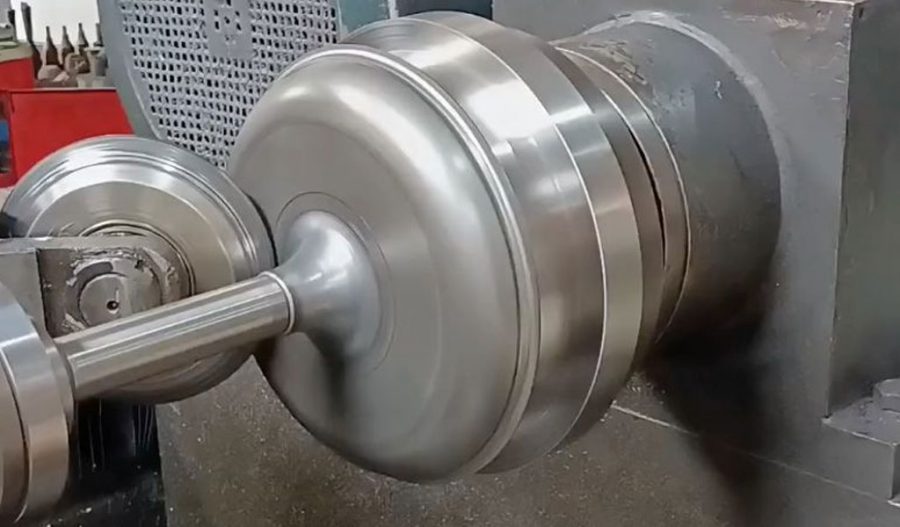
The manufacturing of gas turbine engine components is a highly specialized field within aerospace engineering, requiring precision, durability, and adherence to stringent performance standards. Among the various fabrication techniques employed, metal spinning stands out as a versatile and cost-effective process for producing rotationally symmetric parts, such as compressor housings, combustor liners, and turbine shrouds. Metal spinning, also known as spin forming or spinning, is a metalworking process that shapes a flat metal disc or tube into a desired geometry by rotating it at high speed and applying localized pressure with a tool. This article provides a comprehensive exploration of the metal spinning process as applied to gas turbine engine parts, covering its principles, materials, equipment, process parameters, advantages, limitations, and comparisons with alternative manufacturing methods. The discussion is grounded in scientific principles and includes detailed tables for comparative analysis.
Gas turbine engines, used in aircraft propulsion and power generation, rely on components that must withstand extreme temperatures, pressures, and mechanical stresses. The choice of manufacturing process significantly impacts the performance, cost, and reliability of these components. Metal spinning is particularly suited for producing seamless, high-strength parts with complex geometries, making it an attractive option for aerospace manufacturers. This article aims to elucidate the intricacies of metal spinning in the context of gas turbine engine part production, offering insights into its technical, economic, and practical aspects.
Historical Context of Metal Spinning
Metal spinning has roots dating back thousands of years, with early applications in ancient civilizations for creating pottery and simple metal vessels. The modern industrial application of metal spinning began in the 19th century, driven by advancements in machinery and metallurgy. By the 20th century, the aerospace industry adopted metal spinning for producing lightweight, high-strength components, particularly during the development of jet engines in the mid-20th century.
In the context of gas turbine engines, metal spinning gained prominence due to its ability to form large, thin-walled, rotationally symmetric parts with minimal material waste. The process was refined during the post-World War II era, as manufacturers sought to optimize production for increasingly complex engine designs. Today, metal spinning is a cornerstone of advanced manufacturing, supported by computer numerical control (CNC) systems and sophisticated tooling, enabling unprecedented precision and repeatability.
Principles of Metal Spinning
Process Overview
Metal spinning involves rotating a metal workpiece, typically a flat disc or preformed tube, at high speed on a lathe-like machine. A forming tool, often referred to as a roller or spoon, applies localized pressure to the workpiece, gradually shaping it against a mandrel (a solid form that defines the final geometry). The process can be performed manually, semi-automatically, or fully automatically using CNC systems.
