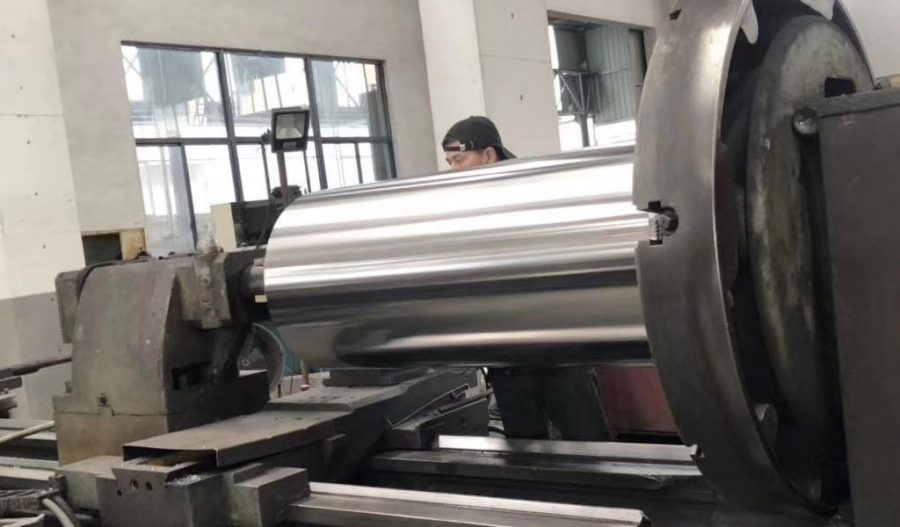
The precision spinning forming process of thin-walled large-size niobium-tungsten alloy nozzles is a critical area of research in the field of advanced materials and manufacturing. This process involves the use of high-precision techniques to shape niobium-tungsten alloys into complex geometries, particularly for applications in aerospace, defense, and high-temperature environments. Niobium-tungsten alloys are prized for their exceptional strength, high melting point, and resistance to corrosion, making them ideal for nozzles that must withstand extreme conditions.
Introduction to Niobium-Tungsten Alloys
Niobium-tungsten alloys are a class of refractory metals known for their superior mechanical properties and high-temperature performance. Niobium (Nb) and tungsten (W) are both transition metals with high melting points, making them suitable for applications requiring resistance to thermal degradation. The combination of these two elements results in an alloy that retains its strength and structural integrity at elevated temperatures, making it a prime candidate for aerospace and defense applications.
Niobium, with a melting point of approximately 2477°C, is known for its excellent corrosion resistance and good weldability. Tungsten, with a melting point of approximately 3422°C, is one of the densest metals and has the highest melting point of all pure metals. When combined, these elements form an alloy that is not only strong and durable but also resistant to oxidation and corrosion.
The Spinning Forming Process
The spinning forming process, also known as spin forming or metal spinning, is a manufacturing technique used to shape metal into axisymmetric parts. This process involves rotating a metal blank at high speeds while applying a localized force to deform the material into the desired shape. The spinning forming process is particularly advantageous for producing thin-walled, large-size components, such as nozzles, due to its ability to achieve high precision and uniform wall thickness.
The spinning forming process for niobium-tungsten alloy nozzles typically involves the following steps:
- Preparation of the Metal Blank: The niobium-tungsten alloy is first prepared in the form of a metal blank. This blank is usually a flat disc or a pre-formed shape that will be spun into the final nozzle shape.
- Mounting and Rotation: The metal blank is mounted onto a spinning mandrel, which is then rotated at high speeds. The rotation speed is carefully controlled to ensure uniform deformation and to prevent material failure.
- Application of Force: A spinning tool, typically a roller or a mandrel, is applied to the rotating blank. The tool exerts a localized force, gradually deforming the metal into the desired shape. The force applied by the tool is precisely controlled to achieve the required wall thickness and dimensional accuracy.
- Annealing and Heat Treatment: After the spinning process, the formed nozzle may undergo annealing and heat treatment to relieve internal stresses and enhance the mechanical properties of the alloy. This step is crucial for ensuring the long-term performance and durability of the nozzle.
- Finishing Operations: The final step involves finishing operations such as machining, polishing, and inspection to ensure the nozzle meets the required specifications and quality standards.
Advantages of the Spinning Forming Process
The spinning forming process offers several advantages for the manufacture of thin-walled large-size niobium-tungsten alloy nozzles:
- High Precision: The spinning process allows for precise control over the wall thickness and dimensional accuracy of the nozzle. This is particularly important for applications requiring tight tolerances and uniform material properties.
