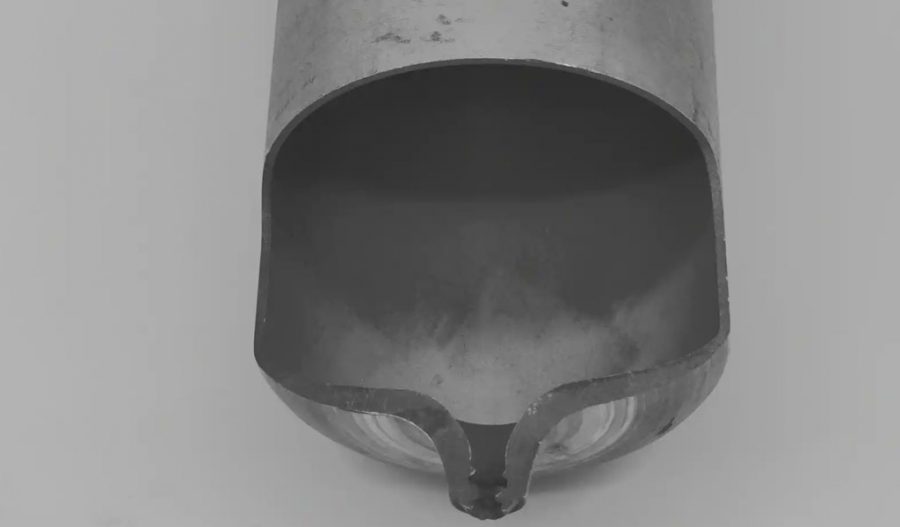
Spinning technology, a cornerstone of mechanical engineering, has found diverse applications across various industries. One of the most intriguing and practical applications is in the design and operation of pulleys. Pulleys, simple machines used to change the direction of a force, are integral components in mechanical systems ranging from elevators to cranes and conveyor belts. The integration of spinning technology in pulleys has revolutionized their efficiency, durability, and overall performance. This article delves into the multifaceted application of spinning technology in pulleys, exploring its historical context, technological advancements, and practical implications.
Historical Context
The concept of pulleys dates back to ancient civilizations, where they were used for lifting heavy objects and facilitating construction. The earliest known pulleys were simple wooden wheels with grooves, around which ropes were wound. Over time, the design evolved to include more sophisticated materials and mechanisms. The introduction of spinning technology marked a significant milestone in the evolution of pulleys. Spinning, a process involving the rapid rotation of a material to shape it, allowed for the creation of more precise and durable pulley components.
Technological Advancements
Material Science and Spinning Technology
The advancement of material science has played a crucial role in the development of spinning technology for pulleys. Traditional materials like wood and iron have been replaced by more advanced materials such as steel, aluminum, and composite materials. These materials offer superior strength, durability, and resistance to wear and tear. The spinning process involves heating the material to a malleable state and then rapidly rotating it to shape it into the desired form. This process ensures uniform distribution of material, reducing the likelihood of defects and enhancing the overall structural integrity of the pulley.
Design and Manufacturing
The design of pulleys has undergone significant changes with the advent of spinning technology. Traditional pulleys were often bulky and inefficient, with limited load-bearing capacity. Spinning technology has enabled the creation of lighter, more compact pulleys with enhanced load-bearing capabilities. The spinning process allows for the precise shaping of the pulley wheel, ensuring that the grooves are uniform and the surface is smooth. This precision is crucial for reducing friction and improving the efficiency of the pulley system.
Comparative Analysis of Traditional vs. Spun Pulleys
Feature | Traditional Pulleys | Spun Pulleys |
---|---|---|
Material | Wood, Iron | Steel, Aluminum, Composite Materials |
Manufacturing Process | Manual crafting, Casting | Spinning |
Weight | Heavy | Lightweight |
Load-Bearing Capacity | Limited | High |
Durability | Moderate | Excellent |
Friction | High | Low |
Efficiency | Low to Moderate | High |
Cost | Low to Moderate | Moderate to High |
Maintenance | Frequent | Minimal |
Practical Implications
Industrial Applications
The application of spinning technology in pulleys has had a profound impact on various industries. In the construction industry, spun pulleys are used in cranes and elevators to lift heavy loads with precision and efficiency. The reduced friction and enhanced durability of spun pulleys ensure smooth operation and minimal downtime, which is crucial for meeting project deadlines.
In the manufacturing sector, spun pulleys are integral to conveyor systems, facilitating the smooth and efficient transport of materials and products. The high load-bearing capacity and low friction of spun pulleys ensure that the conveyor systems operate smoothly, reducing the risk of breakdowns and increasing productivity.
Agricultural Applications
In agriculture, spun pulleys are used in irrigation systems to lift water from wells and distribute it across fields. The efficiency and durability of spun pulleys ensure that water is delivered consistently, even in remote and challenging environments. This reliability is crucial for maintaining crop health and maximizing yield.
Automotive Applications
In the automotive industry, spun pulleys are used in various mechanical systems, including engine belts and transmission systems. The precision and durability of spun pulleys ensure that these systems operate smoothly, reducing wear and tear and extending the lifespan of the vehicle.
Aerospace Applications
In the aerospace industry, spun pulleys are used in aircraft control systems and landing gear mechanisms. The lightweight and high-strength properties of spun pulleys are crucial for ensuring the safety and efficiency of aircraft operations. The reduced friction and enhanced durability of spun pulleys ensure that these systems operate reliably, even under extreme conditions.
