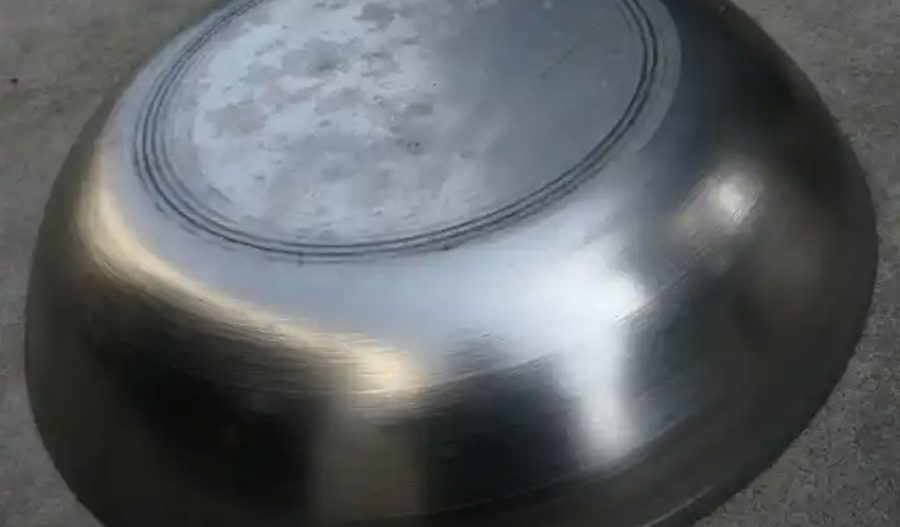
Spinning, also known as spin forming or metal spinning, is a metalworking process used to form axially symmetric parts by rotating a metal blank or tube at high speed while applying localized pressure with a tool. This technique has been employed for centuries in various industries, from aerospace to automotive, and has gained significant traction in the manufacturing of high-speed rail (HSR) components due to its precision, cost-effectiveness, and ability to produce lightweight, high-strength parts. In the context of high-speed rail, spinning is critical for fabricating components such as wheelsets, axles, and structural elements that must withstand extreme dynamic loads, high speeds, and stringent safety requirements.
High-speed rail systems, defined as rail transport networks with trains operating at speeds exceeding 200 km/h (124 mph) on upgraded tracks or 250 km/h (155 mph) on new tracks, demand components that balance durability, weight, and aerodynamic efficiency. Spinning addresses these needs by enabling the production of seamless, high-precision parts with excellent mechanical properties. This article explores the role of spinning in HSR part manufacturing, delving into its principles, applications, technological advancements, and comparative advantages over other manufacturing methods. It also examines global case studies, material considerations, quality control, and future trends, supported by detailed tables comparing spinning with alternative techniques.
Historical Context of Spinning in Rail Manufacturing
The origins of metal spinning trace back to ancient civilizations, where artisans used rudimentary tools to shape metals into vessels and decorative items. However, its industrial application began in the 19th century with the advent of mechanized lathes and the growing demand for precision components during the Industrial Revolution. In rail manufacturing, spinning initially played a minor role, primarily for producing small, symmetrical parts like fittings and connectors. The rise of high-speed rail in the 20th century, starting with Japan’s Tōkaidō Shinkansen in 1964, marked a turning point, as the need for lightweight, high-strength components drove advancements in spinning technology.
By the late 20th century, computer numerical control (CNC) spinning machines revolutionized the process, enabling greater precision and repeatability. In HSR manufacturing, spinning became integral for producing components like wheel rims, axle hubs, and even sections of bogie frames. Countries like Japan, France, Germany, and China, which lead in HSR development, adopted spinning to meet the rigorous demands of trains operating at speeds up to 350 km/h (217 mph) or higher. Today, spinning is a cornerstone of HSR part production, supported by innovations in materials, automation, and quality assurance.
Principles of Metal Spinning
Basic Mechanics of Spinning
Metal spinning involves rotating a metal blank, typically a flat disc or a cylindrical tube, at high speed on a lathe or spinning machine. A tool, often a roller or forming tool, applies controlled pressure to deform the metal incrementally, shaping it over a mandrel or form that defines the final geometry. The process can be performed hot or cold, depending on the material and desired properties. Cold spinning, more common in HSR applications, enhances material strength through work hardening, while hot spinning is used for materials with low ductility or complex shapes.
