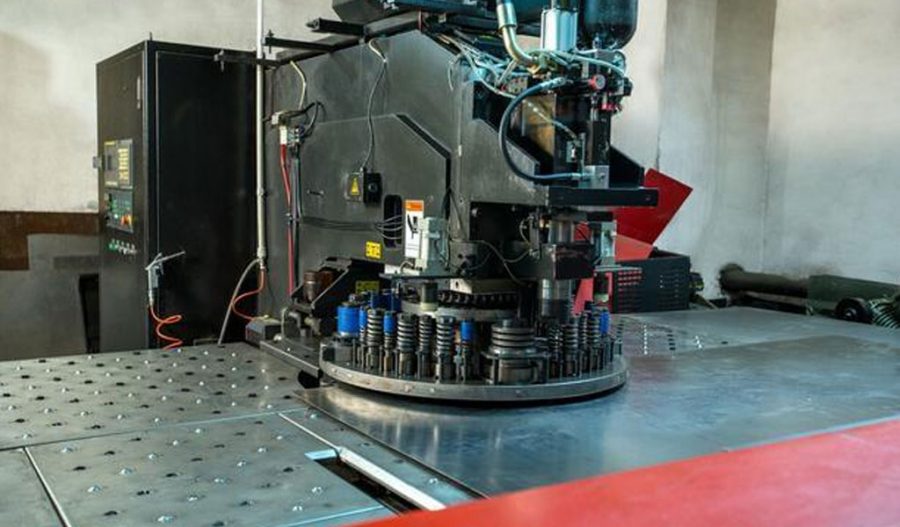
Plastic forming is an important branch in the field of manufacturing within the discipline of mechanical engineering. It utilizes the plasticity of materials, typically applying force through molds, to induce plastic deformation and shape raw materials or parts into required dimensions and shapes. Plastic forming can produce workpieces of various sizes and shapes, and through plastic deformation, it can improve material structure and enhance performance, embodying a dual function of “forming and modifying.” It is a significant method for shaping raw materials or parts. Plastic processing reflects a country’s capabilities and levels in basic and advanced manufacturing. Developing plastic processing technology plays a crucial role in enhancing the core competitiveness of China’s manufacturing industry, ensuring the development of transportation, energy, and national defense security, and promoting rapid economic growth.
The development of plastic forming technology promotes the rapid development of the national economy.
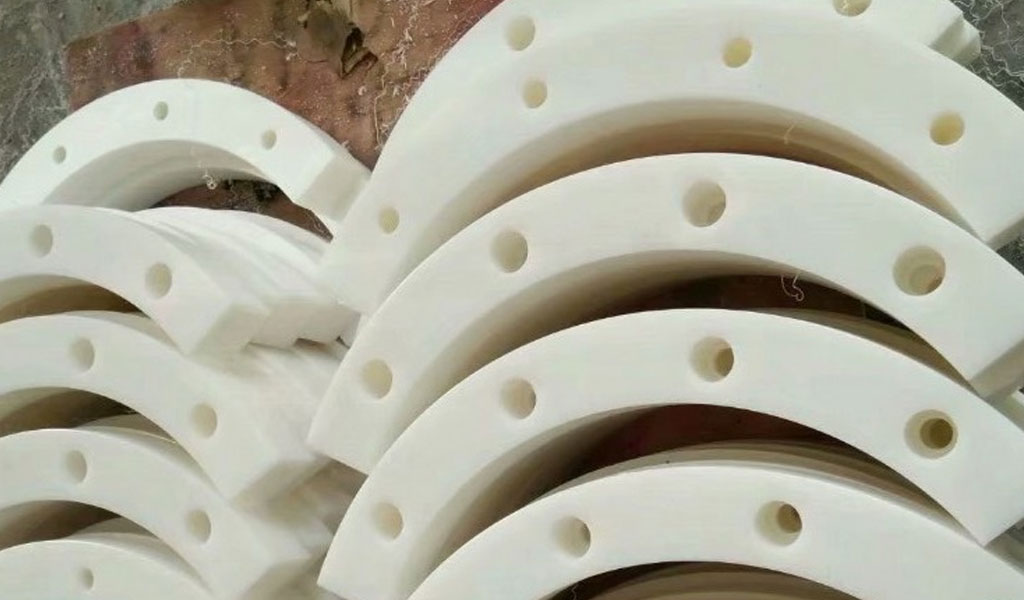
The development of plastic processing and manufacturing technology is advancing towards precision, efficiency, toughness, flexibility, cleanliness, automation, integration, and other technical directions, providing support for the development and industrialization of advanced manufacturing technologies.
