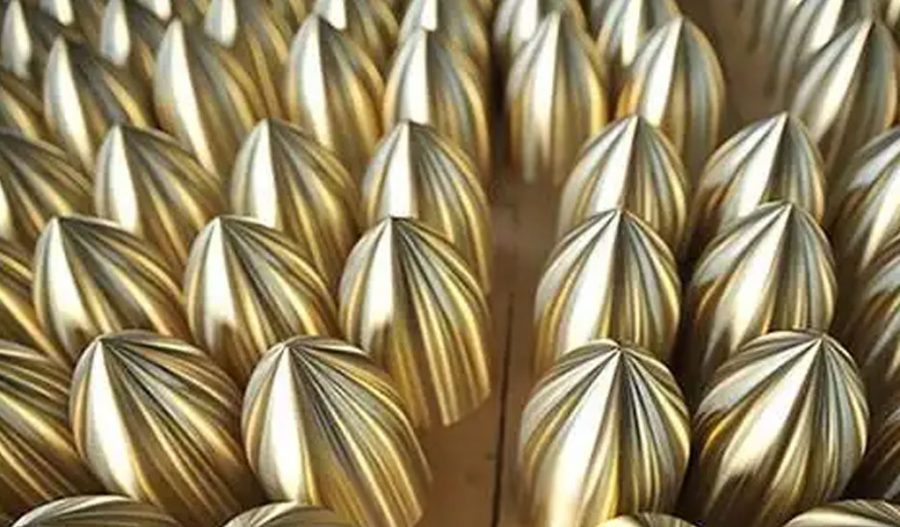
Metal spinning, also known as spin forming or metal turning, is a metalworking process used to create axially symmetric parts by rotating a metal disc or tube at high speed and shaping it over a mandrel. This technique has been employed for centuries, evolving from manual craftsmanship to a sophisticated industrial process aided by modern machinery, such as CNC (Computer Numerical Control) lathes. One of its many applications is the production of custom copper post caps, which serve both functional and aesthetic purposes in architectural and outdoor settings. Copper post caps, typically used to protect wooden fence or deck posts from weathering while enhancing visual appeal, benefit from the ductility and corrosion resistance of copper, making metal spinning an ideal fabrication method. This article explores the scientific principles, technical processes, material properties, and practical considerations involved in using metal spinning to craft custom copper post caps, supplemented by detailed comparative tables.
Fundamentals of Metal Spinning
Metal spinning is rooted in the principles of plastic deformation, where a metal blank—a flat, circular sheet—is subjected to controlled forces that exceed its yield strength but remain below its ultimate tensile strength. The process begins with securing the blank against a mandrel, a pre-shaped form that dictates the final geometry of the part. The mandrel, mounted on a lathe, rotates at speeds typically ranging from 300 to 1,200 RPM, depending on the material and part size. A forming tool, historically manipulated by hand but now often controlled by CNC systems, applies pressure to the rotating blank, gradually conforming it to the mandrel’s shape.
The mechanics of metal spinning involve both shear and tensile stresses. As the tool presses against the blank, the metal flows outward and downward, thinning slightly in some areas while retaining its integrity. This differs from other metalworking methods like stamping or forging, which often involve cutting or compressive forces alone. The absence of material removal in spinning makes it a cost-effective and waste-minimizing technique, particularly suitable for producing seamless, hollow components like post caps.
Copper, a soft, malleable, and ductile metal, is especially amenable to spinning. With a face-centered cubic (FCC) crystal structure, copper exhibits excellent formability, allowing it to stretch and bend without fracturing. Its yield strength is approximately 33 MPa in its annealed state, while its ultimate tensile strength can reach 210 MPa, depending on work hardening during the process. These properties enable copper to be spun into intricate shapes, such as the conical or pyramidal forms common in post caps, without requiring excessive force or frequent annealing.
Copper as a Material for Post Caps
Copper’s selection for post caps is driven by its unique combination of physical, chemical, and aesthetic properties. Chemically, copper (Cu, atomic number 29) is a transition metal with a high resistance to corrosion, owing to the formation of a protective patina—primarily copper carbonate (Cu₂CO₃)—when exposed to air and moisture. This patina, often appearing as a greenish layer, not only prevents further degradation but also adds a distinctive aged appearance prized in architectural design. Physically, copper has a density of 8.96 g/cm³ and a melting point of 1,085°C, making it stable under typical outdoor conditions. Its thermal conductivity (401 W/m·K) and electrical conductivity (5.96 × 10⁷ S/m) are exceptional, though these are less relevant to post caps than its mechanical properties.
