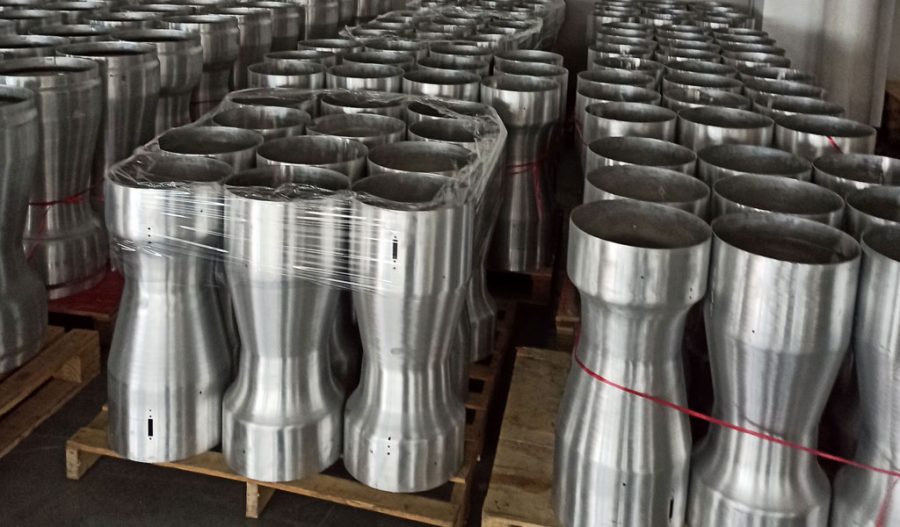
The Venturi air valve is a specialized flow control device widely utilized in heating, ventilation, and air conditioning (HVAC) systems, laboratories, industrial environments, and critical spaces requiring precise airflow regulation. Named after the Italian physicist Giovanni Battista Venturi, who first described the Venturi effect in 1797, this valve leverages the principles of fluid dynamics to achieve pressure-independent airflow control. The Venturi effect, a cornerstone of its operation, describes the reduction in fluid pressure that occurs when a fluid accelerates through a constricted section of a pipe, balanced by an increase in velocity as dictated by the continuity equation and Bernoulli’s principle. In modern engineering, the Venturi air valve stands out for its mechanical simplicity, rapid response to pressure changes, and ability to maintain consistent airflow across a range of operating conditions, making it a vital component in environments where safety, precision, and energy efficiency are paramount.
Principles of Operation
The Venturi air valve operates based on the Venturi effect, which arises from the conservation of mass and energy in fluid flow. As air passes through the valve’s characteristic hourglass-shaped body—featuring a converging inlet, a narrow throat, and a diverging outlet—the cross-sectional area decreases at the throat, causing the air velocity to increase. According to the continuity equation, Q=A⋅v, where Q is the volumetric flow rate, A is the cross-sectional area, and v is the velocity, a reduction in A necessitates an increase in v v v to maintain constant flow. Simultaneously, Bernoulli’s principle, expressed as P+21ρv2+ρgh=constant(where P P P is pressure, ρ \rho ρ is density, v v v is velocity, g g g is gravitational acceleration, and h h h is elevation), dictates that this increase in velocity results in a corresponding decrease in static pressure at the throat.
In practical terms, the Venturi air valve incorporates a spring-loaded cone assembly within the throat. This assembly dynamically adjusts its position in response to changes in duct static pressure, modulating the effective flow area to maintain a preset airflow rate. Unlike traditional variable air volume (VAV) systems that rely on dampers and external sensors, the Venturi valve’s mechanical pressure independence eliminates the need for continuous feedback loops, reducing signal latency and enhancing responsiveness. Factory calibration aligns the cone’s position with specific airflow rates, ensuring accuracy within a typical tolerance of ±5%, even as upstream conditions fluctuate.
