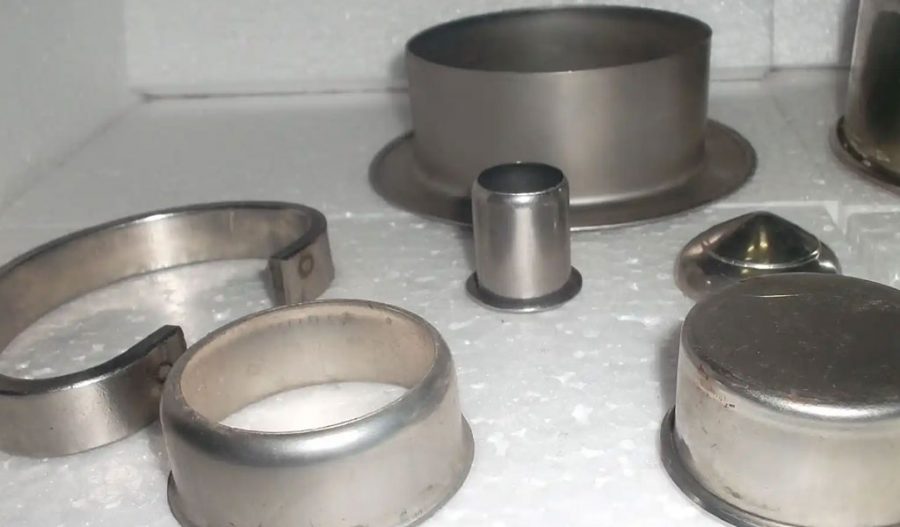
Precision spinning forming technology is a advanced manufacturing process used to produce high-quality, complex-shaped parts from various materials, including aluminum alloys. This technology is particularly effective for creating curved busbar type rotating body parts, which are essential components in electrical and mechanical systems. The precision spinning process involves the controlled deformation of a rotating workpiece using a spinning tool, resulting in parts with exceptional dimensional accuracy and surface finish.
Aluminum alloys are widely used in precision spinning due to their excellent formability, lightweight properties, and high strength-to-weight ratio. These alloys are particularly suitable for applications requiring high electrical conductivity, such as busbars in electrical systems. The curved busbar type rotating body parts produced through precision spinning are characterized by their intricate shapes and high precision, making them ideal for use in advanced engineering applications.
Historical Background
The origins of spinning technology can be traced back to ancient times, where it was used for shaping metal into various forms. However, the modern precision spinning process emerged in the early 20th century with the advent of industrial machinery. The development of computer numerical control (CNC) technology in the latter half of the 20th century further revolutionized the spinning process, enabling the production of highly precise and complex parts.
Aluminum alloys gained prominence in the aerospace and automotive industries due to their lightweight and high-strength properties. The need for precision-formed aluminum parts led to the adoption of precision spinning technology in these sectors. Over the years, advancements in material science and manufacturing techniques have enhanced the capabilities of precision spinning, making it a preferred method for producing curved busbar type rotating body parts.
Principles of Precision Spinning
Precision spinning is a cold forming process that involves the plastic deformation of a rotating workpiece using a spinning tool. The workpiece, typically a disc or a tube, is mounted on a spinning lathe and rotated at high speeds. The spinning tool, which can be a roller or a mandrel, is then applied to the workpiece to gradually shape it into the desired form. The process can be categorized into two main types: conventional spinning and shear spinning.
- Conventional Spinning: In conventional spinning, the workpiece is deformed by a roller that moves radially inward or outward, depending on the desired shape. This method is suitable for producing axisymmetric parts with simple geometries.
- Shear Spinning: Shear spinning involves the use of a mandrel that applies a shearing force to the workpiece, causing it to flow plastically around the mandrel. This technique is ideal for producing parts with complex shapes and thin walls.
Material Selection
The selection of the appropriate aluminum alloy is crucial for the success of the precision spinning process. Aluminum alloys are classified into various series based on their primary alloying elements. The most commonly used series for precision spinning include:
- 1xxx Series: These are pure aluminum alloys with high formability and excellent corrosion resistance. They are suitable for applications requiring high electrical conductivity.
- 2xxx Series: Alloyed with copper, these alloys offer high strength and good formability. They are often used in aerospace applications.
- 5xxx Series: Alloyed with magnesium, these alloys provide good strength and excellent weldability. They are commonly used in marine and automotive applications.
- 6xxx Series: Alloyed with magnesium and silicon, these alloys offer a good balance of strength, formability, and corrosion resistance. They are widely used in structural applications.
- 7xxx Series: Alloyed with zinc, these alloys provide the highest strength among aluminum alloys. They are used in high-performance applications such as aerospace and defense.
