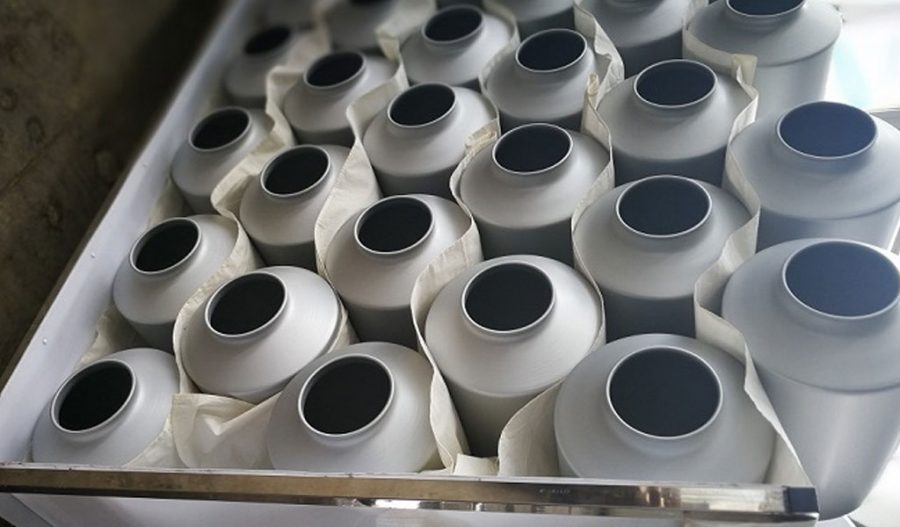
The manufacturing of thin-walled cylindrical parts with large aspect ratios and concave bottoms presents significant challenges due to their complex geometries and stringent dimensional requirements. These parts are commonly used in various industries, including aerospace, automotive, and medical devices, where precision and reliability are paramount. This article delves into the precision forming methods employed to manufacture such parts, focusing on the technological advancements, material considerations, and process parameters that ensure high-quality outcomes.
Introduction
Thin-walled cylindrical parts with large aspect ratios and concave bottoms are characterized by their high length-to-diameter ratios and intricate bottom shapes. These parts are often subjected to high stresses and must maintain dimensional stability under various operational conditions. Traditional manufacturing methods, such as machining and casting, often fall short in meeting the precision and efficiency requirements for these parts. As a result, precision forming methods have emerged as viable alternatives, offering enhanced accuracy, reduced material waste, and improved production rates.
Material Considerations
The selection of appropriate materials is crucial for the successful precision forming of thin-walled cylindrical parts. Common materials used in these applications include:
- Aluminum Alloys: Known for their lightweight and high strength-to-weight ratio, aluminum alloys are widely used in aerospace and automotive industries.
- Stainless Steel: Offers excellent corrosion resistance and strength, making it suitable for medical and food processing applications.
- Titanium Alloys: Provide high strength, low density, and excellent biocompatibility, making them ideal for medical implants and aerospace components.
- Copper Alloys: Known for their high thermal and electrical conductivity, copper alloys are used in electrical and heat exchange applications.