The spinning process is divided into two main types: conventional spinning and shear spinning. Conventional spinning maintains the blank’s thickness while stretching it over the mandrel, ideal for producing thin-walled, seamless parts like wheel rims. Shear spinning, also known as power spinning, reduces the blank’s thickness while maintaining its diameter, suitable for creating thicker, high-strength components like axle hubs. Both methods are used in HSR manufacturing, depending on the part’s requirements.
Key Parameters in Spinning
Several parameters influence the spinning process, including rotational speed, tool feed rate, tool geometry, and material properties. Rotational speed, typically ranging from 500 to 2,000 RPM, affects the material’s flow and surface finish. Higher speeds reduce forming time but may cause excessive heat or vibration, impacting precision. Tool feed rate, measured in mm/rev, determines the rate of deformation and must be optimized to avoid defects like wrinkling or cracking. Tool geometry, including roller radius and angle, influences the contact area and forming forces, critical for achieving tight tolerances in HSR parts.
Material properties, such as ductility, yield strength, and strain hardening behavior, are pivotal. Common materials in HSR spinning include high-strength steels, aluminum alloys, and titanium alloys, each requiring specific spinning conditions. For example, aluminum alloys, used for lightweight wheel components, are spun at lower forces due to their high ductility, while high-strength steels, used for axles, require higher forces and sometimes hot spinning to prevent cracking.
Equipment and Tooling
Modern spinning machines for HSR manufacturing are highly automated, featuring CNC controls, multi-axis tool paths, and real-time monitoring systems. These machines range from small, single-spindle lathes for producing fittings to large, heavy-duty machines capable of spinning parts up to 2 meters in diameter. Tooling includes mandrels, rollers, and tailstocks, designed to withstand high forces and maintain dimensional accuracy. Mandrels are typically made of hardened steel or composites to resist wear, while rollers are coated with materials like carbide or ceramic to reduce friction and extend tool life.
Applications of Spinning in High-Speed Rail Manufacturing
Wheelsets and Axles
Wheelsets, comprising wheels and axles, are among the most critical HSR components, as they bear the train’s weight, transmit traction, and ensure stability at high speeds. Spinning is widely used to manufacture wheel rims and axle hubs due to its ability to produce seamless, high-strength parts with uniform grain structure. For wheels, conventional spinning forms the rim from a flat steel or aluminum disc, creating a lightweight, fatigue-resistant component. Shear spinning is used for axle hubs, reducing thickness to optimize weight while maintaining strength.
The advantages of spinning for wheelsets include reduced material waste, improved mechanical properties, and the ability to produce complex geometries without welds, which are potential failure points. For example, the CRH380A train, used in China’s HSR network, features spun wheel rims made from high-strength steel, achieving a weight reduction of 15% compared to forged wheels while meeting safety standards.
Bogie Components
Bogies, the chassis that support wheelsets and connect the train to the track, require components like pivot pins, suspension housings, and structural rings, many of which are produced via spinning. These parts must withstand dynamic loads, vibrations, and thermal stresses, making spinning’s ability to enhance material strength through work hardening particularly valuable. For instance, suspension housings are spun from aluminum alloys to reduce weight, while pivot pins are spun from high-strength steel for durability.
Spinning enables the production of bogie components with precise tolerances, critical for maintaining alignment and stability at speeds exceeding 300 km/h. The seamless nature of spun parts also reduces the risk of fatigue cracks, a common issue in welded or cast components.
Structural and Aerodynamic Components
HSR trains operate in high-drag environments, necessitating aerodynamic components like nose cones, fairings, and structural tubes. Spinning is used to produce these parts from lightweight materials like aluminum or titanium alloys, ensuring smooth surfaces and complex curvatures that minimize air resistance. For example, the nose cone of Japan’s Shinkansen N700 series is spun from an aluminum alloy, achieving a streamlined shape that reduces drag by 10% compared to earlier designs.