- Cost-Effective: Compared to other manufacturing methods, such as casting or forging, the spinning forming process is more cost-effective. It requires less material and fewer processing steps, reducing both material and labor costs.
- Improved Material Properties: The spinning process can enhance the mechanical properties of the niobium-tungsten alloy by inducing work hardening and grain refinement. This results in a stronger and more durable final product.
- Versatility: The spinning forming process is highly versatile and can be used to produce a wide range of axisymmetric components, including nozzles, cones, and cylinders. This makes it a valuable technique for various industrial applications.
Challenges and Considerations
Despite its advantages, the spinning forming process of niobium-tungsten alloy nozzles presents several challenges and considerations:
- Material Behavior: Niobium-tungsten alloys are known for their high strength and resistance to deformation. This can make the spinning process more challenging, as higher forces and temperatures may be required to achieve the desired deformation.
- Tool Wear: The high strength and hardness of niobium-tungsten alloys can lead to increased tool wear during the spinning process. This requires the use of specialized tools and frequent tool maintenance to ensure consistent performance.
- Thermal Management: The spinning process generates significant heat due to the high rotation speeds and localized deformation. Effective thermal management is essential to prevent overheating and material failure.
- Quality Control: Ensuring the quality and consistency of the spun nozzles requires rigorous inspection and testing. This includes dimensional inspection, material testing, and non-destructive evaluation to detect any defects or inconsistencies.
Research and Development
Extensive research and development have been conducted to optimize the spinning forming process for niobium-tungsten alloy nozzles. Key areas of focus include:
- Process Parameters: Researchers have investigated the effects of various process parameters, such as rotation speed, tool force, and temperature, on the spinning process. Optimizing these parameters is crucial for achieving the desired nozzle shape and material properties.
- Material Characterization: Detailed material characterization studies have been conducted to understand the behavior of niobium-tungsten alloys during the spinning process. This includes studying the microstructure, mechanical properties, and deformation mechanisms of the alloy.
- Tool Design: Innovations in tool design have been developed to improve the efficiency and precision of the spinning process. This includes the use of advanced tool materials, such as ceramics and high-speed steels, to reduce tool wear and enhance performance.
- Simulation and Modeling: Computational simulations and finite element modeling have been employed to predict and optimize the spinning process. These tools allow researchers to simulate the deformation behavior of the alloy and identify potential issues before actual manufacturing.
Comparative Analysis
To provide a comprehensive understanding of the spinning forming process for niobium-tungsten alloy nozzles, a comparative analysis with other manufacturing methods is presented below.
Manufacturing Method | Precision | Cost | Material Waste | Mechanical Properties | Versatility |
---|---|---|---|---|---|
Spinning Forming | High | Low | Low | Enhanced | High |
Casting | Moderate | Moderate | High | Good | Moderate |
Forging | Moderate | High | Moderate | Excellent | Low |
Machining | High | High | High | Good | High |
Additive Manufacturing | High | High | Low | Variable | High |
Case Studies
Several case studies have been conducted to demonstrate the effectiveness of the spinning forming process for niobium-tungsten alloy nozzles. These case studies highlight the practical applications and benefits of the process in real-world scenarios.
- Aerospace Nozzles: In the aerospace industry, niobium-tungsten alloy nozzles are used in rocket engines and thrust chambers. The spinning forming process has been successfully employed to produce high-precision nozzles with uniform wall thickness and excellent mechanical properties. These nozzles have demonstrated superior performance in high-temperature and high-pressure environments, making them ideal for space exploration missions.
- Defense Applications: Niobium-tungsten alloy nozzles are also used in defense applications, such as in the manufacture of missile components. The spinning forming process has been utilized to produce thin-walled, large-size nozzles with tight tolerances and high strength. These nozzles have been tested under extreme conditions and have shown exceptional durability and reliability.
- Industrial Applications: In industrial applications, niobium-tungsten alloy nozzles are used in high-temperature processing equipment, such as furnaces and reactors. The spinning forming process has been employed to produce nozzles with precise dimensions and enhanced material properties. These nozzles have been successfully integrated into various industrial processes, improving efficiency and performance.
Future Directions
The future of the spinning forming process for niobium-tungsten alloy nozzles holds great promise. Advances in materials science, manufacturing technology, and computational modeling are expected to further enhance the precision and efficiency of the process. Key areas of future research include:
- Advanced Materials: The development of new niobium-tungsten alloys with improved mechanical properties and deformation behavior will enable the production of even more advanced nozzles. Research into nanocomposites and functionally graded materials is expected to yield significant benefits.
