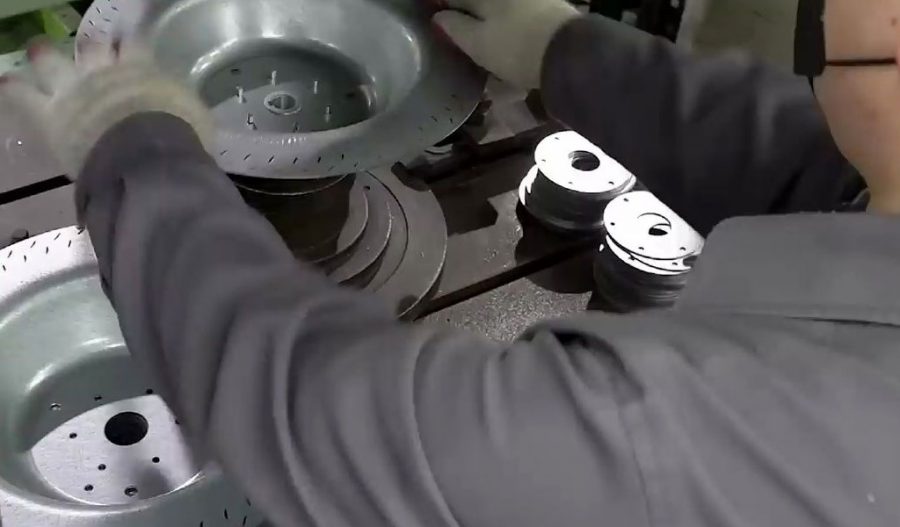
The fabrication of aluminum drum shells represents a fascinating intersection of materials science, acoustics, and craftsmanship. Aluminum, a lightweight, durable, and corrosion-resistant metal, has become a popular choice in the construction of drum shells due to its unique sonic properties and manufacturing versatility. This article delves into the intricate process of creating an aluminum drum shell, exploring the metallurgical principles, engineering techniques, and practical steps involved. By examining the properties of aluminum alloys, the methods of forming drum shells, and the acoustic outcomes, we aim to provide a thorough, scientifically grounded understanding of this process. Detailed tables comparing alloys, forming techniques, and finishing methods will supplement the discussion, ensuring a robust and data-driven analysis.
Aluminum, with the atomic number 13 and symbol Al, is the third most abundant element in the Earth’s crust, constituting approximately 8% by weight. Its widespread use in drum manufacturing stems from its favorable strength-to-weight ratio, machinability, and ability to be alloyed with other elements to enhance specific properties. The process of crafting an aluminum drum shell begins with the selection of an appropriate alloy, proceeds through forming and shaping techniques, and concludes with finishing processes that influence both aesthetics and sound quality. Each step requires precision and an understanding of how material properties translate into the final product—a resonant, durable drum shell capable of delivering a wide range of tones.
Aluminum Alloys in Drum Shell Construction
The first critical decision in aluminum drum shell fabrication is the choice of alloy. Pure aluminum, while lightweight and corrosion-resistant, lacks the mechanical strength required for a drum shell that must withstand tension from drumheads and repeated striking. Therefore, manufacturers typically employ aluminum alloys, which are mixtures of aluminum with other elements such as magnesium, silicon, copper, or zinc. These alloys are categorized into series based on their primary alloying element, as defined by the Aluminum Association’s nomenclature system.
The 6000-series alloys, particularly 6061, are among the most commonly used for drum shells. Alloy 6061 consists of aluminum alloyed with approximately 1% magnesium and 0.6% silicon, offering a balance of strength, weldability, and corrosion resistance. Its tensile strength typically ranges from 124–290 MPa, depending on temper (heat treatment), making it suitable for both rolled and extruded drum shells. Another contender is the 5000-series, such as 5052, which includes magnesium as the primary alloying element (approximately 2.5%). This alloy provides excellent corrosion resistance and formability, with a yield strength of around 193 MPa in its H32 temper, though it is less suited to welding than 6061.
For high-end applications, some manufacturers opt for the 7000-series, such as 7075, which incorporates zinc (5.6–6.1%) and offers exceptional strength, with tensile strengths exceeding 500 MPa in its T6 temper. However, 7075 is more brittle and costly, requiring careful handling during forming processes. The choice of alloy influences not only the structural integrity of the drum shell but also its acoustic properties—higher strength alloys tend to produce brighter, more focused tones, while softer alloys may yield warmer, more diffuse sounds.
