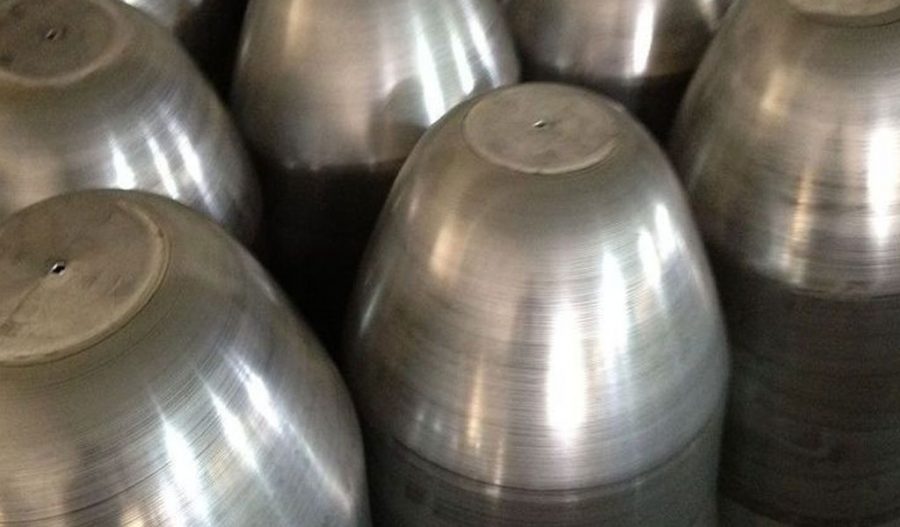
Metal spinning, a centuries-old craft rooted in both artisanal and industrial traditions, involves the shaping of sheet metal into axially symmetrical forms through controlled deformation over a rotating mandrel. Among the myriad finishing techniques applied to spun metal components, rolling the edge—also referred to as edge rolling, beading, or curling—stands out as a critical process that enhances both the functionality and aesthetics of the final product. This article explores the multifaceted process of rolling the edge of metal spinnings, delving into its history, principles, techniques, equipment, material considerations, and applications. Through a comprehensive examination, supported by comparative tables, this discussion aims to provide a thorough understanding of edge rolling in the context of modern manufacturing and traditional craftsmanship.
Historical Context of Metal Spinning and Edge Rolling
The origins of metal spinning trace back to ancient civilizations, with evidence of hand-spun metal artifacts appearing in Egyptian, Mesopotamian, and Chinese cultures as early as the 3rd millennium BCE. These early metalworkers employed rudimentary tools to shape soft metals like gold, silver, and copper into decorative and utilitarian objects, such as bowls, chalices, and ceremonial vessels. Edge rolling, as a complementary technique, likely emerged to address practical needs: strengthening the rim of a spun piece, improving its safety by eliminating sharp edges, and enhancing its visual appeal through smooth, uniform contours.
By the Middle Ages, metal spinning had evolved into a skilled trade across Europe and Asia, with guilds formalizing techniques and training apprentices in the art of shaping metal. Edge rolling became more standardized during this period, as blacksmiths and armorers recognized the importance of reinforced edges on helmets, shields, and cookware. The Industrial Revolution in the 18th and 19th centuries marked a turning point, introducing mechanized lathes and specialized tooling that allowed for greater precision and scalability. The advent of steam-powered and later electrically driven machinery enabled manufacturers to produce spun metal components in large quantities, with edge rolling becoming a critical step in industries ranging from cookware to automotive parts.
In the 20th century, advancements in metallurgy and automation further refined the process. The development of computer numerical control (CNC) technology in the late 20th century revolutionized metal spinning, allowing for intricate edge profiles that were previously unattainable. Today, edge rolling remains a vital technique in industries such as aerospace, automotive, lighting, and consumer goods, where spun metal parts require both structural integrity and aesthetic refinement.
