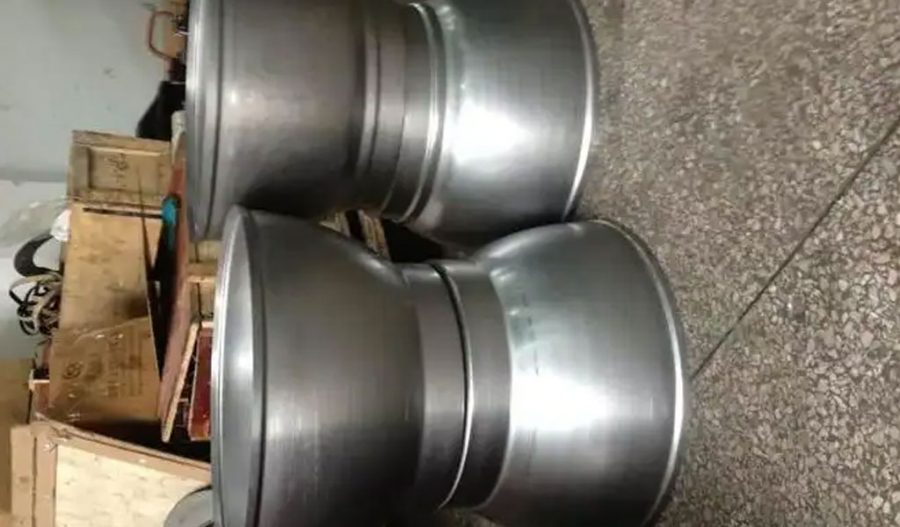
Spinning technology, also known as metal spinning, spin forming, or metal turning, is a metalworking process that shapes a rotating disc or tube of sheet metal into axially symmetric parts using localized pressure from a forming tool. This technique has been employed for centuries, with origins tracing back to ancient Egypt, but its modern applications in the automotive industry have transformed it into a sophisticated method for producing complex, high-precision components. In the context of automobile manufacturing, spinning technology is critical for creating lightweight, durable, and intricate sheet metal parts that meet stringent performance, safety, and aesthetic requirements.
The automotive industry relies heavily on sheet metal fabrication to produce components such as body panels, structural frames, exhaust systems, and engine parts. Spinning technology stands out among other forming processes—such as stamping, deep drawing, and hydroforming—due to its ability to produce seamless, high-strength parts with minimal material waste. Its versatility allows for the processing of a wide range of materials, including aluminum, steel, stainless steel, and advanced alloys, which are essential for modern vehicle designs that prioritize fuel efficiency, crashworthiness, and environmental sustainability.
This article explores the application of spinning technology in the processing of complex sheet metal parts for automobiles, covering its principles, techniques, materials, equipment, advantages, challenges, and future trends. Detailed comparisons with other forming methods, case studies, and technical data are provided to offer a comprehensive understanding of its role in automotive manufacturing.
Principles of Spinning Technology
Basic Mechanics of Metal Spinning
Metal spinning involves clamping a flat or preformed metal blank against a mandrel, which is mounted on a lathe or spinning machine. The mandrel, shaped to the desired geometry of the final part, rotates at high speeds along with the blank. A roller or forming tool applies localized force to the rotating blank, causing it to deform plastically and conform to the mandrel’s contour. The process is incremental, often requiring multiple passes of the roller to achieve the final shape.
The deformation in spinning is governed by principles of plastic flow, where the metal is stretched, compressed, or sheared depending on the technique used. Unlike subtractive manufacturing processes like machining, spinning is a non-material-removal process, preserving the original volume of the blank while altering its shape. This results in parts with consistent wall thickness (in conventional spinning) or controlled thinning (in shear spinning or flow forming).
Types of Spinning Processes
Spinning technology encompasses several distinct processes, each suited to specific applications in automotive part production:
- Conventional Spinning: The most basic form, where the blank is shaped over the mandrel while maintaining its original thickness. The diameter of the blank decreases, and its depth increases. This method is ideal for producing conical or cylindrical parts like wheel rims or exhaust cones.