Alloy Series | Primary Alloying Element | Typical Alloy | Tensile Strength (MPa) | Yield Strength (MPa) | Formability | Weldability | Corrosion Resistance | Acoustic Character |
---|---|---|---|---|---|---|---|---|
5000 | Magnesium | 5052 | 228 (H32) | 193 | Excellent | Moderate | Excellent | Warm, diffuse |
6000 | Magnesium + Silicon | 6061 | 124–290 (T6) | 55–276 | Good | Excellent | Good | Bright, balanced |
7000 | Zinc | 7075 | 572 (T6) | 503 | Moderate | Poor | Moderate | Sharp, focused |
Raw Material Preparation
Once the alloy is selected, the aluminum must be prepared in a form suitable for drum shell fabrication. Aluminum is typically supplied in sheets or billets, depending on the forming method. For rolled or spun shells, sheets of uniform thickness (commonly 1.5–3 mm for drum applications) are procured. These sheets are produced through hot rolling or cold rolling processes, where aluminum ingots are passed through rollers to achieve the desired gauge. Cold rolling enhances surface finish and dimensional precision, which are critical for consistent shell thickness—a key factor in uniform sound projection.
Billets, cylindrical blocks of aluminum, are used for extrusion or casting methods. Extrusion involves forcing heated aluminum (typically at 400–500°C) through a die to create a continuous tube, which is then cut to length. This method ensures a seamless shell, eliminating the need for welding and reducing potential weak points. The extrusion process aligns the grain structure of the aluminum, enhancing its strength along the length of the shell, which aligns with the direction of vibrational stress during drumming.
Forming Techniques
The transformation of raw aluminum into a cylindrical drum shell involves several forming techniques, each with distinct advantages and implications for the final product. The three primary methods are rolling and welding, spinning, and extrusion.
Rolling and Welding
Rolling begins with a flat aluminum sheet cut to precise dimensions based on the desired shell diameter and depth. For a standard 14-inch diameter snare drum with a 6.5-inch depth, the sheet’s width would approximate the circumference (π × 14 ≈ 43.98 inches, or 111.7 cm), and its length would match the depth (6.5 inches, or 16.5 cm). The sheet is then fed into a rolling machine, where it is bent around a mandrel—a cylindrical form—until the edges meet. This forms a seam, which is typically welded using tungsten inert gas (TIG) welding due to its precision and ability to produce clean, strong joints in aluminum.
The welding process introduces heat-affected zones (HAZs) near the seam, where the alloy’s microstructure may soften, potentially reducing strength by 10–20% compared to the base material. To mitigate this, post-weld heat treatment (e.g., annealing at 300–400°C followed by controlled cooling) can restore uniformity. The seam’s placement is acoustically significant—positioned parallel to the shell’s axis, it minimally disrupts radial vibrations, preserving the drum’s resonance. Rolled and welded shells are cost-effective and widely used in mass production, though the seam may subtly influence tone, often adding a slight metallic “zing.”
Metal Spinning
Metal spinning offers a seamless alternative, producing shells with exceptional uniformity. A flat aluminum disc, slightly larger than the final shell’s diameter, is clamped against a spinning mandrel on a lathe. As the disc rotates at high speed (typically 500–1000 RPM), a forming tool gradually presses the aluminum over the mandrel, stretching and thinning the material into a cylindrical shape. For a 14-inch diameter shell, the disc might start at 16–18 inches to account for material flow and trimming.
Spinning work-hardens the aluminum, increasing its strength by aligning the grain structure circumferentially. This enhances the shell’s ability to withstand hoop stress from drumhead tension, which can exceed 1000 N for a tightly tuned head. The absence of a seam eliminates potential vibrational discontinuities, resulting in a clearer, more resonant tone. However, spinning requires skilled labor and specialized equipment, making it more expensive than rolling. Thickness variations—thinner at the edges (e.g., 1.2 mm) and thicker near the center (e.g., 1.8 mm)—can also occur, subtly affecting sound projection.