Design and Components
A typical Venturi air valve consists of several key components:
- Valve Body: Constructed from materials such as aluminum alloy, stainless steel, or coated carbon steel, the body features a converging-diverging geometry. The hourglass shape is engineered to minimize turbulence and pressure loss while maximizing flow control precision.
- Cone Assembly: Positioned within the throat, this movable component is attached to a lever arm and spring mechanism. Its shape and material are optimized to balance aerodynamic forces and mechanical resistance.
- Spring Mechanism: Provides the restoring force that adjusts the cone’s position, enabling passive response to pressure variations without external power.
- Actuator (Optional): In actuated models, an electric or pneumatic actuator enhances control for variable airflow applications, integrating with building management systems (BMS) via protocols like BACnet or Modbus.
- Potentiometer: Measures the cone’s position, correlating it to airflow rates based on factory-characterized data curves, eliminating the need for direct airflow sensors in the airstream.
The valve’s design avoids the pitfalls of traditional airflow measurement devices, such as susceptibility to dust accumulation or the need for straight duct runs, enhancing reliability in contaminated or space-constrained environments.
Applications
Venturi air valves are predominantly deployed in settings requiring stringent airflow control, including:
- Laboratories: In chemical and biological labs, they regulate exhaust through fume hoods, maintaining negative pressure to prevent hazardous substance release. Their rapid response (often within milliseconds) ensures safety during sudden pressure shifts.
- Healthcare Facilities: Operating rooms and isolation wards use Venturi valves to sustain positive or negative pressurization, protecting patients and staff from airborne pathogens.
- Cleanrooms: In semiconductor manufacturing and pharmaceutical production, these valves maintain laminar flow and precise pressure differentials, safeguarding product integrity.
- Industrial Ventilation: Processes involving dust, fumes, or volatile compounds benefit from the valve’s ability to handle variable exhaust demands efficiently.
Comparison with Traditional VAV Systems
To understand the Venturi air valve’s advantages, a comparison with conventional VAV terminal boxes is instructive. VAV systems use butterfly dampers modulated by actuators responding to sensor feedback, adjusting airflow based on temperature or pressure signals. While effective in non-critical environments like offices, their reliance on external controls introduces delays and potential inaccuracies in dynamic conditions.
Table 1: Venturi Air Valve vs. Traditional VAV System
Feature | Venturi Air Valve | Traditional VAV System |
---|---|---|
Pressure Independence | Mechanical, inherent to design | Requires sensors and actuators |
Response Time | <0.1 seconds | 1–5 seconds (signal latency) |
Airflow Measurement | Indirect via cone position | Direct via sensors (e.g., pitot tubes) |
Turndown Ratio | High (up to 20:1) | Moderate (typically 10:1) |
Maintenance | Minimal, no sensors in airstream | Regular sensor cleaning/calibration |
Energy Efficiency | Optimized at low pressures | Higher fan power at low flows |
Cost | Higher initial cost, lower lifecycle cost | Lower initial cost, higher maintenance |
The Venturi valve’s superior turndown ratio—its ability to maintain accuracy across a wide range of flow rates—stems from its factory characterization, reducing energy waste in low-demand scenarios. Conversely, VAV systems often require higher duct pressures, increasing fan energy consumption.
Material Selection and Durability
Material choice significantly impacts the valve’s performance and longevity. Aluminum alloys, prized for their lightweight and corrosion-resistant properties, dominate in HVAC applications. Stainless steel, with its resistance to rust and high-pressure tolerance, suits aggressive environments like chemical labs. Advanced coatings, such as PTFE or epoxy, enhance durability against corrosive gases or particulate matter.
Table 2: Material Properties for Venturi Air Valves
Material | Density (kg/m³) | Tensile Strength (MPa) | Corrosion Resistance | Typical Use |
---|---|---|---|---|
Aluminum Alloy | 2,700 | 300–500 | High | General HVAC, labs |
Stainless Steel | 8,000 | 500–700 | Very High | Chemical labs, healthcare |
Coated Carbon Steel | 7,850 | 400–600 | Moderate (coating-dependent) | Industrial ventilation |
Carbon Fiber | 1,800 | 1,500–2,000 | High | Specialized applications |
Stainless steel’s higher density increases weight, potentially complicating installation, but its robustness justifies the trade-off in critical settings. Carbon fiber, though cost-prohibitive, offers exceptional strength-to-weight ratios for niche uses.
