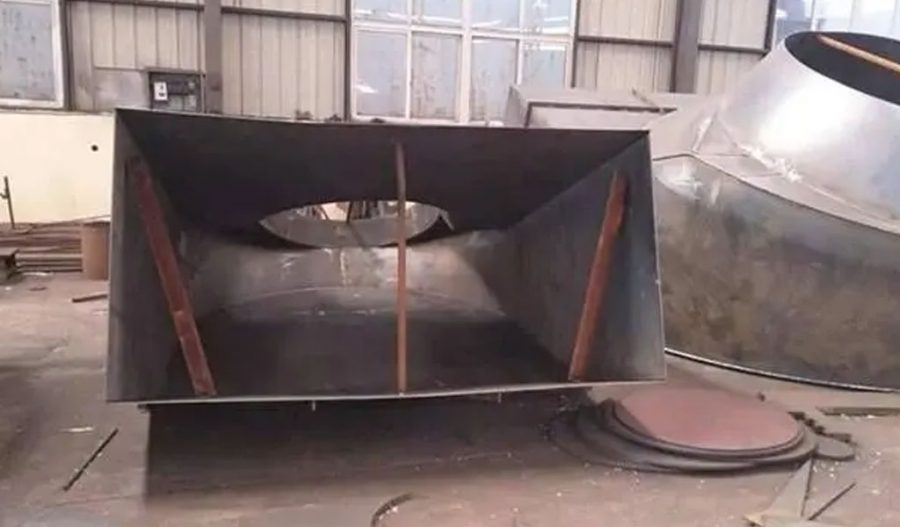
Variable Air Volume (VAV) Boxes are critical components in modern Heating, Ventilation, and Air Conditioning (HVAC) systems, particularly in large commercial and institutional buildings. Unlike Constant Air Volume (CAV) systems, which supply a constant airflow at variable temperatures, VAV systems adjust the amount of air supplied to different zones within a building based on the specific demand of each area. This approach not only enhances occupant comfort but also significantly improves the energy efficiency of HVAC systems.
The concept of VAV systems dates back to the mid-20th century, coinciding with the increasing demand for more energy-efficient and controllable HVAC systems. The development of VAV technology has paralleled advances in building automation, allowing for more sophisticated control over the indoor environment.
VAV boxes, the terminal units of these systems, play a crucial role in modulating the volume of air delivered to various zones. These devices ensure that each area receives just the right amount of conditioned air, maintaining desired temperature and humidity levels while minimizing energy consumption. The versatility and efficiency of VAV systems have made them a preferred choice in a wide range of applications, from office buildings to hospitals, schools, and industrial facilities.
Components of a VAV Box
A typical VAV box consists of several key components, each playing a specific role in the system’s operation:
- Damper Mechanism: The damper is a movable component within the VAV box that regulates the flow of air. It adjusts its position based on the cooling or heating demand of the zone it serves, either allowing more air to pass through or restricting the airflow.
- Sensors and Controls: VAV boxes are equipped with various sensors that monitor conditions such as temperature, pressure, and airflow. These sensors are connected to a control system that processes the data and adjusts the damper position accordingly. Modern VAV boxes often integrate with building automation systems (BAS), allowing for centralized monitoring and control.
- Terminal Units: These are the end points of the air distribution system where conditioned air is delivered to specific zones. In some cases, terminal units may include additional heating elements, such as electric heaters or hot water coils, to provide supplemental heating as needed.
Types of VAV Boxes
VAV boxes come in several types, each suited to different applications and system designs:
- Single Duct VAV Boxes: These are the most common type, featuring a single air inlet and outlet. They regulate the volume of supply air based on the demand in the zone.
- Dual Duct VAV Boxes: These boxes have two inlets, one for cold air and one for warm air. They mix the two streams to achieve the desired temperature, making them ideal for spaces requiring precise temperature control.
- Fan-Powered VAV Boxes: These units incorporate a small fan to help distribute air more evenly. They are often used in spaces where low airflow could lead to uneven heating or cooling.
- Series Fan-Powered VAV Boxes: In this configuration, the fan operates continuously, ensuring a consistent airflow regardless of the damper position.
