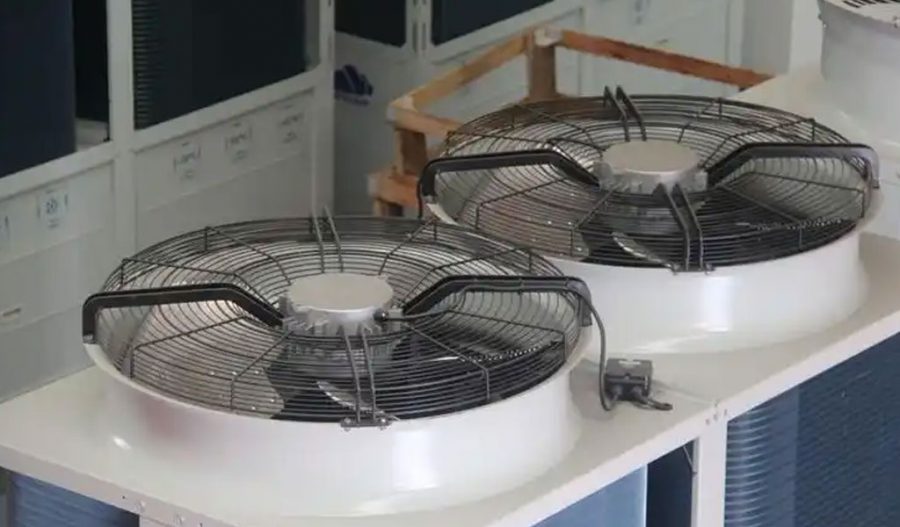
Metal spinning, a process that involves rotating a metal disc or tube at high speeds and shaping it into cylindrical or conical forms, is integral to various industries, including HVAC (Heating, Ventilation, and Air Conditioning). This versatile and cost-effective manufacturing process allows for the creation of precision components with exceptional strength, uniform thickness, and intricate shapes. In the HVAC sector, metal spinning is used to fabricate components that require high durability, thermal resistance, and efficient airflow. This article explores the top 20 metal spinning applications within the HVAC industry, highlighting their significance, the materials involved, and the role of this process in modern HVAC technologies.
1. HVAC Ductwork Components
Ductwork components are central to HVAC systems, facilitating the transportation of air throughout buildings. Metal spinning is used to create air ducts, fittings, and elbows, which require precise dimensions and smooth surfaces to maintain airflow efficiency. The process ensures that these components have uniform wall thicknesses, minimal welds, and a high degree of symmetry, contributing to optimal airflow and minimal energy loss.
Spun aluminum, galvanized steel, and stainless steel are commonly used materials for HVAC duct components due to their resistance to corrosion and lightweight properties. The ability of metal spinning to produce seamless and consistent parts without the need for extensive welding is crucial for the long-term performance of HVAC ductwork systems.
2. Ventilation Grills and Diffusers
Ventilation grills and diffusers are essential elements in HVAC systems, controlling the distribution and direction of airflow within a building. Metal spinning offers an ideal solution for producing these components with intricate designs and tight tolerances. By spinning materials like aluminum or stainless steel, manufacturers can create vents and diffusers with complex geometries that enhance the aesthetic appeal and functional performance of HVAC systems.
Spun metal parts also ensure superior durability and resistance to wear, making them ideal for use in environments where ventilation systems are subject to high levels of stress and frequent handling. The precision offered by metal spinning allows for the creation of grills and diffusers that fit perfectly into the ductwork, reducing air leaks and improving system efficiency.
3. Fan Housings
Fan housings are critical to the operation of HVAC systems, protecting the fan blades and ensuring consistent airflow. These components must be manufactured with high accuracy to avoid vibration, reduce noise, and maximize energy efficiency. Metal spinning allows for the creation of fan housings with smooth surfaces and consistent geometries, contributing to the overall performance of the HVAC system.
Aluminum and stainless steel are frequently chosen for fan housing production due to their excellent corrosion resistance and ability to withstand high temperatures. The spinning process allows for the production of lightweight yet robust fan housings, which is crucial for both residential and industrial HVAC applications.
