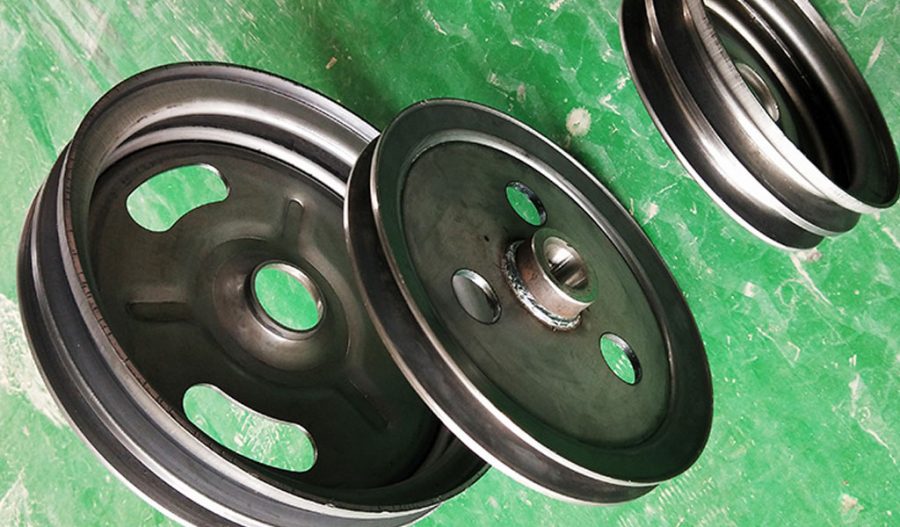
Aluminum alloy thin-wall seamless liners are advanced materials used in various industrial applications due to their superior mechanical properties, lightweight nature, and corrosion resistance. These liners are particularly valuable in aerospace, automotive, and chemical industries, where precision and durability are critical. This article delves into the precision spinning forming method used to manufacture aluminum alloy thin-wall seamless liners, their applications, and a detailed comparison with other manufacturing techniques.
Introduction to Aluminum Alloy Thin-Wall Seamless Liners
Aluminum alloys are a class of materials that combine aluminum with other elements to enhance their properties. Common alloying elements include copper, magnesium, silicon, and zinc. These alloys are prized for their high strength-to-weight ratio, excellent corrosion resistance, and good formability. Thin-wall seamless liners made from aluminum alloys are particularly useful in applications requiring lightweight, high-strength components.
Precision Spinning Forming Method
Precision spinning, also known as metal spinning or spin forming, is a manufacturing process that shapes a flat metal disc or tube into a seamless, axisymmetric part. This method is particularly suitable for producing thin-wall components with high dimensional accuracy and surface finish. The process involves several key steps:
- Blank Preparation: The process begins with a flat metal disc or tube, known as the blank. The blank is typically cut from a sheet or extruded tube of the desired aluminum alloy.
- Clamping: The blank is securely clamped onto a spinning mandrel or chuck. The mandrel rotates at high speeds, typically ranging from 500 to 3000 RPM, depending on the material and desired shape.
- Forming: A forming tool, usually a roller or a set of rollers, is applied to the spinning blank. The tool gradually shapes the blank against the mandrel, creating the desired profile. The forming process can be performed in multiple passes to achieve complex shapes and high precision.
- Finishing: After the initial forming, the part may undergo additional finishing operations such as trimming, polishing, or heat treatment to enhance its mechanical properties and surface finish.
Advantages of Precision Spinning
Precision spinning offers several advantages over other manufacturing methods:
- High Precision: The process can achieve tight dimensional tolerances and excellent surface finish, making it ideal for thin-wall components.
- Cost-Effective: Compared to other methods like machining or casting, precision spinning can be more cost-effective for producing axisymmetric parts.
- Material Efficiency: The process minimizes material waste, as it does not involve cutting or removing material.
- Versatility: Precision spinning can be used to produce a wide range of shapes and sizes, from small components to large diameter parts.