There are two primary types of metal spinning relevant to gas turbine engine parts:
- Conventional Spinning: The workpiece is deformed over a mandrel without significantly altering its thickness. This method is ideal for producing parts with uniform wall thickness, such as combustor liners.
- Shear Spinning: The workpiece undergoes significant thinning as it is formed, resulting in a part with varying wall thickness. Shear spinning is used for components requiring high strength-to-weight ratios, such as turbine shrouds.
Mechanics of Deformation
The deformation in metal spinning is governed by plastic flow, where the metal is subjected to compressive and shear stresses. The process can be described using principles of continuum mechanics, with the stress-strain relationship influenced by the material’s yield strength, strain hardening, and ductility. The key mechanical phenomena include:
- Radial and Tangential Stresses: As the roller presses against the rotating workpiece, radial compression and tangential tension develop, driving material flow.
- Thinning and Stretching: In shear spinning, the material undergoes significant thinning, governed by the sine law, which relates the wall thickness to the angle of the mandrel’s surface.
- Springback: Elastic recovery after deformation can affect dimensional accuracy, requiring precise control of process parameters.
Material Flow and Formability
The formability of a metal in spinning depends on its ductility, grain structure, and strain rate sensitivity. Materials with high elongation-to-fracture ratios, such as aluminum alloys and certain stainless steels, are well-suited for spinning. The process induces work hardening, which increases the material’s strength but may reduce ductility, necessitating careful control to avoid cracking or wrinkling.
Materials for Gas Turbine Engine Parts
Gas turbine engine components are typically made from high-performance materials capable of withstanding extreme operating conditions. The choice of material for metal spinning depends on the component’s function, operating environment, and manufacturing requirements. Common materials include:
- Aluminum Alloys: Used for compressor housings and other low-temperature components due to their lightweight and excellent formability. Alloys such as 6061 and 7075 are commonly spun.
- Stainless Steels: Austenitic stainless steels (e.g., 304, 316) are used for combustor liners and exhaust components due to their corrosion resistance and high-temperature strength.
- Nickel-Based Superalloys: Inconel 718 and Hastelloy X are employed for turbine shrouds and other hot-section components, offering exceptional creep resistance and thermal stability.
- Titanium Alloys: Ti-6Al-4V is used for compressor blades and casings, balancing strength, weight, and corrosion resistance.
Material Properties and Spinning Characteristics
The following table summarizes the properties and spinning characteristics of common materials used in gas turbine engine parts:
Material | Density (g/cm³) | Yield Strength (MPa) | Elongation (%) | Spinning Suitability | Applications |
---|---|---|---|---|---|
Aluminum 6061 | 2.7 | 276 | 12-17 | Excellent | Compressor housings, fan casings |
Stainless Steel 304 | 8.0 | 215 | 40-60 | Good | Combustor liners, exhaust ducts |
Inconel 718 | 8.2 | 1036 | 12-20 | Moderate | Turbine shrouds, nozzle components |
Ti-6Al-4V | 4.4 | 880 | 10-15 | Moderate | Compressor blades, casings |
Challenges in Spinning High-Performance Alloys
Spinning nickel-based superalloys and titanium alloys presents challenges due to their high strength and low ductility at room temperature. These materials often require elevated temperatures (hot spinning) to enhance formability, typically between 800°C and 1200°C for nickel alloys and 600°C to 900°C for titanium alloys. Hot spinning introduces additional complexities, such as thermal expansion, oxidation, and the need for specialized tooling materials (e.g., molybdenum or ceramic rollers).
Equipment and Tooling
Spinning Machines
Metal spinning machines range from manual lathes to advanced CNC spinning centers. For gas turbine engine parts, CNC spinning machines are preferred due to their precision and ability to handle complex geometries. Key components of a spinning machine include:
- Spindle: Rotates the workpiece at speeds typically ranging from 500 to 2000 RPM, depending on the material and part size.