Precision Forming Techniques
Several precision forming techniques have been developed to address the unique challenges posed by thin-walled cylindrical parts with large aspect ratios and concave bottoms. These techniques include:
- Hydroforming: Hydroforming involves the use of high-pressure fluid to shape a metal blank into the desired form. The process begins with the placement of a metal blank into a die cavity. High-pressure fluid is then introduced, forcing the blank to conform to the die’s shape. Hydroforming is particularly effective for creating complex shapes with uniform wall thicknesses.Advantages:
- Uniform wall thickness
- High dimensional accuracy
- Suitable for complex geometries
- High initial tooling costs
- Limited to certain material types
- Spin Forming: Spin forming is a metalworking process where a metal blank is rotated at high speeds while a forming tool shapes it into the desired profile. This method is particularly effective for creating axisymmetric parts with large aspect ratios.Advantages:
- High production rates
- Suitable for large aspect ratios
- Minimal material waste
- Limited to axisymmetric parts
- Requires specialized equipment
- Deep Drawing: Deep drawing involves the use of a punch to force a metal blank through a die, gradually forming it into the desired shape. This method is commonly used for creating cylindrical parts with large aspect ratios.Advantages:
- High production rates
- Suitable for large aspect ratios
- Minimal material waste
- Limited to certain material types
- Requires careful control of process parameters
- Incremental Forming: Incremental forming is a flexible manufacturing process where a forming tool incrementally deforms a metal blank into the desired shape. This method is particularly effective for creating complex geometries with high dimensional accuracy.Advantages:
- High dimensional accuracy
- Suitable for complex geometries
- Flexible and adaptable
- Lower production rates
- Requires specialized equipment
Process Parameters
The success of precision forming methods depends on the careful control of various process parameters. Key parameters include:
- Forming Pressure: The pressure applied during the forming process significantly influences the final part dimensions and surface quality. Optimal forming pressure ensures uniform deformation and minimizes defects such as wrinkling and tearing.
- Forming Temperature: The temperature at which the forming process is conducted affects the material’s ductility and formability. Elevated temperatures can enhance formability but may also introduce thermal stresses and distortions.
- Tool Geometry: The design and geometry of the forming tools play a critical role in achieving the desired part dimensions and surface finish. Precise tooling ensures consistent and accurate forming.
- Lubrication: Proper lubrication reduces friction between the metal blank and the forming tools, facilitating smooth deformation and minimizing tool wear.
Comparative Analysis
The following table provides a comparative analysis of the precision forming methods discussed:
Forming Method | Material Suitability | Production Rate | Dimensional Accuracy | Tooling Costs | Complexity Handling |
---|---|---|---|---|---|
Hydroforming | Aluminum, Stainless Steel, Titanium | Moderate | High | High | High |
Spin Forming | Aluminum, Copper | High | Moderate | Moderate | Moderate |
Deep Drawing | Aluminum, Stainless Steel | High | Moderate | Moderate | Moderate |
Incremental Forming | Aluminum, Titanium | Low | High | High | High |
Case Studies
- Aerospace Industry: In the aerospace industry, thin-walled cylindrical parts with large aspect ratios are commonly used in structural components and fuel tanks. Hydroforming has been successfully employed to manufacture these parts, ensuring high dimensional accuracy and uniform wall thicknesses. The use of hydroforming has resulted in significant weight savings and improved structural integrity.
- Automotive Industry: The automotive industry utilizes thin-walled cylindrical parts in various applications, including exhaust systems and fuel lines. Spin forming has proven effective in producing these parts, offering high production rates and minimal material waste. The precision and consistency achieved through spin forming have contributed to enhanced vehicle performance and reliability.
- Medical Devices: In the medical device industry, thin-walled cylindrical parts are used in implants and surgical instruments. Incremental forming has been employed to manufacture these parts, ensuring high dimensional accuracy and complex geometry handling. The flexibility and precision of incremental forming have enabled the production of customized medical devices tailored to individual patient needs.
Future Trends
The field of precision forming is continually evolving, driven by advancements in material science, process technology, and automation. Future trends in precision forming methods for thin-walled cylindrical parts include:
- Advanced Materials: The development of new materials, such as high-strength composites and advanced alloys, will expand the range of applications for precision forming methods. These materials offer enhanced mechanical properties and formability, enabling the production of more complex and durable parts.
- Hybrid Forming Techniques: The integration of multiple forming techniques, such as combining hydroforming with incremental forming, will enable the production of parts with even more intricate geometries and higher dimensional accuracy. Hybrid forming techniques will leverage the strengths of individual methods to overcome their limitations.
- Automation and Digitalization: The adoption of automation and digital technologies, such as robotics and machine learning, will enhance the efficiency and precision of forming processes. Automated systems will enable real-time monitoring and control of process parameters, ensuring consistent and high-quality outcomes.
