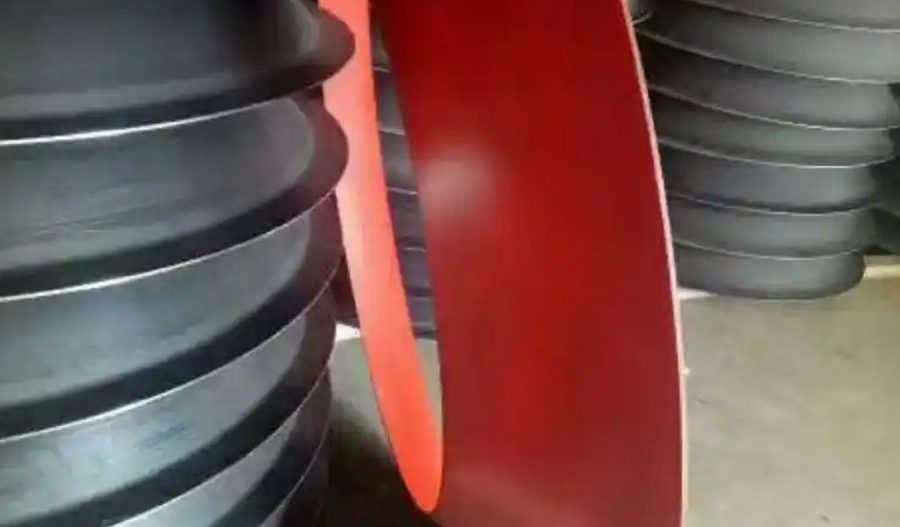
Metal spinning, also known as spin forming or metal turning, is a metalworking process used to form axially symmetric parts by rotating a metal blank or tube at high speed while applying localized pressure with a tool to shape it against a mandrel. This technique is widely employed in industries such as aerospace, automotive, and consumer goods manufacturing to produce components like cookware, lighting fixtures, and rocket nose cones. The process can be performed under different thermal conditions, primarily categorized as cold working and hot working, each imparting distinct mechanical, structural, and economic outcomes to the final product. This article provides a comprehensive comparison of cold working and hot working in metal spinning, exploring their definitions, processes, material behaviors, applications, advantages, disadvantages, and economic considerations. Detailed tables are included to summarize key differences and facilitate understanding.
1. Introduction to Metal Spinning
Metal spinning is a versatile forming process that dates back centuries, with origins in ancient craftsmanship, such as pottery wheel techniques adapted for metals. In modern industrial applications, it involves mounting a flat or cylindrical metal blank on a lathe, which rotates at high speeds. A forming tool, often a roller or a blunt instrument, applies pressure to the rotating blank, gradually shaping it over a mandrel that defines the desired geometry. The process is incremental, allowing for complex shapes to be formed without the need for extensive tooling, as in deep drawing or stamping.
The thermal conditions under which spinning is performed significantly influence the material’s behavior and the final component’s properties. Cold working occurs at or near room temperature, below the metal’s recrystallization temperature, while hot working is conducted at elevated temperatures, above the recrystallization temperature, where the metal is more malleable. These thermal regimes affect the microstructure, mechanical properties, surface finish, and dimensional accuracy of the spun parts, making the choice between cold and hot working a critical decision in manufacturing.
2. Definitions and Fundamental Principles
2.1 Cold Working in Metal Spinning
Cold working in metal spinning refers to the deformation of a metal blank at temperatures below its recrystallization temperature, typically at ambient or slightly elevated temperatures (e.g., up to 0.3 times the metal’s melting point on an absolute temperature scale). For most metals, such as aluminum, copper, and low-carbon steel, this means room temperature or slightly above. The process relies on plastic deformation, where the metal is stretched, compressed, or bent, causing permanent changes in shape without fracturing.
During cold spinning, the metal undergoes work hardening (also known as strain hardening), a phenomenon where plastic deformation increases the density of dislocations in the crystal structure. These dislocations impede further movement of atoms, enhancing the metal’s strength and hardness but reducing its ductility. Cold spinning is typically performed using manual or CNC-controlled lathes, with the forming tool applying localized pressure to shape the blank incrementally.
2.2 Hot Working in Metal Spinning
Hot working in metal spinning involves deforming the metal at temperatures above its recrystallization temperature, typically between 0.6 and 0.9 times the metal’s melting point. For example, steel is hot worked at temperatures between 1,100°C and 1,250°C, while aluminum is processed at around 400°C to 500°C. At these elevated temperatures, the metal is in a plastic state, exhibiting high ductility and low resistance to deformation.