- Shear Spinning: Involves reducing the wall thickness of the blank while maintaining its diameter, governed by the Sine Law (final thickness = original thickness × sine of the semi-apex angle for conical parts). Shear spinning enhances mechanical properties through compressive forces and is used for lightweight structural components.
- Flow Forming (Tube Spinning): A process where a tubular blank is elongated axially along a mandrel, reducing wall thickness and increasing length. It is used for precision cylindrical parts like drive shafts or suspension components.
- Hot Spinning: Performed at elevated temperatures to improve formability of low-ductility materials like titanium or high-strength steels. A heating torch is applied during spinning, enabling the production of complex geometries.
- Friction Spinning: An innovative variant combining metal spinning with friction welding principles, where self-induced heat from friction enhances formability and allows for tailored material properties. This is particularly useful for functionally graded automotive parts.
Each process is selected based on the part’s geometry, material properties, and performance requirements. For example, shear spinning is preferred for lightweight parts, while hot spinning is used for materials that are difficult to deform at room temperature.
Key Components of Spinning Equipment
The equipment used in metal spinning includes lathes or dedicated spinning machines, which consist of the following components:
- Mandrel: A rotating form that defines the internal shape of the part. Mandrels can be made of metal, wood, or even ice for complex or temporary forms.
- Roller: The tool that applies force to the blank. Rollers vary in diameter and radius, with wider rollers producing smoother surfaces and thinner rollers enabling sharper radii.
- Headstock and Spindle: Drive the rotation of the mandrel and blank.
- Tailstock: Clamps the blank against the mandrel, ensuring stability during spinning.
- Tool Rest: Supports the roller or lever arms, providing leverage for manual or automated forming.
Modern spinning machines often incorporate Computer Numerical Control (CNC) or Programmable Numerical Control (PNC) systems, enabling precise control over roller paths and process parameters. CNC spinning machines, such as the Leifeld PNC350-800, are widely used in automotive manufacturing for their automation, repeatability, and ability to handle large workpieces.
Applications in Automotive Sheet Metal Processing
Body Panels and Structural Components
Spinning technology is extensively used to produce body panels and structural components that require seamless, axially symmetric geometries. Examples include:
- Wheel Rims: Spinning is used to form lightweight aluminum or steel wheel rims with precise dimensions and high strength. Flow forming is particularly effective for reducing wall thickness, improving fuel efficiency.
- Exhaust Cones and Pipes: Conical exhaust components are produced using conventional or shear spinning, offering smooth internal surfaces that enhance exhaust flow and reduce backpressure.
- Fuel Tank Components: Spinning creates seamless hemispherical or cylindrical sections for fuel tanks, ensuring high pressure resistance and structural integrity.
- Structural Brackets: Complex brackets for chassis or suspension systems are formed using spinning to achieve intricate shapes with minimal material waste.
These components benefit from spinning’s ability to produce parts with uniform thickness, high strength-to-weight ratios, and excellent surface finishes, which are critical for aerodynamic performance and vehicle safety.
Engine and Transmission Parts
Spinning technology is also applied in the production of engine and transmission components, where precision and durability are paramount:
- Pulleys and Flywheels: Spinning forms lightweight, balanced pulleys and flywheels with consistent wall thickness, reducing rotational inertia and improving engine efficiency.
- Drive Shafts: Flow forming produces seamless, high-strength drive shafts with tailored wall thickness, enhancing torque transmission and reducing weight.
- Turbocharger Housings: Hot spinning is used to form complex geometries from high-temperature alloys like Inconel, ensuring resistance to thermal fatigue in turbocharger applications.
These parts require tight tolerances and robust mechanical properties, which spinning achieves through controlled deformation and work hardening.