4. HVAC Condenser and Evaporator Coils
Condenser and evaporator coils are central to the heat exchange process in HVAC systems, responsible for transferring heat between the air and the refrigerant. Metal spinning is used to fabricate these coils from materials such as copper, aluminum, and brass, which have high thermal conductivity. The spinning process enables the creation of coils with precise dimensions, uniform wall thicknesses, and smooth internal surfaces, optimizing the heat transfer capabilities of the system.
The use of metal spinning in coil production offers several advantages, including reduced material waste, improved heat exchange efficiency, and faster production times compared to traditional manufacturing methods like welding or casting.
5. Air Handling Unit Casings
Air handling units (AHUs) are integral to HVAC systems, responsible for conditioning and circulating air. The casings of these units are typically made from sheet metal and are subject to high levels of wear and tear. Metal spinning is an ideal method for producing the casings of AHUs, as it allows for the creation of seamless, strong, and durable components. These casings are spun from materials such as galvanized steel or stainless steel, ensuring that they can withstand the harsh conditions of HVAC systems.
The precise nature of the metal spinning process helps minimize the risk of deformation and ensures that the AHU casings are airtight, improving energy efficiency and system performance.
6. Round and Square Transitions
Round and square transitions are used in HVAC systems to connect ducts of different shapes and sizes. These transitions must be manufactured with high precision to ensure an airtight seal and efficient airflow between the connected ducts. Metal spinning allows for the creation of smooth, uniform transitions that minimize air resistance and prevent leaks, contributing to the overall efficiency of the HVAC system.
Materials such as galvanized steel, aluminum, and stainless steel are often used in the production of these transitions, as they offer the required strength, durability, and corrosion resistance for long-term performance in HVAC applications.
7. HVAC Vibration Dampeners
Vibration dampeners are crucial components in HVAC systems, designed to reduce noise and vibrations caused by moving air or mechanical equipment. Metal spinning is used to produce vibration dampeners, such as flexible metal connectors and isolators, which help prevent the transmission of vibrations throughout the system. These components are typically made from materials like stainless steel, which offers excellent strength and flexibility.
By using metal spinning, manufacturers can create vibration dampeners with precise geometries, ensuring that they effectively absorb and dissipate vibrations while maintaining the structural integrity of the HVAC system.
8. Heat Exchanger Components
Heat exchangers are essential in HVAC systems, transferring heat between fluids or gases to regulate temperatures. The construction of heat exchanger components, such as manifolds and plates, requires materials that can withstand high temperatures and pressure while maintaining excellent thermal conductivity. Metal spinning is used to fabricate these components from metals like copper, aluminum, and stainless steel, which provide the necessary thermal properties and durability.
Spun metal heat exchanger components offer advantages such as improved surface area for heat transfer, reduced material waste, and lower manufacturing costs compared to traditional fabrication methods.
9. Blower Fan Components
Blower fans are responsible for circulating air in HVAC systems, and their components, such as fan blades and housings, must be carefully manufactured to ensure optimal performance. Metal spinning is used to produce blower fan components with high precision, allowing for the creation of aerodynamic shapes that minimize energy loss and noise while maximizing airflow efficiency.
Materials such as aluminum and stainless steel are commonly used for these components, providing the necessary strength and corrosion resistance for long-lasting performance in HVAC applications.
10. HVAC Dampers
Dampers are used to regulate the flow of air in HVAC systems, controlling the volume of air entering or leaving a duct. Metal spinning is ideal for producing damper components, such as blades, shafts, and housings, with precise dimensions and smooth surfaces that ensure consistent airflow. These components are typically made from galvanized steel or stainless steel, which offer the required strength and resistance to corrosion.
Spinning allows for the creation of damper components with minimal tolerances, ensuring that the damper operates efficiently without leakage or resistance.
11. Exhaust Hoods
Exhaust hoods are an essential part of HVAC systems, especially in commercial kitchens and industrial applications, where they capture and remove smoke, fumes, and heat from the air. Metal spinning is used to create these hoods, which are typically made from stainless steel for its high heat resistance and ease of cleaning. The spinning process allows for the creation of smooth, seamless hoods that effectively channel exhaust gases while minimizing energy loss.