The key feature of hot working is dynamic recrystallization, where new, strain-free grains form during deformation, preventing work hardening. This allows for large deformations without compromising the metal’s ductility, making hot spinning suitable for complex geometries. Hot spinning requires specialized equipment, such as heated mandrels or torches, to maintain the workpiece at the desired temperature throughout the process.
3. Process Mechanics and Equipment
3.1 Cold Spinning Process
In cold spinning, the metal blank is clamped onto a rotating mandrel, and a forming tool applies pressure to shape the material. The process can be manual, where a skilled operator manipulates the tool, or automated using CNC machines for precision and repeatability. The equipment typically includes:
- Lathe or Spinning Machine: A robust lathe capable of high rotational speeds (e.g., 500–2,000 RPM) and sufficient torque to handle the forces involved.
- Mandrel: A precisely machined form that defines the internal shape of the spun part, often made from hardened steel or aluminum.
- Forming Tools: Rollers or blunt tools made from tool steel or carbide, designed to withstand high contact pressures without deforming.
- Lubrication Systems: To reduce friction and heat buildup, lubricants such as oil-based compounds or synthetic greases are applied.
Cold spinning is typically performed in multiple passes, with the tool gradually shaping the blank to avoid excessive thinning or cracking. The process is well-suited for ductile metals like aluminum, copper, and brass, which can withstand significant deformation at room temperature.
3.2 Hot Spinning Process
Hot spinning requires additional considerations to manage the elevated temperatures. The blank is preheated using furnaces, induction heaters, or gas torches to reach the required temperature before spinning begins. During the process, the workpiece is maintained at a high temperature using external heat sources or heated mandrels. Key equipment includes:
- Heating Systems: Gas torches, induction coils, or infrared heaters to preheat and maintain the blank’s temperature.
- Insulated Mandrels: Mandrels designed to withstand high temperatures without deforming, often coated with refractory materials.
- High-Temperature Lubricants: Specialized lubricants, such as graphite-based compounds, to reduce friction at elevated temperatures.
- Temperature Monitoring: Thermocouples or infrared pyrometers to ensure the workpiece remains within the desired temperature range.
Hot spinning is typically faster than cold spinning due to the metal’s increased ductility, allowing for larger deformations in fewer passes. However, maintaining uniform temperature distribution is critical to prevent defects like warping or uneven grain growth.
4. Material Behavior and Microstructural Changes
4.1 Microstructural Effects of Cold Spinning
Cold spinning induces significant changes in the metal’s microstructure due to plastic deformation at low temperatures. The primary effects include:
- Work Hardening: Plastic deformation increases dislocation density, strengthening the metal but reducing its ductility. This is beneficial for applications requiring high strength but can lead to brittleness if overworked.
- Grain Distortion: The grains elongate and align in the direction of deformation, creating a fibrous texture that enhances anisotropic properties.
- Residual Stresses: Cold spinning introduces internal stresses due to non-uniform deformation, which may require post-processing (e.g., annealing) to relieve.
- Texture Development: Preferred crystallographic orientations develop, affecting mechanical properties like tensile strength and fatigue resistance.
For example, in cold-spun aluminum, the yield strength can increase by 20–50% due to work hardening, but the elongation at break may decrease significantly, limiting further forming.
4.2 Microstructural Effects of Hot Spinning
Hot spinning, conducted above the recrystallization temperature, results in different microstructural outcomes:
- Dynamic Recrystallization: New, strain-free grains form during deformation, preventing work hardening and maintaining high ductility. This results in a more uniform grain structure.
- Grain Refinement: Repeated recrystallization can refine grain size, improving mechanical properties like toughness and fatigue resistance.
- Reduced Residual Stresses: The high temperatures and recrystallization minimize internal stresses, producing parts with greater dimensional stability.
- Potential for Grain Growth: If the temperature is too high or the process is prolonged, excessive grain growth can occur, reducing strength.
For instance, hot-spun steel components exhibit refined grains and improved ductility compared to their cold-spun counterparts, making them suitable for applications requiring complex shapes and toughness.