Decorative and Functional Trim
In addition to functional components, spinning is used to create decorative trim pieces, such as hubcaps, bezels, and interior accents. These parts often require high-quality surface finishes and intricate shapes, which spinning delivers efficiently. For example, aluminum hubcaps are spun to achieve polished, seamless surfaces that enhance vehicle aesthetics.
Table 1: Automotive Components Produced by Spinning Technology
Component | Spinning Process | Material | Key Benefits | Applications |
---|---|---|---|---|
Wheel Rims | Flow Forming | Aluminum, Steel | Lightweight, High Strength | Passenger Cars, Trucks |
Exhaust Cones | Conventional/Shear Spinning | Stainless Steel | Seamless, Smooth Flow | Exhaust Systems |
Fuel Tank Sections | Conventional Spinning | Aluminum | Pressure Resistance, Seamless | Fuel Storage |
Drive Shafts | Flow Forming | Steel | High Strength, Reduced Weight | Powertrain |
Pulleys | Conventional Spinning | Aluminum | Balanced, Lightweight | Engine Systems |
Turbocharger Housings | Hot Spinning | Inconel | Thermal Resistance, Complex Geometry | Turbochargers |
Hubcaps | Conventional Spinning | Aluminum | Aesthetic Finish, Seamless | Exterior Trim |
Materials Used in Automotive Spinning
Common Materials and Their Properties
The choice of material in spinning is critical to achieving the desired performance characteristics of automotive parts. The following materials are commonly used:
- Aluminum: Lightweight, corrosion-resistant, and highly formable, aluminum is ideal for wheel rims, fuel tank components, and decorative trim. Its high strength-to-weight ratio supports fuel efficiency.
- Steel: Offers exceptional strength and durability, used for structural components like drive shafts and exhaust pipes. Mild steel (up to 9 mm thick) and high-strength steels are commonly spun.
- Stainless Steel: Provides corrosion resistance and high-temperature performance, suitable for exhaust systems and turbocharger housings. Thicknesses up to 3 mm are typically spun.
- Titanium: High strength-to-weight ratio and corrosion resistance make titanium suitable for premium components like suspension parts, though it requires hot spinning due to low ductility.
- High-Temperature Alloys (e.g., Inconel, Hastelloy): Used in demanding applications like turbocharger housings, these alloys require hot spinning to achieve complex shapes.
The formability of these materials depends on their ductility, tensile elongation, and work-hardening behavior. Spinning enhances material properties through plastic deformation, increasing strength and hardness.
Material Selection Criteria
Material selection for spinning in automotive applications is based on:
- Mechanical Properties: Strength, ductility, and fatigue resistance are critical for structural and functional components.
- Formability: Materials with high tensile elongation and low yield strength are easier to spin, reducing the risk of cracking or wrinkling.
- Corrosion Resistance: Essential for components exposed to environmental factors, such as exhaust systems or body panels.
- Weight: Lightweight materials like aluminum and titanium are prioritized to improve fuel efficiency and vehicle dynamics.
- Cost: Balances performance requirements with production economics, as high-cost materials like titanium are reserved for specialized applications.
Table 2: Material Properties for Spinning in Automotive Applications
Material | Density (g/cm³) | Yield Strength (MPa) | Tensile Elongation (%) | Corrosion Resistance | Typical Applications |
---|---|---|---|---|---|
Aluminum (6061) | 2.7 | 276 | 12-25 | High | Wheel Rims, Fuel Tanks |
Mild Steel | 7.85 | 250-400 | 20-30 | Moderate | Drive Shafts, Brackets |
Stainless Steel (304) | 8.0 | 215 | 40-60 | High | Exhaust Systems |
Titanium (Ti-6Al-4V) | 4.43 | 880 | 10-15 | Very High | Suspension Components |
Inconel 718 | 8.19 | 1036 | 12-20 | Very High | Turbocharger Housings |
Comparison with Other Sheet Metal Forming Processes
Overview of Alternative Processes
Spinning technology competes with other sheet metal forming processes in automotive manufacturing, including:
- Stamping/Pressing: Uses dies to press sheet metal into shapes, suitable for high-volume production of body panels and brackets.