For post caps, copper’s durability is a key advantage. Wooden posts, commonly made from cedar, pine, or pressure-treated lumber, are vulnerable to water infiltration at their exposed tops, leading to rot and structural failure over time. A well-fitted copper cap acts as a barrier, shedding water and extending the post’s lifespan. Aesthetically, copper transitions from a bright, reddish-orange hue when new to a rich brown and eventually the iconic verdigris patina, offering a dynamic visual evolution that complements rustic or classical settings.
The Metal Spinning Process for Copper Post Caps
Creating custom copper post caps via metal spinning involves several stages: design, material selection, blank preparation, spinning, finishing, and installation. Each step requires precision to ensure the final product meets both functional and aesthetic requirements.
Design and Mandrel Fabrication
The process begins with designing the post cap, which typically takes the form of a pyramid, cone, or flat-topped cap with folded edges. Dimensions are determined by the post size—common standards include 4×4 in (101.6 × 101.6 mm), 6×6 in (152.4 × 152.4 mm), or custom sizes. The design must account for a slight overhang (e.g., 0.5–1 inch or 12.7–25.4 mm) to ensure water runoff and a secure fit.
The mandrel, a critical component, is machined from steel, aluminum, or hardwood, depending on production volume and precision needs. For a pyramidal post cap, the mandrel is a truncated pyramid with a base matching the post’s cross-section and a tapered top. The mandrel’s surface is polished to minimize friction and prevent scratching the copper. CNC machining ensures dimensional accuracy, with tolerances as tight as ±0.01 mm for high-end applications.
Material Selection and Blank Preparation
Copper sheet is selected based on thickness, typically ranging from 16 gauge (1.29 mm) to 20 gauge (0.91 mm) for post caps. Thicker sheets (e.g., 16 gauge) provide greater durability but require more force to spin, while thinner sheets (e.g., 20 gauge) are easier to form but less robust. The copper should be in an annealed state—heated to approximately 400–600°C and cooled slowly—to maximize ductility and reduce residual stresses.
The blank is cut as a circular disc using shears or a laser cutter. Its diameter is calculated based on the mandrel’s geometry and the desired overhang. For a 4×4 post cap with a 0.5-inch overhang and a 2-inch height, the blank diameter can be approximated using the formula for the surface area of a frustum plus excess material:
D=4×(s×(R1+R2)+R12+R22) D = \sqrt{4 \times (s \times (R_1 + R_2) + R_1^2 + R_2^2)} D=4×(s×(R1+R2)+R12+R22)
Where:
- D D D = blank diameter
- s s s = slant height (derived from Pythagorean theorem: h2+(R1−R2)2\sqrt{h^2 + (R_1 – R_2)^2}h2+(R1−R2)2)
- R1 R_1 R1 = base radius (e.g., 2.25 in, including overhang)
- R2 R_2 R2 = top radius (e.g., smaller apex dimension)
- h h h = height (e.g., 2 in)
For simplicity, empirical adjustments often increase the diameter by 20–30% beyond theoretical values to account for material flow.
Spinning the Copper Blank
The blank is clamped between the mandrel and a tailstock on a lathe. Rotation begins at a moderate speed (e.g., 500 RPM), and a forming tool—typically a steel roller or spoon-shaped implement—is applied with controlled pressure. The tool follows a path from the center outward, gradually shaping the copper over the mandrel. For a pyramidal cap, multiple passes are made, each deepening the form and refining the edges.
Copper’s work-hardening behavior necessitates monitoring during spinning. As the metal deforms, its hardness increases (e.g., from 40 HV to 80 HV on the Vickers scale), potentially causing cracking if overworked. If resistance becomes excessive, annealing is performed by heating the partially formed cap to 400°C and quenching it in water to restore ductility. Modern CNC spinning machines automate this process, using programmed tool paths to ensure uniformity and reduce operator fatigue.