- Mandrel: A precision-machined form that defines the inner geometry of the part. Mandrels are typically made from tool steel or aluminum for durability.
- Tailstock: Applies axial pressure to secure the workpiece against the mandrel.
- Tooling System: Includes rollers or spoons, which may be single-point or multi-point, depending on the desired forming action.
Tooling Materials and Design
The choice of tooling material is critical to withstand the high forces and temperatures encountered in spinning. Common tooling materials include:
- Tool Steel: Used for cold spinning of aluminum and stainless steel.
- Molybdenum: Employed for hot spinning of nickel and titanium alloys due to its high melting point and strength.
- Ceramics: Used in specialized applications for their wear resistance and thermal stability.
Tool geometry, such as roller radius and angle, significantly affects the quality of the spun part. Smaller roller radii provide greater precision but increase the risk of surface defects, while larger radii distribute forces more evenly but may reduce control over fine details.
CNC Integration
Modern spinning machines incorporate CNC systems to control tool paths, spindle speed, and feed rates. CNC spinning allows for multi-pass forming, where the workpiece is shaped incrementally to minimize stress concentrations and improve surface finish. The integration of sensors and real-time monitoring systems further enhances process control, enabling manufacturers to detect defects such as wrinkling or thinning during production.
Process Parameters
The success of metal spinning depends on optimizing key process parameters, which influence the quality, efficiency, and cost of the final part. These parameters include:
- Spindle Speed: Higher speeds reduce forming time but may cause excessive heat generation, particularly in hot spinning.
- Feed Rate: The rate at which the roller advances along the workpiece affects surface finish and material flow. Typical feed rates range from 0.5 to 2 mm/rev.
- Roller Pressure: The force applied by the roller determines the degree of deformation. Excessive pressure can cause thinning or cracking, while insufficient pressure may result in incomplete forming.
- Temperature: For hot spinning, precise control of workpiece and tooling temperatures is essential to maintain material formability and prevent defects.
Optimization Strategies
Process optimization often involves finite element analysis (FEA) to simulate material flow, stress distribution, and potential defects. FEA models can predict the effects of varying spindle speed, feed rate, and roller pressure, allowing manufacturers to develop robust process parameters before production begins. Experimental validation, such as trial spinning runs, is also critical to ensure repeatability and quality.
Applications in Gas Turbine Engines
Metal spinning is used to produce a variety of gas turbine engine components, each with specific requirements for geometry, material, and performance. Key applications include:
Compressor Housings
Compressor housings encase the compressor stages, directing airflow and maintaining structural integrity under high pressure. These components are typically made from aluminum or titanium alloys and require precise tolerances to ensure aerodynamic efficiency. Metal spinning is ideal for producing seamless compressor housings with smooth internal surfaces, minimizing turbulence and improving engine performance.
Combustor Liners
Combustor liners contain the combustion process, enduring temperatures exceeding 1500°C. Stainless steel or nickel-based superalloys are commonly used, with metal spinning employed to form thin-walled, cylindrical liners with complex cooling hole patterns. The seamless nature of spun liners reduces stress concentrations and enhances durability.
Turbine Shrouds
Turbine shrouds surround the turbine blades, maintaining tight clearances to optimize efficiency. These components are often made from nickel-based superalloys and require shear spinning to achieve thin walls and high strength. The ability to produce near-net-shape shrouds via spinning reduces machining costs and material waste.
Exhaust Ducts
Exhaust ducts channel high-temperature exhaust gases out of the engine. Stainless steel or Inconel is typically used, with metal spinning employed to create large, thin-walled ducts with smooth contours. The process allows for the integration of flanges and mounting features directly into the spun part, simplifying assembly.
Advantages of Metal Spinning
Metal spinning offers several advantages for manufacturing gas turbine engine parts:
- Material Efficiency: The process generates minimal waste, as the workpiece is deformed rather than cut away.
- Seamless Construction: Spun parts lack welds or joints, reducing stress concentrations and improving fatigue life.
