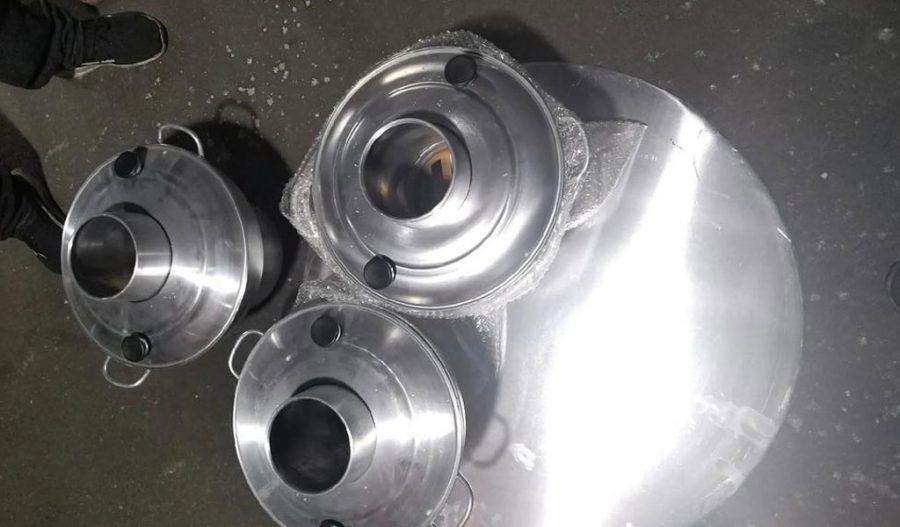
Sheet metal spinning, also known as metal spinning or spin forming, is a metalworking process by which a flat metal disc or tube is rotated at high speed and formed into an axially symmetric part, such as a bowl, using a combination of rotational force and pressure applied via specialized tools. This technique, rooted in ancient craftsmanship yet refined through modern engineering, allows for the creation of seamless, durable, and aesthetically pleasing sheet metal bowls with applications ranging from industrial components to decorative household items. The process is distinct from other forming methods, such as deep drawing or stamping, due to its reliance on incremental deformation and its ability to produce complex geometries with minimal tooling costs. This article provides a comprehensive exploration of the science, techniques, tools, materials, and practical considerations involved in spinning sheet metal bowls, offering a detailed guide suitable for both novice and experienced practitioners.
The origins of metal spinning can be traced back thousands of years, with evidence of spun metal objects appearing in ancient Egyptian, Greek, and Chinese artifacts. These early examples were likely produced using rudimentary lathes powered by hand or foot, with artisans employing wooden or bone tools to shape soft metals like copper or gold. The Industrial Revolution marked a significant turning point, introducing mechanized lathes and stronger alloys, which expanded the scope and precision of the craft. Today, metal spinning is a sophisticated process supported by computer numerical control (CNC) technology, yet it retains its fundamental principles: a rotating workpiece, a forming tool, and skilled manipulation to achieve the desired shape.
At its core, metal spinning involves mounting a circular metal blank—typically a disc cut from a sheet—onto a spinning lathe. The lathe rotates the blank at speeds that can range from 300 to 1,200 revolutions per minute (RPM), depending on the material, thickness, and diameter of the blank, as well as the desired bowl dimensions. A forming tool, often a roller or a pointed stick made of hardened steel, is then pressed against the spinning blank, gradually shaping it over a mandrel—a pre-shaped form that dictates the final contour of the bowl. The mandrel, typically machined from steel, aluminum, or wood, serves as a mold around which the metal is stretched and compressed. The interplay between rotational speed, tool pressure, and material properties governs the success of the spinning process, making it both an art and a science.
The choice of material is a critical factor in spinning sheet metal bowls, as it influences the ease of forming, the quality of the finished product, and the durability of the bowl. Common materials include aluminum, stainless steel, copper, brass, and mild steel, each with distinct mechanical properties that affect their behavior under spinning forces. Aluminum, for instance, is favored for its ductility and low density, allowing it to be spun into lightweight bowls with smooth finishes. Stainless steel, while more challenging due to its higher strength and tendency to work-harden, offers superior corrosion resistance and structural integrity, making it ideal for functional bowls used in kitchens or industrial settings. Copper and brass, prized for their malleability and attractive patinas, are often chosen for decorative or artisanal pieces. The thickness of the sheet metal, typically ranging from 0.5 mm to 3 mm for bowl spinning, also plays a role, with thinner sheets being easier to form but more prone to wrinkling or tearing, while thicker sheets require greater force and skill to manipulate.