Applications of Aluminum Alloy Thin-Wall Seamless Liners
Aluminum alloy thin-wall seamless liners find applications in various industries due to their unique properties:
- Aerospace Industry: In the aerospace industry, these liners are used in the manufacture of aircraft components such as fuel tanks, hydraulic lines, and structural elements. The lightweight and high strength of aluminum alloys make them ideal for reducing the overall weight of the aircraft, thereby improving fuel efficiency.
- Automotive Industry: In the automotive sector, thin-wall seamless liners are used in engine components, exhaust systems, and structural parts. The corrosion resistance and formability of aluminum alloys make them suitable for these applications.
- Chemical Industry: In the chemical industry, these liners are used in the production of pressure vessels, piping, and storage tanks. The corrosion resistance of aluminum alloys makes them ideal for handling aggressive chemicals and harsh environments.
- Consumer Goods: Aluminum alloy thin-wall seamless liners are also used in the manufacture of consumer goods such as cookware, appliances, and sporting equipment. The lightweight and durability of these materials enhance the performance and longevity of these products.
Comparison with Other Manufacturing Methods
To understand the advantages of precision spinning for producing aluminum alloy thin-wall seamless liners, it is essential to compare it with other manufacturing methods. The following table provides a detailed comparison:
Feature | Precision Spinning | Machining | Casting | Forging |
---|---|---|---|---|
Dimensional Accuracy | High | High | Moderate | Moderate |
Surface Finish | Excellent | Good | Fair | Fair |
Material Waste | Low | High | Moderate | Low |
Cost | Moderate | High | Low | Moderate |
Production Speed | Moderate | Slow | Fast | Moderate |
Versatility | High | High | Moderate | Moderate |
Suitability for Thin-Wall Components | Excellent | Poor | Poor | Poor |
Detailed Analysis of Precision Spinning Parameters
The success of precision spinning depends on various parameters, including the rotational speed of the mandrel, the feed rate of the forming tool, the geometry of the tool, and the properties of the aluminum alloy. The following sections provide a detailed analysis of these parameters:
- Rotational Speed: The rotational speed of the mandrel is a critical parameter that affects the forming process. Higher speeds can improve the surface finish and dimensional accuracy but may also increase the risk of material failure. Optimal speeds are determined based on the material properties and the desired shape.
- Feed Rate: The feed rate of the forming tool determines the rate at which the material is deformed. A slower feed rate can improve the precision and surface finish but may increase the production time. Faster feed rates can reduce production time but may compromise the quality of the final part.
- Tool Geometry: The geometry of the forming tool plays a crucial role in the precision spinning process. The shape, size, and angle of the tool affect the material flow and the final shape of the part. Different tool geometries are used for various applications, depending on the desired profile and material properties.
- Material Properties: The properties of the aluminum alloy, such as its ductility, strength, and hardness, significantly influence the precision spinning process. Alloys with higher ductility are easier to form but may require additional heat treatment to enhance their mechanical properties.
Case Studies and Real-World Applications
Several case studies and real-world applications demonstrate the effectiveness of precision spinning for producing aluminum alloy thin-wall seamless liners:
- Aerospace Component Manufacturing: A leading aerospace manufacturer used precision spinning to produce thin-wall fuel tanks for aircraft. The process resulted in a 30% reduction in material waste and a 20% improvement in dimensional accuracy compared to traditional machining methods.
- Automotive Exhaust Systems: An automotive company employed precision spinning to manufacture thin-wall exhaust pipes. The process enabled the production of lightweight, high-strength components with excellent corrosion resistance, leading to improved fuel efficiency and reduced emissions.
- Chemical Pressure Vessels: A chemical processing plant utilized precision spinning to produce thin-wall pressure vessels. The vessels exhibited superior corrosion resistance and durability, ensuring safe and efficient handling of aggressive chemicals.
Future Trends and Innovations
The field of precision spinning for aluminum alloy thin-wall seamless liners is continually evolving, driven by advancements in technology and material science. Some of the future trends and innovations include:
- Advanced Materials: The development of new aluminum alloys with enhanced properties, such as higher strength, improved ductility, and better corrosion resistance, will expand the applications of thin-wall seamless liners.
