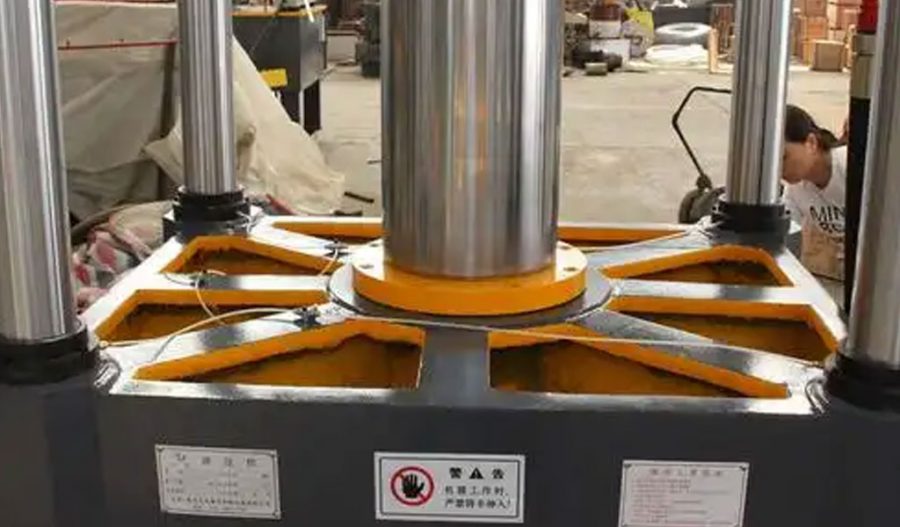
Hydroforming is a specialized manufacturing process used to shape ductile metals, such as aluminum, brass, copper, steel, and stainless steel, into structurally robust, lightweight components. This technique employs high-pressure hydraulic fluid to press metal into a die, enabling the creation of complex geometries that are often unattainable through conventional metal-forming methods like stamping or forging. Hydroforming is widely utilized across industries, including automotive, aerospace, plumbing, and consumer goods, due to its ability to produce parts with high strength-to-weight ratios, minimal material waste, and enhanced structural integrity. This article provides an in-depth exploration of hydroforming, covering its principles, processes, equipment, materials, applications, advantages, limitations, and future trends, with a focus on scientific rigor and technical detail.
1. Introduction to Hydroforming
1.1 Definition and Scope
Hydroforming is a metal-forming process that uses pressurized fluid to shape metal workpieces into desired configurations. Unlike traditional mechanical pressing, which relies on rigid punches and dies, hydroforming employs a fluid medium—typically water mixed with additives or oil—to apply uniform pressure to the workpiece. This results in smooth, precise deformation, even for intricate shapes. The process is versatile, applicable to both sheet metal and tubular components, and is categorized into two primary types: sheet hydroforming and tube hydroforming.
1.2 Historical Background
The origins of hydroforming can be traced to the early 20th century, with significant advancements during the 1940s and 1950s. Initially developed for producing small, complex parts for plumbing and bicycle manufacturing, hydroforming gained prominence in the automotive industry during the late 20th century. The demand for lightweight, fuel-efficient vehicles spurred innovations in hydroforming technology, enabling the production of chassis components, exhaust systems, and structural frames. Today, hydroforming is a cornerstone of modern manufacturing, supported by advancements in computer-aided design (CAD), finite element analysis (FEA), and hydraulic systems.
1.3 Importance in Modern Manufacturing
Hydroforming addresses several challenges in metal forming, including the need for lightweight structures, complex geometries, and cost-effective production. Its ability to reduce the number of welds and joints in assemblies enhances component durability and reduces manufacturing costs. Industries such as aerospace rely on hydroforming to produce seamless, high-strength parts, while the automotive sector uses it to meet stringent fuel economy and safety standards. The process’s flexibility also makes it suitable for prototyping and low-volume production, bridging the gap between custom and mass manufacturing.