5. Mechanical Properties of Spun Components
5.1 Cold-Spun Components
Cold spinning enhances the mechanical properties of the metal through work hardening, resulting in:
- Increased Strength and Hardness: The higher dislocation density increases tensile and yield strength. For example, cold-spun 6061 aluminum can achieve a tensile strength of 300–350 MPa compared to 150–200 MPa in the annealed state.
- Reduced Ductility: The loss of ductility limits the extent of deformation, increasing the risk of cracking during subsequent forming or service.
- Improved Fatigue Resistance: The compressive residual stresses on the surface can enhance fatigue life, beneficial for cyclic loading applications.
- Anisotropic Properties: The textured microstructure results in direction-dependent properties, which must be considered in design.
5.2 Hot-Spun Components
Hot spinning produces components with distinct mechanical characteristics:
- High Ductility: The absence of work hardening allows for greater elongation and formability, ideal for complex geometries.
- Moderate Strength: The recrystallized microstructure results in lower strength compared to cold-spun parts but higher toughness and impact resistance.
- Uniform Properties: The lack of significant residual stresses and uniform grain structure minimizes anisotropy, improving reliability.
- Potential for Surface Oxidation: High temperatures can cause scaling or oxidation, which may degrade surface properties unless controlled.
For example, hot-spun stainless steel retains excellent corrosion resistance and ductility, making it suitable for chemical processing equipment.
6. Applications of Cold and Hot Spinning
6.1 Applications of Cold Spinning
Cold spinning is widely used in industries requiring high precision, strength, and surface quality. Common applications include:
- Aerospace: Production of lightweight components like satellite dishes, radar reflectors, and aircraft nose cones, where aluminum and titanium alloys are cold spun for strength and dimensional accuracy.
- Automotive: Manufacturing of wheel rims, hubcaps, and exhaust components from steel or aluminum, leveraging cold spinning’s ability to produce smooth surfaces and tight tolerances.
- Consumer Goods: Fabrication of cookware (e.g., pots, pans), lighting reflectors, and decorative items from aluminum, copper, or brass, where aesthetic finish is critical.
- Medical Devices: Spinning of stainless steel or titanium components for surgical instruments and implants, benefiting from cold spinning’s precision and strength.
6.2 Applications of Hot Spinning
Hot spinning is preferred for applications requiring complex shapes, large deformations, or materials with low room-temperature ductility. Examples include:
- Aerospace: Forming of high-strength steel or nickel alloy components, such as turbine shrouds and rocket nozzles, which require elevated temperatures to achieve the desired geometry.
- Energy Sector: Production of large-diameter pipes, pressure vessel heads, and wind turbine components from carbon or stainless steel, where hot spinning ensures formability and toughness.
- Industrial Equipment: Manufacturing of heavy-duty components like mixing bowls, chemical reactor vessels, and centrifuge drums, often made from refractory metals or high-temperature alloys.
- Defense: Spinning of armor components or missile casings from high-strength alloys, where hot working enables the formation of thick-walled, complex shapes.
7. Advantages and Disadvantages
7.1 Advantages of Cold Spinning
- High Precision: Cold spinning achieves tight dimensional tolerances (e.g., ±0.1 mm) due to minimal thermal expansion and contraction.
- Superior Surface Finish: The absence of high-temperature oxidation results in smooth, polished surfaces, reducing the need for secondary finishing.
- Increased Strength: Work hardening enhances the mechanical properties, making cold-spun parts suitable for load-bearing applications.
- Energy Efficiency: No heating is required, reducing energy costs and simplifying the process setup.
- Material Savings: Cold spinning produces near-net-shape parts, minimizing waste compared to machining.
7.2 Disadvantages of Cold Spinning
- Limited Ductility: The reduced ductility of work-hardened metals restricts the complexity of shapes and may cause cracking.
- High Forces Required: The higher strength of the metal at room temperature necessitates robust equipment and tools, increasing capital costs.
- Residual Stresses: Internal stresses can lead to springback or distortion, requiring post-processing like annealing.
- Material Limitations: Only ductile metals (e.g., aluminum, copper, low-carbon steel) can be cold spun effectively, limiting material selection.
7.3 Advantages of Hot Spinning
- Enhanced Formability: High temperatures increase ductility, allowing for complex shapes and large deformations without cracking.
- Lower Forming Forces: The reduced yield strength at elevated temperatures requires less force, enabling the use of lighter equipment.
- Minimal Residual Stresses: Dynamic recrystallization eliminates internal stresses, improving dimensional stability.