Extrusion
Extrusion produces seamless shells directly from aluminum billets. The billet is preheated to its plastic deformation range (400–500°C) and forced through a circular die under high pressure (up to 1000 tons). The resulting tube is cooled, cut to length, and machined to precise dimensions. Extruded shells offer consistent wall thickness (typically 2–3 mm) and a smooth interior surface, minimizing internal reflections that could muddy the tone. The process is highly automated, ensuring repeatability, but initial setup costs for dies are significant, making it economical only for large-scale production.
Forming Method | Seam | Thickness Uniformity | Strength Enhancement | Cost | Labor Skill | Acoustic Impact |
---|---|---|---|---|---|---|
Rolling + Welding | Yes | High | Moderate (post-weld) | Low | Moderate | Slight metallic overtone |
Spinning | No | Moderate (variable) | High (work-hardening) | High | High | Clear, resonant |
Extrusion | No | Very High | Moderate (grain-aligned) | Moderate | Low | Focused, consistent |
Machining and Reinforcement
After forming, the shell undergoes machining to refine its shape and add functional features. Edges are trimmed to ensure flat, parallel bearing edges—the surfaces where the drumhead rests. The bearing edge profile significantly affects sound: a 45° single-cut edge produces a bright, articulate tone by focusing head vibration, while a rounded edge softens the attack for a warmer sound. Precision is critical—variations as small as 0.1 mm can alter pitch and sustain.
Holes are drilled for lugs, tension rods, and vents using computer numerical control (CNC) machines to ensure alignment and repeatability. For a 14-inch snare with 10 lugs, 20 holes (10 per side) are typically spaced equidistantly around the circumference (every 36°). Reinforcing rings, often made from thicker aluminum (e.g., 3–5 mm), may be welded or press-fit near the edges to increase stiffness and reduce unwanted overtones. These rings increase the shell’s mass, slightly lowering its resonant frequency, a trade-off for enhanced durability.
Finishing Processes
The shell’s surface finish influences both aesthetics and acoustics. Raw aluminum oxidizes naturally, forming a thin Al₂O₃ layer that protects against corrosion but may appear dull. Polishing with abrasives (e.g., 400–1200 grit sandpaper followed by buffing compounds) creates a mirror-like finish, enhancing visual appeal and slightly brightening the tone by reducing surface damping. Anodizing, an electrochemical process, thickens the oxide layer (to 10–25 µm), improving durability and allowing color customization. Anodized shells resist scratches and maintain tonal clarity, though thick coatings may dampen high frequencies.
Powder coating, where a polymer powder is electrostatically applied and baked at 180–200°C, adds a protective, textured layer (50–100 µm). This increases mass and damping, producing a darker, more controlled sound, though it may reduce projection. Each finish alters the shell’s boundary conditions—polished surfaces reflect vibrations efficiently, while textured finishes absorb energy, affecting sustain and overtones.
Finish Type | Process | Thickness (µm) | Durability | Aesthetic | Acoustic Effect |
---|---|---|---|---|---|
Polished | Abrasive buffing | N/A (surface) | Moderate | Shiny, reflective | Bright, sustained |
Anodized | Electrochemical oxidation | 10–25 | High | Colored, matte | Clear, slightly damped |
Powder Coated | Electrostatic + heat curing | 50–100 | Very High | Textured, matte | Darker, controlled |
Acoustic Properties and Testing
The completed aluminum shell’s acoustic performance depends on its material, geometry, and construction. Aluminum’s high stiffness (Young’s modulus ≈ 70 GPa) and low density (2.7 g/cm³) yield a high speed of sound (≈ 5000 m/s), producing a fast attack and bright tone compared to wood (e.g., maple, 1.5 g/cm³, 4000 m/s). Shell depth influences pitch—deeper shells (e.g., 8 inches) resonate at lower frequencies than shallow ones (e.g., 5 inches)—while diameter affects volume and projection, with larger shells (e.g., 16 inches) delivering greater output.
Testing involves mounting the shell with heads (typically polyester or coated fabric) and tuning to a range of tensions (50–150 N per tension rod). Frequency analysis using a microphone and spectrum analyzer reveals the fundamental tone and overtones. For a 14×6.5-inch 6061 shell, the fundamental might center at 200–250 Hz, with prominent harmonics at 400–600 Hz, contributing to its characteristic “crack.” Spun or extruded shells often exhibit fewer unwanted overtones due to their seamless construction, while welded shells may introduce subtle noise from the seam.