2. Fundamental Principles of Hydroforming
2.1 Mechanics of Fluid Pressure
At its core, hydroforming leverages Pascal’s principle, which states that pressure applied to a confined fluid is transmitted uniformly in all directions. In hydroforming, a sealed chamber or die contains the workpiece, and hydraulic fluid is pressurized to deform the metal against the die’s contours. The uniform pressure distribution minimizes localized stress concentrations, reducing the risk of cracking or thinning in the workpiece. The pressure required varies depending on the material’s yield strength, thickness, and the complexity of the desired shape, typically ranging from 10 MPa to 400 MPa (1,450 psi to 58,000 psi).
2.2 Material Deformation and Plasticity
Hydroforming induces plastic deformation in the workpiece, causing it to permanently adopt the shape of the die. The process exploits the material’s ductility, which is its ability to undergo significant deformation without fracturing. Key material properties, such as yield strength, ultimate tensile strength, and elongation, influence the hydroforming process. For instance, aluminum alloys with high elongation are ideal for hydroforming due to their ability to stretch without tearing. The process also benefits from the Bauschinger effect, where prior deformation in one direction reduces the yield strength in the opposite direction, facilitating complex forming operations.
2.3 Role of Friction and Lubrication
Friction between the workpiece and the die affects material flow and surface quality in hydroforming. Excessive friction can lead to uneven deformation or surface defects, while insufficient friction may cause the workpiece to slip, resulting in inaccurate shapes. Lubricants, such as oil-based emulsions or polymer films, are applied to reduce friction and enhance material flow. The choice of lubricant depends on the material, die surface, and process conditions, with water-based lubricants being common for aluminum and oil-based lubricants preferred for steel.
3. Types of Hydroforming Processes
3.1 Sheet Hydroforming
Sheet hydroforming involves forming flat metal sheets into three-dimensional shapes using a single die and a pressurized fluid. The sheet is placed over a die cavity, and a flexible diaphragm or bladder applies fluid pressure to press the sheet into the die. This method is ideal for producing shallow, complex parts, such as automotive body panels, appliance housings, and aircraft skin components. Sheet hydroforming is further divided into two subtypes: high-pressure hydroforming and low-pressure hydroforming.
3.1.1 High-Pressure Sheet Hydroforming
High-pressure sheet hydroforming uses pressures exceeding 100 MPa to form intricate shapes with tight tolerances. The process is suitable for materials with low ductility, such as high-strength steels, and is often used in automotive and aerospace applications. The high pressure ensures uniform material flow, reducing springback—the tendency of metal to revert to its original shape after deformation.
3.1.2 Low-Pressure Sheet Hydroforming
Low-pressure sheet hydroforming operates at pressures below 100 MPa and is used for larger, less complex parts, such as fuel tank components or architectural panels. This method is cost-effective for materials with high ductility, such as aluminum and copper, and requires simpler equipment compared to high-pressure systems.
3.2 Tube Hydroforming
Tube hydroforming shapes hollow metal tubes into complex geometries by expanding them within a die using internal fluid pressure. The tube is sealed at both ends, and hydraulic fluid is injected to expand the tube against the die walls. Axial feeding, where the tube ends are compressed to supply additional material, enhances the process’s ability to form intricate shapes without thinning the tube walls. Tube hydroforming is widely used for automotive chassis components, exhaust systems, and bicycle frames.
3.2.1 High-Pressure Tube Hydroforming
High-pressure tube hydroforming applies pressures up to 400 MPa to achieve significant expansion ratios, enabling the production of complex, lightweight structures. This method is common in the automotive industry for components like engine cradles and side rails, where structural integrity is critical.
3.2.2 Low-Pressure Tube Hydroforming
Low-pressure tube hydroforming uses pressures below 100 MPa and is suitable for simpler shapes or materials with high ductility. This method is less equipment-intensive and is often employed in plumbing and HVAC applications, such as copper tubing for refrigeration systems.