Energy Efficiency and Environmental Impact
Energy efficiency is a defining feature of Venturi air valves, particularly in usage-based control (UBC) configurations. By maintaining minimal safe airflow rates and scaling up only when occupancy or process demands increase, these valves reduce unnecessary ventilation, cutting fan power usage by up to 30% compared to constant-volume systems. Studies, such as those conducted by Phoenix Controls, demonstrate annual energy savings exceeding $75,000 in large facilities like the University of St. Thomas, achieved by retrofitting Venturi valves with low-pressure designs.
The environmental footprint is further minimized by the valve’s longevity and low maintenance needs. Unlike VAV systems, which require frequent sensor recalibration, Venturi valves’ mechanical simplicity reduces waste from component replacement, aligning with sustainability goals in modern building design.
Historical Development
The Venturi air valve’s roots trace back to Giovanni Battista Venturi’s 18th-century experiments, though its modern incarnation emerged in the 1980s with Phoenix Controls’ introduction of pressure-independent airflow solutions for laboratories. Early HVAC systems relied on orifice plates and dampers, which lacked the precision needed for critical environments. The integration of springs and cones in Venturi valves marked a leap forward, paralleling advancements in fluid dynamics modeling and manufacturing precision.
By the 1990s, widespread adoption in hospitals and research facilities underscored the valve’s reliability. Subsequent innovations—actuated models, digital integration, and material enhancements—expanded its versatility, cementing its status as a cornerstone of airflow control technology.
Technical Specifications and Performance Metrics
Performance hinges on several parameters, including flow accuracy, pressure range, and response dynamics. Factory-calibrated Venturi valves typically achieve airflow accuracy within ±5% across a static pressure range of 0.3 to 3.0 inches of water column (in. w.c.), though some models extend to 8.0 in. w.c. Response time, critical in safety applications, averages less than 100 milliseconds, far surpassing VAV systems.
Table 3: Performance Metrics of Leading Venturi Air Valve Models
Manufacturer | Model | Flow Range (CFM) | Pressure Range (in. w.c.) | Accuracy | Response Time (ms) |
---|---|---|---|---|---|
Phoenix Controls | Standard VV | 50–2,000 | 0.3–3.0 | ±5% | 80 |
Triatek | VAV-1000 | 35–1,500 | 0.6–3.0 | ±5% | 90 |
Antec Controls | Precision Valve | 100–3,000 | 0.3–8.0 | ±3% | 70 |
EB Air Control | Venturi VAV | 50–2,500 | 0.5–5.0 | ±5% | 85 |
Antec Controls’ Precision Valve, with its ±3% accuracy and extended pressure range, exemplifies high-end performance, though at a premium cost. Triatek’s VAV-1000, conversely, targets cost-sensitive applications without sacrificing core functionality.
Limitations and Challenges
Despite its advantages, the Venturi air valve is not without drawbacks. High initial costs, driven by precision manufacturing and calibration, can deter adoption in budget-constrained projects. Its mechanical design, while robust, struggles at extremely low duct pressures (below 0.3 in. w.c.), where alternatives like the AccuValve, with electronic airflow sensing, excel. Maintenance, though minimal, requires periodic inspection of the spring and cone for wear, particularly in dusty environments.
Critics also note the lack of direct airflow measurement, relying instead on positional feedback, which assumes consistent duct conditions. In highly variable systems, this can introduce minor inaccuracies, though rarely beyond acceptable thresholds for critical applications.
