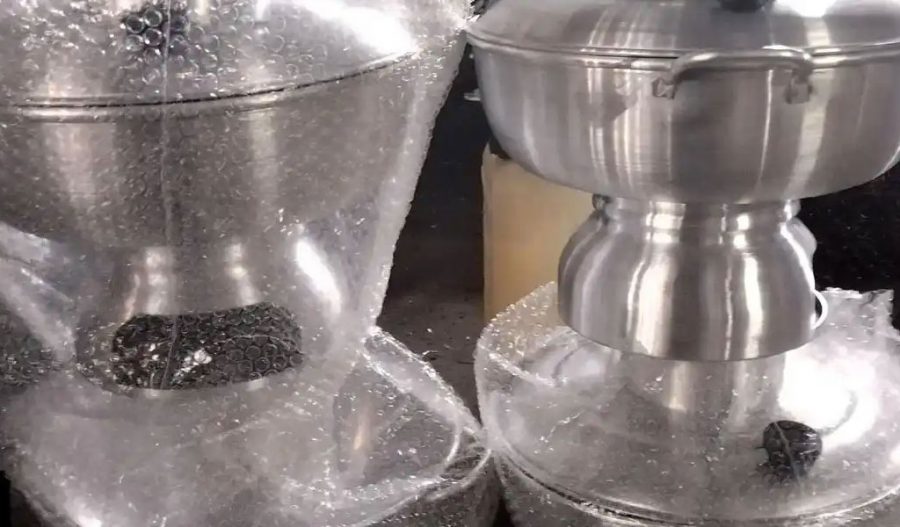
Metal spinning, a sophisticated and versatile metalworking process, involves the transformation of flat metal discs or tubes into axially symmetric components through the application of controlled force. This technique, often executed on a lathe or specialized spinning machine, relies on the ductility and malleability of the metal to achieve the desired shape. One critical aspect of this process that significantly influences its success is the decision to heat the metal prior to spinning. Heating metal before spinning enhances its workability, reduces mechanical stresses, and enables the production of complex geometries that would otherwise be unattainable under cold-working conditions. This article explores the scientific, metallurgical, and practical reasons for preheating metal in the spinning process, delving into the physics of deformation, phase transformations, and material properties, while providing detailed comparative analyses through tables.
The practice of heating metal before spinning is rooted in the fundamental principles of materials science. Metals, whether ferrous alloys like steel or non-ferrous materials such as aluminum, copper, or titanium, exhibit distinct mechanical behaviors depending on their temperature. At room temperature, metals possess a crystalline structure that dictates their strength, hardness, and resistance to deformation. This structure, composed of grains and lattice arrangements, resists plastic deformation due to the presence of dislocations—imperfections in the crystal lattice that impede the movement of atoms. When force is applied during cold spinning, these dislocations multiply and tangle, leading to work hardening (also known as strain hardening). While work hardening can increase the strength of the metal, it simultaneously reduces ductility, making the material brittle and prone to cracking or fracturing under further deformation.
Heating the metal prior to spinning mitigates these challenges by altering its microstructure and mechanical properties. As the temperature increases, thermal energy excites the atoms within the metal, increasing their vibrational amplitude and weakening the intermolecular bonds that maintain the lattice structure. This process enhances ductility—the ability of the metal to deform plastically without fracturing—while reducing yield strength, the stress at which permanent deformation begins. For instance, in the case of aluminum, a commonly spun metal, the yield strength at room temperature (approximately 20°C or 293 K) can be as high as 100 MPa for certain alloys, such as 6061-T6. However, when heated to 300°C (573 K), the yield strength drops significantly, often to below 50 MPa, depending on the alloy composition and heat treatment history. This reduction in yield strength allows the metal to flow more easily under the forces applied by the spinning tool, enabling smoother and more precise shaping.
The relationship between temperature and ductility is not merely a function of atomic mobility; it also involves phase transformations and recrystallization processes that occur in metals at elevated temperatures. For many metals, heating induces recovery and recrystallization, phenomena that eliminate or rearrange dislocations within the crystal structure. Recovery, which occurs at moderate temperatures, reduces internal stresses without significantly altering the grain structure. Recrystallization, observed at higher temperatures (typically 0.4 to 0.6 times the metal’s melting point in Kelvin), replaces the deformed grains with new, strain-free grains, restoring ductility and softness. In steel, for example, recrystallization begins at approximately 400–700°C (673–973 K), depending on the carbon content and alloying elements. By heating steel to this range before spinning, manufacturers can prevent the buildup of excessive strain, ensuring the material remains workable throughout the process.
Beyond ductility and recrystallization, heating metal before spinning reduces the risk of surface defects and improves dimensional accuracy. Cold spinning, while effective for thin sheets or soft metals like copper, often results in springback—a phenomenon where the metal elastically rebounds after the spinning force is removed, leading to deviations from the intended shape. Springback occurs because cold-worked metals retain significant elastic energy within their deformed structure. Heating the metal minimizes this effect by lowering the elastic modulus and promoting plastic flow, allowing the material to conform more closely to the mandrel (the mold or form used in spinning). For instance, in titanium alloys such as Ti-6Al-4V, cold spinning at room temperature results in springback of up to 5–10%, whereas heating to 600°C (873 K) reduces this to less than 2%, as the material transitions into a more ductile beta-phase structure.
