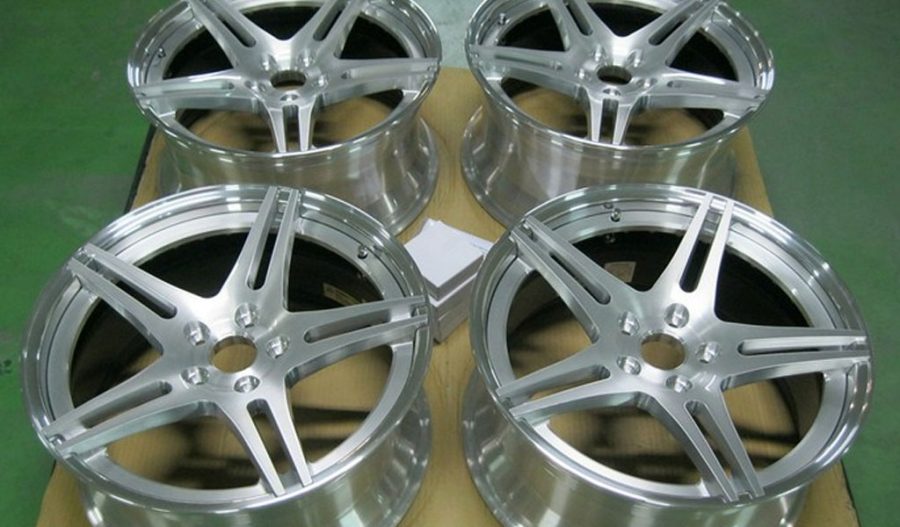
Metal spinning and low pressure casting are two distinct manufacturing processes used in the production of metal components. Each method has its own advantages, limitations, and applications, making them suitable for different industries and purposes. This article delves into the intricacies of both metal spinning and low pressure casting, providing a comprehensive analysis of their processes, materials, tools, applications, and the various factors that influence their selection.
History and Development
Metal Spinning
Metal spinning, also known as spin forming, has its roots in ancient craftsmanship. The process dates back to the early days of metalworking, where artisans manually shaped metal sheets into cylindrical objects using simple tools. The method was primarily used to create objects like bowls, goblets, and other hollow forms.
The industrial revolution in the 18th and 19th centuries brought significant advancements in metal spinning. The introduction of powered lathes and more sophisticated tooling allowed for greater precision and repeatability. By the 20th century, metal spinning had evolved into a well-established manufacturing process, widely used in industries such as aerospace, automotive, and lighting.
Low Pressure Casting
Low pressure casting is a more recent development compared to metal spinning. The process emerged in the early 20th century as a solution to the limitations of traditional gravity casting. It was developed to improve the quality of cast components by minimizing defects such as porosity and shrinkage.
The technique gained popularity in the automotive industry, where the demand for lightweight and high-strength components led to the widespread adoption of low pressure casting. Over the years, the process has been refined with advancements in materials, mold design, and automation, making it a preferred method for producing complex, high-quality metal parts.
Process Overview
Metal Spinning
Metal spinning involves the shaping of a metal disc or tube by rotating it at high speed and applying pressure with a forming tool. The process can be performed either manually or with the aid of a CNC machine.
- Setup: The process begins with the selection of a metal blank, typically a disc or tube, which is mounted onto a spinning lathe.
- Spinning: The lathe rotates the blank at high speed. A roller or forming tool is then brought into contact with the blank, applying pressure to shape it against a mandrel or form.
- Forming: The tool gradually moves along the length of the blank, shaping it into the desired form. The metal is stretched and compressed, following the contour of the mandrel.
- Finishing: Once the desired shape is achieved, the component may undergo additional finishing processes, such as trimming, polishing, or heat treatment.
The versatility of metal spinning allows for the production of a wide range of shapes, including cones, cylinders, hemispheres, and parabolic forms.
Low Pressure Casting
Low pressure casting involves the controlled filling of a mold with molten metal under low pressure, typically between 0.1 to 1.0 bar. The process is designed to produce high-quality castings with minimal defects.
- Preparation: The process starts with the preparation of a mold, which can be made from sand, metal, or a combination of materials. The mold cavity is designed to match the shape of the desired component.
- Melting: Metal is melted in a furnace and maintained at a specific temperature to ensure proper flow and solidification.
- Filling: The molten metal is drawn into the mold cavity through a riser tube by applying low pressure. The pressure ensures a smooth and controlled filling, reducing the likelihood of air entrapment and other defects.
- Solidification: As the metal fills the mold, it begins to cool and solidify. The low pressure is maintained throughout this stage to ensure consistent metal flow and prevent shrinkage defects.
- Ejection: Once the metal has fully solidified, the pressure is released, and the casting is ejected from the mold for further processing, such as machining or heat treatment.
Low pressure casting is particularly well-suited for producing components with intricate geometries and thin walls, such as automotive wheels, engine components, and aerospace parts.
