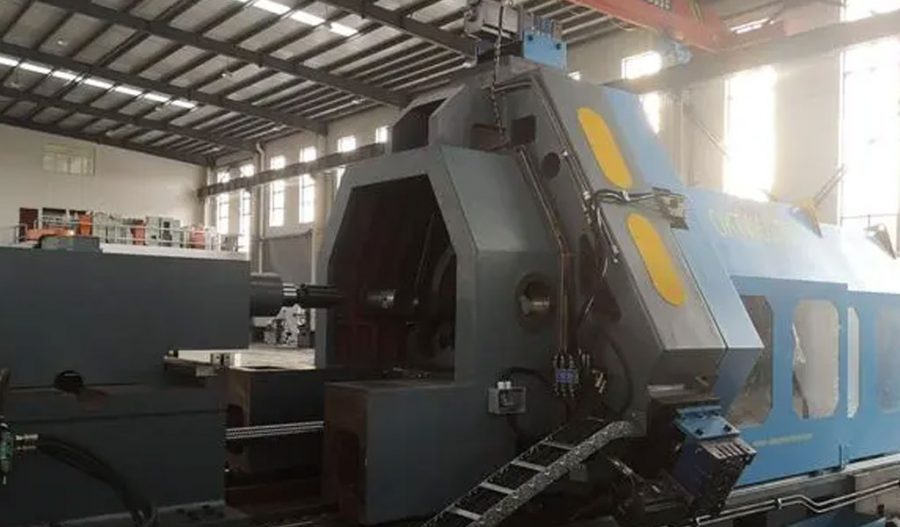
A metal lathe is a fundamental machine tool used in metalworking for shaping metal and other materials through rotational cutting. It has been essential in manufacturing and engineering for over a century, evolving from manual lathes to sophisticated computer-controlled systems. The speed at which a metal lathe spins, or its rotational speed, is a critical parameter that influences machining efficiency, surface finish, tool wear, and overall productivity. This article provides a comprehensive overview of the factors affecting lathe speed, the types of lathes, and the implications of different speeds in metalworking.
Historical Context Of Metal Lathe Rotation Speeds
The metal lathe’s origins can be traced back to ancient Egypt and Greece, where primitive forms of the lathe were used for turning wooden objects. The transition to metalworking lathes began in the 19th century with the advent of industrialization. Early lathes were driven by belts and pulleys, but advancements in technology introduced motorized drives and computerized controls. These developments allowed for more precise and variable control of rotational speeds.
Types of Metal Lathes
- Engine Lathes: Also known as manual lathes, these machines are commonly used in workshops. They feature a range of speed options, typically controlled by a combination of belts and pulleys or a variable-speed gearbox.
- Turret Lathes: Designed for repetitive production work, turret lathes have multiple cutting tools mounted on a rotating turret. The speed of these lathes is generally higher than that of engine lathes, facilitating faster production rates.
- CNC Lathes: Computer Numerical Control (CNC) lathes use computerized controls to adjust rotational speeds and other parameters. They offer high precision and flexibility, with speeds that can be adjusted automatically based on the machining requirements.
- Automatic Lathes: These lathes are used for high-volume production and can automatically perform a series of machining operations. They can achieve very high rotational speeds to maximize output.
Factors Affecting Lathe Speed
- Material Properties: The type of material being machined affects the optimal cutting speed. For example, hard metals require slower speeds to prevent excessive tool wear and overheating, while softer materials can be machined at higher speeds.
- Tooling: The material and geometry of the cutting tool influence the choice of lathe speed. High-speed steel (HSS) tools and carbide inserts have different optimal cutting speeds.
- Workpiece Diameter: The diameter of the workpiece affects the surface speed. Larger diameters require slower spindle speeds to maintain the same cutting conditions at different radii.
- Cutting Conditions: The depth of cut, feed rate, and type of cut (e.g., roughing or finishing) all play a role in determining the appropriate spindle speed.
Speed Calculation and Adjustment
The rotational speed of a lathe is typically measured in revolutions per minute (RPM). The formula for calculating the optimal speed is:
Speed (RPM)=Cutting Speed (SFM)×12/Diameter of Workpiece (inches)
Where SFM (Surface Feet per Minute) is determined based on the material being cut and the cutting tool used. This formula helps machinists set the lathe speed for various operations and materials.