Practical Steps for Fabrication
For an individual or small-scale manufacturer, crafting an aluminum drum shell is feasible with the right tools and materials. Begin by selecting a 6061-T6 sheet (2 mm thick) and cutting it to size (e.g., 111.7 × 16.5 cm for a 14×6.5-inch shell). Roll the sheet using a slip roller, adjusting pressure incrementally to avoid cracking. TIG weld the seam with a 4043 filler rod, maintaining a steady arc to minimize HAZ. Trim and machine the edges with a router or lathe, cutting a 45° bearing edge. Drill lug holes with a CNC drill press or template-guided hand drill. Polish the surface with progressively finer abrasives, then anodize if desired. Assemble with heads, lugs, and tension rods, tuning to taste.
Conclusion
The fabrication of an aluminum drum shell is a multidisciplinary endeavor, blending metallurgy, mechanics, and acoustics. From alloy selection to finishing, each step shapes the shell’s durability, appearance, and sound. Whether rolled, spun, or extruded, aluminum shells offer a distinctive voice in percussion—bright, responsive, and enduring. This exploration, supported by detailed comparisons, underscores the scientific precision and artistry behind this process, inviting further experimentation and innovation in drum design.
Maximize Tooling and CNC Metal Spinning Capabilities.
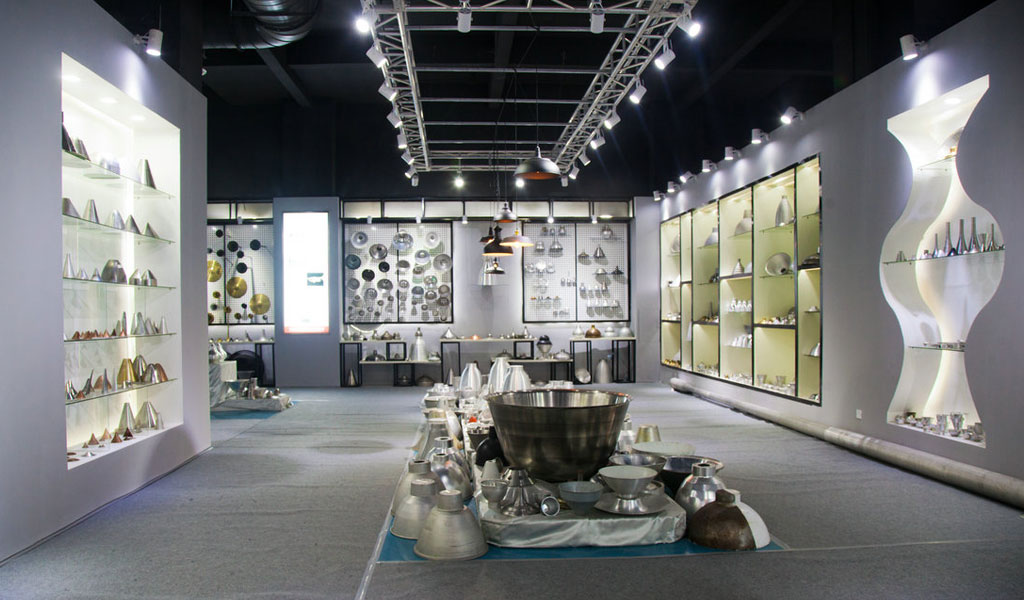
At BE-CU China Metal Spinning company, we make the most of our equipment while monitoring signs of excess wear and stress. In addition, we look into newer, modern equipment and invest in those that can support or increase our manufacturing capabilities. Our team is very mindful of our machines and tools, so we also routinely maintain them to ensure they don’t negatively impact your part’s quality and productivity.
Talk to us today about making a rapid prototype with our CNC metal spinning service. Get a direct quote by chatting with us here or request a free project review.
BE-CU China CNC Metal Spinning service include : CNC Metal Spinning,Metal Spinning Die,Laser Cutting, Tank Heads Spinning,Metal Hemispheres Spinning,Metal Cones Spinning,Metal Dish-Shaped Spinning,Metal Trumpet Spinning,Metal Venturi Spinning,Aluminum Spinning Products,Stainless Steel Spinning Products,Copper Spinning Products,Brass Spinning Products,Steel Spinning Product,Metal Spinnin LED Reflector,Metal Spinning Pressure Vessel,