Finishing and Trimming
Once spun, the cap’s edges are trimmed using a lathe-mounted cutting tool or tin snips to remove excess material and achieve a clean, uniform lip. Surface finishing options include polishing to retain copper’s luster, applying a clear coat to prevent patina formation, or leaving it untreated for natural aging. Burrs are removed with abrasive pads or a deburring tool to ensure safety and fit.
Installation
The finished cap is secured to the post using adhesives (e.g., construction-grade silicone or epoxy) or copper nails. The fit should be snug, with the overhang directing water away from the post’s end grain. Proper installation enhances both protection and longevity.
Scientific Principles Underpinning Metal Spinning
The efficacy of metal spinning for copper post caps rests on several scientific principles:
- Plastic Deformation: Copper’s FCC structure allows dislocations to move easily under shear stress, enabling smooth flow over the mandrel. The process operates within the metal’s strain-hardening regime, balancing formability and strength.
- Friction and Lubrication: Friction between the blank and mandrel affects material flow. Lubricants like water-soluble oils or waxes reduce heat and wear, improving surface quality. Coefficients of friction typically range from 0.1 to 0.3, depending on lubrication.
- Stress-Strain Behavior: Copper’s stress-strain curve shows a distinct elastic region followed by significant plastic deformation. Spinning exploits this plasticity, with strains often exceeding 50% in deep forms.
- Heat Generation: High-speed rotation and tool pressure generate heat, softening the copper (a thermally activated process) but also risking localized overheating. Controlled speeds and annealing mitigate this.
Comparative Analysis of Fabrication Methods
To highlight metal spinning’s advantages, Table 1 compares it with alternative methods for producing copper post caps: stamping, casting, and manual forming.
Method | Material Thickness (mm) | Tooling Cost (USD) | Production Time (min/part) | Waste (%) | Seamlessness | Complexity Limit | Corrosion Resistance |
---|---|---|---|---|---|---|---|
Metal Spinning | 0.91–1.29 | 100–500 | 5–15 | 5–10 | Yes | Moderate-High | High (due to copper) |
Stamping | 0.5–2.0 | 1,000–5,000 | 1–5 | 20–30 | No (welded seams) | High | High (due to copper) |
Casting | 2.0–5.0 | 2,000–10,000 | 10–30 (plus cooling) | 10–15 | Yes | High | High (due to copper) |
Manual Forming | 0.5–1.5 | 50–200 | 30–60 | 10–20 | No (folded edges) | Low | High (due to copper) |
Analysis: Metal spinning offers a balance of low tooling costs, moderate production speed, and minimal waste, making it ideal for small to medium runs of custom post caps. Stamping excels in high-volume production but requires expensive dies, while casting suits thicker, complex parts but is cost-prohibitive for small batches. Manual forming is labor-intensive and less precise, limiting its scalability.
Material Properties Comparison
Table 2 compares copper with alternative metals for post caps, such as aluminum and stainless steel, focusing on properties relevant to spinning and outdoor use.
Material | Density (g/cm³) | Yield Strength (MPa) | Ductility (% Elongation) | Corrosion Resistance | Thermal Conductivity (W/m·K) | Cost (USD/kg) |
---|---|---|---|---|---|---|
Copper | 8.96 | 33 (annealed) | 50–60 | High (patina forms) | 401 | 8–10 |
Aluminum | 2.70 | 35–100 | 20–40 | High (oxide layer) | 237 | 2–3 |
Stainless Steel | 7.85 | 200–300 | 40–50 | Very High | 16 | 3–5 |
Analysis: Copper’s superior ductility and natural corrosion resistance make it a top choice for spinning and outdoor applications, despite its higher cost and density. Aluminum is lighter and cheaper but less durable, while stainless steel offers strength but is harder to spin due to its higher yield strength.
Practical Considerations and Optimization
Several factors optimize the spinning of copper post caps:
- Tooling: Hardened steel tools with polished surfaces minimize wear and improve finish. Roller tools reduce localized stress compared to point tools.
- Speed: Optimal RPM varies with blank size (e.g., 600–800 RPM for 6-inch blanks). Excessive speed risks tearing; too slow reduces efficiency.