Materials and Tools
Metal Spinning Materials
The choice of material for metal spinning depends on the desired properties of the final component, such as strength, ductility, and corrosion resistance. Common materials used in metal spinning include:
- Aluminum: Known for its light weight and excellent formability, aluminum is widely used in industries such as aerospace and automotive.
- Stainless Steel: Offers high strength and corrosion resistance, making it suitable for applications in food processing, medical devices, and chemical processing.
- Copper and Brass: These materials are valued for their electrical conductivity and aesthetic appeal, often used in architectural and decorative applications.
- Titanium: Preferred for its high strength-to-weight ratio and resistance to corrosion, titanium is commonly used in aerospace and medical applications.
Tools used in metal spinning include:
- Lathe: A machine that rotates the metal blank at high speed, providing the necessary centrifugal force for forming.
- Mandrel: A form or mold against which the metal is shaped. Mandrels can be made from wood, plastic, or metal, depending on the application.
- Forming Tools: These are typically made from hardened steel or carbide and are used to apply pressure to the rotating blank, shaping it against the mandrel.
Low Pressure Casting Materials
Low pressure casting is suitable for a variety of metals, with aluminum alloys being the most commonly used due to their excellent casting properties and widespread application in the automotive industry. Other materials include:
- Magnesium Alloys: Known for their lightweight and high strength-to-weight ratio, magnesium alloys are used in applications where weight reduction is critical.
- Copper Alloys: These materials offer excellent thermal and electrical conductivity, making them suitable for electrical components and heat exchangers.
- Zinc Alloys: Zinc is often used in die casting but can also be employed in low pressure casting for components requiring high precision and detail.
Tools used in low pressure casting include:
- Furnace: A device for melting the metal and maintaining it at the required temperature.
- Mold: A cavity into which the molten metal is poured. Molds can be made from various materials, including sand, steel, and ceramic.
- Riser Tube: A tube that connects the furnace to the mold, through which the molten metal is drawn into the mold under low pressure.
- Pressure System: A system that controls the application of pressure during the casting process, ensuring a smooth and controlled flow of metal into the mold.
Advantages and Disadvantages
Metal Spinning
Advantages:
- Versatility: Metal spinning can produce a wide range of shapes and sizes, making it suitable for diverse applications.
- Material Efficiency: The process generates minimal waste, as the metal is formed rather than cut away.
- Strength: The metal is work-hardened during the spinning process, resulting in a component with enhanced strength and durability.
- Cost-Effective for Small Batches: Metal spinning is economical for low-volume production, especially when compared to processes that require expensive molds or dies.
Disadvantages:
- Limited Complexity: While metal spinning is versatile, it is not ideal for producing highly complex or detailed geometries.
- Thickness Variation: The process can result in uneven wall thickness, especially for deep or complex shapes.
- Tooling Wear: The forming tools can wear out over time, especially when working with hard materials, leading to increased maintenance costs.
Low Pressure Casting
Advantages:
- High Quality: Low pressure casting produces components with excellent surface finish, dimensional accuracy, and minimal defects.
- Complex Geometries: The process is well-suited for producing components with intricate shapes and thin walls.
- Material Utilization: The controlled filling process minimizes waste and reduces the likelihood of defects, leading to higher material utilization.
- Consistency: Low pressure casting offers excellent repeatability and consistency, making it ideal for high-volume production.
Disadvantages:
- Initial Investment: The process requires specialized equipment and molds, leading to higher initial costs.
- Longer Cycle Times: Compared to other casting methods, low pressure casting can have longer cycle times due to the need for controlled filling and solidification.
- Limited Material Range: While suitable for a variety of metals, low pressure casting is not ideal for all materials, particularly those with high melting points.
Applications
Metal Spinning Applications
Metal spinning is used across a wide range of industries, including:
- Aerospace: Production of nose cones, engine components, and other cylindrical or conical parts.
- Automotive: Manufacturing of wheel rims, exhaust components, and decorative trims.
- Lighting: Creation of reflector housings, lampshades, and other lighting fixtures.
- Architectural: Fabrication of ornamental components, such as domes, spires, and columns.
Low Pressure Casting Applications
Low pressure casting is commonly used in industries that require high-quality, complex components, such as:
- Automotive: Production of engine blocks, cylinder heads, and wheels.
- Aerospace: Manufacturing of structural components, turbine blades, and other high-performance parts.
- Industrial Equipment: Creation of pump housings, valves, and other machinery components.
- Electronics: Casting of heat sinks, enclosures, and other components requiring high thermal conductivity.
Comparison of Metal Spinning and Low Pressure Casting
Process Efficiency
Metal spinning is generally faster for producing simple, cylindrical shapes, especially in low to medium volumes. The lack of a need for complex molds or dies allows for rapid prototyping and shorter lead times. However, for more complex geometries, low pressure casting is often more efficient, as it can produce intricate details in a single operation.