- Cost-Effectiveness: Metal spinning requires relatively low tooling costs compared to forging or casting, making it suitable for low- to medium-volume production.
- Flexibility: The process can accommodate a wide range of materials and geometries, from small compressor housings to large exhaust ducts.
- High Strength: Work hardening during spinning enhances the mechanical properties of the part, improving its performance under load.
Limitations of Metal Spinning
Despite its advantages, metal spinning has limitations that must be considered:
- Geometric Constraints: The process is limited to rotationally symmetric parts, restricting its applicability to certain components.
- Material Challenges: High-strength alloys, such as nickel-based superalloys, require hot spinning, increasing complexity and cost.
- Surface Finish: Spinning may produce surface imperfections, such as tool marks, requiring secondary finishing operations.
- Tool Wear: The high forces and temperatures involved in spinning can lead to rapid tool wear, particularly for hard materials.
- Dimensional Accuracy: Springback and thinning can affect tolerances, necessitating precise process control and post-processing.
Comparison with Alternative Manufacturing Methods
To evaluate the suitability of metal spinning for gas turbine engine parts, it is useful to compare it with alternative manufacturing methods, such as forging, casting, and additive manufacturing. The following table provides a detailed comparison:
Criterion | Metal Spinning | Forging | Casting | Additive Manufacturing |
---|---|---|---|---|
Material Efficiency | High (minimal waste) | Moderate (some material loss) | Low (significant waste in gating) | High (near-net-shape) |
Geometric Flexibility | Limited to rotationally symmetric parts | High (complex shapes possible) | High (complex shapes possible) | Very high (intricate geometries) |
Mechanical Properties | Good (work hardening) | Excellent (grain refinement) | Moderate (potential defects) | Variable (depends on process) |
Tooling Cost | Low to moderate | High | Moderate to high | Low (no tooling required) |
Production Volume | Low to medium | Medium to high | Medium to high | Low to medium |
Surface Finish | Moderate (may require finishing) | Good | Poor (requires finishing) | Poor (requires finishing) |
Lead Time | Short (simple tooling) | Long (complex dies) | Moderate (mold preparation) | Short (digital design) |
Typical Applications | Compressor housings, combustor liners | Turbine discs, shafts | Turbine blades, casings | Prototypes, complex cooling channels |
Discussion of Comparison
- Forging excels in producing high-strength components with refined grain structures, making it ideal for critical parts like turbine discs. However, its high tooling costs and long lead times make it less competitive for low-volume production.
- Casting is suitable for complex geometries, such as turbine blades with internal cooling passages, but it suffers from potential defects (e.g., porosity) and significant material waste.
- Additive Manufacturing offers unparalleled geometric freedom, enabling the production of intricate components like lattice structures. However, its mechanical properties are often inferior to those of spun or forged parts, and surface finish remains a challenge.
- Metal Spinning strikes a balance between cost, material efficiency, and mechanical performance, making it a preferred choice for rotationally symmetric parts in gas turbine engines.
Quality Control and Inspection
Ensuring the quality of spun gas turbine engine parts requires rigorous inspection and testing. Common quality control methods include:
- Dimensional Inspection: Coordinate measuring machines (CMMs) and laser scanners verify tolerances, typically within ±0.05 mm for aerospace components.
- Non-Destructive Testing (NDT): Techniques such as ultrasonic testing, X-ray radiography, and dye penetrant inspection detect internal defects like cracks or voids.
- Metallurgical Analysis: Microstructural examination ensures proper grain structure and absence of defects like inclusions or recrystallization.
- Mechanical Testing: Tensile, fatigue, and creep tests validate the part’s performance under operating conditions.
Common Defects and Mitigation
Spinning can introduce defects such as:
- Wrinkling: Caused by excessive compressive stresses, mitigated by optimizing feed rate and roller pressure.
- Cracking: Resulting from excessive thinning or low material ductility, prevented by controlling temperature and strain rate.
- Surface Imperfections: Tool marks or scratches, addressed through secondary polishing or coating.