- Wider Material Range: Hot spinning can process high-strength or brittle materials, such as stainless steel, titanium, and nickel alloys.
- Improved Toughness: The refined grain structure enhances impact resistance and fatigue life.
7.4 Disadvantages of Hot Spinning
- Surface Oxidation: High temperatures can cause scaling or oxidation, degrading surface quality and requiring additional cleaning or coating.
- Lower Precision: Thermal expansion and contraction lead to less accurate tolerances (e.g., ±0.5 mm), often necessitating post-machining.
- Energy Intensive: Heating the workpiece and maintaining temperature increases energy consumption and operational costs.
- Equipment Complexity: Specialized heating systems and high-temperature mandrels increase equipment costs and maintenance requirements.
- Grain Growth Risk: Prolonged exposure to high temperatures can cause excessive grain growth, reducing strength.
8. Economic Considerations
8.1 Cost Factors in Cold Spinning
Cold spinning is generally more cost-effective for small to medium production runs due to its simplicity and energy efficiency. Key cost factors include:
- Equipment Costs: Cold spinning lathes and tools are relatively affordable, with costs ranging from $50,000 to $500,000 for CNC systems.
- Tooling Costs: Mandrels and forming tools are durable but require precision machining, costing $1,000 to $10,000 per set.
- Labor Costs: Manual cold spinning requires skilled operators, increasing labor costs, while CNC automation reduces this expense.
- Material Costs: Ductile metals like aluminum and copper are less expensive than high-strength alloys, keeping material costs low.
- Post-Processing: Annealing or stress-relieving may be needed to address residual stresses, adding $0.50–$2.00 per part.
8.2 Cost Factors in Hot Spinning
Hot spinning is more capital-intensive due to the need for heating systems and specialized equipment. Cost considerations include:
- Equipment Costs: Hot spinning systems, including furnaces and high-temperature mandrels, range from $100,000 to $1 million.
- Energy Costs: Preheating and maintaining workpiece temperature can consume 10–50 kWh per part, significantly increasing operational costs.
- Tooling Costs: High-temperature mandrels and tools are more expensive, costing $5,000 to $50,000 due to refractory materials and coatings.
- Labor Costs: Hot spinning often requires automation to maintain temperature control, reducing labor costs but increasing setup complexity.
- Post-Processing: Surface cleaning to remove oxides or machining to achieve tolerances adds $1.00–$5.00 per part.
8.3 Economic Comparison
Cold spinning is preferred for high-volume production of simple, precise parts due to lower energy and equipment costs. Hot spinning is more economical for low-volume, complex parts made from high-strength materials, where formability is critical. The breakeven point depends on production volume, material type, and part complexity, typically favoring cold spinning for volumes above 1,000 units and hot spinning for volumes below 500 units.
9. Comparison Tables
The following tables summarize the key differences between cold and hot spinning across various parameters, providing a concise reference for engineers, manufacturers, and researchers.
Table 1: Process Characteristics
Parameter | Cold Spinning | Hot Spinning |
---|---|---|
Temperature | Below recrystallization temperature (e.g., 20–100°C for aluminum) | Above recrystallization temperature (e.g., 400–500°C for aluminum, 1,100–1,250°C for steel) |
Equipment | Standard lathe, CNC spinning machine, durable mandrels | Heated lathe, furnaces, high-temperature mandrels, temperature monitoring systems |
Forming Forces | High due to higher yield strength at room temperature | Low due to reduced yield strength at elevated temperatures |
Process Speed | Slower due to multiple passes to avoid cracking | Faster due to increased ductility and fewer passes |
Lubrication | Oil-based or synthetic lubricants | High-temperature lubricants (e.g., graphite-based) |
Table 2: Material and Microstructural Effects
Parameter | Cold Spinning | Hot Spinning |
---|---|---|
Work Hardening | Significant, increases strength and hardness | Absent due to dynamic recrystallization |
Grain Structure | Elongated, distorted, anisotropic | Recrystallized, refined, more isotropic |
Residual Stresses | High, may cause springback or distortion | Low, improved dimensional stability |
Texture Development | Pronounced, affects mechanical properties | Minimal, uniform properties |
Grain Size | Reduced due to fragmentation | Refined but risk of growth if overheated |
Table 3: Mechanical Properties
Parameter | Cold Spinning | Hot Spinning |
---|---|---|
Tensile Strength | Increased (e.g., 300–350 MPa for 6061 aluminum) | Moderate, lower than cold-spun (e.g., 200–250 MPa for 6061 aluminum) |
