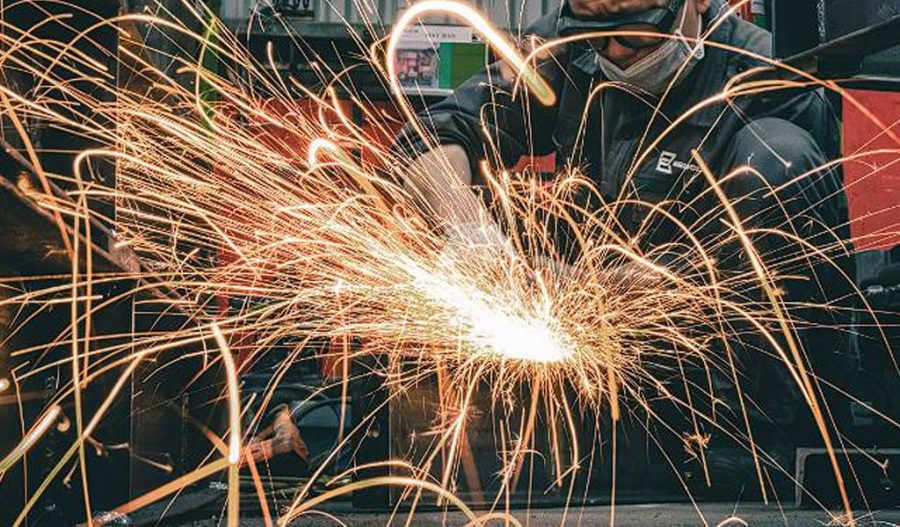
金属から何かを作るには、鋸引き、鋳造、成形などの作業が必要です。最終製品は、製造時に以前に製造された部品から組み立てられるのではなく、原材料または半製品から製造されます。
製造プロセスと技術は多岐にわたり、選択される方法は、製造の初期段階で使用される金属の種類と、希望する最終製品によって異なります。カスタム製品と大量生産品の両方が製造されます。金属は、あらゆる分野、あらゆる家庭のあらゆる機器にとって不可欠です。製造には、未加工の金属を組み立てられた部品に変換する作業が含まれます。手順は多面的で複雑です。
切削工程
さまざまな金属切削プロセスでは、想像以上に幅広い産業機械が使用されています。金属はこれまで以上に多様な形状やサイズに切断できるようになり、その潜在的な用途は大幅に拡大しています。その結果、以前の技術革新よりも滑らかで堅牢な製品が生まれています。これらの切断方法により、金属製品を迅速かつ正確に得ることができます。
共有
この金属加工技術では、2 つの工具を使用して 1 本の長くまっすぐな切断を行います。1 つは金属の上に持ち、もう 1 つは金属を下から押し下げます。上部の刃が固定された下部の刃を押し下げると、金属が破断します。その後、亀裂は内側に広がり、きれいに切断されます。通常、切断された端は見えません。刃はさまざまな角度で取り付けることができるため、短い長さや不規則な形状の材料を切断するために必要な力が大幅に軽減されます。
レーザー切断
多くの企業は、データ品質に関して厳しい基準を設けています。現代的ではないアプローチは数多くありますが、レーザー カッターの精度と正確さに匹敵するものでなければなりません。カッターの強力なレーザー ビームにより、他の手段では実現不可能なさまざまな形状や用途が可能になります。趣味の人は、自宅で快適に使用できる小型レーザー カッターを購入できます。さまざまな企業が、これらの巨大で精密な機械を使用しています。これは、さまざまな製品を迅速かつ効率的に経済的に大量生産できるためです。
レーザー切断は高速かつ正確であるため、広く使用されています。実際、レーザーの用途は多岐にわたります。アルミニウム、軟鋼、ステンレス鋼はすべてレーザー切断に適しています。鮮明で正確な結果を求めているとします。従来の金属切断方法では実現不可能だった複雑な形状も、レーザー カッターを使用すれば作成できます。レーザー切断で使用される集中した光線は、かなりの熱エネルギーを生成できます。
レーザーカッターとコンピュータプログラムを使用すると、非常にきれいにカットされたさまざまなデザインを作成できます。レーザーカットの精度により、職人に人気のツールとなっています。
プラズマ切断
プラズマ切断は、比較的新しい金属切断方法です。この方法では、細い管を流れるガスを電気アークで加熱します。プラズマ切断は、空気、酸素、窒素、アルゴンなど、さまざまなガスで行うことができます。ガスに電流が流れると、プラズマが生成されます。
プラズマ切断トーチは、材料を切断するのに十分な強さのガス流を集中させるために銅製のノズルを使用します。場合によっては、高速酸素と不活性ガスの使用も必要になることがあります。電気と高温のプラズマ流を組み合わせることで、金属を素早く溶かし、すぐに吹き飛ばします。その結果、レーザー切断と同じくらい正確で効率的になります。ただし、結果はレーザー カッターほど正確ではないことに注意してください。精度を求めるなら、レーザー カッターが最適です。
