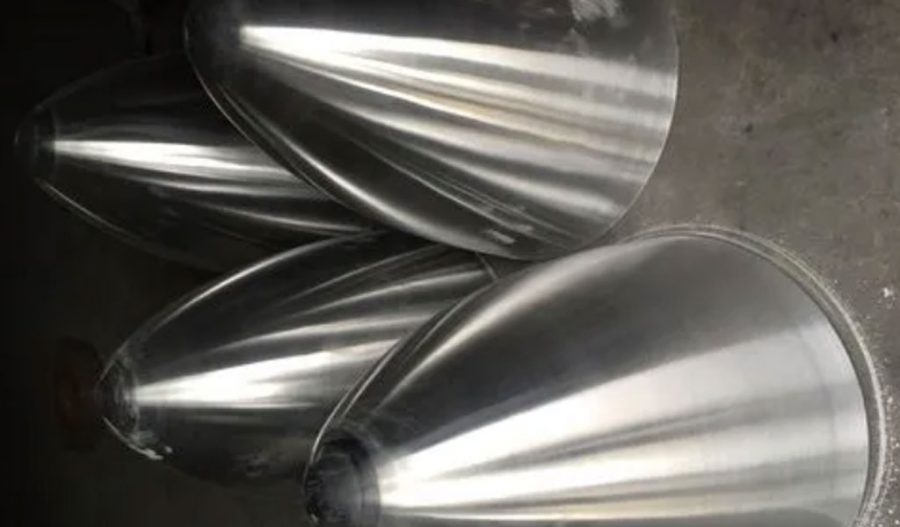
Conical shapes are integral components in various industries, including aerospace, automotive, and manufacturing. They are utilized in applications ranging from funnels and nozzles to pressure vessels and rocket components. Traditionally, metal spinning has been the primary method for producing metal cones. However, with advancements in additive manufacturing, 3D printing has emerged as a viable alternative. This article provides a comprehensive comparison between 3D printing and metal spinning for the production of conical components, highlighting the advantages, limitations, and practical applications of each method.
Metal Spinning
Metal spinning, also known as spin forming or metal turning, is a metalworking process where a flat metal disc, called a blank, is rotated at high speed on a lathe while being gradually formed into a desired shape by applying localized pressure. This process is typically used to produce symmetrical, axially symmetric parts, such as cones, hemispheres, and cylindrical shapes.
Process and Equipment
The metal spinning process begins with the selection of a suitable metal blank, which is then mounted on a spinning lathe. A forming tool, often made from hardened steel or carbide, is pressed against the rotating blank to shape it into the desired conical form. The process may involve multiple passes, with the tool progressively shaping the metal until the final geometry is achieved.
There are two primary types of metal spinning: manual spinning, where the operator controls the tool’s movement, and CNC spinning, which uses computer numerical control for more precise and repeatable operations. CNC spinning allows for greater complexity and consistency, especially for high-volume production.
Advantages of Metal Spinning
- Material Efficiency: Metal spinning is a near-net-shape process, meaning that it produces minimal waste. The process stretches the metal, allowing for efficient use of material.
- Strength and Integrity: The cold-working nature of metal spinning enhances the strength of the material by refining its grain structure. This results in a more durable and resilient final product.
- Scalability: Metal spinning is well-suited for both low and high-volume production. Manual spinning is cost-effective for small batches, while CNC spinning can efficiently handle large-scale production runs.
- Versatility: Metal spinning can work with a wide range of metals, including aluminum, steel, copper, and titanium. The process is also flexible in terms of shape complexity, accommodating various conical and cylindrical forms.
Limitations of Metal Spinning
- Labor-Intensive: Manual spinning requires skilled operators, and the process can be time-consuming, particularly for complex shapes.
- Limited to Symmetrical Parts: Metal spinning is primarily limited to the production of axially symmetric parts. Producing non-symmetrical or highly intricate geometries is challenging.
- Tooling Costs: Initial tooling and setup costs can be high, especially for custom or intricate designs.