The strength and development of a country or region ultimately depend on the competitiveness of the products and services provided by its manufacturing industry. The development of plastic forming technology will greatly promote the development of advanced manufacturing technology, thereby enhancing China’s competitiveness in the international community.
Plastic forming technology is being applied in an increasing number of manufacturing technologies, and interdisciplinary collaboration between technologies is becoming more extensive. Research and application of plastic forming will inevitably drive and promote research in materials science, high precision, and micro-dimensions. The development of plastic forming theory and numerical simulation technology will lead to the development of high-precision measurement techniques.
Key manufacturing sectors have a huge demand for plastic forming technology.
In the transportation sector: Approximately 12% to 17% of the added value to the gross domestic product (GDP) is provided by the automobile and automobile parts manufacturing industry. The majority of automobile and automobile parts manufacturing is done through plastic processing techniques, with over 75% of automobile parts being stamped components. Techniques like internal high-pressure forming, spin forming, etc., also find extensive application in the automotive industry. Additionally, there’s a trend towards larger and more complex forged components in the marine sector, such as typical forged shafts, gears, and engine cylinder heads.
In the aerospace sector: There’s an increasing demand for large rotary parts in missiles, launch vehicles, and aircraft. These components typically feature thin walls, large diameters, and complex structures, and are made of special materials like high-strength steel, ultra-high-strength steel, titanium alloys, and high-temperature alloys. Rotary swaging is considered the most effective method for forming these components due to considerations of structural integrity, strength, precision, and efficiency. High-pressure forming is the preferred technology for closed-section integral components in aircraft.
In the construction sector: Advanced manufacturing technologies capable of producing high-quality three-dimensional curved surface components are urgently needed for many major construction projects and engineering endeavors. Multipoint forming technology can be widely used for the digital forming of architectural three-dimensional curved surface components, effectively suppressing wrinkles and springback during the forming process of plate-like curved surface components, improving the processing accuracy of three-dimensional curved surface components, and reducing the cost of irregular buildings and various decorative three-dimensional curved surface components.
In the energy sector: Key components in heavy-duty equipment for energy production, characterized by large size, complex shapes, and high performance requirements, require seamless forming with fine and uniform microstructures. Precise hot ring rolling is an irreplaceable forming manufacturing technology. Large forgings, such as rotor assemblies for steam turbines in thermal power plants, turbine casings, turbine rotors for hydroelectric power plants, and large rolling bodies, are critical and basic components of the energy industry and require large forging forming technologies for manufacturing. Tension leg forgings for offshore platforms, large forging nodes, forgings and structural components for oil drilling, and large pipelines for oil transportation are expected to have significant demand, which cannot be ignored.
In the defense industry: Tank tracks, gears, idlers, traction bar bodies, directional arcs, universal joint forks on artillery, gun housings, sight bases on firearms, missile nozzles, shells, cartridges, and fuses mainly adopt forging and extrusion forming processes. Meanwhile, a variety of plate-like components such as projectile caps, fuse casings, tank friction pads, military vehicle motorcycle parts, etc., mainly use stamping forming processes. There’s also a growing demand for plastic forming processes for micro-components and ultra-high-strength steel. The development of precision plastic forming molds to meet the requirements of new materials and processes, as well as plastic forming molds for micro-parts, will be the main direction of mold technology development in the field of weapons and equipment in the future.
In other sectors: Electronics, communications, medical devices, light industry, as well as utensils, accessories, home appliances, etc., also have extensive applications for plastic processing technology. In recent years, continuous molds have begun to move towards multifunctional and intelligent directions, capable of not only completing the stamping production of electronic components but also achieving functions such as assembly, welding, and online testing of processed parts. Biochips, as typical micro-structural components, have been widely used in the medical field. Spin forming to produce lampshades and lamp bases is the best process choice for the lighting industry.
Key Technologies to be Emphasized in the Development of Plastic Forming Techniques
1.Special Plastic Forming Techniques
Special plastic forming refers to some process techniques different from conventional plastic forming, including differences in material microstructure, component size, and external fields applied during forming. The essence of special forming includes special physical forms of the raw materials used for forming, special organizational states of materials, special dimensions of formed components, special physical fields applied to materials during forming, and special methods of applying forming forces.