Table 1: Properties of Common Aluminum Alloys
Alloy Series | Primary Alloying Element | Strength (MPa) | Formability | Corrosion Resistance | Electrical Conductivity (IACS%) |
---|---|---|---|---|---|
1xxx | Aluminum | 70-150 | Excellent | Excellent | 61-64 |
2xxx | Copper | 200-500 | Good | Fair | 30-45 |
5xxx | Magnesium | 150-300 | Good | Good | 35-45 |
6xxx | Magnesium, Silicon | 150-350 | Good | Good | 40-50 |
7xxx | Zinc | 350-600 | Fair | Fair | 30-40 |
Process Parameters
The success of precision spinning depends on several critical process parameters, including:
- Rotational Speed: The speed at which the workpiece rotates affects the deformation behavior and surface finish. Higher speeds generally result in better surface quality but may increase the risk of defects.
- Feed Rate: The rate at which the spinning tool moves relative to the workpiece influences the deformation rate and final dimensions. A slower feed rate allows for more controlled deformation but increases processing time.
- Tool Geometry: The design of the spinning tool, including its shape and size, plays a crucial role in determining the final shape and surface finish of the part.
- Lubrication: Proper lubrication is essential to reduce friction and heat generation during the spinning process. Common lubricants include oils, greases, and solid lubricants.
- Temperature: The temperature of the workpiece and tool affects the material’s flow behavior and formability. Precision spinning is typically performed at room temperature, but heated tools or workpieces may be used for certain alloys.
Table 2: Typical Process Parameters for Precision Spinning
Parameter | Range/Type | Effect on Process |
---|---|---|
Rotational Speed | 500-3000 RPM | Influences deformation behavior and surface finish |
Feed Rate | 0.5-5 mm/rev | Affects deformation rate and final dimensions |
Tool Geometry | Roller, Mandrel | Determines final shape and surface finish |
Lubrication | Oils, Greases, Solid Lubricants | Reduces friction and heat generation |
Temperature | Room Temperature, Heated Tools | Affects material flow behavior and formability |
Advantages of Precision Spinning
Precision spinning offers several advantages over traditional manufacturing methods such as casting, forging, and machining. These advantages include:
- High Dimensional Accuracy: Precision spinning can achieve tight tolerances and high dimensional accuracy, making it suitable for producing parts with complex geometries.
- Excellent Surface Finish: The controlled deformation process results in parts with a smooth and uniform surface finish, reducing the need for additional finishing operations.
- Material Savings: Precision spinning is a near-net-shape process, minimizing material waste and reducing the need for subsequent machining operations.
- Cost-Effective: The process is highly efficient and can be automated, leading to reduced production costs and increased productivity.
- Versatility: Precision spinning can be applied to a wide range of materials and part geometries, making it a versatile manufacturing method.
Applications
Curved busbar type rotating body parts produced through precision spinning are used in various industries, including:
- Aerospace: Aluminum alloy parts are used in aircraft structures, engine components, and electrical systems due to their lightweight and high-strength properties.
- Automotive: Precision-spun parts are used in vehicle bodies, engine components, and electrical systems, contributing to weight reduction and improved performance.
- Electrical: Busbars and other electrical components benefit from the high electrical conductivity and precise dimensions achieved through precision spinning.
- Defense: High-strength aluminum alloy parts are used in military vehicles, aircraft, and other defense applications, requiring robust and reliable components.
- Consumer Goods: Precision-spun parts are used in various consumer products, including appliances, electronics, and sporting goods, due to their aesthetic appeal and functional performance.
Table 3: Applications of Precision Spinning in Different Industries
Industry | Application Examples | Benefits |
---|---|---|
Aerospace | Aircraft structures, Engine components | Lightweight, High strength |
Automotive | Vehicle bodies, Engine components | Weight reduction, Improved performance |
Electrical | Busbars, Electrical components | High electrical conductivity, Precise dimensions |
Defense | Military vehicles, Aircraft | Robust, Reliable components |
Consumer Goods | Appliances, Electronics, Sporting goods | Aesthetic appeal, Functional performance |
Challenges and Limitations
Despite its numerous advantages, precision spinning also faces several challenges and limitations:
- Tool Wear: The spinning tool is subject to wear and tear due to the high forces and friction involved in the process. Regular maintenance and replacement of tools are necessary to ensure consistent quality.
- Material Limitations: Not all materials are suitable for precision spinning. Materials with poor formability or high strength may be difficult to spin, requiring alternative manufacturing methods.
- Complex Geometries: While precision spinning can produce complex shapes, there are limitations to the geometries that can be achieved. Parts with intricate features or sharp corners may require additional machining operations.
- Process Control: Precise control of process parameters is essential to achieve the desired part quality. Variations in rotational speed, feed rate, and tool geometry can lead to defects and inconsistencies.
- Cost: Although precision spinning is generally cost-effective, the initial investment in equipment and tooling can be high. Additionally, the need for skilled operators and regular maintenance can add to the overall cost.