Ductility | Reduced, higher risk of cracking | High, allows complex shapes |
Hardness | Increased due to work hardening | Lower, maintained by recrystallization |
Fatigue Resistance | Improved by compressive surface stresses | Moderate, depends on grain refinement |
Anisotropy | Significant, direction-dependent properties | Minimal, more uniform properties |
Table 4: Applications and Suitability
Parameter | Cold Spinning | Hot Spinning |
---|---|---|
Typical Materials | Aluminum, copper, brass, low-carbon steel | Stainless steel, titanium, nickel alloys, high-strength steel |
Applications | Cookware, wheel rims, satellite dishes, medical devices | Turbine shrouds, rocket nozzles, pressure vessels, large pipes |
Shape Complexity | Limited to simpler geometries due to reduced ductility | Suitable for complex, thick-walled shapes |
Production Volume | High-volume, cost-effective for simple parts | Low-volume, suitable for specialized components |
Industry Sectors | Automotive, consumer goods, aerospace (lightweight parts) | Aerospace (high-strength parts), energy, defense |
Table 5: Economic and Operational Considerations
Parameter | Cold Spinning | Hot Spinning |
---|---|---|
Equipment Cost | $50,000–$500,000 | $100,000–$1,000,000 |
Energy Consumption | Low, no heating required | High, 10–50 kWh per part for heating |
Tooling Cost | $1,000–$10,000 per mandrel set | $5,000–$50,000 per high-temperature mandrel set |
Labor Requirements | Skilled operators for manual, moderate for CNC | Automated systems preferred, higher setup complexity |
Post-Processing | Annealing for stress relief ($0.50–$2.00/part) | Surface cleaning, machining ($1.00–$5.00/part) |
10. Case Studies and Practical Examples
10.1 Cold Spinning: Automotive Wheel Rims
In the automotive industry, cold spinning is widely used to produce aluminum wheel rims. The process begins with a flat aluminum blank (e.g., 6061 alloy), which is spun over a mandrel to form the rim’s profile. The cold spinning process enhances the rim’s strength through work hardening, achieving a tensile strength of 300–350 MPa, compared to 150–200 MPa for the annealed material. The smooth surface finish eliminates the need for extensive polishing, and tight tolerances (±0.1 mm) ensure compatibility with tires. However, the reduced ductility requires careful control to prevent cracking, and residual stresses may necessitate stress-relieving heat treatment.
10.2 Hot Spinning: Aerospace Rocket Nozzles
Hot spinning is critical in aerospace for forming rocket nozzles from high-strength alloys like Inconel or titanium. The process involves preheating the blank to 1,000–1,200°C and spinning it over a mandrel to create a conical or bell-shaped nozzle. The high temperature ensures sufficient ductility to form complex geometries without cracking, and dynamic recrystallization produces a refined grain structure, enhancing toughness. However, the process is energy-intensive, and surface oxidation requires post-spinning cleaning or coating. The lower precision (±0.5 mm) often necessitates machining to achieve final dimensions.
11. Future Trends and Innovations
11.1 Advances in Cold Spinning
Recent advancements in cold spinning focus on automation and material efficiency. CNC spinning machines with real-time force and displacement monitoring improve repeatability and reduce operator skill requirements. Hybrid processes, combining spinning with other techniques like flow forming, enhance dimensional accuracy and allow for thinner walls, reducing material costs. Additionally, the development of high-strength, ductile alloys, such as advanced aluminum-lithium alloys, expands the range of materials suitable for cold spinning.
11.2 Advances in Hot Spinning
Hot spinning is benefiting from innovations in heating and temperature control. Induction heating systems provide rapid, localized heating, reducing energy consumption and improving temperature uniformity. Advanced refractory coatings for mandrels extend tool life, lowering costs. Furthermore, the integration of simulation software, such as finite element analysis (FEA), allows engineers to predict material flow, temperature distribution, and potential defects, optimizing process parameters before production.
11.3 Sustainability Considerations
Both cold and hot spinning are evolving to address sustainability concerns. Cold spinning’s energy efficiency and minimal waste make it inherently sustainable, but efforts are underway to use recycled metals and biodegradable lubricants. Hot spinning, while energy-intensive, is adopting renewable energy sources and heat recovery systems to reduce its carbon footprint. Both processes are increasingly aligned with circular economy principles, emphasizing material reuse and lifecycle management.