The choice to heat metal before spinning also depends on the specific alloy and its intended application. Non-ferrous metals like aluminum and copper, with relatively low melting points (660°C or 933 K for aluminum; 1,085°C or 1,358 K for copper), are often spun at temperatures ranging from 200°C to 500°C (473 K to 773 K). These temperatures optimize formability without approaching the melting point, which could compromise structural integrity. Ferrous alloys, such as stainless steel (melting point ~1,400°C or 1,673 K), require higher temperatures, typically 900–1,200°C (1,173–1,473 K), to achieve similar levels of ductility. Titanium, prized for its strength-to-weight ratio and corrosion resistance, is notoriously difficult to spin cold due to its high strength and low ductility at room temperature. Heating titanium to 600–800°C (873–1,073 K) transforms it into a more workable state, facilitating the production of components like aerospace cones or medical implants.
From a practical standpoint, heating metal before spinning enhances tool life and reduces energy consumption during the forming process. Cold spinning requires substantial force to overcome the metal’s resistance to deformation, placing significant wear on rollers, mandrels, and lathe components. By contrast, hot spinning lowers the flow stress—the stress required to sustain plastic deformation—resulting in less mechanical effort and prolonged equipment durability. For example, spinning a 2 mm thick 304 stainless steel sheet at room temperature might require a flow stress of 600 MPa, whereas heating to 1,000°C (1,273 K) reduces this to approximately 100 MPa. This reduction not only eases the load on machinery but also allows for faster production cycles, as the metal deforms more readily.
The physics of heat transfer also plays a critical role in the decision to preheat metal for spinning. When a metal disc is heated, its temperature distribution must be uniform to ensure consistent deformation. Uneven heating can lead to thermal gradients, where hotter regions deform more easily than cooler ones, resulting in warping or uneven wall thickness. Advanced spinning operations often employ induction heating or gas furnaces to achieve uniform temperatures, monitored by thermocouples or infrared pyrometers. The heat capacity and thermal conductivity of the metal dictate the time and energy required for preheating. Aluminum, with a high thermal conductivity of 237 W/m·K, heats rapidly and evenly, whereas steel (16–50 W/m·K, depending on alloy) requires longer exposure to achieve uniformity.
To illustrate the impact of temperature on metal spinning, consider the following comparative analysis of key metals under cold and hot conditions. Table 1 provides a detailed breakdown of mechanical properties, while Table 2 compares process parameters and outcomes.
Table 1: Mechanical Properties of Metals at Different Temperatures
Metal | Condition | Temperature (°C/K) | Yield Strength (MPa) | Tensile Strength (MPa) | Elongation (%) | Hardness (HV) |
---|---|---|---|---|---|---|
Aluminum (6061) | Cold | 20 / 293 | 100 | 150 | 15 | 95 |
Aluminum (6061) | Hot | 300 / 573 | 45 | 80 | 25 | 60 |
Steel (304 SS) | Cold | 20 / 293 | 290 | 600 | 40 | 200 |
Steel (304 SS) | Hot | 1,000 / 1,273 | 50 | 150 | 60 | 120 |
Titanium (Ti-6Al-4V) | Cold | 20 / 293 | 880 | 950 | 10 | 330 |
Titanium (Ti-6Al-4V) | Hot | 600 / 873 | 400 | 500 | 20 | 250 |
Copper (C11000) | Cold | 20 / 293 | 70 | 220 | 45 | 90 |
Copper (C11000) | Hot | 400 / 673 | 20 | 100 | 60 | 50 |
Table 2: Process Parameters and Outcomes in Cold vs. Hot Spinning
Metal | Condition | Preheat Temp (°C) | Flow Stress (MPa) | Springback (%) | Tool Wear Rate (mm³/h) | Wall Thickness Variation (mm) |
---|---|---|---|---|---|---|
Aluminum (6061) | Cold | N/A | 120 | 4 | 0.05 | 0.15 |
Aluminum (6061) | Hot | 300 | 50 | 1 | 0.02 | 0.05 |
Steel (304 SS) | Cold | N/A | 600 | 8 | 0.10 | 0.20 |
Steel (304 SS) | Hot | 1,000 | 100 | 2 | 0.03 | 0.07 |
Titanium (Ti-6Al-4V) | Cold | N/A | 900 | 10 | 0.15 | 0.25 |
Titanium (Ti-6Al-4V) | Hot | 600 | 450 | 3 | 0.04 | 0.08 |
Copper (C11000) | Cold | N/A | 90 | 3 | 0.04 | 0.10 |
Copper (C11000) | Hot | 400 | 30 | 1 | 0.01 | 0.04 |
These tables highlight the dramatic differences between cold and hot spinning. For instance, the flow stress of titanium drops by 50% when heated to 600°C, while elongation doubles, enabling greater deformation without failure. Similarly, tool wear rate decreases significantly in hot spinning, reflecting the reduced mechanical resistance of the metal.