Future Directions
Advancements in Venturi air valve technology are poised to address these limitations. Hybrid designs integrating low-power sensors promise direct airflow monitoring without sacrificing mechanical simplicity. Material innovations, such as graphene-based coatings, could enhance durability and reduce weight, while smart actuators with machine learning algorithms may optimize energy use in real time. As building codes tighten energy and safety standards—e.g., ASHRAE 90.1 and 130—Venturi valves will likely evolve to maintain their edge over emerging competitors.
Conclusion
The Venturi air valve represents a pinnacle of airflow control engineering, blending historical fluid dynamics with modern precision. Its ability to deliver consistent, pressure-independent performance in laboratories, healthcare, and industrial settings underscores its enduring relevance. While challenges like cost and low-pressure operation persist, ongoing innovations ensure its adaptability to future demands. For engineers, architects, and facility managers, the Venturi air valve remains a reliable, efficient solution for managing the invisible yet critical currents of air that sustain safe and productive environments.
Maximize Tooling and CNC Metal Spinning Capabilities.
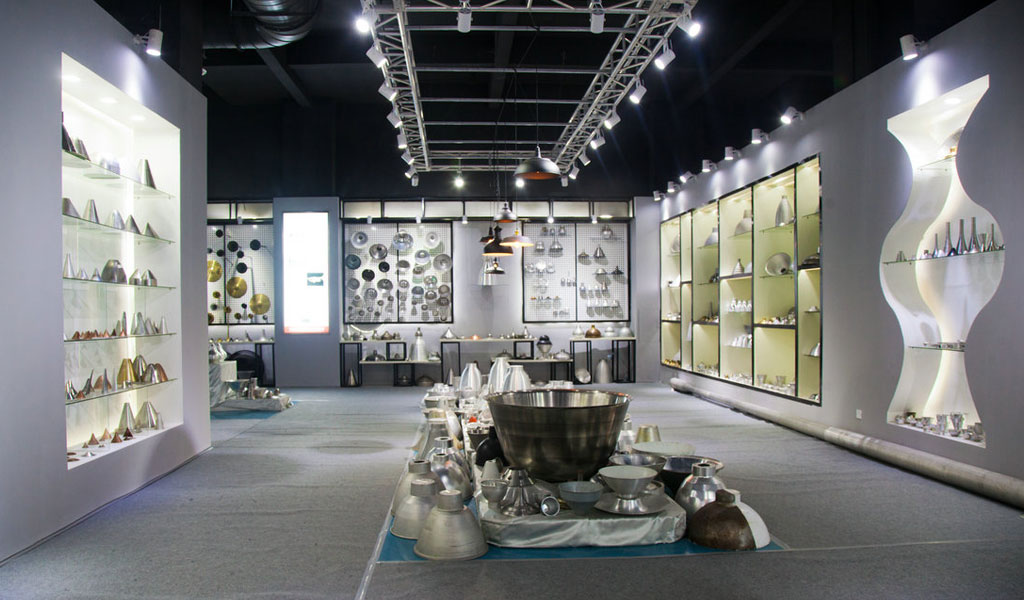
At BE-CU China Metal Spinning company, we make the most of our equipment while monitoring signs of excess wear and stress. In addition, we look into newer, modern equipment and invest in those that can support or increase our manufacturing capabilities. Our team is very mindful of our machines and tools, so we also routinely maintain them to ensure they don’t negatively impact your part’s quality and productivity.
Talk to us today about making a rapid prototype with our CNC metal spinning service. Get a direct quote by chatting with us here or request a free project review.
BE-CU China CNC Metal Spinning service include : CNC Metal Spinning,Metal Spinning Die,Laser Cutting, Tank Heads Spinning,Metal Hemispheres Spinning,Metal Cones Spinning,Metal Dish-Shaped Spinning,Metal Trumpet Spinning,Metal Venturi Spinning,Aluminum Spinning Products,Stainless Steel Spinning Products,Copper Spinning Products,Brass Spinning Products,Steel Spinning Product,Metal Spinnin LED Reflector,Metal Spinning Pressure Vessel,