Future Trends
The future of precision spinning technology holds promise for further advancements and innovations. Key trends include:
- Advanced Materials: The development of new aluminum alloys with improved formability and strength will expand the applications of precision spinning. Research is ongoing to create alloys with enhanced properties tailored for specific applications.
- Automation and Digitalization: The integration of automation and digital technologies, such as robotics and artificial intelligence, will enhance the efficiency and precision of the spinning process. Real-time monitoring and control systems will enable better process optimization and quality control.
- Hybrid Manufacturing: Combining precision spinning with other manufacturing techniques, such as additive manufacturing and machining, will allow for the production of parts with even more complex geometries and improved performance.
- Sustainability: There is a growing emphasis on sustainable manufacturing practices. Precision spinning, with its material-saving capabilities and reduced waste generation, aligns well with sustainability goals. Future developments will focus on further reducing the environmental impact of the process.
- Customization: The demand for customized parts is increasing across various industries. Precision spinning, with its flexibility and versatility, is well-suited to meet this demand. Advances in CNC technology will enable the production of highly customized parts with precise specifications.
Conclusion
Precision spinning forming technology is a highly effective and versatile manufacturing process for producing aluminum alloy curved busbar type rotating body parts. Its ability to achieve high dimensional accuracy, excellent surface finish, and material savings makes it a preferred method for various industrial applications. The selection of appropriate aluminum alloys, careful control of process parameters, and continuous innovation will drive the future growth and adoption of precision spinning technology.
As the demand for high-performance, lightweight, and precise components continues to rise, precision spinning will play a crucial role in meeting the needs of advanced engineering applications. The integration of automation, digitalization, and hybrid manufacturing techniques will further enhance the capabilities of precision spinning, ensuring its relevance and importance in the manufacturing landscape.
Maximize Tooling and CNC Metal Spinning Capabilities.
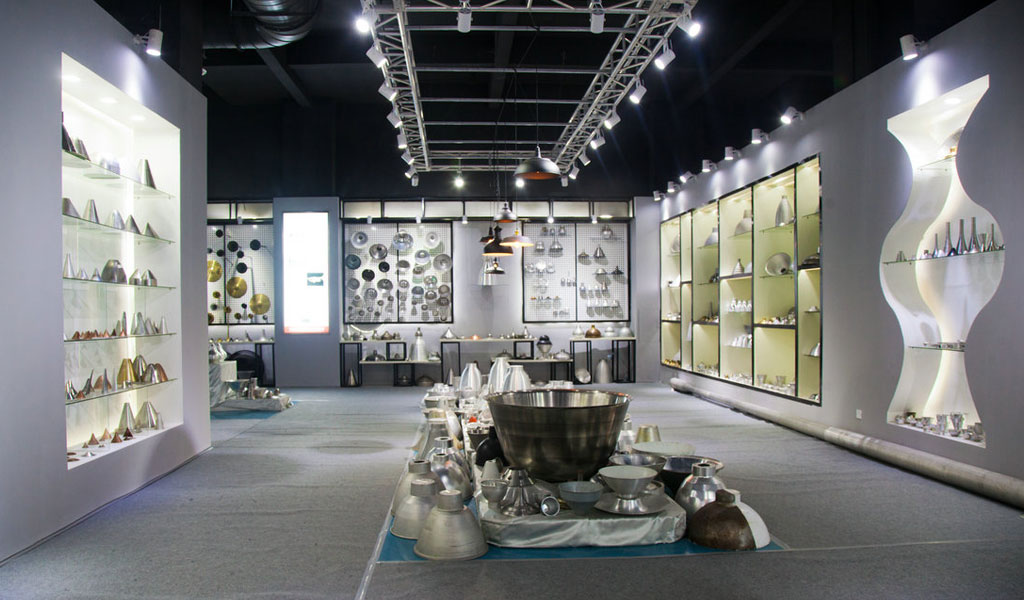
At BE-CU China Metal Spinning company, we make the most of our equipment while monitoring signs of excess wear and stress. In addition, we look into newer, modern equipment and invest in those that can support or increase our manufacturing capabilities. Our team is very mindful of our machines and tools, so we also routinely maintain them to ensure they don’t negatively impact your part’s quality and productivity.
Talk to us today about making a rapid prototype with our CNC metal spinning service. Get a direct quote by chatting with us here or request a free project review.
BE-CU China CNC Metal Spinning service include : CNC Metal Spinning,Metal Spinning Die,Laser Cutting, Tank Heads Spinning,Metal Hemispheres Spinning,Metal Cones Spinning,Metal Dish-Shaped Spinning,Metal Trumpet Spinning,Metal Venturi Spinning,Aluminum Spinning Products,Stainless Steel Spinning Products,Copper Spinning Products,Brass Spinning Products,Steel Spinning Product,Metal Spinnin LED Reflector,Metal Spinning Pressure Vessel,