- Deep Drawing: Pulls sheet metal into a die cavity to form deep, seamless parts like fuel tanks or fenders.
- Hydroforming: Uses high-pressure hydraulic fluid to shape metal into complex geometries, ideal for chassis components and structural brackets.
- Stretch Forming: Stretches and bends sheet metal over a die, used for large panels like door skins or roof sections.
Each process has unique advantages and limitations, making them complementary or competitive depending on the application.
Comparative Analysis
Spinning offers distinct advantages over other processes in specific scenarios, particularly for axially symmetric parts with complex geometries. The following table compares spinning with alternative processes based on key metrics:
Table 3: Comparison of Sheet Metal Forming Processes
Process | Material Waste | Tooling Cost | Production Volume | Part Complexity | Surface Finish | Typical Automotive Applications |
---|---|---|---|---|---|---|
Spinning | Low | Low-Moderate | Low to High | High (Axisymmetric) | High | Wheel Rims, Exhaust Cones |
Stamping | Moderate | High | High | Moderate | Moderate | Body Panels, Brackets |
Deep Drawing | Moderate | High | High | High (Deep Parts) | Moderate | Fuel Tanks, Fenders |
Hydroforming | Low | High | Moderate to High | Very High | High | Chassis Components |
Stretch Forming | Low | Moderate | Low to Moderate | Moderate (Large Parts) | High | Door Skins, Roof Panels |
Advantages of Spinning
- Low Material Waste: Spinning preserves the original blank volume, reducing scrap compared to stamping or deep drawing.
- Cost-Effective Tooling: Mandrels are simpler and less expensive than dies used in stamping or hydroforming, making spinning economical for low to medium volumes.
- Flexibility: Spinning accommodates a wide range of materials and thicknesses (0.25–9 mm), with quick adjustments to forming parameters.
- Seamless Parts: Produces seamless components with high structural integrity, ideal for pressure vessels and exhaust systems.
- Enhanced Mechanical Properties: Work hardening during spinning increases strength and fatigue resistance.
Limitations of Spinning
- Limited to Axisymmetric Parts: Spinning is less suitable for non-circular or highly asymmetric geometries.
- Skill Dependency: Manual spinning requires skilled operators, though CNC automation mitigates this.
- Wrinkling and Fracture Risks: Improper process parameters can lead to defects, particularly in thin or low-ductility materials.
- Lower Throughput for Complex Parts: Multiple passes increase cycle times compared to single-stroke processes like stamping.
Advanced Techniques and Innovations
CNC and PNC Spinning
The integration of CNC and PNC systems has revolutionized spinning technology, enabling precise control over roller paths, feed rates, and spinning forces. CNC spinning machines, such as the Leifeld PNC350-800, offer:
- Automation: Reduces reliance on manual skill, improving repeatability and scalability.
- Complex Toolpaths: Enables the production of intricate geometries with multi-pass strategies.
- Playback Mode: Records manual forming movements for automated replication, ideal for high-volume production.
These advancements have made spinning viable for automotive parts requiring tight tolerances, such as wheel rims and drive shafts.
Friction Spinning
Friction spinning combines metal spinning with friction welding principles, using frictional heat to enhance formability. This process is particularly effective for:
- Functionally Graded Parts: Tailors material properties (e.g., strength, grain size) by controlling temperature profiles.
- Complex Geometries: Extends forming limits for materials like titanium or high-strength steels.
- Tube and Sheet Processing: Applicable to both tubular and flat blanks, expanding its automotive applications.
Friction spinning is an emerging technology with potential for lightweight structural components in electric vehicles (EVs).