- Annealing Frequency: For deep spins (height > diameter), anneal every 30–50% of depth to prevent cracking.
- Lubrication: Water-based lubricants lower friction without compromising copper’s surface chemistry.
Applications and Benefits
Custom copper post caps produced via metal spinning are widely used in residential fencing, decking, and marine environments (e.g., pier pilings). Benefits include:
- Durability: Seamless construction and copper’s corrosion resistance ensure decades of service.
- Customization: Spinning accommodates unique sizes and shapes without costly retooling.
- Sustainability: Minimal waste aligns with eco-friendly manufacturing trends.
Conclusion
Metal spinning is a scientifically grounded, versatile method for crafting custom copper post caps, leveraging copper’s ductility and corrosion resistance to produce durable, aesthetically pleasing components. By understanding the interplay of material properties, process mechanics, and practical techniques, manufacturers can optimize production for both small-scale artisanal work and industrial applications. Comparative tables underscore spinning’s advantages over alternatives, positioning it as a preferred choice for this niche. As technology advances, integration of CNC and automation will further enhance precision and scalability, solidifying metal spinning’s role in modern metalworking.
Maximize Tooling and CNC Metal Spinning Capabilities.
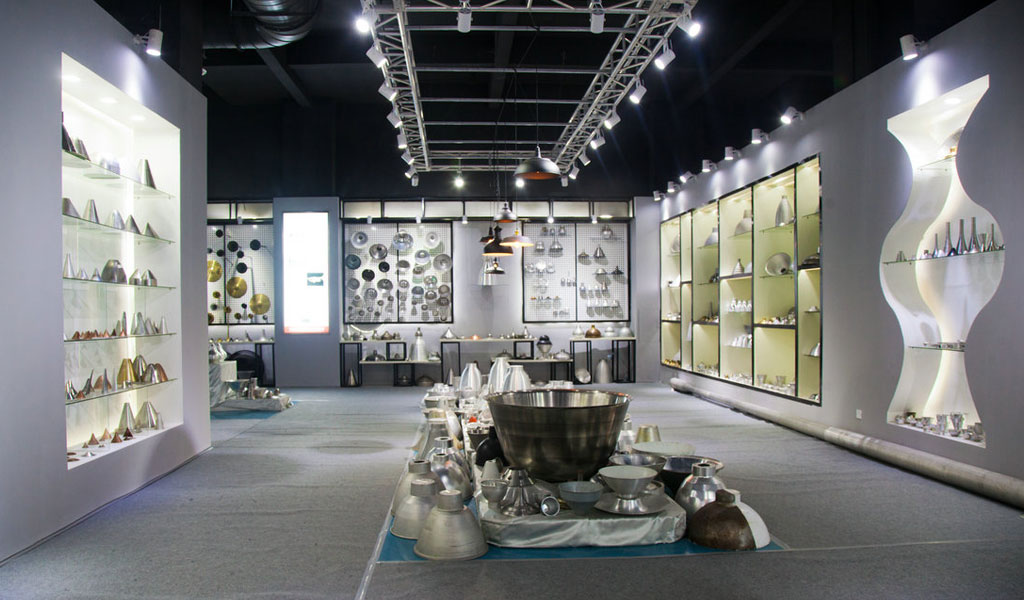
At BE-CU China Metal Spinning company, we make the most of our equipment while monitoring signs of excess wear and stress. In addition, we look into newer, modern equipment and invest in those that can support or increase our manufacturing capabilities. Our team is very mindful of our machines and tools, so we also routinely maintain them to ensure they don’t negatively impact your part’s quality and productivity.
Talk to us today about making a rapid prototype with our CNC metal spinning service. Get a direct quote by chatting with us here or request a free project review.
BE-CU China CNC Metal Spinning service include : CNC Metal Spinning,Metal Spinning Die,Laser Cutting, Tank Heads Spinning,Metal Hemispheres Spinning,Metal Cones Spinning,Metal Dish-Shaped Spinning,Metal Trumpet Spinning,Metal Venturi Spinning,Aluminum Spinning Products,Stainless Steel Spinning Products,Copper Spinning Products,Brass Spinning Products,Steel Spinning Product,Metal Spinnin LED Reflector,Metal Spinning Pressure Vessel,