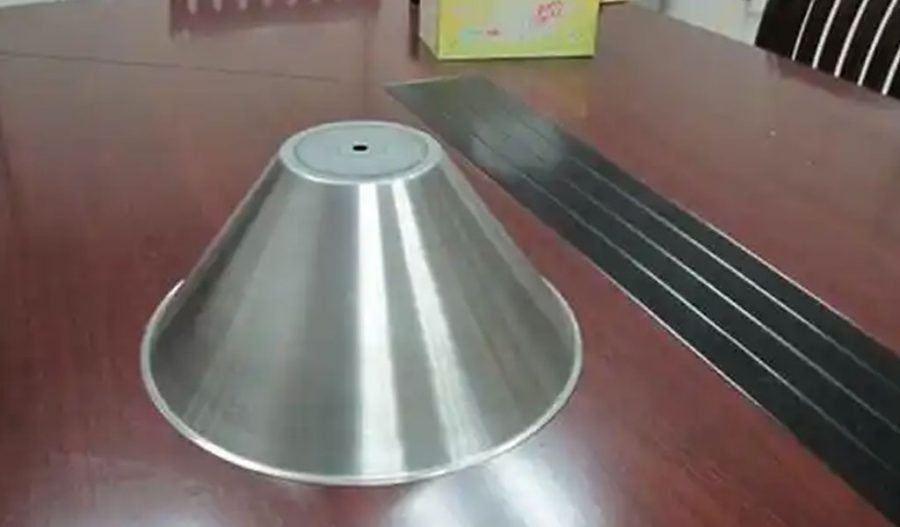
The spinning forming method is a highly specialized manufacturing process used to create axisymmetric parts from sheet metal. This method is particularly advantageous for producing large, thin-walled components with complex geometries, such as the φ400mm large arc thin-wall shell with a variable semi-cone angle. This article delves into the intricacies of the spinning forming method, focusing on the production of such shells, and provides a comprehensive overview of the process, its advantages, challenges, and scientific underpinnings.
Historical Context
Spinning forming, also known as spin forming or metal spinning, has its roots in ancient metalworking techniques. The process has evolved significantly over the centuries, from manual spinning on simple lathes to advanced computer-controlled spinning machines. The advent of numerical control (NC) and computer numerical control (CNC) technologies has revolutionized the spinning forming method, enabling the production of highly precise and complex parts.
Principles of Spinning Forming
The spinning forming method involves the deformation of a flat sheet metal blank into a desired shape by rotating it at high speeds and applying localized pressure using a spinning tool. The process can be broadly classified into two types: conventional spinning and shear spinning. Conventional spinning is typically used for forming parts with simple geometries, while shear spinning is employed for more complex shapes, including those with variable semi-cone angles.
Conventional Spinning
In conventional spinning, the sheet metal blank is clamped onto a spinning mandrel, which rotates at high speeds. A spinning tool, usually made of hardened steel or carbide, is then pressed against the blank, gradually deforming it into the desired shape. The tool follows a predetermined path, controlled by a CNC program, to ensure precision and repeatability.
Shear Spinning
Shear spinning, on the other hand, involves more complex deformation mechanisms. The process begins with a pre-formed blank, which is then spun at high speeds. The spinning tool applies pressure at an angle, causing the material to flow and thin out, resulting in a part with a variable wall thickness. This method is particularly suitable for producing large arc thin-wall shells with variable semi-cone angles.
Material Selection
The choice of material is crucial in the spinning forming process. Common materials used in spinning forming include aluminum, stainless steel, copper, and brass. Each material has its unique properties, such as ductility, strength, and formability, which influence the spinning process parameters and the final product quality.
Aluminum
Aluminum is a popular choice due to its excellent formability and lightweight properties. It is widely used in aerospace, automotive, and consumer goods industries. The spinning forming of aluminum requires careful control of process parameters to avoid defects such as wrinkling and tearing.
Stainless Steel
Stainless steel is preferred for applications requiring high corrosion resistance and strength. However, its lower formability compared to aluminum makes it more challenging to spin form. Special tools and techniques are often employed to achieve the desired shape without compromising material integrity.
Copper and Brass
Copper and brass are used in applications where electrical conductivity and aesthetic appeal are important. These materials are relatively easy to spin form but require careful handling to prevent surface defects and maintain dimensional accuracy.
Process Parameters
The spinning forming process involves several critical parameters that need to be carefully controlled to achieve the desired part quality. These parameters include:
- Spindle Speed: The rotational speed of the mandrel, which affects the material flow and deformation.