Hot Spinning for Advanced Alloys
Hot spinning addresses the challenges of forming low-ductility materials by heating the blank to forging temperatures during processing. This technique is critical for:
- High-Temperature Alloys: Enables the production of turbocharger housings and exhaust components from Inconel or Hastelloy.
- Thick Blanks: Facilitates the spinning of materials up to 25 mm thick, suitable for heavy-duty structural parts.
- Reduced Forming Forces: Lowers the energy required for deformation, improving process efficiency.
Hot spinning is increasingly used in high-performance vehicles and EVs, where advanced materials are prevalent.
Non-Axisymmetric and Novel Spinning Processes
Recent research has explored non-axisymmetric spinning and non-circular blank spinning, challenging the traditional limitation of axisymmetric parts. These processes involve:
- Non-Circular Blanks: Spinning octagonal or irregular blanks to produce asymmetric components, as demonstrated in studies with AL-1050 aluminum.
- Tooth-Shaped Spinning: Creates parts with complex cross-sections, such as gear-like structures.
- Multi-Axis Spinning: Uses advanced CNC systems to control multiple axes, enabling the production of non-symmetric geometries.
These innovations expand spinning’s applicability to a broader range of automotive components, including custom chassis parts and aesthetic trim.
Case Studies in Automotive Applications
Case Study 1: Aluminum Wheel Rims
Background: A leading automotive manufacturer sought to produce lightweight aluminum wheel rims for a new line of electric vehicles to improve range and efficiency.
Process: Flow forming was selected to reduce wall thickness and weight while maintaining strength. A 6061 aluminum alloy blank was spun over a mandrel using a CNC flow forming machine. The process involved multiple passes to achieve a final thickness of 2 mm from an initial 5 mm blank.
Outcome:
- Weight Reduction: 20% lighter than stamped steel rims, improving fuel efficiency.
- Strength: Enhanced tensile strength due to work hardening.
- Cost Savings: Lower tooling costs compared to forging, with a 15% reduction in material waste.
- Production Rate: 500 rims per day, suitable for medium-volume production.
Challenges: Initial wrinkling defects were mitigated by optimizing feed rates and roller angles, demonstrating the importance of process parameter control.
Case Study 2: Stainless Steel Exhaust Cones
Background: An aftermarket exhaust system supplier needed seamless conical components for high-performance vehicles to reduce backpressure and enhance aesthetics.
Process: Shear spinning was used to form 304 stainless steel blanks into conical shapes. The process reduced wall thickness by 30% while maintaining diameter, improving flow characteristics. A CNC spinning machine ensured precise dimensional control.
Outcome:
- Performance: Smooth internal surfaces reduced turbulence, increasing exhaust efficiency by 10%.
- Aesthetics: Polished finish enhanced visual appeal.
- Durability: Seamless construction improved resistance to thermal fatigue.
- Cycle Time: 25 seconds per component, suitable for high-volume production.
Challenges: High initial setup costs for CNC programming were offset by long-term production efficiency.
Case Study 3: Inconel Turbocharger Housings
Background: A manufacturer of high-performance vehicles required turbocharger housings capable of withstanding extreme temperatures and pressures.
Process: Hot spinning was employed to form Inconel 718 blanks at forging temperatures (approximately 1000°C). The process used a CNC hot spinning machine with integrated heating torches to maintain material ductility.
Outcome:
- Thermal Resistance: Parts withstood temperatures up to 900°C without deformation.
- Complex Geometry: Achieved intricate internal contours unattainable with stamping.
- Production Efficiency: Reduced forming forces lowered energy consumption by 20%.
- Cost: Higher material and energy costs were justified by performance requirements.
Challenges: Precise temperature control was critical to prevent cracking, requiring advanced process monitoring.
Challenges and Limitations
Process Parameter Optimization
The success of spinning depends on optimizing parameters such as mandrel speed, feed rate, roller radius, and roller angle. Improper settings can lead to defects like:
- Wrinkling: Occurs in thin blanks or at high roller feeds, particularly in large-diameter parts.