Economic Considerations
The economic viability of metal spinning for gas turbine engine parts depends on several factors:
- Tooling Costs: Spinning requires relatively inexpensive mandrels and rollers compared to forging dies or casting molds.
- Material Costs: The high material efficiency of spinning reduces raw material expenses, particularly for costly alloys like Inconel.
- Labor Costs: Manual spinning is labor-intensive, but CNC automation reduces labor requirements and improves consistency.
- Production Volume: Spinning is most cost-effective for low- to medium-volume production, as high-volume runs may justify the higher tooling costs of forging or casting.
Cost Comparison
The following table compares the approximate costs of manufacturing a typical gas turbine engine component (e.g., a combustor liner) using different methods:
Method | Tooling Cost (USD) | Material Cost (USD/part) | Labor Cost (USD/part) | Total Cost (USD/part) |
---|---|---|---|---|
Metal Spinning | 5,000 – 10,000 | 200 | 50 | 300 – 350 |
Forging | 50,000 – 100,000 | 250 | 75 | 400 – 500 |
Casting | 20,000 – 50,000 | 300 | 100 | 450 – 600 |
Additive Manufacturing | 0 (no tooling) | 400 | 150 | 550 – 700 |
Note: Costs are approximate and vary based on part size, material, and production volume.
Environmental Impact
Metal spinning is relatively environmentally friendly compared to other manufacturing processes due to its high material efficiency and low energy consumption. Key environmental considerations include:
- Material Waste: Spinning generates minimal scrap, reducing the need for recycling or disposal.
- Energy Use: CNC spinning machines consume less energy than forging presses or casting furnaces.
- Emissions: Hot spinning may produce emissions from heating processes, necessitating proper ventilation and filtration systems.
Sustainability Strategies
Manufacturers can enhance the sustainability of metal spinning by:
- Using recycled materials, such as aluminum or stainless steel, to reduce the environmental footprint.
- Implementing energy-efficient CNC machines and optimizing process parameters to minimize power consumption.
- Adopting closed-loop cooling systems for hot spinning to reduce water usage.
Future Trends and Innovations
The metal spinning process continues to evolve, driven by advancements in materials, automation, and digital technologies. Emerging trends include:
- Hybrid Manufacturing: Combining metal spinning with additive manufacturing to produce complex parts with integrated features, such as cooling channels in combustor liners.
- Smart Manufacturing: Integrating artificial intelligence (AI) and machine learning to optimize process parameters in real-time, improving quality and reducing defects.
- Advanced Materials: Developing new alloys with enhanced formability for spinning, such as high-entropy alloys or metal matrix composites.
- Sustainability: Focusing on eco-friendly spinning processes, such as cold spinning with recycled materials or low-energy CNC systems.
Research Directions
Ongoing research in metal spinning for gas turbine engine parts focuses on:
- Improving the formability of high-strength alloys through novel heating techniques, such as laser-assisted spinning.
- Developing multi-axis CNC spinning machines to produce non-rotationally symmetric parts, expanding the process’s applicability.
- Enhancing surface finish through in-process polishing or coating techniques, reducing the need for secondary operations.
Case Studies
Case Study 1: Compressor Housing for a Commercial Jet Engine
A leading aerospace manufacturer used metal spinning to produce compressor housings for a commercial jet engine. The housings, made from aluminum 6061, required a diameter of 800 mm and a wall thickness of 3 mm. CNC spinning was employed with a multi-pass forming strategy, achieving tolerances of ±0.1 mm. The seamless construction reduced assembly time and improved aerodynamic performance, resulting in a 15% cost savings compared to forging.
Case Study 2: Combustor Liner for a Military Turbine
A military turbine required combustor liners made from Inconel 718 to withstand temperatures up to 1400°C. Hot spinning at 1000°C was used to form the liners, with a mandrel designed to incorporate cooling hole patterns. The process achieved a 20% reduction in material waste compared to casting, and the spun liners exhibited superior fatigue life due to work hardening.