Principles of Edge Rolling in Metal Spinning
Edge rolling is the process of mechanically deforming the outer rim of a spun metal component to create a folded, curled, or beaded edge. The primary objectives of edge rolling are threefold: to enhance structural rigidity, to eliminate sharp or jagged edges for safety, and to improve the visual and tactile qualities of the part. The process is typically performed after the primary spinning operation, which shapes the metal blank into its desired form, such as a cone, cylinder, or hemisphere.
The mechanics of edge rolling rely on plastic deformation, wherein the metal is subjected to controlled forces that exceed its yield strength, causing it to bend or flow into a new shape without fracturing. This deformation occurs under compressive and tensile stresses, depending on the specific edge profile being created. For example, a simple fold involves bending the edge inward or outward, while a full curl requires rolling the edge into a tight, tubular shape. The choice of edge profile depends on the intended application, material properties, and design specifications.
Key factors influencing the edge rolling process include:
- Material Properties: The ductility, thickness, and hardness of the metal determine its suitability for edge rolling. Softer, more ductile metals like aluminum and copper are easier to roll than harder alloys like stainless steel.
- Tooling Design: The shape and material of the rolling tool, typically a hardened steel roller or form tool, dictate the precision and quality of the edge.
- Machine Parameters: Rotational speed, feed rate, and applied pressure must be carefully calibrated to prevent defects such as cracking, wrinkling, or uneven deformation.
- Edge Geometry: The desired profile—whether a single fold, double fold, bead, or curl—requires specific tooling and process adjustments.
Edge rolling can be performed manually, semi-automatically, or fully automatically, depending on the scale of production and the complexity of the part. Manual edge rolling is common in small-scale or artisanal settings, where skilled operators use hand-held tools to shape the edge. In contrast, industrial settings rely on CNC spinning lathes or dedicated edge-rolling machines to achieve high throughput and consistency.
Materials Suitable for Edge Rolling
The choice of material is a critical consideration in edge rolling, as it directly affects the feasibility and quality of the process. Metals commonly used in spinning and edge rolling include aluminum, copper, brass, mild steel, stainless steel, and certain titanium alloys. Each material presents unique challenges and advantages, which are summarized in the following table:
Material | Ductility | Thickness Range (mm) | Edge Rolling Ease | Common Applications | Challenges |
---|---|---|---|---|---|
Aluminum | High | 0.5–6.0 | Easy | Cookware, lighting reflectors, aerospace | Prone to surface scratches |
Copper | Very High | 0.5–4.0 | Very Easy | Decorative items, electrical components | High cost, oxidizes over time |
Brass | High | 0.5–5.0 | Easy | Plumbing fixtures, musical instruments | May require annealing for thick gauges |
Mild Steel | Moderate | 0.8–8.0 | Moderate | Automotive parts, containers | Susceptible to rust, requires coating |
Stainless Steel | Low to Moderate | 0.5–4.0 | Difficult | Medical equipment, food processing | High hardness, requires robust tooling |
Titanium Alloys | Low | 0.5–3.0 | Very Difficult | Aerospace, medical implants | Expensive, prone to cracking without heat |
Aluminum
Aluminum is a preferred material for edge rolling due to its high ductility and lightweight properties. Commonly used alloys, such as 1100, 3003, and 6061, offer excellent formability, making them ideal for applications requiring intricate edge profiles. However, aluminum’s softness can lead to surface imperfections if tooling is not properly polished or if excessive pressure is applied.
Copper
Copper’s exceptional malleability makes it one of the easiest metals to roll. Its natural corrosion resistance and aesthetic appeal suit it for decorative and electrical applications. Edge rolling copper requires minimal force, but care must be taken to avoid overworking the material, which can lead to work hardening and potential cracking.
Brass
Brass, an alloy of copper and zinc, combines ductility with a distinctive golden hue, making it popular for both functional and ornamental parts. Edge rolling brass is straightforward for thinner gauges, but thicker sections may require annealing to restore ductility before rolling.
Mild Steel
Mild steel is widely used in industrial spinning due to its affordability and strength. Edge rolling mild steel is moderately challenging, as its lower ductility compared to non-ferrous metals necessitates precise control of rolling parameters. Protective coatings are often applied post-rolling to prevent corrosion.