Looking towards 2030, the development of special plastic forming techniques involves four key technologies:
- Ultrafine-grained superplastic forming;
- Microforming;
- Powder forming;
- Electroforming.
2.Internal High Pressure Forming Technology
High-pressure forming, also known as internal high-pressure forming, is a forming technique where tubular material is used as the blank, and high-pressure liquid and axial supplement are applied inside the tube to press it into the shape of the desired workpiece in the mold cavity. It is also called tube hydroforming because emulsion (a mixture of water and small amounts of corrosion inhibitors, etc.) is used as the hydraulic medium.
The ultra-high-pressure control precision of internal high-pressure forming equipment reaches 0.2~0.5 MPa, and the displacement control precision reaches 0.05 mm, realizing controllable process parameters. At the same time, the ultra-high internal pressure provides conditions for increasing the complexity and forming accuracy of parts. The parts produced have various cross-sectional changes, good shape fixity, and quickly gain favor in the automotive and aerospace manufacturing industries. After solving the key technical issues of rapid and stable sealing under production conditions of ultra-high pressure and rapid response and feedback of control system, it is possible to manufacture a part within 30 seconds or even shorter time, thus widely used in mass production of lightweight components for automobiles.
Looking towards 2030, the development of internal high-pressure forming technology involves three key technologies:
- Hot-state internal pressure forming;
- Forming of ultra-high strength steel;
- New forming processes.
3.Special Rolling Forming Technology
Special rolling belongs to high-tech deep processing of steel, which can better improve the quality, reduce the cost, and increase the variety of steel rolling production compared to traditional rolling technology, representing the development of traditional rolling theory.
China has made great progress in part rolling technology, but there is still a big gap from the requirements of building a resource-saving society. The main manifestations are low application rate of part rolling forming technology and the need to break through some key technical problems, which makes it difficult to expand the application scope.
Looking towards 2030, the development of special rolling forming technology involves four key technologies:
- Radial forging technology;
- Ring rolling and composite ring rolling technology;
- Oscillating rolling technology;
- Wedge cross rolling and inclined rolling technology.
4.Precision Forging Forming Technology
Precision forging technology is a kind of forming technology where the formed parts only need a small amount of machining or no further machining to meet the requirements of the parts, mainly used for producing net shape parts and near-net shape parts. Precision forging technology was formerly known as chipless forging technology, precise forging technology, and in recent years, it has been called near/net forging forming technology domestically and internationally.
Precision forging technology is an important part of advanced manufacturing technology. Compared with traditional forming technology, it reduces subsequent machining volume, reduces material and energy consumption, shortens processing steps, improves production efficiency, ensures product quality, and reduces production costs. It is a widely used part manufacturing technology in industries such as automotive, mining, aerospace, weapons, energy, and construction.
Looking towards 2030, the development of precision forging forming technology involves two key technologies:
- Warm/hot precision forging technology;
- Cold precision forging technology.
5.Multi-point Forming Technology
Multi-point digital forming technology is an advanced manufacturing technology for forming sheet metal flexibly, mainly achieved through computer-aided design and manufacturing. It transforms the traditional sheet metal processing method and embodies its technical features in several aspects: achieving dieless forming, saving mold materials and design/manufacturing costs; processing various shapes of parts on one machine; achieving variable path forming; facilitating integration of CAD/CAE/CAM and forming automation; shortening the development cycle of new products and reducing manufacturing costs.
Looking towards 2030, the development of multi-point forming technology involves four key technologies:
- Large-scale multi-point forming technology and large-area multi-point forming equipment;
- Fine multi-point forming technology;
- Flexible roller and multi-point shaping technology;
- Continuous flexible multi-point forming.
6.Spin Forming Technology
Spin forming is a metal plastic forming method used for shaping thin-walled hollow rotating parts. It integrates the characteristics of forging, extrusion, stretching, bending, ring rolling, cross rolling, and rolling, representing an advanced process with minimal or even no cutting. Spin forming has the following characteristics: point-by-point forming; low pressure during spinning; wide range of products; high material utilization; low production costs; significantly improved product performance; high surface finish; small dimensional tolerances; reduced manufacturing steps, etc. Spin forming is typically used to produce seamless rotating hollow parts, processing difficult-to-deform metal parts.