3.3 Other Hydroforming Variants
In addition to sheet and tube hydroforming, specialized variants exist for niche applications. These include:
- Explosive Hydroforming: Uses controlled explosions to generate pressure, ideal for large, thick-walled components in aerospace and defense.
- Electro-Hydraulic Forming: Employs electrical discharges in a liquid medium to create shock waves, suitable for high-speed forming of thin sheets.
- Rubber Pad Forming: Combines a rubber pad with hydraulic pressure to form delicate materials, often used in prototyping.
4. Hydroforming Equipment and Systems
4.1 Hydraulic Press Systems
The backbone of hydroforming is the hydraulic press, which generates the force needed to pressurize the fluid. Modern presses are equipped with servo-hydraulic or electro-mechanical systems for precise control of pressure and speed. Press capacities range from 1,000 kN to over 50,000 kN, depending on the application. Key components include the hydraulic cylinder, fluid reservoir, and pressure intensifier, which amplifies fluid pressure to the required levels.
4.2 Die Design and Materials
Dies in hydroforming are typically made from high-strength tool steels, such as AISI D2 or H13, to withstand repeated high-pressure cycles. For complex geometries, dies may incorporate multiple segments or movable inserts to facilitate part removal. Computer-aided engineering (CAE) tools, such as finite element analysis, are used to optimize die design, ensuring uniform pressure distribution and minimizing wear.
4.3 Fluid Systems and Additives
The hydraulic fluid in hydroforming is typically a water-based emulsion or synthetic oil, chosen for its viscosity, lubricity, and corrosion resistance. Additives, such as anti-corrosion agents, anti-foaming agents, and viscosity modifiers, enhance fluid performance. The fluid system includes pumps, valves, and filters to maintain consistent pressure and cleanliness, as contaminants can damage the workpiece or die.
4.4 Control Systems and Automation
Modern hydroforming systems integrate advanced control systems, including programmable logic controllers (PLCs) and human-machine interfaces (HMIs), to monitor and adjust process parameters in real time. Sensors measure pressure, temperature, and material deformation, while algorithms optimize cycle times and energy consumption. Automation, such as robotic loading and unloading, enhances productivity in high-volume production.
5. Materials in Hydroforming
5.1 Commonly Used Metals
Hydroforming is compatible with a wide range of ductile metals, each with unique properties that influence process parameters and outcomes. Table 1 provides a comparison of commonly hydroformed materials.
Table 1: Properties of Commonly Hydroformed Metals
Material | Yield Strength (MPa) | Elongation (%) | Common Applications | Hydroforming Suitability |
---|---|---|---|---|
Aluminum (6061-T6) | 275 | 12-17 | Automotive panels, aerospace components | High ductility, lightweight, corrosion-resistant |
Stainless Steel (304) | 215 | 40-60 | Exhaust systems, medical devices | Excellent formability, high strength |
Mild Steel (A36) | 250 | 20-30 | Chassis components, structural frames | Cost-effective, moderate formability |
Copper | 70-200 | 30-50 | Plumbing fittings, electrical components | High ductility, excellent conductivity |
Brass | 100-400 | 20-50 | Decorative parts, fittings | Good formability, aesthetic appeal |
Titanium (Grade 2) | 345 | 20-30 | Aerospace, medical implants | High strength, challenging to form |
5.2 Material Selection Criteria
Material selection for hydroforming depends on the part’s functional requirements, such as strength, weight, and corrosion resistance, as well as process constraints, including die design and pressure limits. Aluminum and stainless steel are favored for their balance of formability and strength, while copper and brass are chosen for applications requiring conductivity or aesthetics. Titanium, though difficult to hydroform due to its high yield strength, is used in high-performance applications where weight savings are critical.
5.3 Material Preparation
Before hydroforming, workpieces undergo preparation steps, such as cleaning, annealing, and lubrication. Annealing softens the metal, increasing its ductility and reducing the risk of cracking. Cleaning removes surface contaminants that could affect fluid performance or die longevity. Lubrication, applied as a thin film, ensures smooth material flow and prevents galling—a form of adhesive wear between the workpiece and die.
