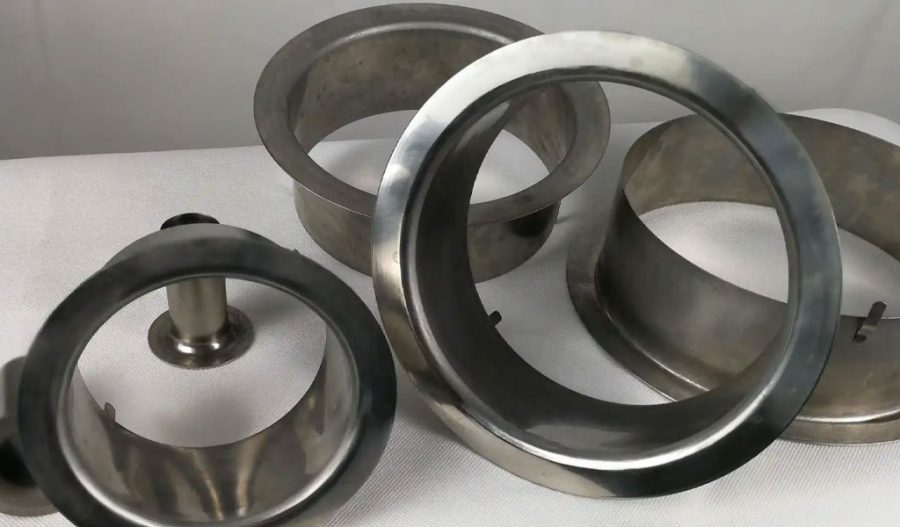
Flexible annular metal bellows are critical components in various industrial applications, including aerospace, automotive, and chemical engineering, due to their ability to withstand high pressures, temperatures, and corrosive environments. The manufacturing of these bellows involves complex processes that require high precision and reliability. One of the advanced technologies in this domain is spinning-rolling combined precision forming. This article delves into the research, development, and applications of this technology, providing a comprehensive overview of its principles, advantages, and challenges.
Historical Background and Evolution
The concept of metal bellows dates back to the early 20th century, with initial applications in industrial piping and pressure vessels. The traditional manufacturing methods included deep drawing, hydroforming, and welding. However, these methods often resulted in inconsistent wall thickness, poor surface finish, and limited flexibility. The advent of spinning-rolling combined precision forming in the late 20th century revolutionized the manufacturing process, offering superior precision and flexibility.
Principles of Spinning-Rolling Combined Precision Forming
Spinning-rolling combined precision forming integrates the principles of spinning and rolling to achieve high-precision forming of metal bellows. The process involves the following key steps:
- Material Preparation: The raw material, typically a thin metal sheet, is cut to the required dimensions and pre-treated to enhance its formability.
- Spinning: The metal sheet is spun at high speeds while a forming tool applies pressure, gradually shaping the material into a cylindrical form.
- Rolling: The spun cylinder is then subjected to rolling, where a set of rollers applies controlled pressure to form the annular corrugations.
- Annealing: The formed bellows undergo annealing to relieve internal stresses and improve material properties.
- Finishing: The final step involves trimming, polishing, and quality inspection to ensure the bellows meet the required specifications.
Advantages of Spinning-Rolling Combined Precision Forming
The spinning-rolling combined precision forming technology offers several advantages over traditional methods:
- High Precision: The combination of spinning and rolling ensures uniform wall thickness and precise dimensional control.
- Improved Surface Finish: The process results in a smooth and consistent surface finish, reducing the need for post-processing.
- Enhanced Flexibility: The technology allows for the production of bellows with complex geometries and varying wall thicknesses.
- Cost-Effective: The automated nature of the process reduces labor costs and increases production efficiency.
- Material Versatility: The technology can be applied to a wide range of materials, including stainless steel, titanium, and high-strength alloys.
Research and Development
Extensive research has been conducted to optimize the spinning-rolling combined precision forming process. Key areas of research include:
- Material Science: Studies have focused on the behavior of different materials under spinning and rolling conditions, aiming to identify the optimal material properties for bellows manufacturing.
- Process Parameters: Researchers have investigated the effects of spinning speed, rolling pressure, and annealing temperature on the final product quality.
- Tool Design: Innovations in tool design have led to the development of advanced forming tools that enhance precision and reduce defects.
- Simulation and Modeling: Finite element analysis (FEA) and other simulation techniques have been employed to predict and optimize the forming process.
Comparative Analysis
To illustrate the advantages of spinning-rolling combined precision forming, a comparative analysis with traditional methods is presented in the table below:
Parameter | Spinning-Rolling Combined Precision Forming | Deep Drawing | Hydroforming | Welding |
---|---|---|---|---|
Wall Thickness Uniformity | High | Moderate | Moderate | Low |
Surface Finish | Excellent | Good | Good | Poor |
Flexibility | High | Moderate | Moderate | Low |
Production Cost | Low | Moderate | High | High |
Material Versatility | High | Moderate | Moderate | Low |
Defect Rate | Low | Moderate | Moderate | High |
Applications
The spinning-rolling combined precision forming technology finds applications in various industries:
- Aerospace: Bellows are used in fuel systems, hydraulic systems, and environmental control systems due to their ability to withstand extreme conditions.