Material Properties
Metal spinning can enhance the strength of the final component due to work hardening. However, it may result in uneven material properties, particularly in components with varying wall thicknesses. Low pressure casting, on the other hand, offers more uniform material properties and is better suited for components requiring consistent mechanical performance.
Cost Considerations
The cost-effectiveness of each process depends on the production volume and the complexity of the component. Metal spinning is more economical for small batches or prototypes, as it does not require expensive molds. Low pressure casting, while having higher initial costs, becomes more cost-effective for high-volume production due to its ability to produce complex shapes with high repeatability.
Environmental Impact
Both processes have relatively low environmental impacts compared to other manufacturing methods. Metal spinning generates minimal waste, as the material is formed rather than cut away. Low pressure casting also minimizes waste through efficient material utilization and reduced defect rates. However, the energy consumption of each process varies depending on the material and the specific application.
Future Trends and Developments
Metal Spinning Innovations
The future of metal spinning lies in advancements in automation and materials. CNC spinning machines are becoming increasingly sophisticated, allowing for greater precision and the ability to spin more complex geometries. Additionally, the development of new materials and alloys will expand the range of applications for metal spinning.
Low Pressure Casting Innovations
Low pressure casting is expected to benefit from advancements in mold design and materials. The use of 3D printing for mold production is likely to reduce lead times and costs, making the process more accessible for smaller manufacturers. Additionally, the development of new alloys and composite materials will enhance the performance and application of low pressure cast components.
Conclusion
Metal spinning and low pressure casting are both valuable manufacturing processes, each with its own strengths and weaknesses. The choice between the two depends on a variety of factors, including the desired properties of the final component, the complexity of the geometry, and the production volume. As technology continues to advance, both processes are likely to evolve, offering new opportunities and applications in a wide range of industries.
Maximize Tooling and CNC Metal Spinning Capabilities.
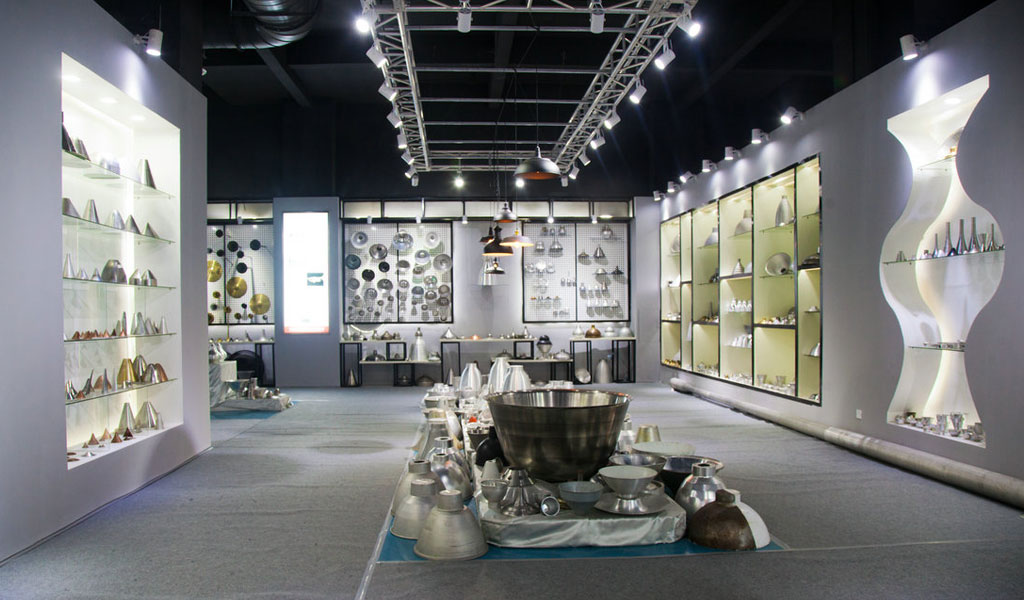
At BE-CU China Metal Spinning company, we make the most of our equipment while monitoring signs of excess wear and stress. In addition, we look into newer, modern equipment and invest in those that can support or increase our manufacturing capabilities. Our team is very mindful of our machines and tools, so we also routinely maintain them to ensure they don’t negatively impact your part’s quality and productivity.
Talk to us today about making a rapid prototype with our CNC metal spinning service. Get a direct quote by chatting with us here or request a free project review.
BE-CU China CNC Metal Spinning service include : CNC Metal Spinning,Metal Spinning Die,Laser Cutting, Tank Heads Spinning,Metal Hemispheres Spinning,Metal Cones Spinning,Metal Dish-Shaped Spinning,Metal Trumpet Spinning,Metal Venturi Spinning,Aluminum Spinning Products,Stainless Steel Spinning Products,Copper Spinning Products,Brass Spinning Products,Steel Spinning Product,Metal Spinnin LED Reflector,Metal Spinning Pressure Vessel,