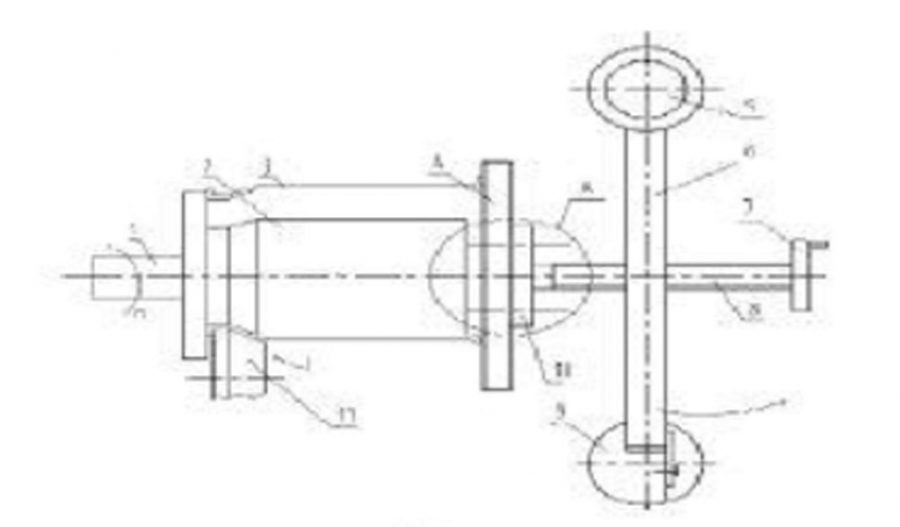
As a typical continuous local plastic forming technology, spinning has become an important development direction of plastic forming technology due to its static pressure (no impact, vibration, environmental damage), high product precision, good process flexibility, easy mechanization and automation, and material saving. It is an advanced manufacturing technology that realizes thin-walled rotating parts with little or no cutting. After the middle of the 20th century, with the development of industry, the spinning process was widely used in the field of metal sheet forming, which promoted the research and development of this process. Many European and American countries have produced advanced spinning equipment with a high degree of standardization. Although the development of spinning technology in my country is still very backward, it has made great progress in recent years. The precision and performance of many products have approached or reached the advanced level of foreign countries.
The principle of metal spinning is to put the processed metal blank (tube blank) on the core mold, press it on the end of the core mold through the tail top, and rotate with the main shaft together with the core mold. The spinning wheel moves along the core mold. Under the pressure of the spinning wheel, the plasticity of the metal is used to process the metal parts point by point into the required hollow rotary parts. The characteristics of spinning: it has the advantages of saving raw materials, low cost, simple equipment and high product quality. Therefore, the spinning process has played an increasingly important role in many industries such as national defense, chemical industry, metallurgy, electronics, machinery, etc., and the barrel making industry is also used in it.
During the working process, the workpiece 3 is put on the core mold 2, the tail push mechanism 6 rotates clockwise along the column 5 to the position shown in the figure, the handle 7 is turned to make the top plate 4 support the workpiece, the spinning wheel 11 is moved to make the workpiece close to the core mold, the main shaft 1 is started, and the spinning wheel is fed at a uniform speed until the shrinking process is completed; the main shaft stops, the spinning wheel retreats to its original position, the handle 7 is rotated to move the top plate 4 to the right, the tail push mechanism rotates counterclockwise, and the workpiece is taken out.
Problems in necking forming and structural improvement of the tail top device
The tail top device of the original equipment is in rigid contact with the end face of the barrel body. The length of the barrel body will extend during the forming process. When the pressure exceeds the buckling limit of the barrel, the barrel body will buckle, which affects the quality of the product. Based on the above problems, I carefully analyzed and changed the rigid tail fixed device to elastic. In this way, it can not only ensure that the tail top has a certain pressure on the barrel body during the forming process, but also ensure that the spring is compressed during the elongation of the barrel body to make the length “free” (free under pressure) elongate. As shown in Figure 2.