ウォータージェット切断
高熱を利用できるのは一部の金属のみです。温度が高すぎると、形状や材質が破壊される可能性があります。表面が繊細な金属は慎重に扱う必要があります。この目的にはウォータージェット切断が最適です。ウォータージェット技術を使用すると、工業用速度で金属の風化をシミュレートできます。ウォータージェット技術にさらされると金属は侵食されるため、切断が簡単になります。
ウォータージェットでは、柔らかい素材も硬い素材も同じように切断できます。金属は高圧水流で簡単に 2 つに切断できます。ウォータージェット カッターの切断力は、標準的な高圧洗浄機の 30 倍です。厚さ 4 インチまでの複数の素材を同時に切断できます。ウォータージェット切断は、汚れやすいプロセスであるため、汚れを抑えるために水中で行うのが最適です。水中で行うと、汚れや水しぶきが少なくなります。ウォータージェット技術は非常に効果的なので、操作には注意してください。
成形プロセス
金属成形は金属加工の 1 つのステップで、平らな金属板や管をより複雑な形に成形します。これはさまざまな製品にとって重要なプロセスであり、現代の生活は金属成形なしには成り立ちません。今日使用されている金属製品の大部分は、さまざまな金属成形プロセスによって製造されています。巨大な足場から軽量のスチール製ベンチまで、あらゆるものに金属成形が必要です。さらに、今日使用されている金属成形プロセスは複数あり、それぞれが独自の機能を果たし、製造業者に独自の利点をもたらします。
曲げ
板金曲げ加工は、幅広い形状と構造のカスタマイズを可能にする一般的な金属成形プロセスです。この目的には、ブレーキ プレスなどのプレス機がよく使用されます。金属板をダイ ブロックの上に置き、下からパンチング力を板に加えます。金属を曲げる際、この力を使用して板に押し当て、希望する曲げや角度を実現します。これは、板に穴を開ける切断や穴あけとは異なります。
板金曲げは、使用する金型の種類に基づいて、回転曲げ、プレスブレーキ、ロール曲げなどのサブカテゴリに分類できます。各アプローチには独自の利点があり、プロジェクトごとに適切なものが選択されます。金属板の曲げは、建設、自動車、製造部門など、多くの分野で重要なプロセスです。その効果、精度、複雑な形状を作成する能力により、高く評価されています。
ロール成形
ロール成形は、複数のローラー セットを次々に使用する、時間を節約できる金属成形技術です。ロール成形機では、金属ワークピースが一定の圧力と操作を受けながら、複数のローラー セットから供給されます。各ローラー セットは、金属が機械内を移動する際に、金属を目的の断面に成形および曲げます。
この手順を繰り返すことで、金属は理想的な形状とサイズを永久に記録することができます。連続プロファイルと構造部品は長さが長いため、ロール成形に最適です。時間と距離を超えて信頼性と一貫性があるため、大量生産に最適です。
ストレッチ
ストレッチングは、特殊な金型を使用して金属片を曲げたり伸ばしたりする、非常に効率的な金属成形プロセスです。この方法は、曲がった金属部品や複雑な金属部品の製造に適用すると効果を発揮します。