Looking towards 2030, the development of spin forming technology involves three key technologies:
- Mechanics of spin forming, trajectory of multi-pass spin forming, forming limits/quality and other forming theories;
- Improvement of spin forming processes, combination of spin forming technology with various technologies, application of new materials for spin forming, and improvement of spin forming efficiency;
- Development of large-scale/standardized spin forming equipment, multifunctional/flexible spin forming equipment, and professional/automated spin forming equipment.
7.Large Forging Forming Technology
Large forgings, usually forged on hydraulic presses with a pressure above 10 MN, are referred to as large forgings. Large forgings are mostly directly forged from steel ingots. Large forgings are typically critical components in major equipment, and their production involves many processes such as smelting, ingot casting, heating, forging, rough machining, heat treatment, and quality inspection. It has characteristics such as long cycle, strong continuity, labor-intensive, high technical content, and high production difficulty. Large forging production is characterized by single-piece, small batch production, large variety changes, and strong flexibility.
Looking towards 2030, the development of large forging forming technology involves two key technologies:
- Improving and mastering the core manufacturing technologies of large forgings;
- Strengthening research on basic common technologies of large forgings.
8.Forging Equipment Technology
Forging equipment technology mainly aims to achieve the best energy and motion matching of materials, deformation conditions, loads, transmission, and drive in plastic processing. It studies the interaction mechanism of solid, fluid, gas substances, and physical fields such as electricity, magnetism, temperature, and light, as well as the transformation and control methods of characteristics such as motion and power between drive, transmission, and load.
Large die forging hydraulic press is an indispensable important equipment in the machinery manufacturing industry. It is also an important symbol of a country’s scientific and technological level and comprehensive national strength, and more importantly, a strategic equipment to safeguard national security. In addition to being essential equipment for the development of the aviation and aerospace industries, large die forging hydraulic presses are also indispensable in other important industrial sectors, such as the production of large turbine forgings for gas turbines, large disc forgings for gas turbines, various engine blades, large forgings for shipbuilding, large forgings for power plants, pressure vessel forgings, and the production of other types of civil forging products. All of these productions cannot be separated from large forging equipment.
Looking towards 2030, the development of forging equipment technology involves five key technologies:
- Research on servo digitization of forging equipment;
- Research on high-performance and precision forging equipment;
- Research on high-speed and ultra-high-speed forging equipment;
- Development of non-standard forging equipment;
- Networking of forging equipment.
9.Stamping Forming Technology
Stamping forming is a method of plastic processing. It utilizes the material’s plastic deformation capability to change its geometric shape and size through the action of molds installed on equipment, thereby achieving the purpose of stamping forming. Stamping forming can be used for processing both metal materials and non-metal materials (such as rubber wood, acrylic, cardboard, leather, etc.). It has a wide range of applications, high productivity, stable product quality, good interchangeability (generally no further processing is required), easy operation, easy realization of mechanization, automation, low cost, and material saving.
Automobile body panels, body frames, chassis and exhaust pipe parts, aircraft skins, wings, and various types of small curved aluminum alloy thin-walled parts, aerospace engine flame tubes, sealing rings made of high-temperature alloys and titanium alloys, as well as titanium alloy and high-strength aluminum alloy profiled pipes, fairings, and other thin-walled parts for rockets and missiles, all require precise sheet metal forming technology for manufacturing. As an advanced processing method, stamping technology plays an irreplaceable key role in the national economy and national defense construction.
Looking towards 2030, the development of stamping forming technology involves nine key technologies:
- Welded assembly plate stamping forming technology;
- Hot stamping technology for high-strength steel plates;
- Forming technology for light alloy sheets;
- High-speed stamping forming technology;
- Precision stamping technology for thick plates;
- Precision stamping technology for micro components;
- High-efficiency stamping forming technology;
- Combined forging and stamping forming technology;
- Composite material sheet forming.
10.Extrusion Forming Technology
Extrusion forming is a plastic processing method in which the billet placed in a closed extrusion cylinder (die) is squeezed out through the die or gap under three-directional non-uniform pressure stress to obtain the required product (component) plastic processing method. Extrusion forming has high material utilization, improves material structure, enhances mechanical properties, is simple to operate, has high productivity, and can produce long rods, deep holes, thin-walled, and special-shaped cross-section parts. It is an important method of chipless processing.