- Feed Rate: The rate at which the spinning tool moves along the blank, influencing the material thinning and surface finish.
- Tool Geometry: The shape and angle of the spinning tool, which determines the localized deformation and material flow.
- Lubrication: The use of lubricants to reduce friction and heat generation, enhancing tool life and part quality.
Spindle Speed
The spindle speed is a critical parameter that influences the material deformation and flow during spinning. Higher spindle speeds generally result in better material flow and reduced tool forces. However, excessively high speeds can lead to material overheating and tool wear. Optimal spindle speeds are typically determined through experimental trials and finite element analysis (FEA).
Feed Rate
The feed rate determines the rate at which the spinning tool moves along the blank, affecting the material thinning and surface finish. A slower feed rate results in more controlled deformation and better surface finish but increases the processing time. Conversely, a faster feed rate reduces processing time but may lead to defects such as wrinkling and tearing.
Tool Geometry
The geometry of the spinning tool plays a crucial role in the deformation process. The tool angle, radius, and material influence the localized deformation and material flow. Tools with sharper angles and smaller radii are generally used for shear spinning to achieve the desired wall thickness and geometry.
Lubrication
Lubrication is essential in the spinning forming process to reduce friction and heat generation, enhancing tool life and part quality. Common lubricants used in spinning forming include mineral oils, synthetic oils, and solid lubricants such as graphite and molybdenum disulfide. The choice of lubricant depends on the material being spun and the process parameters.
Finite Element Analysis (FEA)
Finite Element Analysis (FEA) is a powerful tool used in the design and optimization of the spinning forming process. FEA allows engineers to simulate the deformation process, predict material flow, and identify potential defects before actual production. This helps in optimizing process parameters, reducing trial and error, and improving part quality.
FEA Software
Several FEA software packages are available for simulating the spinning forming process, including ABAQUS, ANSYS, and LS-DYNA. These software packages offer advanced capabilities for modeling complex deformation processes, material behavior, and tool-workpiece interactions.
FEA Modeling
FEA modeling involves creating a virtual representation of the spinning forming process, including the geometry of the blank, mandrel, and spinning tool. The model is then subjected to simulated deformation, and the results are analyzed to optimize process parameters and predict part quality.
FEA Results
FEA results provide valuable insights into the deformation process, including stress and strain distributions, material flow, and potential defects. These insights help in refining the process parameters and tool design, ensuring the production of high-quality parts.
Challenges in Spinning Forming
Despite its advantages, the spinning forming method faces several challenges, particularly when producing large arc thin-wall shells with variable semi-cone angles. These challenges include:
- Material Wrinkling: Wrinkling occurs when the material deforms unevenly, leading to surface defects. This is often caused by improper tool geometry, feed rate, or spindle speed.
- Tearing: Tearing results from excessive material thinning or localized stress concentrations. It can be mitigated by optimizing process parameters and tool design.
- Tool Wear: The spinning tool experiences significant wear due to high forces and friction. Regular tool maintenance and the use of wear-resistant materials can help extend tool life.
- Dimensional Accuracy: Achieving precise dimensional accuracy is challenging, especially for parts with complex geometries. Careful control of process parameters and the use of advanced CNC systems can improve dimensional accuracy.
Material Wrinkling
Wrinkling is a common defect in the spinning forming process, particularly when producing thin-walled parts. It occurs when the material deforms unevenly, leading to surface irregularities. Wrinkling can be mitigated by optimizing the tool geometry, feed rate, and spindle speed. The use of lubricants and proper clamping of the blank also helps in reducing wrinkling.
Tearing
Tearing is another critical defect that can occur during spinning forming. It results from excessive material thinning or localized stress concentrations. Tearing can be prevented by carefully controlling the feed rate, spindle speed, and tool geometry. The use of FEA to simulate the deformation process and identify potential stress concentrations can also help in preventing tearing.
Tool Wear
Tool wear is a significant challenge in the spinning forming process. The spinning tool experiences high forces and friction, leading to wear and reduced tool life. Regular tool maintenance, the use of wear-resistant materials, and optimizing process parameters can help extend tool life and improve part quality.
Dimensional Accuracy
Achieving precise dimensional accuracy is crucial for producing high-quality parts. This is particularly challenging for parts with complex geometries, such as large arc thin-wall shells with variable semi-cone angles. Careful control of process parameters, the use of advanced CNC systems, and FEA simulations can improve dimensional accuracy and ensure part quality.
