必要があります。不可能ではありませんが、通常の MIG 溶接に余分な作業が追加されます。
ポータビリティ
MIG 溶接に必要な機器はかさばる傾向があります。溶接機器自体、ガス タンク、必要な金属は持ち運びできません。頻繁に移動するよりも、作業場などの固定された場所に設置した方が便利です。
メンテナンス
MIG 溶接のメンテナンスには多くの時間と労力が必要です。可動部品が多く、溶接機、ワイヤー、金属に至るまで、すべてを完璧にメンテナンスする必要があります。投資したすべての機械と備品は、継続的にサービスとメンテナンスを行っていれば役に立ちます。
大型構造物には不向き
MIG 溶接は、頑丈で精密な小規模プロジェクトに最適です。残念ながら、このため、大規模な溶接プロジェクトには適していません。小規模な作業には適していますが、幅広いプロジェクトに取り組む必要があるプロの溶接工には、さらに優れた溶接技術が必要です。そのためには、複数のタイプの溶接に精通している必要があります。
結論
MIG 溶接中に固体ワイヤを母材に注入すると、強力な溶接部ができるので、この溶接法は人気があります。MIG 溶接の不活性ガスのシールド効果により、溶接部から不要な要素が排除されます。MIG 溶接は汎用性が高いため、日常的な金属加工作業からより複雑なプロジェクトまで、あらゆる用途に使用できます。必要な設備が少なく、金属が非常に強いため、より繊細で小規模な作業に最適です。アルミニウム、銅、ニッケル合金、鋼鉄は、MIG 溶接で溶接される最も一般的な材料の一部です。
溶接では、銅のコンタクト チューブにワイヤ電極を通し、シールド ガスを使用してフィラー材料、ワークピース、および環境の反応を防ぐ必要があります。半自動溶接では、ワイヤの送り速度、アーク長、ワイヤの位置を簡単に調整できます。ワイヤ電極から溶融池に金属を移動するために、溶接工は、スプレー、球状、パルス、または短絡の 4 つの金属転送モードのいずれかを使用できます。スプレー モードでは、芯線付きまたはソリッド ワイヤ電極を比較的高いエネルギー レベルで継続的に堆積させることにより、溶融金属から均一な形状の液滴が一定に流れます。球状モードでは、金属芯付きまたはソリッド ワイヤ電極上で短絡と重力による巨大な液滴が交互に発生するため、均一な形状の巨大な液滴が生成されます。パルス モードはスプレー モードの厳密に制御された変形であるため、高電流レベルと低電流レベルでの溶接が可能です。
ワークピースの位置が難しい場合、抵抗が大きい場合、または溶融欠陥がある場合は、短絡モードを使用して作業を完了できます。この技術は、ロボットや自動溶接での使用に適応できます。多用途で多くの用途があるため、MIG 溶接はアマチュアや初心者の溶接工に人気があります。短絡モード (ディップ モードと呼ばれることもあります) MIG 溶接は、金属芯またはソリッド ワイヤ電極から繰り返し電流パルスを介して金属を堆積させるプロセスです。この低発熱により金属の移行に最適で、低入熱モード、溶接歪みの減少、使いやすさの向上、93% 以上の電極効率により、パイプ用途に適しています。
MIG 溶接には、習得の容易さ、溶接品質の清潔さと見た目の美しさ、有害なガスの排出がない、さまざまな金属や合金に適用できるなど、多くの利点があります。汚染、ワイヤ供給機構、高額な設備コスト、放射線、維持管理などは、発生する可能性のある問題のほんの一部にすぎません。
MIG 溶接はよりクリーンで強力な溶接を実現しますが、このプロセスは汚染物質に非常に敏感です。そのため、溶接には完全に乾燥し、ガスや湿気のない空間が必要です。ワイヤ供給システムはそれほど煩雑ではありませんが、3 つの異なる金属と、それらを接続する頑丈なワイヤが必要です。