6. Hydroforming Process Parameters
6.1 Pressure Control
Precise control of fluid pressure is critical to achieving uniform deformation without defects. Pressure profiles are tailored to the material and part geometry, with gradual increases to prevent sudden yielding. For tube hydroforming, internal pressure is synchronized with axial feeding to maintain wall thickness. Typical pressure ranges are shown in Table 2.
Table 2: Typical Pressure Ranges for Hydroforming Processes
Process Type | Pressure Range (MPa) | Applications |
---|---|---|
High-Pressure Sheet | 100-400 | Automotive panels, aerospace parts |
Low-Pressure Sheet | 10-100 | Fuel tanks, architectural panels |
High-Pressure Tube | 100-400 | Chassis components, exhaust systems |
Low-Pressure Tube | 10-100 | Plumbing fittings, HVAC components |
6.2 Temperature Effects
While hydroforming is typically performed at room temperature, elevated temperatures can enhance material ductility for difficult-to-form metals like titanium or high-strength steels. Warm hydroforming, conducted at 100-300°C, reduces yield strength and improves formability. Hot hydroforming, at temperatures above 300°C, is less common due to equipment complexity but is used for specialized aerospace applications.
6.3 Cycle Time and Productivity
Cycle times in hydroforming vary from seconds to minutes, depending on the part size, material, and equipment. Sheet hydroforming typically has shorter cycle times (10-30 seconds) due to simpler setups, while tube hydroforming may take longer (30-120 seconds) due to axial feeding and pressure calibration. Automation and optimized pressure profiles can reduce cycle times, improving throughput in high-volume production.
7. Applications of Hydroforming
7.1 Automotive Industry
Hydroforming is a cornerstone of automotive manufacturing, used to produce lightweight, high-strength components that improve fuel efficiency and safety. Common applications include:
- Chassis Components: Engine cradles, side rails, and crossmembers benefit from tube hydroforming’s ability to create seamless, complex shapes with minimal welds.
- Body Panels: Sheet hydroforming produces hoods, doors, and fenders with smooth surfaces and precise contours.
- Exhaust Systems: Hydroformed stainless steel tubes ensure durability and corrosion resistance in exhaust manifolds and catalytic converter housings.
7.2 Aerospace Industry
In aerospace, hydroforming creates lightweight, high-strength parts critical to aircraft performance. Applications include:
- Fuselage Components: Hydroformed aluminum and titanium panels reduce weight while maintaining structural integrity.
- Engine Components: Complex geometries in turbine housings and fuel system parts are achieved through high-pressure hydroforming.
- Structural Frames: Tube hydroforming produces seamless frames for landing gear and wing supports.
7.3 Consumer Goods and Plumbing
Hydroforming is used to manufacture a range of consumer products and plumbing components, such as:
- Bicycle Frames: Lightweight, seamless aluminum or steel frames improve performance and aesthetics.
- Appliance Housings: Sheet hydroforming creates durable, visually appealing casings for kitchen appliances.
- Plumbing Fittings: Copper and brass fittings benefit from hydroforming’s ability to produce leak-proof, intricate shapes.
7.4 Emerging Applications
Advancements in hydroforming are expanding its use in emerging fields, such as renewable energy and medical devices. Hydroformed components are found in wind turbine frames, solar panel supports, and implantable medical devices, where precision and biocompatibility are essential.
8. Advantages of Hydroforming
8.1 Lightweight Structures
Hydroforming produces parts with high strength-to-weight ratios, critical for industries like automotive and aerospace. By enabling complex geometries without additional material, hydroforming reduces component weight compared to traditional methods like stamping or welding.
8.2 Reduced Tooling Costs
Unlike stamping, which requires matched punch-and-die sets, hydroforming uses a single die, lowering tooling costs. This is particularly advantageous for low-volume production or prototyping, where tooling expenses can be prohibitive.