12. Conclusion
Cold working and hot working in metal spinning represent two distinct approaches to forming axially symmetric parts, each with unique advantages and challenges. Cold spinning excels in producing high-strength, precise components with excellent surface finish, making it ideal for applications in automotive, consumer goods, and aerospace industries. However, its limitations in ductility and higher forming forces restrict its use to simpler shapes and ductile materials. Hot spinning, conversely, offers superior formability and the ability to process high-strength alloys, enabling the creation of complex, robust components for aerospace, energy, and defense applications. Its drawbacks include higher energy costs, lower precision, and surface quality issues due to oxidation.
The choice between cold and hot spinning depends on factors such as material type, part complexity, production volume, and cost constraints. By understanding the process mechanics, material behavior, and economic implications, manufacturers can select the most appropriate method for their needs. The detailed comparison tables provided in this article serve as a valuable resource for decision-making, highlighting the trade-offs and synergies between these techniques. As advancements in automation, materials, and sustainability continue to shape the field, both cold and hot spinning will remain integral to modern manufacturing, driving innovation and efficiency in metal forming.
Maximize Tooling and CNC Metal Spinning Capabilities.
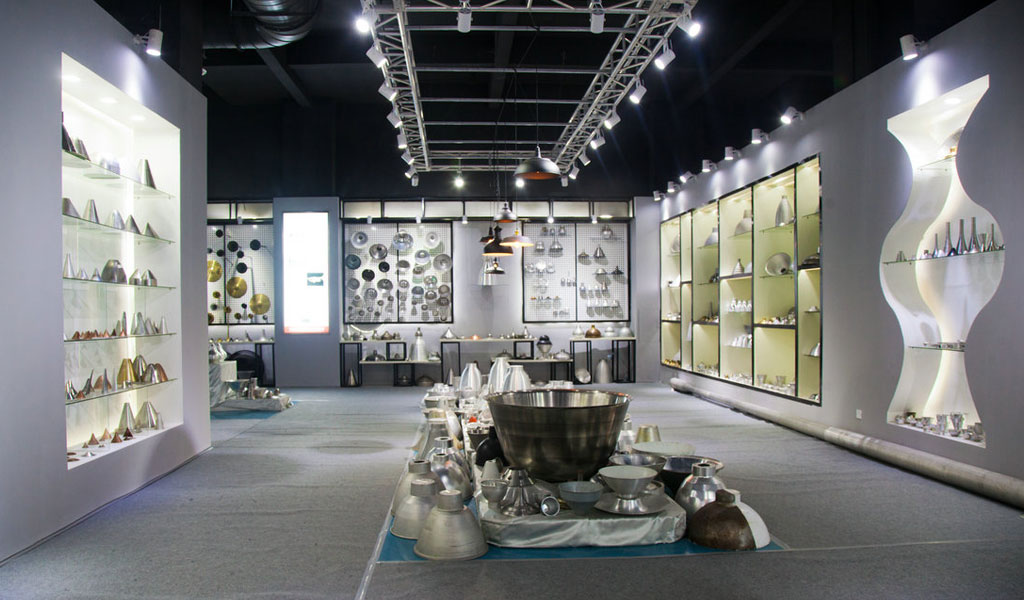
At BE-CU China Metal Spinning company, we make the most of our equipment while monitoring signs of excess wear and stress. In addition, we look into newer, modern equipment and invest in those that can support or increase our manufacturing capabilities. Our team is very mindful of our machines and tools, so we also routinely maintain them to ensure they don’t negatively impact your part’s quality and productivity.
Talk to us today about making a rapid prototype with our CNC metal spinning service. Get a direct quote by chatting with us here or request a free project review.
BE-CU China CNC Metal Spinning service include : CNC Metal Spinning,Metal Spinning Die,Laser Cutting, Tank Heads Spinning,Metal Hemispheres Spinning,Metal Cones Spinning,Metal Dish-Shaped Spinning,Metal Trumpet Spinning,Metal Venturi Spinning,Aluminum Spinning Products,Stainless Steel Spinning Products,Copper Spinning Products,Brass Spinning Products,Steel Spinning Product,Metal Spinnin LED Reflector,Metal Spinning Pressure Vessel,