The physics of metal spinning is governed by principles of plastic deformation, where the metal is stretched beyond its elastic limit but below its fracture point. As the blank spins, the forming tool applies localized pressure, causing the metal to flow and conform to the mandrel’s shape. This incremental deformation distinguishes spinning from other processes like forging, where the entire workpiece is shaped simultaneously. The strain rate—the speed at which the metal is deformed—must be carefully controlled to avoid defects such as cracking, thinning, or buckling. For a typical bowl, the outer edge of the blank experiences tensile stress as it is drawn inward, while the central region near the mandrel undergoes compressive stress. The balance between these forces determines the uniformity of the bowl’s wall thickness, which ideally remains consistent but may thin slightly toward the rim due to material elongation.
To illustrate the material considerations, Table 1 provides a detailed comparison of common metals used in spinning sheet metal bowls, including their mechanical properties and suitability for various applications.
Table 1: Comparison of Materials for Sheet Metal Spinning
Material | Density (g/cm³) | Yield Strength (MPa) | Elongation (%) | Corrosion Resistance | Ease of Spinning | Typical Thickness (mm) | Applications |
---|---|---|---|---|---|---|---|
Aluminum (1100) | 2.71 | 34 | 35-45 | High | Easy | 0.5-2.0 | Decorative bowls, lightweight containers |
Stainless Steel (304) | 8.00 | 215 | 40-60 | Excellent | Moderate | 0.8-2.5 | Kitchenware, industrial vessels |
Copper (C110) | 8.96 | 70 | 40-50 | Moderate | Easy | 0.5-1.5 | Artisanal bowls, decorative items |
Brass (C260) | 8.53 | 120 | 30-40 | Moderate | Easy | 0.5-2.0 | Ornamental bowls, fittings |
Mild Steel | 7.85 | 250 | 20-30 | Low | Moderate | 1.0-3.0 | Structural bowls, utility items |
The spinning process begins with preparing the blank, which involves cutting a circular disc from a metal sheet using a shear, laser cutter, or water jet. The diameter of the blank is determined by the desired size of the bowl, factoring in the material’s shrinkage and the depth of the form. A general rule of thumb is that the blank diameter should be approximately 1.5 to 2 times the diameter of the finished bowl’s rim, though this varies with the depth and curvature of the design. For example, a bowl with a 20 cm rim diameter and 10 cm depth might require a blank of 30-40 cm in diameter, depending on the material’s ductility and the mandrel’s shape. The blank is then centered on the lathe’s headstock, secured against the mandrel with a tailstock or pressure pad, and lubricated to reduce friction between the metal and the tool. Common lubricants include wax, oil, or soap-based compounds, selected based on the metal type and spinning speed.
Once the blank is mounted, the lathe is set in motion, and the operator begins the forming process by applying the tool to the outer edge of the spinning disc. The tool’s path follows a series of controlled passes, gradually pushing the metal toward the mandrel’s center. For a bowl, the initial passes create a shallow cone or flare, which is then deepened with subsequent strokes until the metal fully contacts the mandrel. The angle and pressure of the tool must be adjusted dynamically to prevent overstressing the material, which could lead to wrinkles—unwanted folds in the metal—or tears. Wrinkling is more common in thinner sheets or softer metals like aluminum, while tearing occurs in brittle or overworked materials. Skilled spinners mitigate these issues by varying the tool’s angle, reducing the feed rate, or annealing the metal mid-process to relieve internal stresses.
Annealing, a heat treatment process, is often employed when spinning harder metals like stainless steel or when the workpiece begins to resist deformation. The metal is heated to a specific temperature—typically 300-400°C for aluminum or 900-1,100°C for stainless steel—then cooled slowly to restore its ductility. This step is particularly useful for deep bowls, where multiple forming stages are required, as it prevents the material from becoming too brittle to shape. The frequency of annealing depends on the material’s work-hardening rate and the complexity of the bowl’s geometry, with some projects requiring two or three cycles to complete.
The choice of spinning tools further influences the process’s outcome. Traditional hand spinning uses long-handled tools with rounded or pointed tips, allowing the operator to apply precise pressure across the blank. Modern setups often incorporate roller tools, which consist of a steel wheel mounted on a handle or CNC arm, providing smoother contact and reducing the risk of tool marks on the metal surface. Table 2 compares the characteristics of common spinning tools, highlighting their advantages and limitations.