8.3 Enhanced Structural Integrity
Hydroformed parts are seamless, with fewer welds or joints, reducing weak points and improving fatigue resistance. The uniform pressure distribution also minimizes material thinning, ensuring consistent wall thickness.
8.4 Material Efficiency
Hydroforming generates minimal material waste, as the process shapes the workpiece directly into the final form without extensive trimming. This reduces raw material costs and aligns with sustainable manufacturing practices.
8.5 Design Flexibility
The ability to form complex, three-dimensional shapes in a single operation allows designers to create innovative components that would be impractical with other methods. Hydroforming also supports rapid prototyping, enabling iterative design improvements.
9. Limitations of Hydroforming
9.1 High Equipment Costs
Hydroforming requires specialized hydraulic presses, dies, and fluid systems, which entail significant capital investment. This can be a barrier for small manufacturers or industries with low production volumes.
9.2 Material Constraints
Hydroforming is limited to ductile metals, excluding brittle materials like cast iron or certain high-carbon steels. Even among ductile metals, materials with low elongation, such as titanium, require careful process optimization to avoid defects.
9.3 Process Complexity
Achieving optimal results in hydroforming demands precise control of pressure, axial feeding, and lubrication. Improper parameter settings can lead to defects like wrinkling, thinning, or bursting, requiring extensive expertise and testing.
9.4 Cycle Time Limitations
While hydroforming is efficient for complex parts, its cycle times are longer than those of stamping or forging for simpler components. This can limit its competitiveness in high-volume production of basic shapes.
10. Comparison with Other Metal-Forming Processes
Hydroforming competes with several traditional and advanced metal-forming processes, each with distinct advantages and limitations. Table 3 compares hydroforming with stamping, forging, and superplastic forming.
Table 3: Comparison of Metal-Forming Processes
Process | Complexity of Shapes | Tooling Cost | Material Waste | Strength-to-Weight Ratio | Typical Applications |
---|---|---|---|---|---|
Hydroforming | High | Moderate | Low | High | Automotive chassis, aerospace panels |
Stamping | Moderate | High | Moderate | Moderate | Body panels, appliance casings |
Forging | Low | High | Low | High | Crankshafts, gears, structural components |
Superplastic Forming | High | High | Low | Moderate | Aerospace components, complex prototypes |
10.1 Hydroforming vs. Stamping
Stamping uses matched dies to press metal sheets into shapes, suitable for high-volume production of simpler parts. However, it generates more material waste and requires costly tooling. Hydroforming excels in forming complex, seamless parts with lower tooling costs, but its cycle times are longer, making it less competitive for basic shapes.
10.2 Hydroforming vs. Forging
Forging compresses metal under high force to create dense, high-strength parts, ideal for components like crankshafts. However, it is limited to simpler geometries and requires expensive dies. Hydroforming offers greater design flexibility and lower tooling costs but cannot match forging’s ability to enhance material grain structure.
10.3 Hydroforming vs. Superplastic Forming
Superplastic forming uses high temperatures and low strain rates to form complex shapes in materials like titanium and aluminum. It is ideal for aerospace prototypes but requires lengthy cycle times and specialized equipment. Hydroforming is faster and more cost-effective for most applications, though it is less suited to superplastic materials.
11. Quality Control and Defect Mitigation
11.1 Common Defects
Hydroforming can result in defects such as:
- Wrinkling: Caused by excessive compressive stress or insufficient pressure, leading to folds in the workpiece.
- Thinning: Occurs when the material stretches excessively, reducing wall thickness and compromising strength.
- Bursting: Results from excessive pressure or material defects, causing the workpiece to rupture.
- Surface Imperfections: Scratches or galling due to inadequate lubrication or die wear.
11.2 Inspection Techniques
Quality control in hydroforming involves non-destructive testing (NDT) methods, such as:
- Ultrasonic Testing: Detects internal defects like cracks or voids.
- X-Ray Inspection: Identifies wall thickness variations and internal irregularities.
- Dimensional Scanning: Ensures parts meet tolerances using laser or optical scanners.