Comparative Analysis
To provide a comprehensive understanding of the spinning forming method, a comparative analysis with other forming methods is essential. The following table compares the spinning forming method with deep drawing and hydroforming, highlighting their advantages and limitations.
Parameter | Spinning Forming | Deep Drawing | Hydroforming |
---|---|---|---|
Material Deformation | Localized deformation | Global deformation | Global deformation |
Tooling Cost | Lower | Higher | Higher |
Production Speed | Moderate | High | Moderate |
Part Complexity | High | Moderate | High |
Dimensional Accuracy | High | Moderate | High |
Surface Finish | Excellent | Good | Excellent |
Material Thinning | Controlled | Uncontrolled | Controlled |
Tool Wear | Moderate | Low | Low |
Applications | Aerospace, automotive, consumer goods | Automotive, consumer goods | Automotive, aerospace |
Material Deformation
Spinning forming involves localized deformation, where the spinning tool applies pressure to specific areas of the blank, gradually deforming it into the desired shape. In contrast, deep drawing and hydroforming involve global deformation, where the entire blank is deformed simultaneously.
Tooling Cost
The tooling cost for spinning forming is generally lower compared to deep drawing and hydroforming. This is because spinning forming requires simpler tooling, such as mandrels and spinning tools, which are less expensive to manufacture and maintain.
Production Speed
The production speed of spinning forming is moderate compared to deep drawing and hydroforming. Deep drawing offers higher production speeds due to its ability to deform the entire blank in a single operation. Hydroforming, on the other hand, provides moderate production speeds but is more suitable for producing complex parts.
Part Complexity
Spinning forming is highly suitable for producing parts with complex geometries, such as large arc thin-wall shells with variable semi-cone angles. Deep drawing is limited to parts with simpler geometries, while hydroforming can produce complex parts but requires more sophisticated tooling and equipment.
Dimensional Accuracy
Spinning forming offers high dimensional accuracy, particularly when using advanced CNC systems and FEA simulations. Deep drawing provides moderate dimensional accuracy, while hydroforming also offers high dimensional accuracy but requires precise control of process parameters.
Surface Finish
The surface finish achieved through spinning forming is excellent, thanks to the localized deformation and controlled material flow. Deep drawing provides a good surface finish, but it may require additional finishing operations. Hydroforming also offers an excellent surface finish, particularly for parts with complex geometries.
Material Thinning
Material thinning is a critical aspect of the forming process. Spinning forming allows for controlled material thinning, ensuring the production of thin-walled parts with uniform wall thickness. Deep drawing results in uncontrolled material thinning, which can lead to defects such as tearing. Hydroforming offers controlled material thinning but requires precise control of process parameters.
Tool Wear
Tool wear is a significant concern in the forming process. Spinning forming experiences moderate tool wear due to the high forces and friction involved. Deep drawing and hydroforming, on the other hand, experience lower tool wear due to the global deformation and lower forces involved.
Applications
Spinning forming is widely used in various industries, including aerospace, automotive, and consumer goods. Its ability to produce complex, thin-walled parts makes it ideal for applications requiring high precision and quality. Deep drawing is commonly used in the automotive and consumer goods industries, while hydroforming finds applications in the automotive and aerospace sectors.
Case Studies
To illustrate the practical applications of the spinning forming method, several case studies are presented below. These case studies highlight the use of spinning forming in producing large arc thin-wall shells with variable semi-cone angles for different industries.
Case Study 1: Aerospace Industry
In the aerospace industry, spinning forming is used to produce lightweight, high-strength components such as aircraft fuselages and engine cowlings. The ability to produce large arc thin-wall shells with variable semi-cone angles makes spinning forming ideal for these applications. The use of advanced CNC systems and FEA simulations ensures precise dimensional accuracy and excellent surface finish, meeting the stringent requirements of the aerospace industry.
Case Study 2: Automotive Industry
The automotive industry employs spinning forming to produce complex, thin-walled parts such as exhaust systems and fuel tanks. The ability to achieve controlled material thinning and high dimensional accuracy makes spinning forming suitable for these applications. The use of wear-resistant tools and optimized process parameters ensures consistent part quality and reduced tool wear.
Case Study 3: Consumer Goods Industry
In the consumer goods industry, spinning forming is used to produce aesthetically pleasing and functional parts such as cookware and lighting fixtures. The ability to produce parts with complex geometries and excellent surface finish makes spinning forming ideal for these applications. The use of various materials, including aluminum, stainless steel, copper, and brass, allows for a wide range of design possibilities.