圧力をかけながら金属を伸ばすと、均一で正確な半径の曲げを持つ大型部品を作成できます。この方法は、完璧な仕上げと複雑な形状が不可欠な分野でよく使用されます。変形中に金属の構造的完全性を維持することで、伸ばすことで高品質で見た目に美しい金属部品を生産できます。
接合プロセス
金属加工において、接合とは 2 つ以上の金属片を結合してより強固な全体を形成することを指します。これらの方法により、強くて長持ちする接合部が作られ、より複雑なデザインや材料の使用が可能になります。
溶接
溶接は、熱と圧力を使って金属部品を接合するプロセスです。金属部品の汎用性により、この方法は魅力的です。スティック溶接、アーク溶接、TIG 溶接、MIG 溶接、フラックス入りアーク溶接の 4 つが、一般的な溶接技術です。
電極棒が金属に接触すると、電流が発生し、電気アークが発生します。この技術は、棒溶接またはシールドメタルアーク溶接 (SMAW) として知られています。アークの強力な熱により、金属が溶接されます。
ガス タングステン アーク溶接 (TIG) は、タングステン不活性ガス溶接とも呼ばれ、タングステン電極棒をワークピースに当てて短いアークを発生させ、ワークピースを溶接します。この方法はより複雑で、熟練した溶接工の専門知識が必要ですが、さまざまな金属製品や複雑な建設作業に使用できます。
ガスメタルアーク溶接では、外部から供給されるガスと連続したソリッドワイヤ電極を使用して、金属が周囲と反応するのを防ぎ、より高速で連続的な溶接を可能にします。シールドガスにより、溶接煙が削減されます。
FCAW(フラックス入りアーク溶接)は、MIG 溶接と同様の技術とツール セットを使用します。使用するワイヤ電極にはガスを生成するコアがあるため、追加のガス源は必要ありません。MIG 溶接やスティック溶接よりも持ち運びが簡単ですが、この技術では薄い金属は扱えません。
はんだ付け
はんだ付けとろう付けは、2 つの類似した接続手順ですが、重要な違いが 1 つあります。はんだ付けで使用されるフィラー メタルはベース メタルよりも融点が低く、通常は華氏 840 度未満です。ベース メタルは溶けませんが、フィラー メタルは濡れて結合し、強力な冶金結合を形成します。
この接合手順により、はんだ付け接合部の信頼性と安全性が保証されます。フィラー金属の融点が低いため、はんだ付けは最も熱に弱い部品でも接合できます。金属部品を強度を損なうことなく接合する必要がある場合、はんだ付けは信頼性が高く効率的なオプションです。
ろう付け
ろう付けは、複数の固体金属片を溶かしてその間に充填金属を広げることで結合します。ろう付けを開始する前に、母材の温度を調整する必要があります。次に、接合部を充填金属で充填します。充填金属の融点は華氏 840 度以上ですが、母材よりは低いです。充填金属は流動性と濡れ性が高いため、流れて母材にくっつき、溶けるのを防ぎます。
代わりに、フィラー金属が冶金結合を確立し、強力で長持ちする溶接を実現します。ろう付けプロセスでは、ベース金属が固体状態に保たれることに注意してください。この特性により、ろう付けは、異なる金属で作られた材料など、通常は熱に耐えられない材料を接合するために使用できます。
接着剤による接合