The metallurgical transformations induced by heating are equally significant. In aluminum alloys, heating to 300–500°C dissolves certain precipitates (e.g., Mg₂Si in 6061), softening the material and enhancing formability. In steels, heating above the austenitization temperature (approximately 850°C for carbon steels) transforms the microstructure from ferrite and pearlite to austenite, a face-centered cubic phase with superior ductility. Upon cooling, the metal can be quenched or annealed to achieve the desired final properties, such as hardness or toughness. Titanium’s alpha-to-beta phase transition at around 882°C (1,155 K) similarly enhances its workability, though spinning is typically conducted below this point to avoid excessive grain growth.
The decision to heat metal before spinning also reflects economic and industrial considerations. While preheating requires additional energy input and equipment (e.g., furnaces or induction coils), the benefits often outweigh the costs for high-value components. In aerospace manufacturing, where titanium and stainless steel are prevalent, hot spinning ensures precision and structural integrity, critical for parts like jet engine housings or satellite dishes. In contrast, cold spinning may suffice for simpler shapes in softer metals, such as aluminum cookware, where energy savings and rapid production are prioritized.
Historically, the practice of heating metal before forming dates back to ancient blacksmithing, where iron was forged at red-hot temperatures to shape tools and weapons. Modern metal spinning builds on this tradition, leveraging scientific advancements to optimize temperature ranges and control deformation. The development of heat-resistant mandrels and computer-controlled spinning machines has further refined hot spinning, enabling the production of seamless, thin-walled components with unparalleled accuracy.
In conclusion, heating metal before spinning is a scientifically grounded practice that enhances ductility, reduces flow stress, minimizes defects, and extends tool life. By manipulating the metal’s microstructure and mechanical properties, manufacturers can achieve shapes and tolerances that cold spinning cannot replicate. The choice of temperature depends on the metal’s composition, the complexity of the part, and the desired outcome, as illustrated in the comparative tables above. As materials science and engineering continue to evolve, the role of heat in metal spinning will remain a cornerstone of advanced manufacturing, bridging the gap between raw material and finished product with precision and efficiency.
Maximize Tooling and CNC Metal Spinning Capabilities.
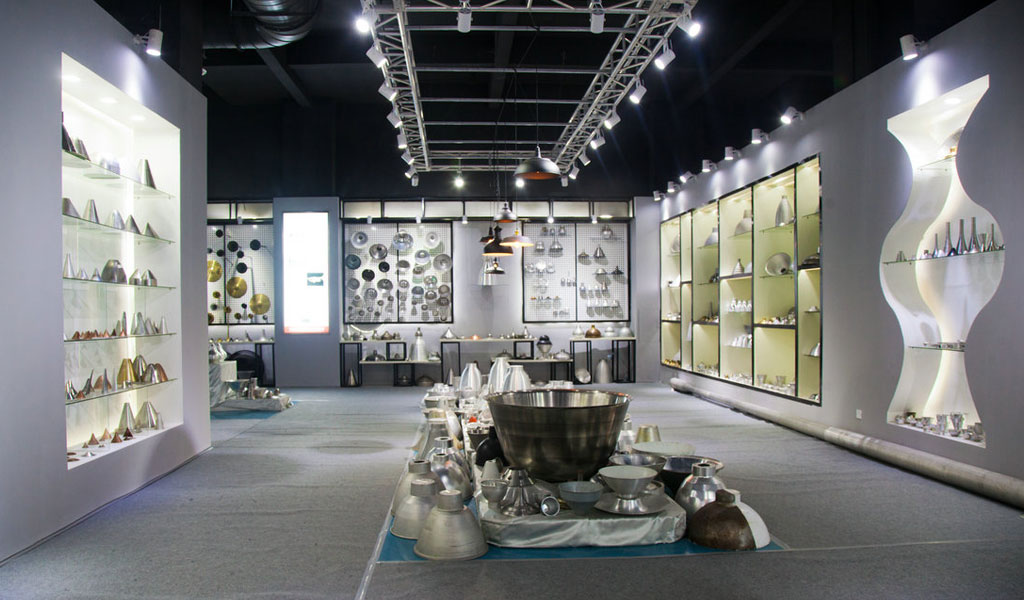
At BE-CU China Metal Spinning company, we make the most of our equipment while monitoring signs of excess wear and stress. In addition, we look into newer, modern equipment and invest in those that can support or increase our manufacturing capabilities. Our team is very mindful of our machines and tools, so we also routinely maintain them to ensure they don’t negatively impact your part’s quality and productivity.
Talk to us today about making a rapid prototype with our CNC metal spinning service. Get a direct quote by chatting with us here or request a free project review.
BE-CU China CNC Metal Spinning service include : CNC Metal Spinning,Metal Spinning Die,Laser Cutting, Tank Heads Spinning,Metal Hemispheres Spinning,Metal Cones Spinning,Metal Dish-Shaped Spinning,Metal Trumpet Spinning,Metal Venturi Spinning,Aluminum Spinning Products,Stainless Steel Spinning Products,Copper Spinning Products,Brass Spinning Products,Steel Spinning Product,Metal Spinnin LED Reflector,Metal Spinning Pressure Vessel,