- Parallel Fan-Powered VAV Boxes: Here, the fan only activates when additional airflow is needed, such as during heating mode or when the damper is nearly closed.
How VAV Boxes Work
The operation of a VAV box is governed by the principle of modulating airflow in response to varying thermal loads within a building’s zones. When the temperature in a zone rises above the setpoint, the VAV box opens its damper to allow more cooled air to enter. Conversely, when the temperature drops, the damper closes to reduce the airflow, thereby preventing overcooling.
Control strategies for VAV systems can be simple or complex, depending on the specific application. Basic VAV systems might use a single sensor and controller to manage a zone, while more advanced setups might involve multiple sensors, networked controls, and integration with building-wide automation systems.
The interaction between VAV boxes and other HVAC components, such as air handling units (AHUs) and chillers, is essential for maintaining overall system efficiency. The VAV boxes signal to the central HVAC system how much air is needed in each zone, enabling the system to adjust the supply air temperature and volume accordingly. This dynamic interaction ensures that energy is used efficiently, reducing unnecessary cooling or heating.
Applications of VAV Boxes
VAV boxes are widely used in various applications due to their versatility and efficiency:
- Commercial Buildings: Office spaces, shopping malls, and conference centers often rely on VAV systems to provide individual temperature control for different zones, enhancing occupant comfort while minimizing energy use.
- Residential Use: While less common, VAV systems can be used in large residential complexes or high-end homes to provide zoned temperature control.
- Industrial Applications: In manufacturing facilities and laboratories, where precise temperature and humidity control is essential, VAV systems are used to maintain specific environmental conditions.
- Special Environments: Cleanrooms, hospitals, and data centers are examples of environments that require stringent air quality and temperature control, making VAV systems an ideal solution.
Advantages and Disadvantages
Advantages:
- Energy Efficiency: VAV systems optimize airflow based on demand, reducing energy consumption compared to constant volume systems.
- Improved Comfort: By providing individual zone control, VAV systems can maintain consistent comfort levels across different areas of a building.
- Flexibility: VAV systems can be easily adjusted to accommodate changes in building occupancy or layout.
Disadvantages:
- Complexity: The design and installation of VAV systems can be more complex than simpler HVAC systems, requiring careful planning and expertise.
- Initial Cost: VAV systems may have higher upfront costs due to the need for sophisticated controls and sensors.
- Maintenance: Regular maintenance is necessary to ensure optimal performance, which can add to the overall operational cost.
Design Considerations
Designing a VAV system involves several critical steps, including load calculations, sizing of VAV boxes, and zoning strategies. Accurate load calculations are essential to determine the heating and cooling requirements of each zone, ensuring that the VAV boxes are appropriately sized. Zoning strategies must consider the layout of the building, the location of heat sources, and the desired level of control.
Integration with Building Automation Systems (BAS) is another key consideration, allowing for centralized control and monitoring of the HVAC system. This integration can enhance energy efficiency and provide valuable data for optimizing system performance.
Installation and Maintenance
Proper installation is crucial for the effective operation of VAV systems. Installation best practices include ensuring proper duct connections, calibrating sensors, and verifying that the control system is correctly configured. Common issues such as improper damper operation or sensor malfunctions can lead to reduced system efficiency or occupant discomfort.
Regular maintenance, including cleaning of dampers and sensors, checking for leaks, and recalibrating controls, is necessary to keep the system running efficiently. Scheduled maintenance can prevent minor issues from developing into major problems, prolonging the life of the system.
Energy Efficiency and Sustainability
VAV systems play a significant role in enhancing the energy efficiency of buildings. By adjusting airflow based on demand, these systems reduce the energy needed for heating and cooling, contributing to lower operational costs and a smaller carbon footprint.
In the context of green building standards, such as LEED (Leadership in Energy and Environmental Design), VAV systems can help buildings achieve higher energy efficiency ratings. Innovations in VAV technology, such as the integration of advanced sensors and controls, are further driving the sustainability of HVAC systems.
Case Studies and Examples
Numerous case studies demonstrate the effectiveness of VAV systems in real-world applications. For instance, the implementation of a VAV system in a large office building might result in significant energy savings, with detailed analysis showing reductions in both cooling and heating costs.