The precise nature of metal spinning ensures that the exhaust hoods fit securely in place, reducing the risk of air leaks and improving overall system efficiency.
12. Airflow Regulators
Airflow regulators are used in HVAC systems to control and adjust the flow of air through ducts, diffusers, and vents. Metal spinning is used to produce regulator components with high precision, ensuring that they operate smoothly and efficiently. These components are typically made from materials such as aluminum or galvanized steel, which provide the necessary durability and corrosion resistance for long-term performance.
The use of metal spinning in the production of airflow regulators ensures that they are manufactured to exact specifications, contributing to the overall efficiency and reliability of HVAC systems.
13. HVAC Piping Fittings
Piping fittings are essential for connecting various sections of piping in HVAC systems. These fittings must be manufactured to precise specifications to ensure airtight seals and efficient fluid or air flow. Metal spinning is used to create various types of piping fittings, including elbows, tees, and reducers, from materials such as stainless steel and brass.
The ability to produce seamless, uniform parts with minimal material waste makes metal spinning an ideal process for HVAC piping fittings. The high precision achieved through spinning also ensures that these fittings are compatible with other system components, reducing the risk of leaks and system inefficiencies.
14. Chimney Caps
Chimney caps are used to cover and protect chimneys in HVAC systems, preventing debris, rain, and animals from entering the flue. Metal spinning is used to fabricate these caps, which are typically made from stainless steel or aluminum for their corrosion resistance and ability to withstand high temperatures. The spinning process allows for the creation of caps with smooth, uniform surfaces that ensure a secure fit and effective protection.
The precision and durability of spun metal chimney caps contribute to the long-term performance and safety of HVAC systems that include chimney ventilation.
15. Air Conditioning Covers
Air conditioning units are exposed to the elements, which can lead to wear and damage over time. Metal spinning is used to produce protective covers for air conditioning units, which are typically made from aluminum or galvanized steel. These covers are designed to shield the unit from rain, snow, and debris while allowing for proper airflow and ventilation.
Spinning allows for the creation of covers with minimal seams, reducing the risk of corrosion and ensuring a long lifespan for HVAC systems.
16. Air Purifier Casings
Air purifiers are increasingly used in HVAC systems to improve indoor air quality by filtering out pollutants, allergens, and particulates. The casings of these air purifiers are often produced using metal spinning, which allows for the creation of seamless, durable, and precisely manufactured components. Materials such as stainless steel are commonly used for their strength and resistance to corrosion.
The use of metal spinning ensures that air purifier casings are both functional and aesthetically pleasing, contributing to the overall performance and appearance of HVAC systems.
17. Induction Fan Blades
Induction fan blades are used in certain HVAC systems to promote the movement of air. These fan blades are typically made from lightweight metals such as aluminum, which allows them to operate efficiently at high speeds. Metal spinning is employed to produce these blades, allowing for precise control over the shape and thickness of the components.
The spinning process also minimizes material waste, making it an environmentally friendly choice for fan blade production in HVAC systems.
18. Expansion Tanks
Expansion tanks are used in HVAC systems to accommodate the expansion of water or air as it heats up, preventing pressure buildup. Metal spinning is used to create these tanks, which are typically made from stainless steel or carbon steel for their strength and durability. The spinning process allows for the creation of tanks with smooth, uniform surfaces that help to reduce the risk of leaks and ensure reliable system operation.
19. HVAC Manifold Components
Manifold components are used in HVAC systems to distribute air or fluid to various parts of the system. These components are typically manufactured using metal spinning, which allows for the creation of high-precision parts that ensure smooth and efficient airflow. Materials such as stainless steel are commonly used for these components, providing the necessary strength and corrosion resistance for long-term performance.
20. Roof Vents
Roof vents are used in HVAC systems to allow air to exit a building or structure. These vents must be designed to withstand the elements while providing effective ventilation. Metal spinning is used to create roof vent components that are durable, lightweight, and resistant to corrosion. Spun metal roof vents ensure efficient airflow and contribute to the overall energy efficiency of the HVAC system.