11.3 Process Optimization
Finite element analysis (FEA) is widely used to simulate hydroforming processes, predicting defects and optimizing parameters like pressure, axial feed, and die design. Real-time monitoring systems, equipped with pressure and displacement sensors, adjust process conditions to prevent defects during production.
12. Environmental and Economic Considerations
12.1 Sustainability
Hydroforming aligns with sustainable manufacturing by minimizing material waste and enabling lightweight designs that reduce energy consumption in end-use applications, such as vehicles and aircraft. The use of water-based fluids and recyclable metals further enhances its environmental footprint. However, the energy-intensive nature of hydraulic presses and the need for fluid disposal require careful management to mitigate environmental impact.
12.2 Cost Analysis
Hydroforming’s economic viability depends on production volume, part complexity, and material costs. For low- to medium-volume production of complex parts, hydroforming is cost-competitive due to lower tooling costs and reduced assembly steps. In high-volume scenarios, its longer cycle times may increase costs compared to stamping. Table 4 summarizes cost factors.
Table 4: Cost Factors in Hydroforming
Cost Component | Impact on Hydroforming | Mitigation Strategies |
---|---|---|
Equipment | High initial investment | Use modular presses, lease equipment |
Tooling | Moderate, single die | Optimize die design with CAE |
Material | Varies by metal type | Select cost-effective alloys, recycle scrap |
Labor | Moderate, skilled operators | Automate processes, train workforce |
Energy | High for hydraulic presses | Use energy-efficient systems, optimize cycles |
13. Innovations and Future Trends
13.1 Advanced Materials
Research is expanding hydroforming’s compatibility with advanced materials, such as magnesium alloys, composites, and ultra-high-strength steels. These materials offer superior strength-to-weight ratios but require specialized processes, such as warm or hot hydroforming, to enhance formability.
13.2 Hybrid Processes
Hybrid hydroforming processes, combining hydroforming with additive manufacturing or laser forming, are emerging to address limitations in geometry and material properties. For example, 3D-printed dies can reduce tooling costs for prototyping, while laser-assisted hydroforming enhances precision in high-strength materials.
13.3 Digitalization and Industry 4.0
The integration of Industry 4.0 technologies, such as the Internet of Things (IoT), artificial intelligence (AI), and digital twins, is transforming hydroforming. Digital twins simulate entire hydroforming systems, enabling predictive maintenance and process optimization. AI algorithms analyze sensor data to adjust parameters in real time, improving quality and efficiency.
13.4 Sustainability Initiatives
Future hydroforming developments are focusing on sustainability, including energy-efficient presses, biodegradable fluids, and closed-loop recycling systems for metals and fluids. These initiatives aim to reduce the process’s environmental footprint while maintaining economic competitiveness.
14. Case Studies
14.1 Automotive Engine Cradle
A leading automaker adopted tube hydroforming to produce an engine cradle for a mid-size SUV. The hydroformed cradle, made from high-strength steel, reduced weight by 15% compared to a welded assembly, improving fuel efficiency. The seamless design also enhanced crash performance, meeting stringent safety standards. The project required a $2 million investment in hydroforming equipment but achieved a 20% reduction in production costs due to fewer assembly steps.
14.2 Aerospace Fuselage Panel
An aerospace manufacturer used sheet hydroforming to create aluminum fuselage panels for a commercial airliner. The panels, formed at 200 MPa, featured complex curvatures that reduced aerodynamic drag. The process eliminated the need for multiple forming steps, cutting production time by 30%. Finite element analysis ensured uniform thickness, meeting aerospace tolerances of ±0.1 mm.
14.3 Bicycle Frame Manufacturing
A bicycle manufacturer employed tube hydroforming to produce lightweight aluminum frames for high-performance road bikes. The process allowed for aerodynamic tube shapes, reducing frame weight by 10% while maintaining stiffness. The use of low-pressure hydroforming minimized equipment costs, making the process viable for small-batch production.