表面接着は、接着接合によって複数の近接した部品を固定する主なメカニズムであり、非常に適応性の高い接合プロセスです。接着接合は、溶接やはんだ付けとは異なり、金属以外の材料を使用します。
ポリマーは優れた接着特性と接着強度を備えているため、このプロセスに最適で、頻繁に使用されます。合わせ面に塗布された接着剤は硬化し、コンポーネント間に強力な接着を形成します。接着剤を使用して 2 つの材料を接着すると、応力がより均等に分散され、振動が軽減され、見た目も美しくなるなど、多くの利点があります。
製品の製造に使用される加工金属
金属製品を製造する際、最終組み立てで使用するために個々の部品を成形することは、多くのステップのうちの 1 つです。その後、家電製品、機械、調理器具、その他の製品は、さまざまな既成部品から組み立てられます。
作業内容に応じて、特定の組み立て部品セットが企業または独立した職人に送られる場合があります。ほとんどのプロジェクトでは、開始するために少なくとも以下のいずれかの資材が必要です。
エキスパンドメタル。
金属は、格子状の金属パネルを必要とする機械や備品に必要な一貫性を持たせるために引き伸ばされます。金属シートを特定のパターンで剪断し、表面に沿ってダイヤモンド形の穴を開けることで、メッシュのような構造が作成されます。各金属シートは、成形される際に最終寸法まで引き伸ばされます。
まさにこの理由から、コンピューターやヒーターの背面パネルには、エキスパンドメタル製の防護壁がよく見られます。エキスパンドメタルパネルは、アパートやゲートコミュニティのフェンスや網戸によく見られます。エキスパンドメタルのシートは格子の大きさがさまざまで、フェンスには大きな穴が一般的に使用され、電子パネルには小さな穴が適しています。エキスパンドメタルの厚さもカスタマイズできます。
溶接ワイヤー。
ワイヤーは金属の撚り線から成り、通常はより太いコードに編まれ、その後スプールに巻かれて溶接に使用されます。名前が示すように、ワイヤーは溶接工程で 2 つの金属片を接合するために使用されます。溶接が進むにつれて、ワイヤーは通常溶接された部品に溶け込みます。さまざまなゲージと金属タイプの溶接ワイヤーが見つかるのが一般的です。
フラットメタル。
平らな金属部品は、さまざまな建設および工業用アセンブリで利用されています。金属シートは、製造プロセス中にさまざまな厚さに切断できます。ピースの厚さは、1 ミリメートル未満から 2 センチメートル以上までさまざまです。平らな金属には、主に 3 つのカテゴリがあります。
- 板金。最も一般的な種類は通常 6 ミリメートルより薄いです。
- 箔金属。最も薄いタイプは箔金属とも呼ばれます。
- 板金。厚さが 0.25 インチを超える最も厚いタイプです。
多くのキッチン家電や家庭用電化製品のサイドパネルは薄い金属板で作られています。
セクショナルメタル。
セクショナル メタルは、建築業界やエンジニアリング業界のさまざまなプロジェクトで頻繁に注文されます。金属部品がプレハブ化され、特定の方法で組み立てられるようになっている場合、それを「セクショナル」と呼びます。
たとえば、建設会社は、業界全体で寸法が標準となっているため、部品メーカーに正確な寸法の構造フレーム パネルを注文する必要がある場合があります。以下は、断面材料の例です。
- 棒。断面が長方形の金属片。