MIG 溶接工としてスタートするのは、数十万ボルト、ワイヤ、金属、クランプ、電力を扱うために必要な機器のコストが高いため、経済的に困難になる可能性があります。白内障、目の痛み、皮膚の問題は、汚染物質との長期接触によって生じる可能性のある悪影響のほんの一部です。
材料は清潔でなければなりません: MIG 溶接では、涼しく乾燥した暗い環境に保管された清潔な金属が必要です。機器は持ち運び可能である必要がありますが、そうではありません。大きな建物は、時間と労力がかかることから、メンテナンスには適していません。
MIG 溶接には多くの利点がありますが、欠点もあります。あまり野心的な作業には適していますが、さまざまな溶接技術の経験が必要です。ただし、大規模な作業に取り組む必要がある熟練の溶接工は、他の方法を検討する必要があります。
ツーリングとCNCの絞り加工能力を最大化する
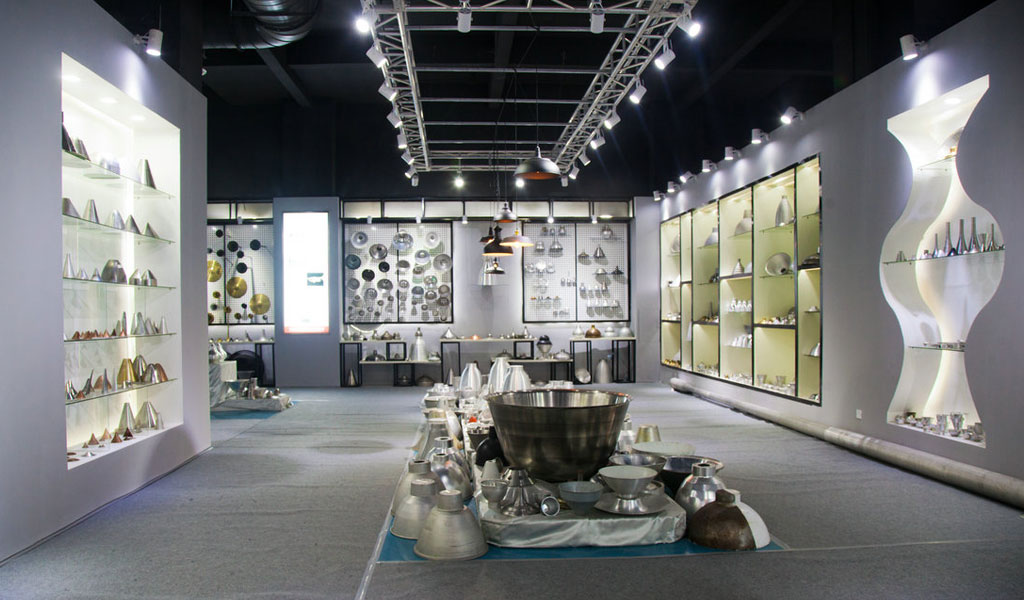
BE-CU 中華のへら 絞り 会社では、過度の摩耗やストレスの兆候を監視しながら、設備を最大限に活用しています。さらに、より新しい最新の設備を検討し、製造能力をサポートまたは向上できる設備に投資しています。当社のチームは機械やツールに細心の注意を払っているため、部品の品質と生産性に悪影響を与えないように定期的にメンテナンスも行っています。
BE-CUの設計とエンジニアリングサポート
BE-CUは、社内の設計およびエンジニアリングチームを活用して、部品生産の初期コンセプトからお客様を支援することができます(提供された設計に対して広範な設計サポートも提供可能です)。私たちのチームは、プロジェクトの開始から終了まで、お客様と定期的かつ透明なコミュニケーションを取りながら、望ましい最終目標に向かって作業を進め、明確な進行方向を提供します。
BE-CUの設計およびエンジニアリングサポートプロセスの一例:
- クライアントがBE-CUチームに部品図面を提供します。
- 当社のエンジニアリングチームが図面をレビューし、ベストプラクティスに基づいて調整を行います。お客様のニーズに応じて、成形または絞り部品を最も効果的に達成する方法を推奨します。
- 図面と設計は必要に応じて改訂され、完璧な形に仕上げられます。財務的な実行可能性も最優先事項として考慮されます。
- 主要な目標は、全ての部品の適合性、形状、機能性を実現することです。
- 研究開発は製造プロセスの重要なステップであり、BE-CUは概念実証や様々な検証要件のためにプロトタイピングサービスを提供しています。研究開発プロセスにおける金属成形については、当社のeBookをご覧ください。
BE-CUが提供する広範な社内サービス
この金属加工プロセスは、軸対称の高性能部品を製造します。スピン成形とも呼ばれ、材料を望ましい形状に切削するのではなく、金属ディスクまたはチューブを円錐形やその他の円形に変形させます。
へら絞りは、手動の手作業によるスピニングプロセスまたは自動CNCスピニングを使用します。BE-CUのへら絞り機能の利点には以下が含まれます:
- コスト削減
- 短いリードタイム
- 最大の設計柔軟性
- シームレスで高品質な構造
対応可能な金属には、ステンレス鋼、炭素鋼、アルミニウム、銅、インコネル、ハステロイ、チタン、ブロンズ、真鍮が含まれます。BE-CUは、センター間60インチから直径100インチまでのカスタム金属絞り部品を製造でき、材料の厚さは0.018インチから2.00インチまで対応可能です。
当社の CNC へら 絞り サービスで迅速なプロトタイプの作成について、今すぐお問い合わせください。こちらでチャットして直接見積もりを取得するか、無料のプロジェクトレビューをリクエストしてください。