Structural tubes, used in the train’s frame or pantograph supports, are also spun to achieve high strength-to-weight ratios. These tubes are often produced via tube spinning, a variant of the process where a cylindrical blank is rotated and formed into a thinner, longer tube. This method is cost-effective and produces parts with excellent surface finish, reducing the need for secondary machining.
Materials Used in Spinning for HSR Parts
High-Strength Steels
High-strength steels, such as AISI 4340 or EN 36NiCrMo4, are the backbone of HSR wheelsets and axles due to their excellent fatigue resistance, toughness, and ability to withstand high dynamic loads. These steels are typically spun cold to enhance strength through work hardening, with yield strengths reaching 1,000 MPa or higher after processing. Hot spinning is used for thicker sections or when forming complex geometries to prevent cracking.
The challenge with high-strength steels is their limited ductility, which requires precise control of spinning parameters. Advances in alloy design, such as microalloying with vanadium or niobium, have improved ductility without sacrificing strength, making these materials more amenable to spinning.
Aluminum Alloys
Aluminum alloys, particularly the 6000 and 7000 series (e.g., 6061-T6, 7075-T6), are used for lightweight components like wheel rims, bogie housings, and aerodynamic fairings. These alloys offer high strength-to-weight ratios, corrosion resistance, and excellent formability, making them ideal for cold spinning. Spun aluminum parts can achieve weight reductions of up to 30% compared to steel equivalents, a critical factor in improving HSR energy efficiency.
The spinning of aluminum alloys requires lower forces than steel, but care must be taken to avoid surface defects like orange peel or galling. Lubricants and ceramic-coated rollers are commonly used to minimize friction and ensure a smooth finish.
Titanium Alloys
Titanium alloys, such as Ti-6Al-4V, are used in high-performance HSR components like suspension pins or aerodynamic fittings, where strength, weight, and corrosion resistance are paramount. These alloys are typically spun hot due to their low ductility at room temperature, with temperatures ranging from 800°C to 1,000°C. Hot spinning enhances formability and allows the production of complex shapes, but it requires specialized equipment to maintain temperature control and prevent oxidation.
The high cost of titanium limits its use to critical components, but its adoption is growing in premium HSR systems, such as Germany’s ICE 4, where weight reduction and durability are prioritized.
Emerging Materials
Emerging materials like magnesium alloys and advanced composites are being explored for HSR spinning, though their use is limited by cost and processing challenges. Magnesium alloys, such as AZ31, offer even lower densities than aluminum but require hot spinning due to their hexagonal crystal structure, which limits ductility. Composites, while not traditionally spun, are being integrated into hybrid spinning processes where metal-composite blanks are formed to combine the strength of metals with the lightweight properties of fibers.
Technological Advancements in Spinning for HSR
CNC and Automation
The integration of CNC technology has transformed spinning from a labor-intensive craft to a highly automated, precise manufacturing process. CNC spinning machines allow for complex tool paths, real-time adjustments, and multi-axis control, enabling the production of intricate HSR parts with tolerances as tight as ±0.05 mm. Automation, including robotic loading/unloading and in-process monitoring, has reduced cycle times and improved consistency, critical for high-volume HSR production.
For example, China’s CRRC Corporation uses fully automated CNC spinning lines to produce wheel rims for the Fuxing series trains, achieving a production rate of 10,000 units per year with minimal human intervention. These systems incorporate sensors to monitor parameters like tool wear, temperature, and vibration, ensuring quality and reducing defects.
Simulation and Modeling
Finite element analysis (FEA) and computational fluid dynamics (CFD) are used to simulate the spinning process, optimizing parameters like tool path, feed rate, and material flow before production begins. These tools predict defects like wrinkling, thinning, or cracking, allowing engineers to adjust designs and process conditions. For HSR parts, FEA is particularly valuable for ensuring that spun components meet dynamic load requirements, such as those encountered at 350 km/h.
Simulation also aids in material selection and mandrel design, reducing trial-and-error costs. For instance, Japan’s Kawasaki Heavy Industries uses FEA to model the spinning of Shinkansen wheel rims, ensuring uniform thickness and stress distribution under high-speed conditions.