15. Conclusion
Hydroforming is a transformative metal-forming process that combines precision, flexibility, and efficiency to produce complex, lightweight components. Its ability to shape ductile metals into seamless, high-strength structures has made it indispensable in industries ranging from automotive to aerospace. Despite challenges, such as high equipment costs and material constraints, hydroforming’s advantages—reduced tooling costs, minimal waste, and enhanced structural integrity—position it as a cornerstone of modern manufacturing. Ongoing innovations in materials, hybrid processes, and digitalization promise to further expand hydroforming’s capabilities, ensuring its relevance in a rapidly evolving industrial landscape.
This article has provided a comprehensive examination of hydroforming, from its fundamental principles to its practical applications and future potential. By leveraging advanced equipment, optimized process parameters, and rigorous quality control, hydroforming continues to push the boundaries of what is possible in metal forming, delivering solutions that balance performance, cost, and sustainability.
Maximize Tooling and CNC Metal Spinning Capabilities.
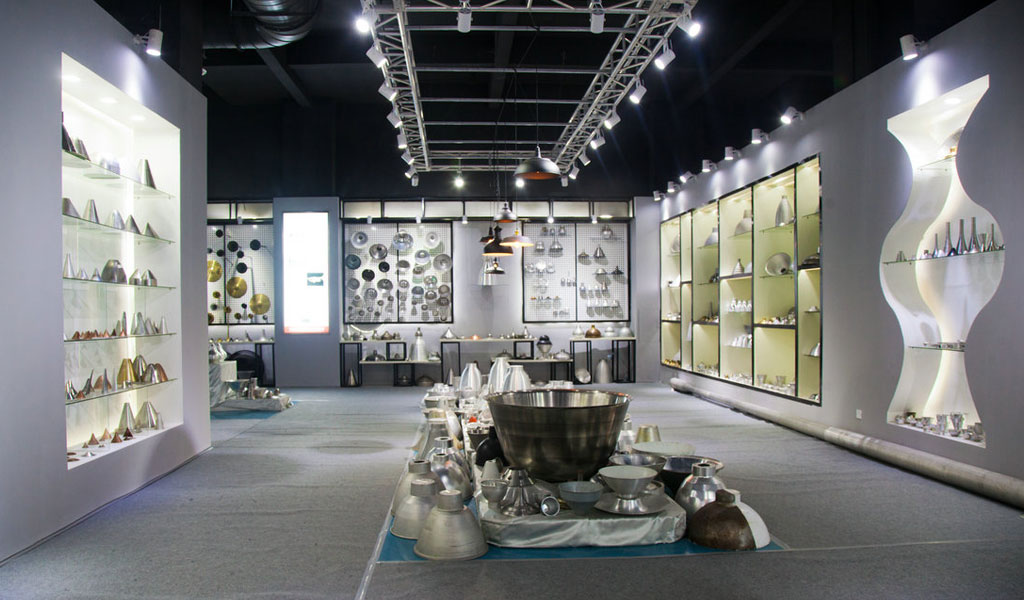
At BE-CU China Metal Spinning company, we make the most of our equipment while monitoring signs of excess wear and stress. In addition, we look into newer, modern equipment and invest in those that can support or increase our manufacturing capabilities. Our team is very mindful of our machines and tools, so we also routinely maintain them to ensure they don’t negatively impact your part’s quality and productivity.
Talk to us today about making a rapid prototype with our CNC metal spinning service. Get a direct quote by chatting with us here or request a free project review.
BE-CU China CNC Metal Spinning service include : CNC Metal Spinning,Metal Spinning Die,Laser Cutting, Tank Heads Spinning,Metal Hemispheres Spinning,Metal Cones Spinning,Metal Dish-Shaped Spinning,Metal Trumpet Spinning,Metal Venturi Spinning,Aluminum Spinning Products,Stainless Steel Spinning Products,Copper Spinning Products,Brass Spinning Products,Steel Spinning Product,Metal Spinnin LED Reflector,Metal Spinning Pressure Vessel,