Implications of Speed on Machining
- Surface Finish: Higher speeds generally improve the surface finish of the workpiece, provided that the cutting conditions are appropriate. Too high a speed, however, can lead to poor surface quality and increased tool wear.
- Tool Life: Tool wear increases with higher speeds due to greater friction and heat generation. Proper speed adjustments are necessary to balance productivity with tool longevity.
- Heat Generation: Increased speed results in more heat, which can affect both the workpiece and the tool. Effective cooling methods, such as lubrication and cooling fluids, are essential for maintaining machining quality.
- Machining Efficiency: Optimal speeds enhance machining efficiency by reducing cycle times and improving accuracy. CNC lathes, with their automated speed adjustments, can achieve higher efficiency compared to manual lathes.
Modern Advances in Lathe Speed Control
The development of CNC technology has revolutionized lathe speed control, allowing for precise adjustments based on real-time data. Modern CNC lathes can automatically adjust spindle speeds in response to changes in cutting conditions, improving both productivity and quality.
Conclusion
The rotational speed of a metal lathe is a critical parameter that affects various aspects of metalworking, from surface finish to tool wear. Understanding the factors that influence lathe speed and how to calculate and adjust it is essential for optimizing machining processes. With advancements in technology, modern lathes offer greater flexibility and precision in controlling rotational speeds, contributing to increased efficiency and improved machining outcomes.
Maximize Tooling and CNC Metal Spinning Capabilities.
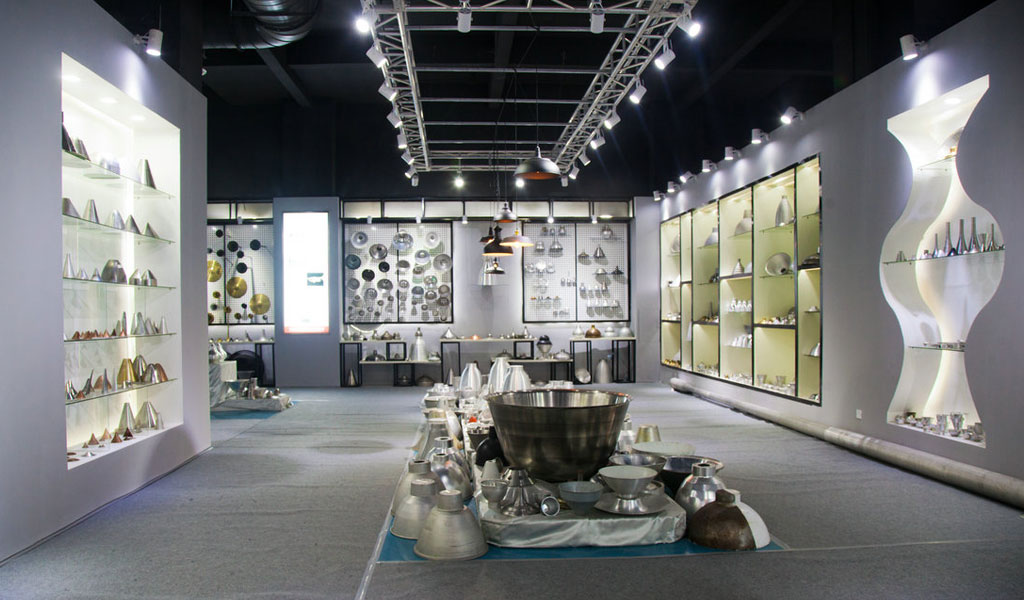
At BE-CU China Metal Spinning company, we make the most of our equipment while monitoring signs of excess wear and stress. In addition, we look into newer, modern equipment and invest in those that can support or increase our manufacturing capabilities. Our team is very mindful of our machines and tools, so we also routinely maintain them to ensure they don’t negatively impact your part’s quality and productivity.
Talk to us today about making a rapid prototype with our CNC metal spinning service. Get a direct quote by chatting with us here or request a free project review.
BE-CU China CNC Metal Spinning service include : CNC Metal Spinning,Metal Spinning Die,Laser Cutting, Tank Heads Spinning,Metal Hemispheres Spinning,Metal Cones Spinning,Metal Dish-Shaped Spinning,Metal Trumpet Spinning,Metal Venturi Spinning,Aluminum Spinning Products,Stainless Steel Spinning Products,Copper Spinning Products,Brass Spinning Products,Steel Spinning Product,Metal Spinnin LED Reflector,Metal Spinning Pressure Vessel,