Stainless Steel
Stainless steel’s high strength and corrosion resistance make it a staple in demanding applications. However, its lower ductility and tendency to work-harden during deformation complicate edge rolling. Specialized tooling and slower feed rates are often required to achieve defect-free edges.
Titanium Alloys
Titanium alloys are prized for their strength-to-weight ratio and biocompatibility but are among the most difficult materials to roll. Edge rolling titanium typically requires elevated temperatures to enhance ductility, along with robust machinery to handle its high yield strength.
Techniques of Edge Rolling
Edge rolling encompasses a variety of techniques, each tailored to produce a specific edge profile. The following sections describe the most common methods, their applications, and the equipment involved.
Manual Edge Rolling
Manual edge rolling is a traditional technique performed by skilled artisans using hand-held tools or basic spinning lathes. The operator guides a roller or forming tool against the rotating workpiece, gradually shaping the edge into the desired profile. This method is best suited for low-volume production, prototyping, or custom work, where flexibility and craftsmanship are prioritized over speed.
Manual edge rolling requires significant expertise, as the operator must maintain consistent pressure and tool alignment to avoid defects. Common tools include steel rollers, wooden form blocks, and levered burnishing tools. While labor-intensive, manual rolling allows for intricate, bespoke edge designs that are difficult to replicate with automated systems.
Semi-Automatic Edge Rolling
Semi-automatic edge rolling bridges the gap between manual and fully automated processes. In this method, a spinning lathe equipped with a pre-set roller or forming tool is controlled by an operator who adjusts the machine’s parameters, such as speed and feed rate, during the process. Semi-automatic systems are common in small to medium-sized workshops, where moderate production volumes justify the investment in specialized tooling but not full automation.
The advantages of semi-automatic rolling include improved consistency over manual methods and reduced operator fatigue. However, the process still relies on human intervention, which can introduce variability if not carefully monitored.
CNC Edge Rolling
CNC edge rolling represents the pinnacle of precision and efficiency in modern metal spinning. CNC lathes are programmed to execute complex edge profiles with minimal human oversight, using servo-driven rollers and multi-axis toolpaths. The process begins with a digital model of the desired edge geometry, which is translated into machine instructions via computer-aided manufacturing (CAM) software.
CNC edge rolling excels in high-volume production, where repeatability and tight tolerances are paramount. Industries such as aerospace and automotive rely on CNC systems to produce components with uniform edges, often incorporating multiple rolling operations in a single setup. The primary drawbacks are the high initial cost of equipment and the need for skilled programmers to optimize toolpaths.
Specialized Edge Rolling Machines
For applications requiring specific edge profiles, such as tight curls or heavy-duty beads, dedicated edge rolling machines are employed. These machines are designed solely for edge forming and feature robust frames, high-torque spindles, and interchangeable tooling. They are particularly common in the production of pressure vessels, HVAC components, and large containers, where thick-gauge materials demand substantial forming forces.
Specialized machines often incorporate auxiliary features, such as laser sensors for edge detection or automated tool changers, to enhance productivity. Their single-purpose design limits versatility but ensures unmatched performance for targeted applications.
Equipment for Edge Rolling
The equipment used in edge rolling varies widely depending on the scale of production, material, and desired edge profile. The following table compares common equipment types:
Equipment Type | Production Scale | Material Suitability | Edge Profiles | Advantages | Limitations |
---|---|---|---|---|---|
Manual Spinning Lathe | Low | Soft metals (Al, Cu, Brass) | Simple folds, basic curls | High flexibility, low cost | Labor-intensive, inconsistent results |
Semi-Automatic Lathe | Low to Medium | Most metals | Folds, curls, beads | Balance of control and efficiency | Requires skilled operator |
CNC Spinning Lathe | Medium to High | All metals | Complex folds, curls, beads | High precision, repeatability | High cost, complex setup |
Dedicated Edge Roller | High | Thick/hard metals (Steel, Ti) | Heavy beads, tight curls | Optimized for specific tasks | Limited versatility |
Manual Spinning Lathes
Manual lathes are the simplest and most affordable option, consisting of a rotating spindle, a tailstock, and a tool rest. Edge rolling on a manual lathe relies on hand-held rollers or form tools, which are pressed against the workpiece to shape the edge. These lathes are ideal for artisanal work but lack the precision and speed required for industrial applications.