- I ビーム。断面が I 字型の梁。
- 棒。長くて四角い、または円形の断面の金属片。
- Z 字型。アルファベットの最後の文字のような形をした断面ピース。
結論
金属加工には、鋸引き、鋳造、成形などの作業が含まれ、最終製品は原材料または半製品から製造されます。製造プロセスと技術は、使用する金属の種類と希望する最終製品によって大きく異なります。金属はあらゆる分野やあらゆる家庭の電化製品に欠かせないものであり、原材料の金属を組み立てられた部品に変換する作業は多面的で複雑です。
切断プロセスには、金属製品を迅速かつ正確に得ることができる幅広い産業機械が関与しています。切断方法には、せん断、レーザー切断、プラズマ切断、ウォータージェット切断、成形などがあります。レーザー切断は、その精度と正確さから広く使用されていますが、プラズマ切断では、電気アークを使用してガスを加熱し、吹き飛ばします。ウォータージェット切断は、繊細な表面の取り扱いに最適ですが、汚れやすく、高熱が必要になります。
成形プロセスには、平らな金属板や管をより複雑な形状に成形することが含まれます。これは現代の生活に不可欠です。金属板の曲げ加工は、幅広い形状と構造のカスタマイズを可能にする一般的な金属成形プロセスです。ロール成形は、複数のローラー セットを連続して使用する、時間を節約する金属成形技術です。ロール成形は、時間と距離に関係なく信頼性と一貫性があるため、大量生産に最適です。ストレッチングは、特殊な金型を使用して金属片を曲げたり伸ばしたりする、非常に効率的な金属成形プロセスです。
要約すると、金属加工は、せん断、レーザー切断、プラズマ切断、ウォータージェット切断、成形など、さまざまな切断方法を伴う多面的で複雑なプロセスです。各プロセスには独自の利点とメリットがあり、さまざまな製品の製造に不可欠です。圧力をかけながら金属を伸ばすことは、金属加工において重要なプロセスであり、一貫した正確な半径の曲げを備えた大型のピースを作成できます。この方法は、変形中に金属の構造的完全性を維持するため、完璧な仕上げと複雑な形状の分野でよく使用されます。
金属加工における接合プロセスでは、2 つ以上の金属片を接合してより強い全体を形成し、強力で長持ちする接合部を作ります。一般的な溶接技術には、スティック溶接、アーク溶接、TIG 溶接、MIG 溶接、フラックス入りアーク溶接の 4 つがあります。スティック溶接では電流が流れ、電気アークが発生しますが、TIG (タングステン不活性ガス溶接) ではタングステン電極棒を使用して短いアークを生成します。
はんだ付けとろう付けは、2 つの類似した接続手順ですが、使用するフィラー金属が異なります。はんだ付けでは、母材よりも低い融点を使用するため、はんだ付け接合部の信頼性と安全性が確保されます。ろう付けでは、複数の固体金属片を溶融してその間にフィラー金属を広げることで結合し、堅牢で長持ちする溶接を実現します。
接着接合は、金属以外の材料(ポリマーなど)を使用して、複数の近接した部品を固定する、適応性の高い接合プロセスです。このプロセスには、応力のより均一な分散、振動の低減、見た目の美しさの向上などの利点があります。