Conclusion
Metal spinning is a versatile and efficient manufacturing process for producing gas turbine engine parts, offering significant advantages in material efficiency, cost, and mechanical performance. Its ability to create seamless, high-strength components makes it a preferred choice for applications such as compressor housings, combustor liners, and turbine shrouds. While the process is limited to rotationally symmetric parts and faces challenges with high-strength alloys, ongoing advancements in CNC technology, materials, and hybrid manufacturing are expanding its capabilities.
This article has provided a comprehensive overview of metal spinning in the context of gas turbine engine part production, covering its principles, materials, equipment, process parameters, and comparisons with alternative methods. Through detailed tables and scientific analysis, it has highlighted the process’s strengths, limitations, and potential for future innovation. As the aerospace industry continues to demand lightweight, durable, and cost-effective components, metal spinning will remain a critical tool in the manufacturing arsenal, driving advancements in gas turbine engine performance and sustainability.
Maximize Tooling and CNC Metal Spinning Capabilities.
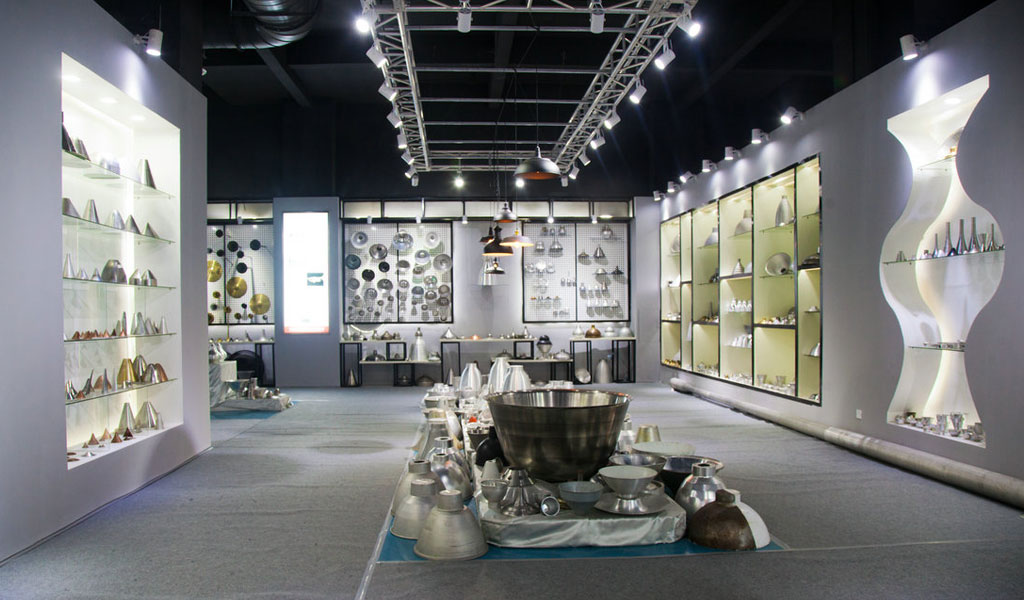
At BE-CU China Metal Spinning company, we make the most of our equipment while monitoring signs of excess wear and stress. In addition, we look into newer, modern equipment and invest in those that can support or increase our manufacturing capabilities. Our team is very mindful of our machines and tools, so we also routinely maintain them to ensure they don’t negatively impact your part’s quality and productivity.
Talk to us today about making a rapid prototype with our CNC metal spinning service. Get a direct quote by chatting with us here or request a free project review.
BE-CU China CNC Metal Spinning service include : CNC Metal Spinning,Metal Spinning Die,Laser Cutting, Tank Heads Spinning,Metal Hemispheres Spinning,Metal Cones Spinning,Metal Dish-Shaped Spinning,Metal Trumpet Spinning,Metal Venturi Spinning,Aluminum Spinning Products,Stainless Steel Spinning Products,Copper Spinning Products,Brass Spinning Products,Steel Spinning Product,Metal Spinnin LED Reflector,Metal Spinning Pressure Vessel,