Hybrid Spinning Processes
Hybrid spinning processes, combining spinning with other techniques like forging or additive manufacturing, are emerging as a way to enhance part performance. For example, flow forming, a hybrid of spinning and extrusion, is used to produce ultra-thin, high-strength axle tubes by simultaneously spinning and elongating a tubular blank. This process achieves thickness reductions of up to 80%, significantly reducing weight.
Additive manufacturing is also being integrated, where a 3D-printed preform is spun to achieve final geometry, combining the flexibility of additive processes with the strength enhancement of spinning. These hybrid approaches are still in development but show promise for next-generation HSR components.
Quality Control and Standards in Spinning
Non-Destructive Testing (NDT)
Quality control is paramount in HSR manufacturing, given the safety-critical nature of components. Spun parts undergo rigorous non-destructive testing (NDT), including ultrasonic testing, magnetic particle inspection, and X-ray radiography, to detect defects like cracks, inclusions, or voids. Ultrasonic testing is particularly effective for wheelsets, as it can identify subsurface flaws that could lead to fatigue failure at high speeds.
For example, the European standard EN 13261 specifies NDT requirements for HSR axles, mandating ultrasonic testing to ensure a defect-free microstructure. Spinning’s ability to produce seamless parts reduces the likelihood of weld-related defects, but NDT remains essential to verify material integrity.
Dimensional Accuracy and Surface Finish
Spun HSR parts must meet stringent dimensional tolerances, often within ±0.1 mm, to ensure proper fit and function. Coordinate measuring machines (CMM) and laser scanning are used to verify geometry, while profilometers assess surface finish, which affects fatigue life and aerodynamic performance. A typical surface roughness target for spun wheel rims is Ra 1.6 µm or better, achieved through optimized tool paths and lubrication.
Material Certification and Traceability
Materials used in HSR spinning must comply with international standards, such as ISO 6892 for tensile testing or ASTM E8 for metallic materials. Certification ensures that raw materials meet specifications for strength, ductility, and chemical composition. Traceability, achieved through batch numbering and digital records, allows manufacturers to track materials from raw stock to finished part, critical for quality assurance and regulatory compliance.
Comparative Analysis of Spinning vs. Other Manufacturing Methods
Spinning competes with forging, casting, and machining for HSR part production, each with distinct advantages and limitations. The following sections compare these methods, supported by detailed tables.
Spinning vs. Forging
Forging involves compressing metal under high pressure to form parts, offering excellent strength and grain alignment. It is widely used for HSR axles and wheel hubs but is more expensive and material-intensive than spinning. Spinning, by contrast, is more cost-effective for seamless, axially symmetric parts and allows greater flexibility in wall thickness.
Table 1: Comparison of Spinning and Forging for HSR Parts
Parameter | Spinning | Forging |
---|---|---|
Material Efficiency | High (minimal waste, up to 90% material utilization) | Moderate (30-40% material loss due to flash and trimming) |
Strength | High (work hardening enhances strength, yield strength up to 1,000 MPa) | Very High (uniform grain flow, yield strength up to 1,200 MPa) |
Cost | Moderate (lower tooling and setup costs) | High (expensive dies and high-energy presses) |
Production Rate | Moderate (1-5 parts/hour for complex parts) | Low (1-3 parts/hour due to multiple steps) |
Geometry Flexibility | High (ideal for axially symmetric parts, complex curvatures) | Moderate (limited to simpler shapes without secondary machining) |
Surface Finish | Good (Ra 1.6 µm achievable with polishing) | Moderate (Ra 3.2 µm, requires machining) |
Applications in HSR | Wheel rims, axle hubs, suspension housings, aerodynamic fairings | Axles, wheel hubs, bogie frames |
Spinning vs. Casting
Casting involves pouring molten metal into a mold to form parts, suitable for complex geometries but prone to defects like porosity or shrinkage. Spinning produces seamless parts with superior mechanical properties, making it preferable for safety-critical HSR components. However, casting is more cost-effective for large, non-symmetric parts like bogie frames.