Semi-Automatic Lathes
Semi-automatic lathes feature motorized spindles and adjustable tool holders, allowing operators to control the rolling process with greater ease. Some models include hydraulic or pneumatic assist systems to reduce the physical effort required. These lathes are versatile and can handle a range of materials and edge profiles, making them a popular choice for small manufacturers.
CNC Spinning Lathes
CNC lathes are equipped with computer-controlled spindles, tool turrets, and feedback systems that monitor variables like force and position in real time. They can execute multiple rolling operations in sequence, producing complex edge geometries with minimal setup time. Advanced models integrate sensors and adaptive control algorithms to compensate for material variations, ensuring consistent results.
Dedicated Edge Rolling Machines
Dedicated edge rollers are purpose-built for high-volume edge forming, often featuring dual rollers or multi-stage forming heads. They are designed to handle heavy-gauge materials and demanding applications, such as rolling the edges of steel drums or titanium aerospace components. These machines are typically found in large-scale manufacturing facilities with specialized production lines.
Process Parameters and Optimization
Successful edge rolling depends on optimizing process parameters to suit the material, equipment, and desired outcome. Key parameters include:
- Spindle Speed: Measured in revolutions per minute (RPM), spindle speed affects the rate of deformation and heat generation. Higher speeds are suitable for soft metals, while harder materials require slower speeds to prevent cracking.
- Feed Rate: The speed at which the rolling tool advances along the edge, typically in millimeters per revolution. A slower feed rate improves control but increases cycle time.
- Tool Pressure: The force applied by the roller, which must be sufficient to deform the metal without causing thinning or tearing. Pressure is often adjusted dynamically during CNC rolling.
- Lubrication: Lubricants reduce friction and heat, preventing tool wear and surface defects. Common lubricants include mineral oils, synthetic emulsions, and graphite-based compounds.
- Tool Geometry: The shape and size of the roller influence the edge profile. For example, a narrow roller is used for tight curls, while a broader roller suits flat folds.
Optimization involves balancing these parameters to achieve a defect-free edge while minimizing cycle time and tool wear. For example, rolling aluminum at 500 RPM with a moderate feed rate and light lubrication may produce a smooth curl, whereas stainless steel may require 200 RPM, a slower feed, and heavier lubrication to avoid work hardening.
Common Edge Profiles and Their Applications
Edge rolling produces a variety of profiles, each serving distinct functional or aesthetic purposes. The following table summarizes the most common profiles:
Edge Profile | Description | Applications | Advantages | Challenges |
---|---|---|---|---|
Single Fold | Edge bent inward or outward at 90° | Cookware rims, lighting fixtures | Simple, strengthens edge | Limited rigidity for thin materials |
Double Fold | Edge folded twice for a flat, thick rim | Automotive wheel rims, containers | High strength, smooth finish | Complex tooling, longer cycle time |
Curl | Edge rolled into a tubular shape | Pressure vessels, HVAC ducts | Maximum rigidity, safe to handle | Difficult for hard metals, prone to cracking |
Bead | Edge formed into a rounded, decorative ridge | Decorative bowls, musical instruments | Aesthetic appeal, moderate strength | Requires precise tool alignment |
Single Fold
A single fold involves bending the edge to a right angle, either inward or outward, to create a stiffened rim. This profile is common in lightweight applications, such as aluminum cookware or decorative lamp bases, where minimal material is used.
Double Fold
A double fold doubles the edge back on itself, creating a thicker, flatter rim. This profile is favored in automotive and industrial applications, where durability is critical. The process requires two rolling passes, increasing complexity but yielding a robust edge.
Curl
A curl rolls the edge into a continuous, tubular shape, maximizing rigidity and safety. Curls are essential for pressure-containing vessels, such as gas cylinders, and for components subject to heavy wear, like HVAC ducting. Achieving a tight, uniform curl demands precise tooling and control.