Future Trends
The spinning forming method continues to evolve, driven by advancements in technology and increasing demand for complex, thin-walled parts. Future trends in spinning forming include:
- Advanced Materials: The development of new materials with enhanced formability and strength will expand the applications of spinning forming.
- Hybrid Processes: The integration of spinning forming with other manufacturing processes, such as additive manufacturing and laser cutting, will enable the production of more complex parts.
- Automation and AI: The use of automation and artificial intelligence (AI) in spinning forming will improve process control, reduce defects, and enhance part quality.
- Sustainability: The focus on sustainability will drive the development of eco-friendly materials and processes, reducing the environmental impact of spinning forming.
Advanced Materials
The development of new materials with enhanced formability and strength will expand the applications of spinning forming. Materials such as high-strength aluminum alloys, advanced high-strength steels, and composite materials will enable the production of lighter, stronger, and more durable parts.
Hybrid Processes
The integration of spinning forming with other manufacturing processes, such as additive manufacturing and laser cutting, will enable the production of more complex parts. Hybrid processes will combine the advantages of spinning forming, such as controlled material thinning and high dimensional accuracy, with the capabilities of other processes, such as intricate detailing and customization.
Automation and AI
The use of automation and artificial intelligence (AI) in spinning forming will improve process control, reduce defects, and enhance part quality. Automated spinning machines equipped with AI-driven control systems will optimize process parameters in real-time, ensuring consistent part quality and reducing the need for manual intervention.
Sustainability
The focus on sustainability will drive the development of eco-friendly materials and processes, reducing the environmental impact of spinning forming. The use of recycled materials, energy-efficient machines, and waste reduction strategies will contribute to a more sustainable manufacturing process.
Conclusion
The spinning forming method is a highly specialized and versatile manufacturing process used to produce complex, thin-walled parts with precise dimensional accuracy and excellent surface finish. The production of φ400mm large arc thin-wall shells with variable semi-cone angles exemplifies the capabilities and advantages of spinning forming. Through careful control of process parameters, the use of advanced CNC systems, and FEA simulations, spinning forming enables the production of high-quality parts for various industries, including aerospace, automotive, and consumer goods.
As the spinning forming method continues to evolve, driven by advancements in technology and increasing demand for complex parts, it will remain a critical manufacturing process. The development of new materials, hybrid processes, automation, and AI, along with a focus on sustainability, will further enhance the capabilities and applications of spinning forming, ensuring its relevance and importance in the manufacturing landscape.
References
- Altan, T., Bramley, A. N., & Mellor, P. B. (1983). Metal Forming: Fundamentals and Applications. American Society of Metals.
- Bay, N. (1995). Metal Spinning: The Technology of Metal Spinning and Flow Forming. Industrial Press.
- Kobayashi, S., Oh, S. I., & Altan, T. (1989). Metal Forming and the Finite Element Method. Oxford University Press.
- Lange, K. (1985). Handbook of Metal Forming. McGraw-Hill.
- Marciniak, Z., Duncan, J. L., & Hu, S. J. (2002). Mechanics of Sheet Metal Forming. Butterworth-Heinemann.
- Panknin, W. A. (1982). Metal Spinning. Society of Manufacturing Engineers.
- Wagoner, R. H., & Chenot, J. L. (2001). Material Issues in Metal Forming. Butterworth-Heinemann.