Table 2: Comparison of Spinning Tools
Tool Type | Material | Tip Shape | Application | Advantages | Limitations |
---|---|---|---|---|---|
Hand Stick | Hardened Steel | Pointed or Rounded | General forming | High precision, low cost | Requires skill, labor-intensive |
Roller Tool | Steel or Carbide | Circular Wheel | Finishing, deep forming | Smooth finish, consistent pressure | Higher cost, less maneuverability |
Wooden Stick | Hardwood | Rounded | Soft metals, initial shaping | Inexpensive, gentle on surface | Wears quickly, limited durability |
CNC Roller | Steel | Variable | Automated spinning | High repeatability, speed | Expensive, complex setup |
For bowls with intricate details, such as fluted rims or embossed patterns, additional techniques like trimming and beading may be applied post-spinning. Trimming removes excess material from the bowl’s edge using a lathe-mounted cutting tool, ensuring a clean, uniform rim. Beading involves rolling the edge inward or outward with a specialized tool, enhancing both the bowl’s strength and its visual appeal. These finishing steps require careful alignment to maintain the bowl’s symmetry, often guided by calipers or templates.
The advent of CNC spinning has revolutionized the production of sheet metal bowls, enabling greater precision and scalability. In a CNC setup, the lathe and tool movements are programmed via computer software, allowing for consistent replication of complex shapes with minimal human intervention. The blank is still mounted and spun as in manual spinning, but the tool path is controlled by servo motors, following a digital model of the bowl. This technology is particularly advantageous for large-scale production or when tight tolerances—such as ±0.1 mm—are required. However, CNC spinning demands significant upfront investment in equipment and programming expertise, making it less accessible for small workshops or hobbyists.
Despite its advantages, metal spinning presents several challenges that must be addressed to achieve high-quality bowls. One common issue is springback, where the metal attempts to revert to its original shape after forming, resulting in slight deviations from the mandrel’s contour. Springback is more pronounced in high-strength materials like stainless steel and can be minimized by over-forming the metal slightly beyond the desired shape or by applying heat during the process. Another challenge is surface finish, as the spinning tool can leave marks or scratches on the metal, particularly if the lubricant is insufficient or the tool is worn. Polishing or sanding the bowl after spinning can restore a smooth, reflective surface, though this adds time and cost to the workflow.
The design of the mandrel is equally critical, as it directly determines the bowl’s final shape. Simple bowls may use a single-piece mandrel machined from a solid block, while complex or multi-part bowls might require segmented mandrels that can be disassembled to release the finished piece. The mandrel’s surface must be smooth and free of imperfections, as any flaws will transfer to the metal during spinning. For shallow bowls, a flat or slightly curved mandrel suffices, but deeper forms demand a more pronounced taper to guide the metal inward without excessive thinning. The mandrel material also matters—steel offers durability for high-volume production, while wood or MDF (medium-density fiberboard) is suitable for prototyping or softer metals due to its lower cost and ease of machining.
To provide a practical example, consider the process of spinning a 25 cm diameter aluminum bowl with a depth of 12 cm. The blank, a 40 cm diameter disc of 1 mm thick 1100 aluminum, is cut and mounted on a lathe spinning at 600 RPM. A wooden mandrel, shaped with a smooth, parabolic curve, is secured to the headstock, and the blank is clamped against it with a tailstock pad. Using a hand-held roller tool lubricated with beeswax, the operator begins at the outer edge, applying steady pressure to form a shallow flare over three passes. The tool angle is adjusted from 45° to 30° as the metal deepens, with each pass overlapping the previous one by 1-2 cm to ensure even deformation. After 10-15 minutes, the aluminum fully conforms to the mandrel, and the bowl is trimmed to a 25 cm rim using a parting tool. The finished piece is then polished with a fine abrasive to remove minor tool marks, yielding a lightweight, seamless bowl suitable for decorative use.
The versatility of metal spinning extends beyond simple bowls to include variations like hemispherical mixing bowls, flanged serving dishes, or even multi-tiered designs for specialized applications. Each variation requires adjustments to the blank size, tool selection, and spinning technique, as well as consideration of the end-use requirements, such as load-bearing capacity or thermal conductivity. For instance, a stainless steel mixing bowl might prioritize wall thickness to withstand rigorous stirring, while a copper decorative bowl might emphasize a thin, elegant profile to highlight its luster.
Safety is a paramount concern in metal spinning, given the high speeds and forces involved. Operators must wear protective gear, including safety glasses, gloves, and hearing protection, to guard against flying debris, sharp edges, and noise levels that can exceed 85 decibels. The lathe should be equipped with guards to contain the workpiece in case of detachment, and tools must be inspected regularly for wear or damage. Proper training is essential, as inexperienced spinners risk injury from mishandling the equipment or misjudging the material’s limits.
Environmental considerations also come into play, particularly in large-scale spinning operations. The process generates scrap metal from blank trimming, which can be recycled to reduce waste. Lubricants and cleaning agents should be chosen for their biodegradability where possible, and energy-efficient lathes can minimize the carbon footprint of production. For hobbyists or small workshops, manual spinning offers a low-impact alternative, relying on human power rather than electricity.