The original screw 8 is changed into two parts, and a connecting rod is added. It is still connected to the top plate 4 in a floating manner, and is connected to the screw by elasticity, as shown in (Figure 2) A (after modification). When the length of the product is extended during the forming process, the top plate 4 and the connecting rod are pressed and moved to the right, and the spring is compressed, thereby avoiding the buckling of the product.
Conclusion
The above is the whole process of the problems and solutions I encountered in the actual production of metal barrel parts. By improving the structure of the tail top device, the scrap rate was reduced and the product quality was guaranteed. This improvement idea was inspired by the elastic pressure (discharge) material structure in the design of punching dies for many years. It was applied to the tail top device structure and achieved good results, indicating that this improvement is feasible.
Maximize Tooling and CNC Metal Spinning Capabilities.
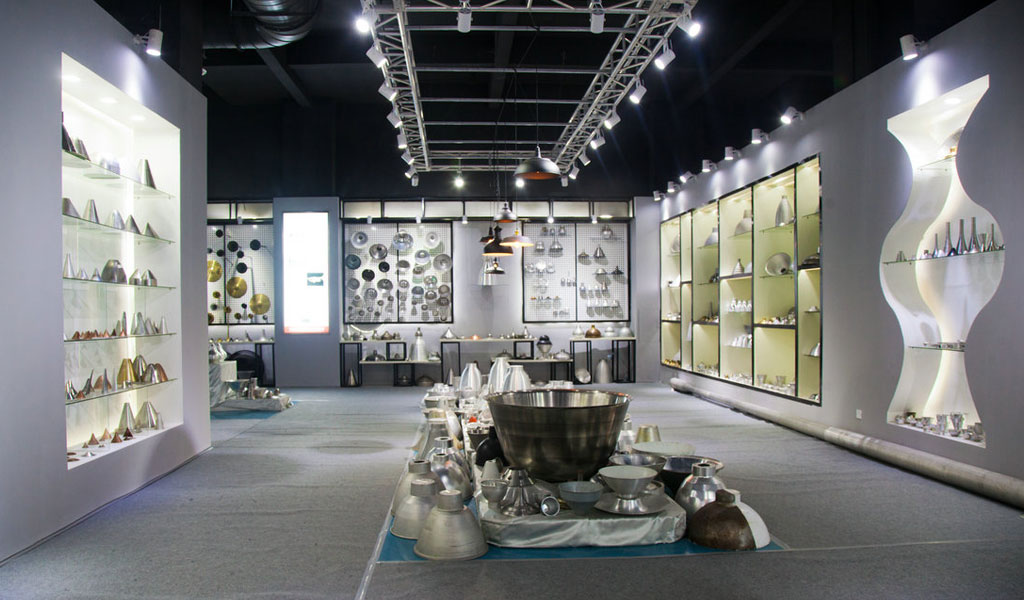
At BE-CU China Metal Spinning company, we make the most of our equipment while monitoring signs of excess wear and stress. In addition, we look into newer, modern equipment and invest in those that can support or increase our manufacturing capabilities. Our team is very mindful of our machines and tools, so we also routinely maintain them to ensure they don’t negatively impact your part’s quality and productivity.
Talk to us today about making a rapid prototype with our CNC metal spinning service. Get a direct quote by chatting with us here or request a free project review.
BE-CU China CNC Metal Spinning service include : CNC Metal Spinning,Metal Spinning Die,Laser Cutting, Tank Heads Spinning,Metal Hemispheres Spinning,Metal Cones Spinning,Metal Dish-Shaped Spinning,Metal Trumpet Spinning,Metal Venturi Spinning,Aluminum Spinning Products,Stainless Steel Spinning Products,Copper Spinning Products,Brass Spinning Products,Steel Spinning Product,Metal Spinnin LED Reflector,Metal Spinning Pressure Vessel,