Table 2: Comparison of Spinning and Casting for HSR Parts
Parameter | Spinning | Casting |
---|---|---|
Material Efficiency | High (near-net-shape forming, minimal waste) | Low (significant waste from sprues, runners, and risers) |
Strength | High (seamless, work-hardened structure) | Moderate (potential for porosity, inclusions; yield strength 500-800 MPa) |
Cost | Moderate (lower for small batches) | Low (economical for large volumes, high tooling costs) |
Production Rate | Moderate (depends on part complexity) | High (multiple parts per mold cycle) |
Geometry Flexibility | Moderate (limited to axially symmetric shapes) | High (complex shapes possible with intricate molds) |
Surface Finish | Good (smooth Surfaces, minimal post-processing) | Poor (requires machining or polishing, Ra 6.3 µm typical) |
Applications in HSR | Wheel rims, axle hubs, structural tubes | Bogie frames, motor housings, non-critical fittings |
Spinning vs. Machining
Machining removes material from a blank to achieve the desired shape, offering high precision but significant material waste. Spinning is more material-efficient and faster for symmetric parts, though machining is preferred for non-symmetric components or when ultra-tight tolerances are required.
Table 3: Comparison of Spinning and Machining for HSR Parts
Parameter | Spinning | Machining |
---|---|---|
Material Efficiency | High (near-net-shape, minimal scrap) | Low (50-70% material removal as chips) |
Strength | High (work hardening improves properties) | Moderate (no strengthening, potential for stress concentrations) |
Cost | Moderate (lower for symmetric parts) | High (labor-intensive, high tooling costs) |
Production Rate | Moderate (faster for repetitive parts) | Low (time-consuming for complex geometries) |
Geometry Flexibility | Moderate (axially symmetric parts only) | High (suitable for any geometry with proper tooling) |
Surface Finish | Good (Ra 1.6 µm, minimal post-processing) | Excellent (Ra 0.8 µm or better with finishing) |
Applications in HSR | Wheel rims, axle hubs, aerodynamic fairings | Gear teeth, bearing surfaces, non-symmetric fittings |
Global Case Studies of Spinning in HSR Manufacturing
Japan: Shinkansen Wheel Rim Production
Japan’s Shinkansen, the world’s first HSR system, relies heavily on spinning for wheel rim production. Kawasaki Heavy Industries, a key supplier, uses CNC spinning to produce wheel rims from high-strength steel (e.g., JIS SSW-Q1R), achieving a thickness variation of less than 0.1 mm. The process involves cold spinning a flat disc over a mandrel, followed by heat treatment to enhance fatigue resistance. These rims are critical for maintaining stability at speeds up to 320 km/h, with a service life exceeding 1 million km.
The use of spinning has reduced wheel weight by 12% compared to forged alternatives, improving energy efficiency and reducing track wear. Japan’s rigorous quality standards, including ultrasonic testing and fatigue analysis, ensure that spun rims meet safety requirements under extreme conditions.
China: CRH380A Axle Hubs
China, with the world’s largest HSR network (over 38,000 km as of 2025), uses spinning extensively for axle hub production. CRRC Corporation employs shear spinning to form axle hubs from AISI 4340 steel, reducing thickness by up to 50% while maintaining a yield strength of 1,100 MPa. The process is fully automated, with CNC machines monitoring tool forces and material flow in real time.
Spinning has enabled CRRC to produce axle hubs at a 20% lower cost than forging, with a production rate of 15,000 units annually. The seamless structure of spun hubs eliminates weld-related defects, contributing to the reliability of trains like the CRH380A, which operates at 380 km/h.
Germany: ICE 4 Suspension Housings
Germany’s ICE 4 trains, manufactured by Siemens Mobility, feature spun aluminum suspension housings that reduce weight by 25% compared to cast equivalents. The housings are produced via conventional spinning of 6061-T6 aluminum, achieving a wall thickness of 3-5 mm and a surface finish of Ra 1.2 µm. The process is optimized using FEA to minimize thinning and ensure uniform stress distribution.
Spinning’s cost-effectiveness and ability to produce lightweight, seamless parts have made it a preferred method for Siemens, particularly for components requiring high corrosion resistance and fatigue life. The ICE 4’s suspension housings undergo rigorous NDT, including X-ray radiography, to ensure defect-free performance at speeds up to 250 km/h.