The economic aspects of spinning sheet metal bowls vary widely depending on scale and purpose. For artisanal production, the primary costs are the raw material, lathe maintenance, and labor, with a single hand-spun bowl potentially fetching $50-$200 depending on its craftsmanship and material. Industrial CNC spinning, by contrast, involves higher initial investments—often $10,000 or more for equipment—but benefits from economies of scale, reducing the per-unit cost to a few dollars for mass-produced items. Table 3 outlines the cost factors for different spinning scenarios.
Table 3: Cost Comparison of Spinning Methods
Method | Equipment Cost ($) | Material Cost ($/bowl) | Labor Time (min) | Energy Use (kWh) | Typical Output (bowls/hr) |
---|---|---|---|---|---|
Manual Spinning | 500-2,000 | 2-10 | 15-30 | Negligible | 2-4 |
CNC Spinning | 10,000-50,000 | 1-5 | 5-10 | 1-3 | 20-50 |
Hybrid (Manual + CNC) | 5,000-20,000 | 2-8 | 10-20 | 0.5-2 | 10-20 |
In conclusion, spinning sheet metal bowls is a multifaceted process that blends traditional craftsmanship with modern technology, offering a flexible and efficient method for producing high-quality metalwork. From material selection to tool dynamics, mandrel design to finishing techniques, every aspect of the process requires careful consideration to achieve optimal results. Whether pursued as a hobby, an artisanal trade, or an industrial operation, metal spinning rewards precision, patience, and an understanding of the underlying science. As the field continues to evolve with advancements in automation and materials science, its potential applications—and the beauty of the bowls it produces—will only expand.
Maximize Tooling and CNC Metal Spinning Capabilities.
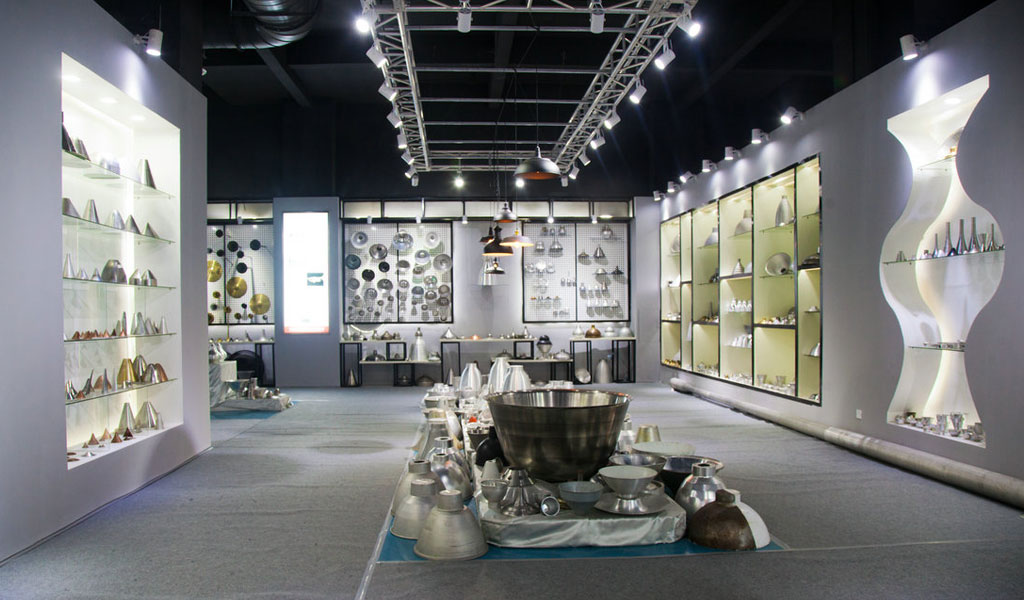
At BE-CU China Metal Spinning company, we make the most of our equipment while monitoring signs of excess wear and stress. In addition, we look into newer, modern equipment and invest in those that can support or increase our manufacturing capabilities. Our team is very mindful of our machines and tools, so we also routinely maintain them to ensure they don’t negatively impact your part’s quality and productivity.
Talk to us today about making a rapid prototype with our CNC metal spinning service. Get a direct quote by chatting with us here or request a free project review.
BE-CU China CNC Metal Spinning service include : CNC Metal Spinning,Metal Spinning Die,Laser Cutting, Tank Heads Spinning,Metal Hemispheres Spinning,Metal Cones Spinning,Metal Dish-Shaped Spinning,Metal Trumpet Spinning,Metal Venturi Spinning,Aluminum Spinning Products,Stainless Steel Spinning Products,Copper Spinning Products,Brass Spinning Products,Steel Spinning Product,Metal Spinnin LED Reflector,Metal Spinning Pressure Vessel,