- Automation and Robotics: The integration of automation and robotics in the precision spinning process will improve efficiency, reduce production time, and enhance the consistency of the final parts.
- Simulation and Modeling: The use of advanced simulation and modeling techniques will enable better prediction of material behavior during the forming process, leading to optimized tool geometries and process parameters.
- Sustainability: The focus on sustainability will drive the development of more environmentally friendly manufacturing processes, including the use of recycled aluminum alloys and energy-efficient spinning techniques.
Conclusion
Aluminum alloy thin-wall seamless liners are critical components in various industries, offering superior mechanical properties, lightweight nature, and corrosion resistance. The precision spinning forming method is a highly effective and efficient way to produce these liners, providing high dimensional accuracy, excellent surface finish, and material efficiency. As technology advances, the applications and benefits of precision spinning for aluminum alloy thin-wall seamless liners will continue to grow, driving innovation and sustainability in manufacturing.
Maximize Tooling and CNC Metal Spinning Capabilities.
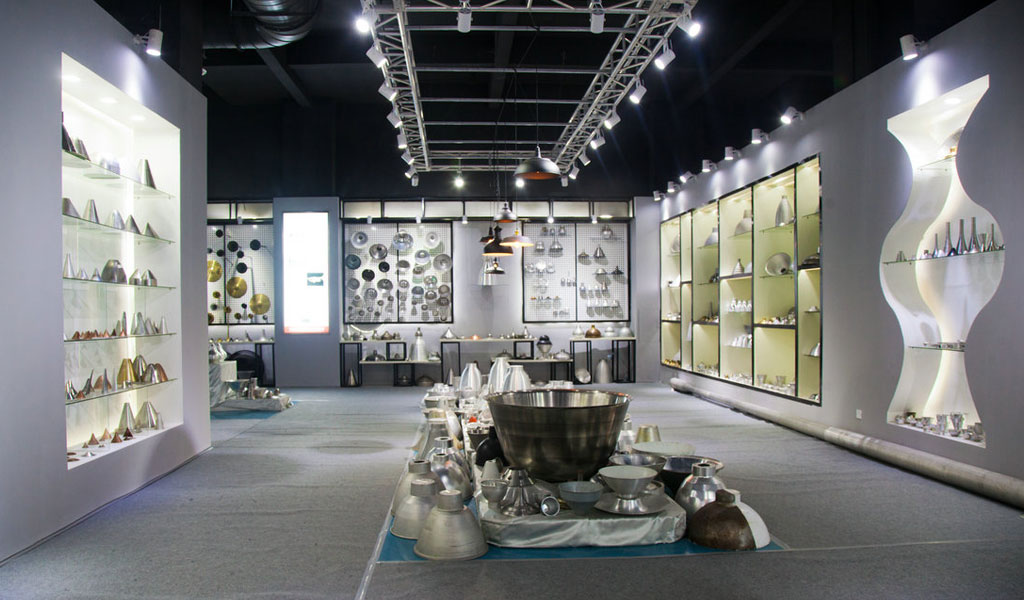
At BE-CU China Metal Spinning company, we make the most of our equipment while monitoring signs of excess wear and stress. In addition, we look into newer, modern equipment and invest in those that can support or increase our manufacturing capabilities. Our team is very mindful of our machines and tools, so we also routinely maintain them to ensure they don’t negatively impact your part’s quality and productivity.
Talk to us today about making a rapid prototype with our CNC metal spinning service. Get a direct quote by chatting with us here or request a free project review.
BE-CU China CNC Metal Spinning service include : CNC Metal Spinning,Metal Spinning Die,Laser Cutting, Tank Heads Spinning,Metal Hemispheres Spinning,Metal Cones Spinning,Metal Dish-Shaped Spinning,Metal Trumpet Spinning,Metal Venturi Spinning,Aluminum Spinning Products,Stainless Steel Spinning Products,Copper Spinning Products,Brass Spinning Products,Steel Spinning Product,Metal Spinnin LED Reflector,Metal Spinning Pressure Vessel,