- Sustainable Manufacturing: The focus on sustainable manufacturing practices will drive the development of eco-friendly forming methods. These methods will aim to minimize material waste, reduce energy consumption, and lower environmental impact, contributing to a more sustainable future.
Conclusion
The precision forming of thin-walled cylindrical parts with large aspect ratios and concave bottoms is a complex and challenging process. The selection of appropriate materials, the use of advanced forming techniques, and the careful control of process parameters are essential for achieving high-quality outcomes. As the field continues to evolve, the integration of advanced materials, hybrid forming techniques, automation, and sustainable practices will further enhance the capabilities and efficiency of precision forming methods. These advancements will enable the production of more complex and durable parts, meeting the demanding requirements of various industries and contributing to technological progress.
Maximize Tooling and CNC Metal Spinning Capabilities.
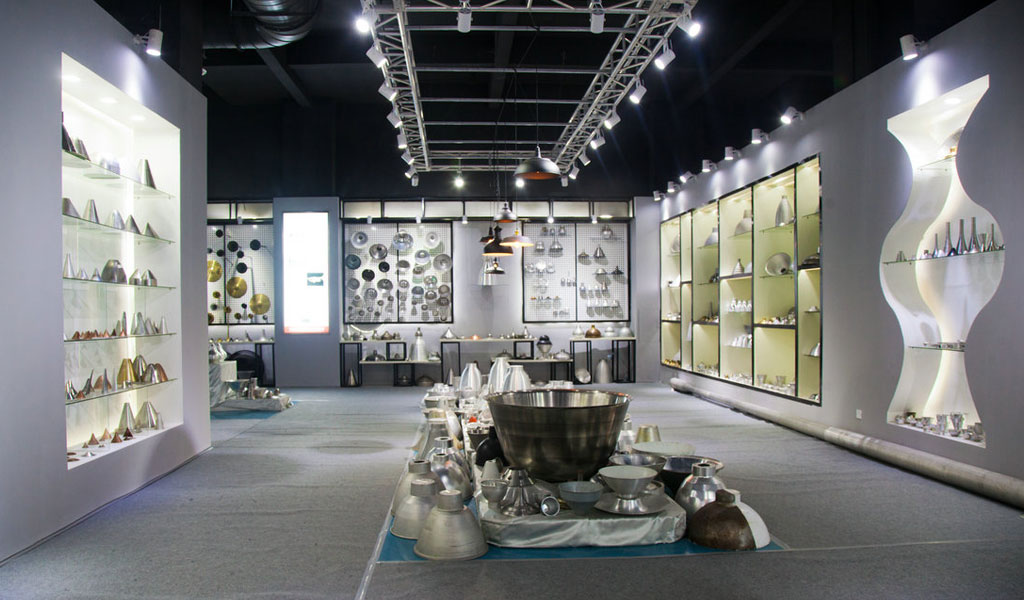
At BE-CU China Metal Spinning company, we make the most of our equipment while monitoring signs of excess wear and stress. In addition, we look into newer, modern equipment and invest in those that can support or increase our manufacturing capabilities. Our team is very mindful of our machines and tools, so we also routinely maintain them to ensure they don’t negatively impact your part’s quality and productivity.
Talk to us today about making a rapid prototype with our CNC metal spinning service. Get a direct quote by chatting with us here or request a free project review.
BE-CU China CNC Metal Spinning service include : CNC Metal Spinning,Metal Spinning Die,Laser Cutting, Tank Heads Spinning,Metal Hemispheres Spinning,Metal Cones Spinning,Metal Dish-Shaped Spinning,Metal Trumpet Spinning,Metal Venturi Spinning,Aluminum Spinning Products,Stainless Steel Spinning Products,Copper Spinning Products,Brass Spinning Products,Steel Spinning Product,Metal Spinnin LED Reflector,Metal Spinning Pressure Vessel,