- Automotive: In automotive applications, bellows are employed in exhaust systems, fuel lines, and cooling systems.
- Chemical Engineering: The chemical industry utilizes bellows in piping systems, pressure vessels, and heat exchangers.
- Medical Devices: Bellows are used in medical devices such as implantable pumps and drug delivery systems.
- Industrial Machinery: In industrial machinery, bellows are used in pneumatic and hydraulic systems, as well as in sealing applications.
Challenges and Future Directions
Despite its advantages, the spinning-rolling combined precision forming technology faces several challenges:
- Material Limitations: Certain high-strength materials may not be suitable for this process due to their limited formability.
- Tool Wear: The high pressures and speeds involved in the process can lead to rapid tool wear, increasing maintenance costs.
- Process Complexity: The technology requires precise control of multiple parameters, making it complex and demanding.
Future research is likely to focus on addressing these challenges through advancements in material science, tool design, and process automation. Additionally, the integration of artificial intelligence and machine learning can enhance the precision and efficiency of the forming process.
Conclusion
Spinning-rolling combined precision forming represents a significant advancement in the manufacturing of flexible annular metal bellows. Its ability to achieve high precision, improved surface finish, and enhanced flexibility makes it a preferred choice for various industrial applications. Continued research and development are essential to overcome the existing challenges and further enhance the capabilities of this technology. As the demand for high-performance bellows continues to grow, the spinning-rolling combined precision forming technology is poised to play a crucial role in meeting the needs of modern industries.
Maximize Tooling and CNC Metal Spinning Capabilities.
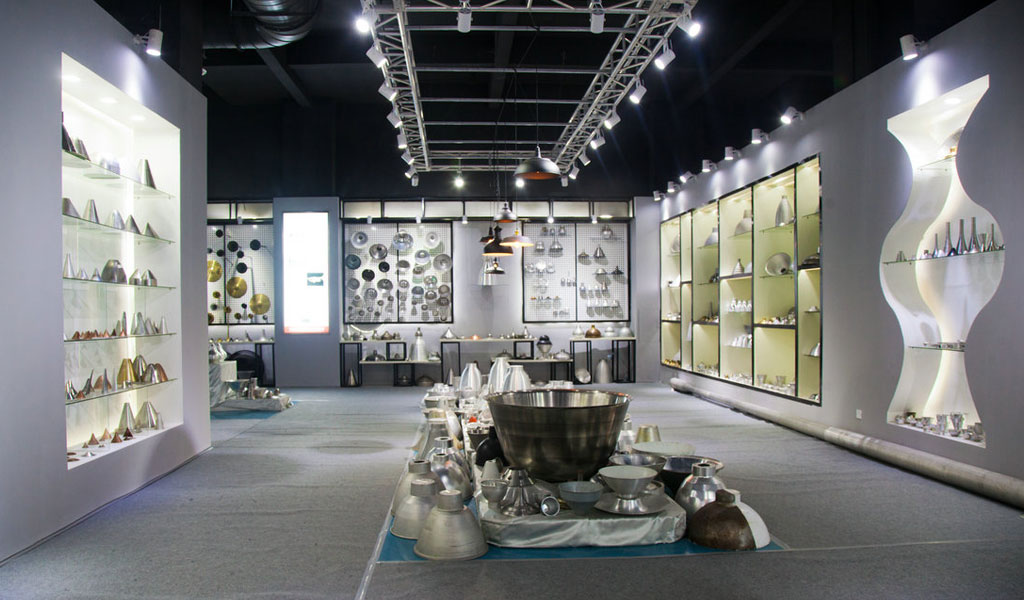
At BE-CU China Metal Spinning company, we make the most of our equipment while monitoring signs of excess wear and stress. In addition, we look into newer, modern equipment and invest in those that can support or increase our manufacturing capabilities. Our team is very mindful of our machines and tools, so we also routinely maintain them to ensure they don’t negatively impact your part’s quality and productivity.
Talk to us today about making a rapid prototype with our CNC metal spinning service. Get a direct quote by chatting with us here or request a free project review.
BE-CU China CNC Metal Spinning service include : CNC Metal Spinning,Metal Spinning Die,Laser Cutting, Tank Heads Spinning,Metal Hemispheres Spinning,Metal Cones Spinning,Metal Dish-Shaped Spinning,Metal Trumpet Spinning,Metal Venturi Spinning,Aluminum Spinning Products,Stainless Steel Spinning Products,Copper Spinning Products,Brass Spinning Products,Steel Spinning Product,Metal Spinnin LED Reflector,Metal Spinning Pressure Vessel,