Economic and Environmental Impacts of Spinning in HSR
Cost Efficiency
Spinning offers significant cost advantages over forging and casting, particularly for small to medium batch sizes. The process requires simpler tooling, with mandrels costing 50-70% less than forging dies or casting molds. Material efficiency, with utilization rates exceeding 90%, reduces raw material costs, a critical factor given the high price of HSR-grade steels and alloys. For example, China’s CRRC reports a 15-20% cost reduction in wheel rim production compared to forging, translating to millions of dollars in savings across its HSR fleet.
Automation further enhances cost efficiency by reducing labor costs and cycle times. A typical CNC spinning line can produce a wheel rim in 5-10 minutes, compared to 20-30 minutes for forging, enabling higher throughput and scalability.
Environmental Benefits
Spinning is an environmentally friendly process due to its high material efficiency and low energy consumption. Unlike casting, which requires melting large volumes of metal, spinning is typically performed cold, reducing energy use by 60-80%. The seamless nature of spun parts also eliminates the need for welding, which consumes energy and produces emissions.
The lightweight components produced via spinning contribute to HSR’s energy efficiency, reducing fuel consumption and greenhouse gas emissions. For instance, a 15% weight reduction in wheelsets can improve train efficiency by 5-7%, a significant impact given the high energy demands of trains operating at 350 km/h. Additionally, spun parts are fully recyclable, aligning with the sustainability goals of modern HSR systems.
Challenges and Limitations
Despite its advantages, spinning has limitations. It is restricted to axially symmetric parts, limiting its applicability to non-symmetric components like gear housings or complex bogie frames. The process also requires skilled operators and precise parameter control to avoid defects, increasing setup costs for small runs. For high-strength materials like titanium, hot spinning adds complexity and cost due to the need for specialized equipment and controlled atmospheres.
Defects like wrinkling, thinning, or cracking can occur if parameters are not optimized, necessitating advanced simulation and quality control. Finally, while spinning is cost-effective for small to medium batches, casting or forging may be more economical for very large volumes due to their higher production rates.
Future Trends in Spinning for HSR Manufacturing
Advanced Materials and Alloys
The development of new alloys, such as ultra-high-strength steels (UHSS) and next-generation aluminum-lithium alloys, is expanding the capabilities of spinning. UHSS, with yield strengths exceeding 1,500 MPa, offers superior strength for wheelsets and axles, while aluminum-lithium alloys, with densities reductions of 10% compared to traditional aluminum, enhance weight savings. These materials require advanced spinning techniques, such as laser-assisted heating or hybrid forming, to overcome ductility limitations.
Industry 4.0 Integration
The integration of Industry 4.0 technologies, including IoT, AI, and digital twins, is transforming spinning for HSR. IoT sensors monitor machine performance and part quality in real time, reducing downtime and defects. AI algorithms optimize spinning parameters, predicting defects and adjusting tool paths dynamically. Digital twins, virtual replicas of spinning machines and parts, enable predictive maintenance and process optimization, improving efficiency and reliability.
For example, Siemens Mobility is piloting AI-driven spinning lines for ICE 4 components, achieving a 10% reduction in cycle time and a 15% improvement in quality consistency. These technologies are expected to become standard in HSR manufacturing by 2030.
Sustainability and Circular Economy
The push for sustainability is driving innovations in spinning, such as the use of recycled materials and energy-efficient processes. Recycled aluminum and steel, with properties comparable to virgin materials, are being spun into HSR components, reducing environmental impact. Energy-efficient spinning machines, equipped with regenerative braking and variable-speed drives, further lower energy consumption.
The circular economy is also influencing spinning, with manufacturers designing parts for easy disassembly and recycling at end-of-life. Spun components, being seamless and free of welds, are easier to recycle than welded or cast parts, supporting HSR’s role in sustainable transportation.
Hypersonic and Maglev Applications
As HSR evolves toward hypersonic (speeds above 600 km/h) and maglev (magnetic levitation) systems, spinning is adapting to meet new demands. Maglev trains, like China’s 600 km/h prototype, require ultra-lightweight, high-precision components to minimize magnetic interference and maximize efficiency. Spinning is being used to produce levitation chassis components and aerodynamic fairings from advanced alloys, leveraging its ability to achieve tight tolerances and smooth surfaces.