- Fracture: Results from excessive thinning or low material ductility.
- Surface Scratches: Caused by inadequate lubrication or improper roller design.
Finite element analysis (FEA) and experimental trials are used to optimize these parameters, but the process remains partly empirical, relying on operator expertise or trial-and-error in industrial settings.
Toolpath Design Complexity
Designing toolpaths for complex parts is a significant challenge, particularly for multi-pass spinning. While CNC systems enable precise control, creating optimal toolpaths requires:
- Simulation: FEA models to predict stress, strain, and thickness distribution.
- Skilled Programming: Knowledge of material behavior and machine capabilities.
- Iterative Testing: Trial runs to refine paths and eliminate defects.
Research is ongoing to automate toolpath design using artificial intelligence and machine learning, but current practices still rely heavily on manual expertise.
Material Formability Limits
Materials with low ductility, such as titanium or high-strength steels, pose challenges in cold spinning, often requiring hot spinning or friction spinning. These processes increase complexity and cost, limiting their use to high-value applications.
Scalability for High-Volume Production
While spinning is cost-effective for low to medium volumes, it is less competitive for high-volume production compared to stamping or deep drawing. The multi-pass nature of spinning increases cycle times, making it less suitable for mass-produced parts like body panels.
Future Trends and Research Directions
Automation and Industry 4.0 Integration
The integration of Industry 4.0 technologies, such as IoT, real-time monitoring, and data analytics, is transforming spinning processes. Future advancements include:
- Smart Spinning Machines: Sensors to monitor forces, temperatures, and defects in real-time, enabling adaptive process control.
- Digital Twins: Virtual models of spinning processes to optimize parameters and predict outcomes.
- Robotics: Automated loading, unloading, and roller manipulation to increase throughput.
These technologies will enhance efficiency, reduce defects, and make spinning more competitive for high-volume automotive production.
Lightweight Materials and Electric Vehicles
The rise of electric vehicles (EVs) is driving demand for lightweight components to extend battery range. Spinning is well-positioned to process advanced materials like:
- Magnesium Alloys: Lightweight but difficult to form, requiring hot spinning or friction spinning.
- Carbon Fiber-Reinforced Composites: Emerging research explores spinning hybrid metal-composite blanks for ultra-light parts.
- Aluminum-Lithium Alloys: Offer superior strength-to-weight ratios for EV structural components.
Spinning’s ability to produce seamless, lightweight parts aligns with EV design goals, making it a key technology for future automotive manufacturing.
Sustainable Manufacturing
Spinning supports sustainable manufacturing through:
- Material Efficiency: Minimal waste compared to subtractive processes.
- Energy Efficiency: Lower forming forces in hot or friction spinning reduce energy consumption.
- Recyclability: Seamless parts are easier to recycle than multi-piece assemblies.
Research is focused on optimizing spinning processes to further reduce environmental impact, such as using renewable energy sources for heating in hot spinning.
Novel Spinning Processes
Emerging spinning processes, such as non-axisymmetric spinning and tooth-shaped spinning, are expanding the range of possible geometries. These processes require advanced CNC systems and novel mandrel designs, opening new applications in automotive chassis and aesthetic components.
Table 4: Future Trends in Spinning Technology
Trend | Description | Impact on Automotive Manufacturing |
---|---|---|
Industry 4.0 | IoT, real-time monitoring, robotics | Increased efficiency, reduced defects |
Lightweight Materials | Magnesium, aluminum-lithium, composites | Lighter EVs, improved range |
Sustainability | Material and energy efficiency | Lower environmental impact |
Novel Processes | Non-axisymmetric, tooth-shaped spinning | Broader range of component designs |
Conclusion
Spinning technology is a versatile and cost-effective method for processing complex sheet metal parts in the automotive industry. Its ability to produce seamless, high-strength, and lightweight components makes it indispensable for applications ranging from wheel rims and exhaust systems to turbocharger housings and structural brackets. By leveraging advanced techniques like CNC spinning, friction spinning, and hot spinning, manufacturers can meet the demanding requirements of modern vehicles, including fuel efficiency, crashworthiness, and aesthetic appeal.