3D Printing Cones
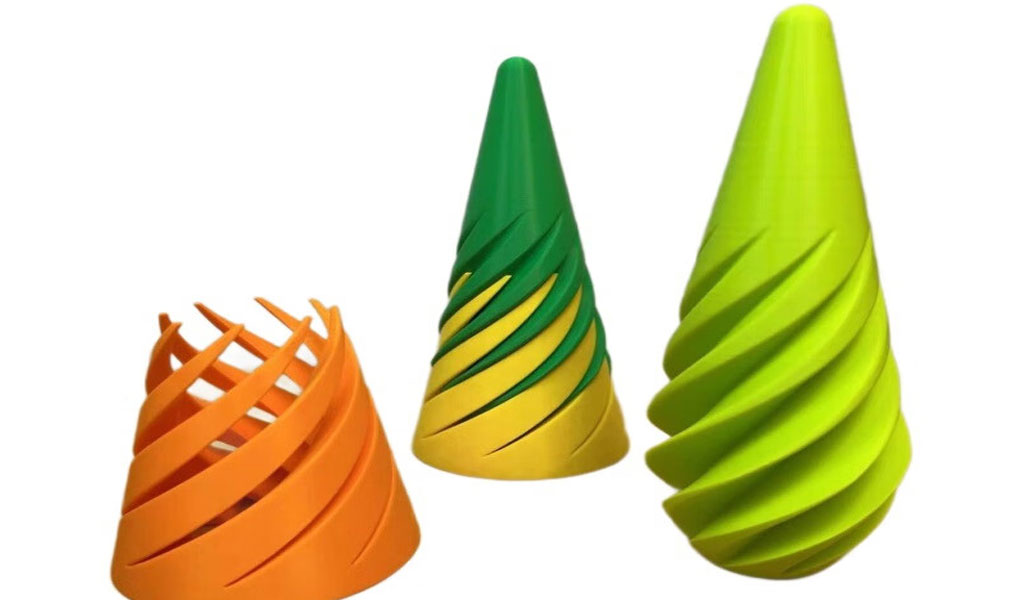
3D printing, also known as additive manufacturing, is a process of creating three-dimensional objects by layering material based on a digital model. This technology has revolutionized manufacturing, offering new possibilities for creating complex geometries and reducing lead times.
Process and Equipment
3D printing involves several techniques, including Fused Deposition Modeling (FDM), Stereolithography (SLA), Selective Laser Sintering (SLS), and Direct Metal Laser Sintering (DMLS). For metal cones, DMLS is the most relevant, as it directly produces metal parts by fusing metal powder layer by layer using a high-powered laser.
The process begins with a digital 3D model, which is sliced into thin layers. The 3D printer then sequentially deposits and fuses material, building the object from the bottom up. Unlike subtractive manufacturing processes, such as metal spinning, 3D printing adds material only where needed, minimizing waste.
Advantages of 3D Printing
- Complex Geometry: 3D printing excels at producing complex shapes that would be difficult or impossible to achieve with traditional methods. Cones with intricate internal structures, variable wall thicknesses, and integrated features can be easily fabricated.
- Rapid Prototyping: 3D printing allows for quick turnaround times from design to finished product. This is particularly valuable in industries where iterative testing and development are required.
- Material Efficiency: As an additive process, 3D printing reduces material waste compared to subtractive processes like metal spinning. This can lead to cost savings, especially when using expensive materials.
- Customization: 3D printing allows for mass customization, where each part can be uniquely tailored without additional tooling costs. This is ideal for producing specialized components or small batches.
Limitations of 3D Printing
- Surface Finish and Post-Processing: 3D-printed metal parts often require post-processing, such as machining, polishing, or heat treatment, to achieve the desired surface finish and mechanical properties.
- Material Limitations: While 3D printing is advancing rapidly, the range of materials available, particularly metals, is still more limited compared to traditional manufacturing methods.
- Production Speed: For high-volume production, 3D printing may be slower compared to traditional methods like metal spinning. However, this is continually improving as technology advances.
- Cost: The cost of 3D printing can be higher for certain applications, especially when considering the expense of metal powders and the need for post-processing.
Comparison of Applications
Aerospace Industry
In the aerospace industry, where weight reduction and complex geometries are crucial, 3D printing is increasingly favored for producing components like rocket engine nozzles and fuel tanks. The ability to create lightweight, structurally optimized cones with integrated cooling channels or lattice structures is a significant advantage.
Metal spinning, however, remains prevalent for producing large, simple conical parts, such as nose cones and structural elements, where material strength and integrity are paramount.