製品の製造に使用される加工金属には、エキスパンドメタル、溶接ワイヤ、平板金属、断面金属などがあります。エキスパンドメタルは格子状の金属パネルを必要とする機械や器具に使用され、溶接ワイヤは 2 つの金属片を溶接で接合するために使用されます。平板金属部品はさまざまな建設および産業アセンブリで使用され、主にシートメタル、リーフメタル、プレートメタルの 3 つのカテゴリに分類されます。断面金属は、正確な寸法の構造フレームパネルなど、建築およびエンジニアリング業界の特定のプロジェクト用に注文されることがよくあります。
ツーリングとCNCの絞り加工能力を最大化する
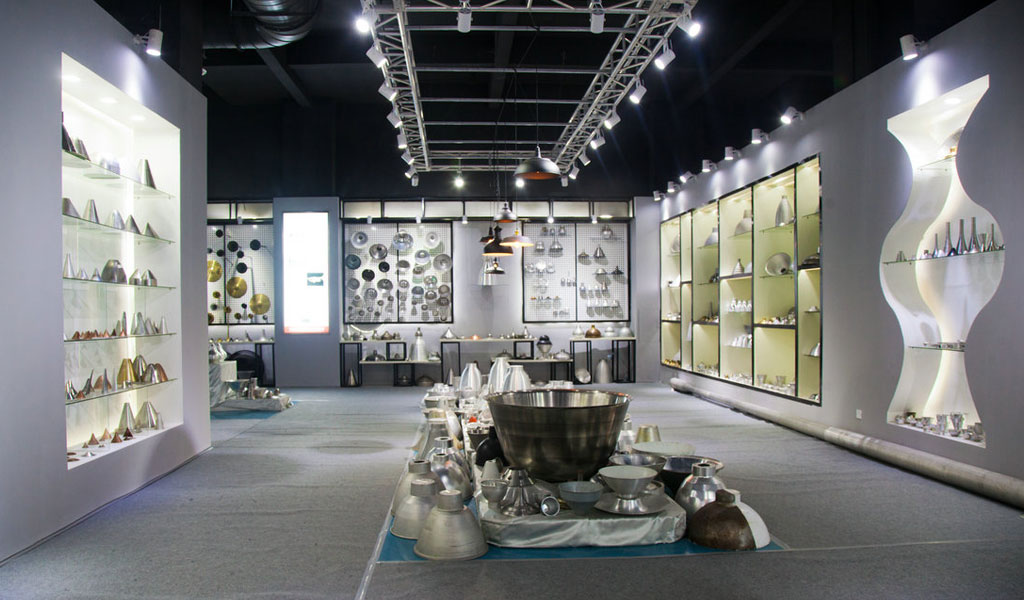
BE-CU 中華のへら 絞り 会社では、過度の摩耗やストレスの兆候を監視しながら、設備を最大限に活用しています。さらに、より新しい最新の設備を検討し、製造能力をサポートまたは向上できる設備に投資しています。当社のチームは機械やツールに細心の注意を払っているため、部品の品質と生産性に悪影響を与えないように定期的にメンテナンスも行っています。
BE-CUの設計とエンジニアリングサポート
BE-CUは、社内の設計およびエンジニアリングチームを活用して、部品生産の初期コンセプトからお客様を支援することができます(提供された設計に対して広範な設計サポートも提供可能です)。私たちのチームは、プロジェクトの開始から終了まで、お客様と定期的かつ透明なコミュニケーションを取りながら、望ましい最終目標に向かって作業を進め、明確な進行方向を提供します。
BE-CUの設計およびエンジニアリングサポートプロセスの一例:
- クライアントがBE-CUチームに部品図面を提供します。
- 当社のエンジニアリングチームが図面をレビューし、ベストプラクティスに基づいて調整を行います。お客様のニーズに応じて、成形または絞り部品を最も効果的に達成する方法を推奨します。
- 図面と設計は必要に応じて改訂され、完璧な形に仕上げられます。財務的な実行可能性も最優先事項として考慮されます。
- 主要な目標は、全ての部品の適合性、形状、機能性を実現することです。
- 研究開発は製造プロセスの重要なステップであり、BE-CUは概念実証や様々な検証要件のためにプロトタイピングサービスを提供しています。研究開発プロセスにおける金属成形については、当社のeBookをご覧ください。
BE-CUが提供する広範な社内サービス
この金属加工プロセスは、軸対称の高性能部品を製造します。スピン成形とも呼ばれ、材料を望ましい形状に切削するのではなく、金属ディスクまたはチューブを円錐形やその他の円形に変形させます。
へら絞りは、手動の手作業によるスピニングプロセスまたは自動CNCスピニングを使用します。BE-CUのへら絞り機能の利点には以下が含まれます:
- コスト削減
- 短いリードタイム
- 最大の設計柔軟性
- シームレスで高品質な構造
対応可能な金属には、ステンレス鋼、炭素鋼、アルミニウム、銅、インコネル、ハステロイ、チタン、ブロンズ、真鍮が含まれます。BE-CUは、センター間60インチから直径100インチまでのカスタム金属絞り部品を製造でき、材料の厚さは0.018インチから2.00インチまで対応可能です。
当社の CNC へら 絞り サービスで迅速なプロトタイプの作成について、今すぐお問い合わせください。こちらでチャットして直接見積もりを取得するか、無料のプロジェクトレビューをリクエストしてください。