Despite challenges such as process parameter optimization and scalability, ongoing innovations in automation, material science, and novel spinning processes are expanding its capabilities. As the automotive industry transitions to electric vehicles and sustainable manufacturing, spinning technology is poised to play a pivotal role in shaping the future of sheet metal fabrication.
This comprehensive exploration of spinning technology highlights its technical principles, practical applications, and potential for growth, providing a valuable resource for engineers, researchers, and industry professionals in automotive manufacturing.
Maximize Tooling and CNC Metal Spinning Capabilities.
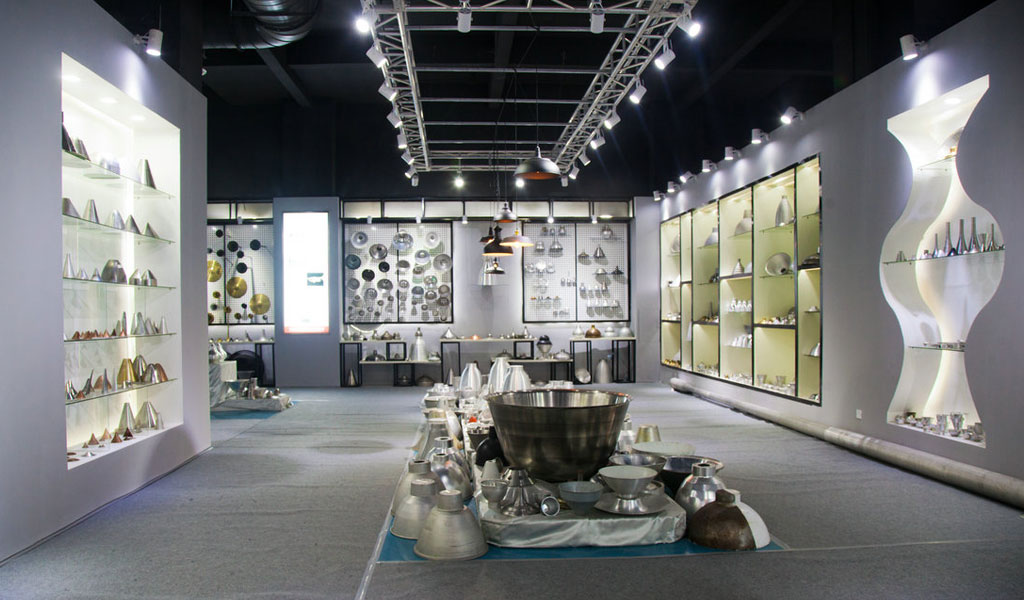
At BE-CU China Metal Spinning company, we make the most of our equipment while monitoring signs of excess wear and stress. In addition, we look into newer, modern equipment and invest in those that can support or increase our manufacturing capabilities. Our team is very mindful of our machines and tools, so we also routinely maintain them to ensure they don’t negatively impact your part’s quality and productivity.
Talk to us today about making a rapid prototype with our CNC metal spinning service. Get a direct quote by chatting with us here or request a free project review.
BE-CU China CNC Metal Spinning service include : CNC Metal Spinning,Metal Spinning Die,Laser Cutting, Tank Heads Spinning,Metal Hemispheres Spinning,Metal Cones Spinning,Metal Dish-Shaped Spinning,Metal Trumpet Spinning,Metal Venturi Spinning,Aluminum Spinning Products,Stainless Steel Spinning Products,Copper Spinning Products,Brass Spinning Products,Steel Spinning Product,Metal Spinnin LED Reflector,Metal Spinning Pressure Vessel,