Lessons learned from these projects can provide valuable insights for future installations, highlighting best practices and potential challenges in VAV system design and operation.
Regulatory and Standardization Aspects
VAV systems are subject to various standards and codes that ensure their safety, efficiency, and performance. These standards may vary by region, but they generally cover aspects such as airflow rates, noise levels, and energy efficiency.
Compliance with these standards is essential for the successful implementation of VAV systems. International perspectives on VAV technology can also provide insights into different approaches and innovations in the field.
Conclusion
Variable Air Volume (VAV) boxes are a cornerstone of modern HVAC systems, providing efficient and flexible control over indoor environments. Their ability to adjust airflow based on demand makes them an ideal solution for a wide range of applications, from commercial buildings to specialized environments.
As the demand for energy-efficient building solutions continues to grow, VAV technology is likely to evolve, with advancements in controls, sensors, and integration with building automation systems leading the way. Understanding the principles and applications of VAV boxes is essential for anyone involved in the design, installation, or maintenance of HVAC systems, ensuring that buildings are both comfortable and energy-efficient.
Maximize Tooling and CNC Metal Spinning Capabilities.
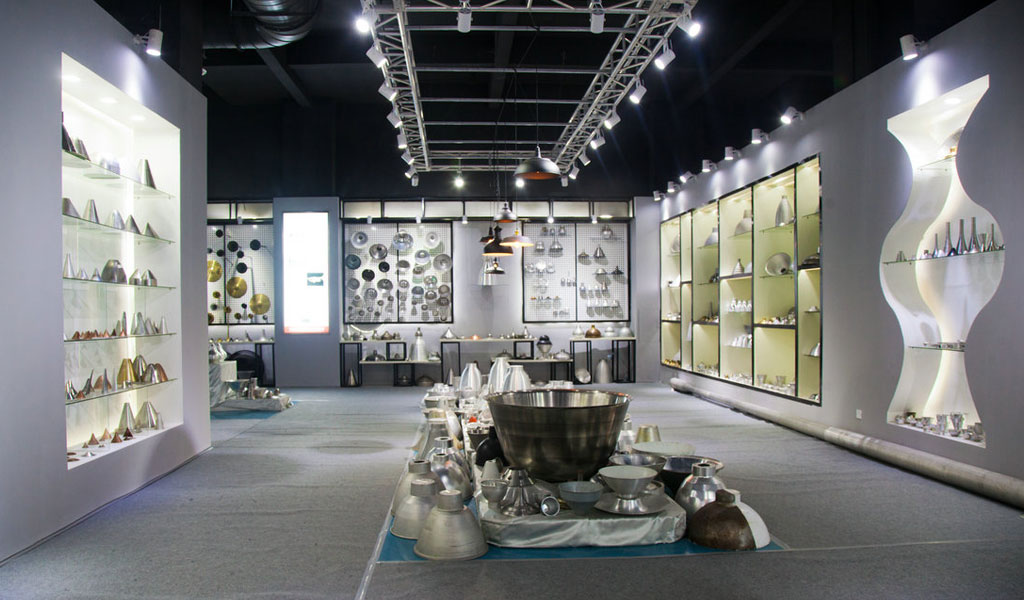
At BE-CU China Metal Spinning company, we make the most of our equipment while monitoring signs of excess wear and stress. In addition, we look into newer, modern equipment and invest in those that can support or increase our manufacturing capabilities. Our team is very mindful of our machines and tools, so we also routinely maintain them to ensure they don’t negatively impact your part’s quality and productivity.
Talk to us today about making a rapid prototype with our CNC metal spinning service. Get a direct quote by chatting with us here or request a free project review.
BE-CU China CNC Metal Spinning service include : CNC Metal Spinning,Metal Spinning Die,Laser Cutting, Tank Heads Spinning,Metal Hemispheres Spinning,Metal Cones Spinning,Metal Dish-Shaped Spinning,Metal Trumpet Spinning,Metal Venturi Spinning,Aluminum Spinning Products,Stainless Steel Spinning Products,Copper Spinning Products,Brass Spinning Products,Steel Spinning Product,Metal Spinnin LED Reflector,Metal Spinning Pressure Vessel,