Hypersonic trains, still in development, will require components capable of withstanding extreme thermal and dynamic loads. Hot spinning of titanium and nickel-based alloys is being explored to produce these parts, with research focusing on high-temperature forming and surface coatings to enhance durability.
Conclusion
Spinning is a cornerstone of high-speed rail manufacturing, enabling the production of lightweight, high-strength, and seamless components critical for safety, efficiency, and performance. Its applications in wheelsets, axles, bogie components, and aerodynamic parts demonstrate its versatility and economic advantages. Compared to forging, casting, and machining, spinning offers superior material efficiency, cost-effectiveness, and mechanical properties for axially symmetric parts, though it is limited by geometric constraints and material challenges.
Global leaders like Japan, China, and Germany have leveraged spinning to advance their HSR systems, supported by innovations in CNC automation, simulation, and hybrid processes. As HSR evolves toward higher speeds and greater sustainability, spinning will continue to play a pivotal role, driven by advancements in materials, Industry 4.0 technologies, and circular economy principles. The future of spinning in HSR manufacturing is bright, with potential applications in hypersonic and maglev systems promising to push the boundaries of rail transportation.
Maximize Tooling and CNC Metal Spinning Capabilities.
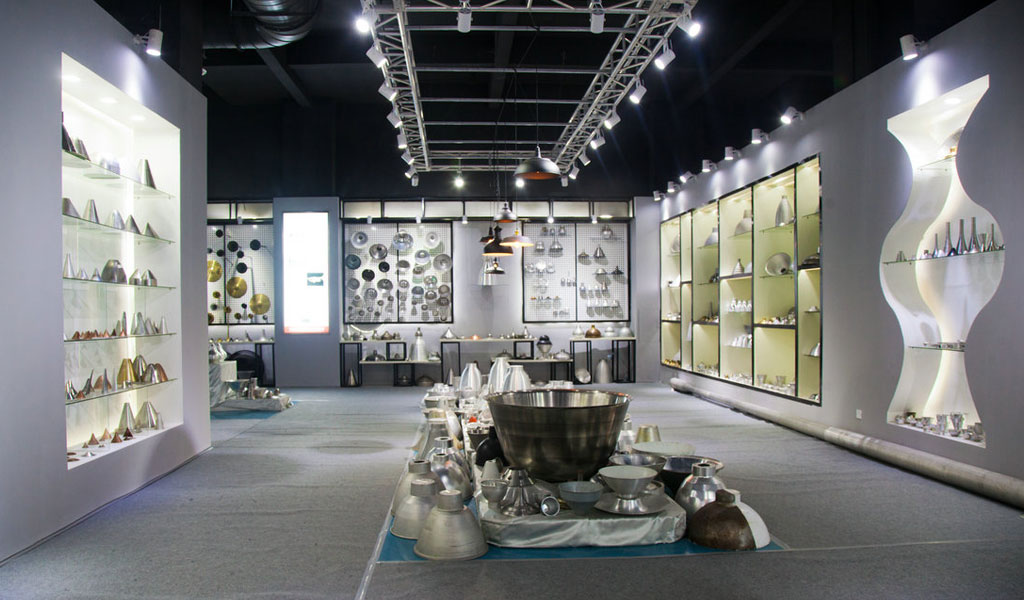
At BE-CU China Metal Spinning company, we make the most of our equipment while monitoring signs of excess wear and stress. In addition, we look into newer, modern equipment and invest in those that can support or increase our manufacturing capabilities. Our team is very mindful of our machines and tools, so we also routinely maintain them to ensure they don’t negatively impact your part’s quality and productivity.
Talk to us today about making a rapid prototype with our CNC metal spinning service. Get a direct quote by chatting with us here or request a free project review.
BE-CU China CNC Metal Spinning service include : CNC Metal Spinning,Metal Spinning Die,Laser Cutting, Tank Heads Spinning,Metal Hemispheres Spinning,Metal Cones Spinning,Metal Dish-Shaped Spinning,Metal Trumpet Spinning,Metal Venturi Spinning,Aluminum Spinning Products,Stainless Steel Spinning Products,Copper Spinning Products,Brass Spinning Products,Steel Spinning Product,Metal Spinnin LED Reflector,Metal Spinning Pressure Vessel,