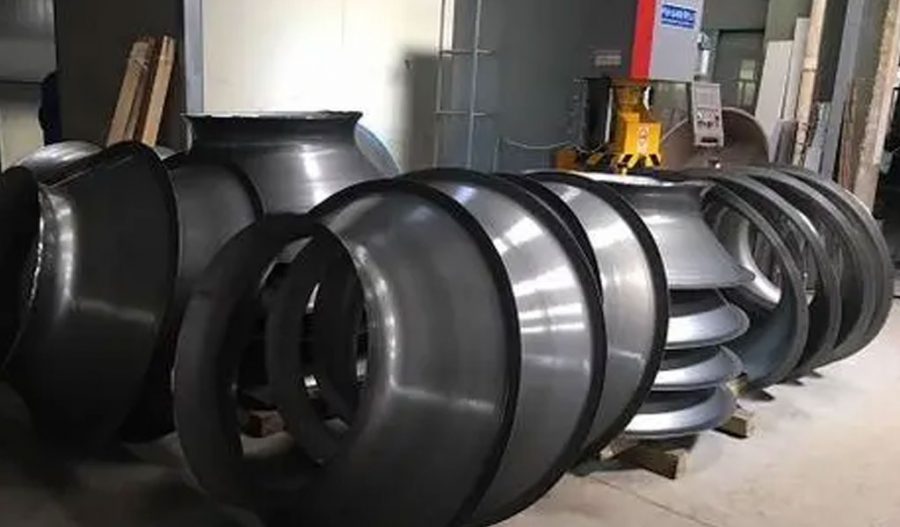
On a rapidly spinning potter’s wheel, a lump of clay is repeatedly molded by a potter’s skilled hands until it gradually forms a beautiful piece of ceramics. In the realm of industrial manufacturing, craftsmen can use a spinning machine to press an ordinary metal sheet into a crucial component.
This metal processing method, akin to pottery, is known in the industry as spinning forming technology, a process that amalgamates the strengths of various techniques. Unlike welding, which involves “joining,” or casting, which involves “solidifying,” spinning forming technology primarily utilizes a spinning machine to deform the billet.
Before delving into the science of spinning forming technology, let’s talk about the spinning machine. The spinning machine consists of two parts, akin to a pair of hands. During processing, the “left hand” rotates the billet, while the “right hand” applies pressure. It is through the coordinated efforts of these “hands” that the desired component is achieved.
When spinning forming technology first emerged, workers used tools such as sticks to apply pressure to the billet. Later, they employed spinning machines driven by water and steam power. For a long period, this technique remained unnamed. It wasn’t until the late 1760s that a German scientist patented the world’s first metal spinning technology, giving this technique its name.
Today, the continuously evolving spinning forming technology has become an indispensable manufacturing process in high-precision fields. In the automotive industry, it is widely used in wheel hub manufacturing; in the aerospace industry, components such as auxiliary fuel tanks, air inlets, and slides of fighter jets are made using this technology; in the space industry, rocket shells and aerospace engine nozzles are also closely related to this technology.
The importance of spinning forming technology lies in its unique advantages, which can be summarized in three points:
First, high strength. Spinning forming is an integral forming technology, where the processed parts have no weld seams, maintaining the integrity of the billet. Data shows that the strength and hardness of materials after spinning forming are increased by more than 30% compared to the base material.
Second, low cost. Spinning forming technology does not require cutting processing of the billet, resulting in high material utilization. The requirements for forming molds and processing equipment are simple, significantly reducing production costs.
Third, high space utilization. Compared to parts of the same strength, spun parts are smaller and lighter, saving more space. Additionally, this technology can detect some defects present in the billet during smelting.
In recent years, the development of spinning forming technology has flourished, with some countries incorporating sensor technology and high-precision numerical control technology into the field. Others are attempting to create “AI spinning” capable of automatic drawing recognition, design planning, and optimization of process parameters. Looking to the future, the application prospects of spinning forming technology in the military industry are vast, and its development is crucial to the quality of weapon and equipment manufacturing.
Maximize Tooling and CNC Metal Spinning Capabilities.
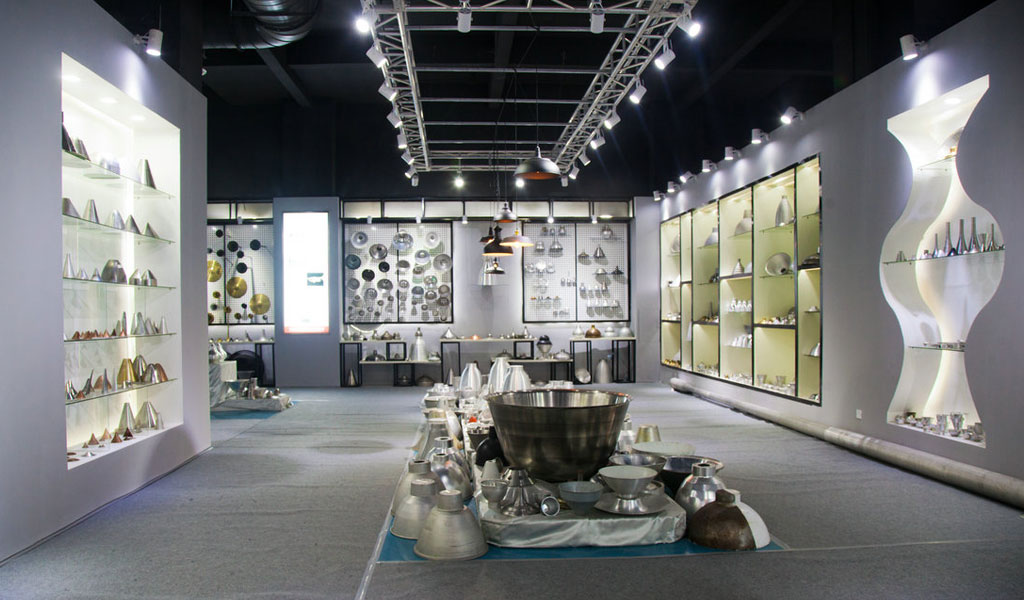
At BE-CU China Metal Spinning company, we make the most of our equipment while monitoring signs of excess wear and stress. In addition, we look into newer, modern equipment and invest in those that can support or increase our manufacturing capabilities. Our team is very mindful of our machines and tools, so we also routinely maintain them to ensure they don’t negatively impact your part’s quality and productivity.
Talk to us today about making a rapid prototype with our CNC metal spinning service. Get a direct quote by chatting with us here or request a free project review.
BE-CU China CNC Metal Spinning service include : CNC Metal Spinning,Metal Spinning Die,Laser Cutting, Tank Heads Spinning,Metal Hemispheres Spinning,Metal Cones Spinning,Metal Dish-Shaped Spinning,Metal Trumpet Spinning,Metal Venturi Spinning,Aluminum Spinning Products,Stainless Steel Spinning Products,Copper Spinning Products,Brass Spinning Products,Steel Spinning Product,Metal Spinnin LED Reflector,Metal Spinning Pressure Vessel,