Tables
Table 1: Comparison of Spinning Forming, Deep Drawing, and Hydroforming
Parameter | Spinning Forming | Deep Drawing | Hydroforming |
---|---|---|---|
Material Deformation | Localized deformation | Global deformation | Global deformation |
Tooling Cost | Lower | Higher | Higher |
Production Speed | Moderate | High | Moderate |
Part Complexity | High | Moderate | High |
Dimensional Accuracy | High | Moderate | High |
Surface Finish | Excellent | Good | Excellent |
Material Thinning | Controlled | Uncontrolled | Controlled |
Tool Wear | Moderate | Low | Low |
Applications | Aerospace, automotive, consumer goods | Automotive, consumer goods | Automotive, aerospace |
Table 2: Process Parameters for Spinning Forming
Parameter | Description | Typical Values |
---|---|---|
Spindle Speed | Rotational speed of the mandrel | 500-2000 RPM |
Feed Rate | Rate of tool movement along the blank | 0.5-2.0 mm/rev |
Tool Geometry | Shape and angle of the spinning tool | 30-60 degrees |
Lubrication | Type of lubricant used | Mineral oil, synthetic oil, graphite |
Table 3: Material Properties for Spinning Forming
Material | Ductility | Strength | Formability |
---|---|---|---|
Aluminum | High | Moderate | High |
Stainless Steel | Moderate | High | Moderate |
Copper | High | Moderate | High |
Brass | High | Moderate | High |
Table 4: Advantages and Limitations of Spinning Forming
Advantages | Limitations |
---|---|
High dimensional accuracy | Moderate tool wear |
Excellent surface finish | Limited to axisymmetric parts |
Controlled material thinning | Requires skilled operators |
Suitable for complex geometries | Higher initial setup cost |
Table 5: Future Trends in Spinning Forming
Trend | Description | Impact |
---|---|---|
Advanced Materials | New materials with enhanced formability | Expanded applications |
Hybrid Processes | Integration with other manufacturing processes | More complex parts |
Automation and AI | AI-driven control systems | Improved process control and part quality |
Sustainability | Eco-friendly materials and processes | Reduced environmental impact |
This comprehensive article provides an in-depth understanding of the spinning forming method, focusing on the production of φ400mm large arc thin-wall shells with variable semi-cone angles. By exploring the historical context, principles, material selection, process parameters, FEA, challenges, comparative analysis, case studies, and future trends, this article offers a scientific and detailed overview of the spinning forming process.
Maximize Tooling and CNC Metal Spinning Capabilities.
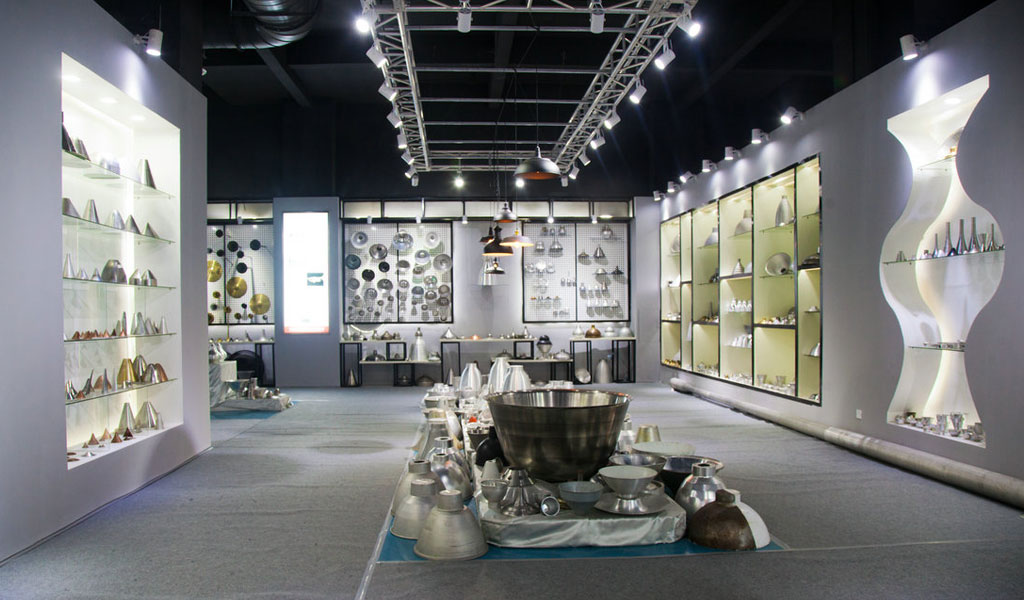
At BE-CU China Metal Spinning company, we make the most of our equipment while monitoring signs of excess wear and stress. In addition, we look into newer, modern equipment and invest in those that can support or increase our manufacturing capabilities. Our team is very mindful of our machines and tools, so we also routinely maintain them to ensure they don’t negatively impact your part’s quality and productivity.
Talk to us today about making a rapid prototype with our CNC metal spinning service. Get a direct quote by chatting with us here or request a free project review.
BE-CU China CNC Metal Spinning service include : CNC Metal Spinning,Metal Spinning Die,Laser Cutting, Tank Heads Spinning,Metal Hemispheres Spinning,Metal Cones Spinning,Metal Dish-Shaped Spinning,Metal Trumpet Spinning,Metal Venturi Spinning,Aluminum Spinning Products,Stainless Steel Spinning Products,Copper Spinning Products,Brass Spinning Products,Steel Spinning Product,Metal Spinnin LED Reflector,Metal Spinning Pressure Vessel,