- Automation and Robotics: The integration of automation and robotics into the spinning forming process will improve consistency and reduce human error. Automated spinning machines and robotic tooling systems are being developed to enhance the precision and efficiency of the process.
- In-Situ Monitoring: The development of in-situ monitoring techniques will allow for real-time control and adjustment of the spinning process. Sensors and data analytics tools will be employed to monitor material deformation, temperature, and tool wear, ensuring optimal process conditions.
- Sustainability: Research into sustainable manufacturing practices will focus on reducing material waste, energy consumption, and environmental impact. The development of recycling and reuse strategies for niobium-tungsten alloys will contribute to a more sustainable manufacturing process.
Conclusion
The precision spinning forming process of thin-walled large-size niobium-tungsten alloy nozzles is a critical area of research with significant implications for aerospace, defense, and industrial applications. This process offers numerous advantages, including high precision, cost-effectiveness, improved material properties, and versatility. However, it also presents challenges related to material behavior, tool wear, thermal management, and quality control.
Extensive research and development have been conducted to optimize the spinning forming process, focusing on process parameters, material characterization, tool design, and simulation modeling. Comparative analysis with other manufacturing methods highlights the unique benefits of the spinning forming process. Case studies demonstrate its practical applications and benefits in real-world scenarios.
The future of the spinning forming process for niobium-tungsten alloy nozzles is promising, with advances in advanced materials, automation, in-situ monitoring, and sustainability expected to further enhance the precision and efficiency of the process. As research continues, the spinning forming process will play an increasingly important role in the manufacture of high-performance nozzles for various applications.
Maximize Tooling and CNC Metal Spinning Capabilities.
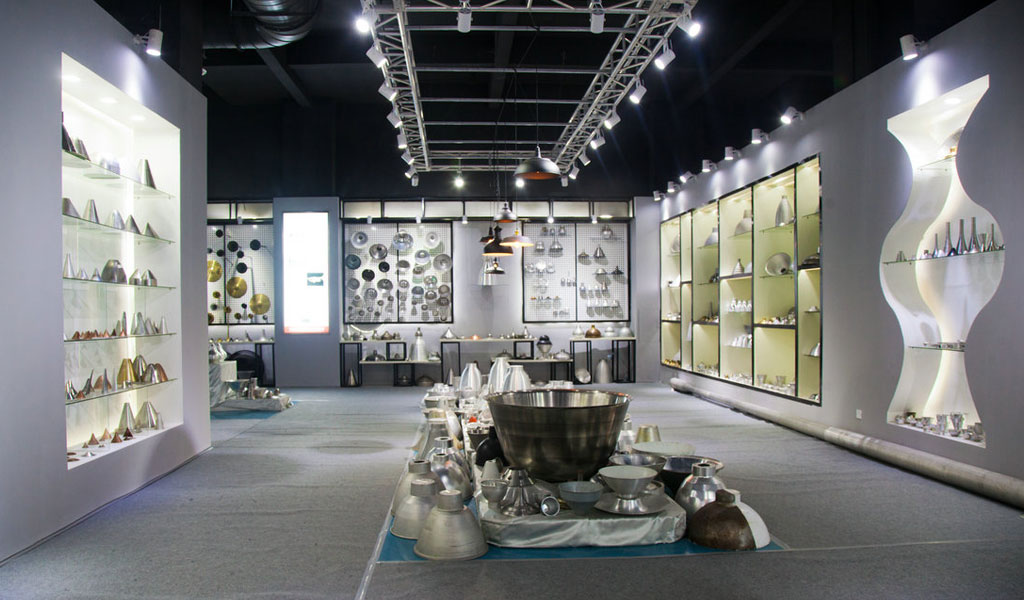
At BE-CU China Metal Spinning company, we make the most of our equipment while monitoring signs of excess wear and stress. In addition, we look into newer, modern equipment and invest in those that can support or increase our manufacturing capabilities. Our team is very mindful of our machines and tools, so we also routinely maintain them to ensure they don’t negatively impact your part’s quality and productivity.
Talk to us today about making a rapid prototype with our CNC metal spinning service. Get a direct quote by chatting with us here or request a free project review.
BE-CU China CNC Metal Spinning service include : CNC Metal Spinning,Metal Spinning Die,Laser Cutting, Tank Heads Spinning,Metal Hemispheres Spinning,Metal Cones Spinning,Metal Dish-Shaped Spinning,Metal Trumpet Spinning,Metal Venturi Spinning,Aluminum Spinning Products,Stainless Steel Spinning Products,Copper Spinning Products,Brass Spinning Products,Steel Spinning Product,Metal Spinnin LED Reflector,Metal Spinning Pressure Vessel,