Automotive Industry
For the automotive industry, 3D printing is used for producing custom exhaust components, turbocharger housings, and other parts that benefit from complex geometries. Metal spinning is typically employed for components that require high strength and durability, such as wheel rims and certain suspension parts.
Manufacturing and Tooling
In general manufacturing, 3D printing is increasingly utilized for creating specialized tooling, fixtures, and prototypes. Metal spinning is preferred for mass production of conical components, such as funnels and industrial filters, where the strength of spun metal and cost efficiency are critical.
Conclusion
Both 3D printing and metal spinning offer unique advantages and limitations when it comes to the production of conical components. The choice between these methods depends on various factors, including the complexity of the design, material requirements, production volume, and cost considerations.
3D printing is ideal for producing complex, customized cones with intricate features, especially in low to medium volumes. It offers flexibility in design and rapid prototyping, making it well-suited for industries where innovation and customization are key.
Metal spinning, on the other hand, is a time-tested process that excels in producing high-strength, symmetrical cones at scale. It is particularly advantageous for applications where material efficiency, durability, and cost-effectiveness are paramount.
As both technologies continue to evolve, their complementary strengths are likely to lead to new hybrid manufacturing approaches, where 3D printing and metal spinning are combined to leverage the best of both worlds.
Maximize Tooling and CNC Metal Spinning Capabilities.
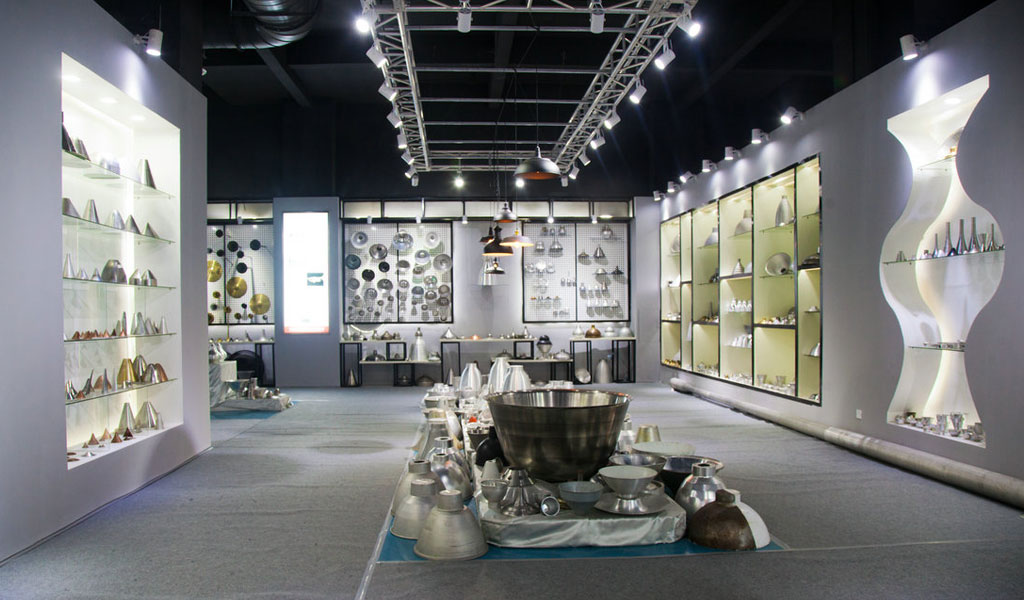
At BE-CU China Metal Spinning company, we make the most of our equipment while monitoring signs of excess wear and stress. In addition, we look into newer, modern equipment and invest in those that can support or increase our manufacturing capabilities. Our team is very mindful of our machines and tools, so we also routinely maintain them to ensure they don’t negatively impact your part’s quality and productivity.
Talk to us today about making a rapid prototype with our CNC metal spinning service. Get a direct quote by chatting with us here or request a free project review.
BE-CU China CNC Metal Spinning service include : CNC Metal Spinning,Metal Spinning Die,Laser Cutting, Tank Heads Spinning,Metal Hemispheres Spinning,Metal Cones Spinning,Metal Dish-Shaped Spinning,Metal Trumpet Spinning,Metal Venturi Spinning,Aluminum Spinning Products,Stainless Steel Spinning Products,Copper Spinning Products,Brass Spinning Products,Steel Spinning Product,Metal Spinnin LED Reflector,Metal Spinning Pressure Vessel,