Bead
A bead forms a rounded ridge along the edge, often for decorative purposes. Beaded edges are prevalent in artisanal metalwork, such as brass vases or silver trays, where aesthetics are as important as function. The process is delicate, as misalignment can distort the bead’s symmetry.
Defects and Troubleshooting
Edge rolling, like any forming process, is susceptible to defects that can compromise the quality of the finished part. Common defects include:
- Cracking: Occurs when the metal is overstressed, particularly in low-ductility materials like stainless steel or titanium. Cracking can be mitigated by reducing feed rate, applying heat, or annealing the material beforehand.
- Wrinkling: Results from compressive stresses causing the edge to buckle, often in thin or soft metals. Wrinkling can be minimized by increasing tool pressure or using a supporting mandrel.
- Thinning: Excessive stretching of the metal during rolling can reduce wall thickness, weakening the edge. Thinning is prevented by optimizing tool geometry and feed rate.
- Surface Scratches: Caused by improper lubrication or contaminated tooling, scratches detract from the part’s appearance. Regular tool maintenance and adequate lubrication are essential.
Troubleshooting involves diagnosing the root cause of the defect and adjusting parameters accordingly. For example, if cracking occurs in stainless steel, the operator might lower the spindle speed and apply a lubricant with higher viscosity. In CNC systems, real-time monitoring can detect anomalies early, allowing for immediate corrections.
Industrial and Artisanal Applications
Edge rolling finds applications across a wide range of industries and crafts, reflecting its versatility and importance. In industrial settings, rolled edges are integral to:
- Aerospace: Fuel tanks, engine nacelles, and satellite dishes rely on curled edges for structural integrity and aerodynamic performance.
- Automotive: Wheel rims, exhaust components, and fuel tanks use folded or curled edges to withstand vibration and impact.
- Consumer Goods: Cookware, lighting fixtures, and appliance housings feature rolled edges for safety and aesthetics.
- HVAC: Ducting and ventilation components use curled edges to ensure airtight seals and durability.
In artisanal contexts, edge rolling enhances the value of handcrafted items, such as:
- Jewelry: Spun metal pendants and bangles often feature beaded edges for elegance.
- Decorative Arts: Vases, bowls, and trays benefit from rolled edges that combine form and function.
- Musical Instruments: Bells and cymbals use beaded edges to influence acoustics and durability.
Safety Considerations
Edge rolling, particularly in industrial settings, involves hazards that require strict safety protocols. Key risks include:
- Rotating Machinery: High-speed lathes can cause injury if operators come into contact with moving parts. Guards, interlocks, and personal protective equipment (PPE) are mandatory.
- Tool Breakage: Worn or improperly secured tools can shatter, posing a projectile hazard. Regular inspection and maintenance prevent such incidents.
- Material Handling: Heavy metal blanks and finished parts can cause strain or crush injuries. Mechanical lifts and proper ergonomics mitigate these risks.
- Noise and Vibration: Prolonged exposure to spinning operations can lead to hearing loss or repetitive strain injuries. Ear protection and anti-vibration gloves are recommended.
Operators must be trained in safe machine operation, emergency procedures, and proper handling of materials. In automated systems, fail-safes and remote monitoring reduce the need for direct interaction with machinery.
Environmental and Economic Impacts
Edge rolling, as part of metal spinning, is generally considered an environmentally efficient process, as it produces minimal waste compared to subtractive manufacturing methods like machining. The ability to form complex shapes from a single blank reduces material consumption, and many metals used in spinning, such as aluminum and steel, are highly recyclable.
Economically, edge rolling adds value to spun components by improving their durability and marketability. However, the process can be capital-intensive, particularly for CNC systems or specialized machinery. Small-scale producers may face challenges competing with large manufacturers, though niche markets for custom or artisanal work remain viable.
Future Trends in Edge Rolling
The future of edge rolling is shaped by ongoing advancements in technology and materials science. Emerging trends include:
- Additive-Assisted Spinning: Combining additive manufacturing with spinning to create hybrid components with tailored edge profiles.