Extrusion is one of the main methods for the production of non-ferrous metals and steel materials and the forming of parts. It is also an important method for the preparation and processing of various advanced materials such as composite materials and powder materials. Extrusion is mostly used for the production of rods, thin-walled and ultra-thick-walled complex section profiles and tubes of non-ferrous metals and alloys, high-alloy steel materials, and mechanical parts. Its products have a wide range of applications, especially in construction, aviation, transportation, communication, and other fields, occupying an extremely important position in the national economy.
Looking towards 2030, the development of extrusion forming technology involves four key technologies:
- Labor-saving extrusion forming technology (high-speed fatigue-resistant components);
- Multi-directional active loading control forming technology for complex components (such as three-way, four-way, and branch type, etc.);
- Rotational extrusion forming technology for internal ribs;
- Roller extrusion forming technology for variable cross-section components (such as variable thickness blades, curved rotating bodies, etc.).
11.Forging Die Technology
Forging die technology refers to the use of energy provided by a press to induce plastic deformation of metal materials in the die to obtain the required shape. It is closely related to specific forming processes and is the key process equipment to achieve forming process requirements. According to the relevant technologies applied in the mold development process, mold technology can be divided into: mold function creation technology, mold design and manufacturing technology, and mold material preparation and heat treatment technology.
Looking towards 2030, the development of forging die technology involves three key technologies:
Maximize Tooling and CNC Metal Spinning Capabilities.
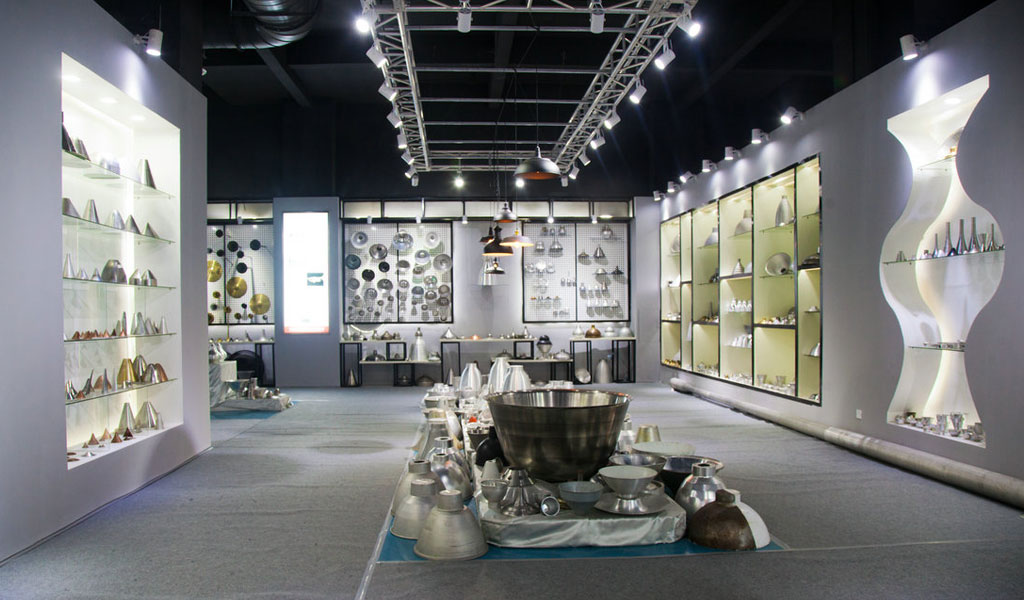
At BE-CU China Metal Spinning company, we make the most of our equipment while monitoring signs of excess wear and stress. In addition, we look into newer, modern equipment and invest in those that can support or increase our manufacturing capabilities. Our team is very mindful of our machines and tools, so we also routinely maintain them to ensure they don’t negatively impact your part’s quality and productivity.
Talk to us today about making a rapid prototype with our CNC metal spinning service. Get a direct quote by chatting with us here or request a free project review.
BE-CU China CNC Metal Spinning service include : CNC Metal Spinning,Metal Spinning Die,Laser Cutting, Tank Heads Spinning,Metal Hemispheres Spinning,Metal Cones Spinning,Metal Dish-Shaped Spinning,Metal Trumpet Spinning,Metal Venturi Spinning,Aluminum Spinning Products,Stainless Steel Spinning Products,Copper Spinning Products,Brass Spinning Products,Steel Spinning Product,Metal Spinnin LED Reflector,Metal Spinning Pressure Vessel,
- Mold function creation technology;
- Mold design and manufacturing technology;
- Mold material preparation and heat treatment.