- Smart Tooling: Tools embedded with sensors to monitor wear and deformation in real time, improving process reliability.
- Sustainable Materials: Increased use of recycled metals and biodegradable lubricants to reduce environmental impact.
- Automation and AI: Machine learning algorithms to optimize rolling parameters and predict defects before they occur.
These innovations promise to enhance the precision, efficiency, and sustainability of edge rolling, ensuring its relevance in both industrial and artisanal contexts.
Conclusion
Rolling the edge of metal spinnings is a sophisticated process that blends art, science, and engineering. From its historical roots in ancient metalworking to its modern applications in high-tech industries, edge rolling has evolved into a cornerstone of manufacturing. By understanding the principles, techniques, and challenges of edge rolling, practitioners can produce components that meet stringent standards of quality and performance. Whether executed by hand or by advanced machinery, the process exemplifies the enduring value of precision craftsmanship in shaping the world around us.
Maximize Tooling and CNC Metal Spinning Capabilities.
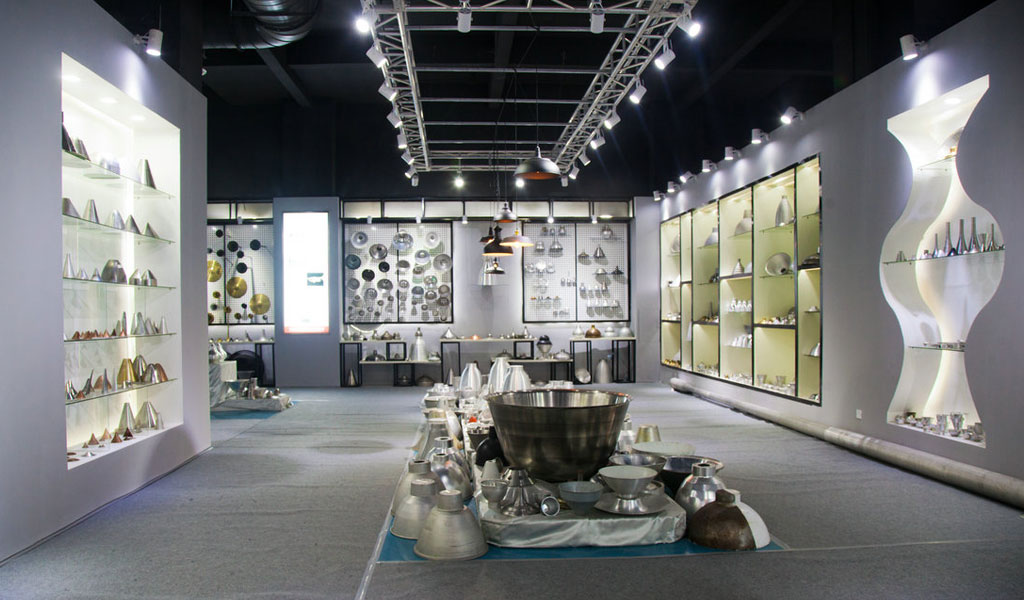
At BE-CU China Metal Spinning company, we make the most of our equipment while monitoring signs of excess wear and stress. In addition, we look into newer, modern equipment and invest in those that can support or increase our manufacturing capabilities. Our team is very mindful of our machines and tools, so we also routinely maintain them to ensure they don’t negatively impact your part’s quality and productivity.
Talk to us today about making a rapid prototype with our CNC metal spinning service. Get a direct quote by chatting with us here or request a free project review.
BE-CU China CNC Metal Spinning service include : CNC Metal Spinning,Metal Spinning Die,Laser Cutting, Tank Heads Spinning,Metal Hemispheres Spinning,Metal Cones Spinning,Metal Dish-Shaped Spinning,Metal Trumpet Spinning,Metal Venturi Spinning,Aluminum Spinning Products,Stainless Steel Spinning Products,Copper Spinning Products,Brass Spinning Products,Steel Spinning Product,Metal Spinnin LED Reflector,Metal Spinning Pressure Vessel,