Marine Applications
In the marine industry, spun pulleys are used in various mechanical systems, including winches and cranes. The corrosion-resistant properties of spun pulleys make them ideal for use in marine environments, where exposure to saltwater and harsh conditions is common. The efficiency and durability of spun pulleys ensure that these systems operate smoothly, reducing the risk of breakdowns and increasing the safety of marine operations.
Energy Sector Applications
In the energy sector, spun pulleys are used in various mechanical systems, including wind turbines and hydroelectric power plants. The efficiency and durability of spun pulleys ensure that these systems operate smoothly, reducing the risk of breakdowns and increasing the reliability of energy production.
Medical Applications
In the medical field, spun pulleys are used in various mechanical systems, including medical imaging equipment and surgical instruments. The precision and durability of spun pulleys ensure that these systems operate smoothly, reducing the risk of breakdowns and increasing the reliability of medical procedures.
Environmental Applications
In environmental applications, spun pulleys are used in various mechanical systems, including water treatment plants and waste management facilities. The efficiency and durability of spun pulleys ensure that these systems operate smoothly, reducing the risk of breakdowns and increasing the reliability of environmental management.
Educational Applications
In educational settings, spun pulleys are used in various mechanical systems, including laboratory equipment and educational models. The precision and durability of spun pulleys ensure that these systems operate smoothly, reducing the risk of breakdowns and increasing the reliability of educational demonstrations.
Research and Development Applications
In research and development, spun pulleys are used in various mechanical systems, including prototyping equipment and testing facilities. The precision and durability of spun pulleys ensure that these systems operate smoothly, reducing the risk of breakdowns and increasing the reliability of research and development activities.
Military Applications
In military applications, spun pulleys are used in various mechanical systems, including weapon systems and logistical equipment. The precision and durability of spun pulleys ensure that these systems operate smoothly, reducing the risk of breakdowns and increasing the reliability of military operations.
Consumer Goods Applications
In consumer goods, spun pulleys are used in various mechanical systems, including household appliances and recreational equipment. The precision and durability of spun pulleys ensure that these systems operate smoothly, reducing the risk of breakdowns and increasing the reliability of consumer goods.
Transportation Applications
In transportation, spun pulleys are used in various mechanical systems, including public transit systems and logistical equipment. The precision and durability of spun pulleys ensure that these systems operate smoothly, reducing the risk of breakdowns and increasing the reliability of transportation services.
Telecommunications Applications
In telecommunications, spun pulleys are used in various mechanical systems, including satellite equipment and network infrastructure. The precision and durability of spun pulleys ensure that these systems operate smoothly, reducing the risk of breakdowns and increasing the reliability of telecommunications services.
Mining Applications
In mining, spun pulleys are used in various mechanical systems, including extraction equipment and processing facilities. The precision and durability of spun pulleys ensure that these systems operate smoothly, reducing the risk of breakdowns and increasing the reliability of mining operations.
Forestry Applications
In forestry, spun pulleys are used in various mechanical systems, including logging equipment and processing facilities. The precision and durability of spun pulleys ensure that these systems operate smoothly, reducing the risk of breakdowns and increasing the reliability of forestry operations.
Fisheries Applications
In fisheries, spun pulleys are used in various mechanical systems, including fishing vessels and processing facilities. The precision and durability of spun pulleys ensure that these systems operate smoothly, reducing the risk of breakdowns and increasing the reliability of fisheries operations.
Recreational Applications
In recreational settings, spun pulleys are used in various mechanical systems, including amusement park rides and sports equipment. The precision and durability of spun pulleys ensure that these systems operate smoothly, reducing the risk of breakdowns and increasing the reliability of recreational activities.
Art and Design Applications
In art and design, spun pulleys are used in various mechanical systems, including sculptures and installations. The precision and durability of spun pulleys ensure that these systems operate smoothly, reducing the risk of breakdowns and increasing the reliability of artistic and design projects.
Cultural Heritage Applications
In cultural heritage, spun pulleys are used in various mechanical systems, including museum exhibits and historical preservation. The precision and durability of spun pulleys ensure that these systems operate smoothly, reducing the risk of breakdowns and increasing the reliability of cultural heritage preservation.
Humanitarian Applications
In humanitarian settings, spun pulleys are used in various mechanical systems, including disaster relief equipment and medical supplies. The precision and durability of spun pulleys ensure that these systems operate smoothly, reducing the risk of breakdowns and increasing the reliability of humanitarian aid.
Legal Applications
In legal settings, spun pulleys are used in various mechanical systems, including forensic equipment and security systems. The precision and durability of spun pulleys ensure that these systems operate smoothly, reducing the risk of breakdowns and increasing the reliability of legal procedures.
Financial Applications
In financial settings, spun pulleys are used in various mechanical systems, including banking equipment and security systems. The precision and durability of spun pulleys ensure that these systems operate smoothly, reducing the risk of breakdowns and increasing the reliability of financial transactions.
Governmental Applications
In governmental settings, spun pulleys are used in various mechanical systems, including public infrastructure and security systems. The precision and durability of spun pulleys ensure that these systems operate smoothly, reducing the risk of breakdowns and increasing the reliability of governmental services.
Non-Profit Applications
In non-profit settings, spun pulleys are used in various mechanical systems, including community projects and educational programs. The precision and durability of spun pulleys ensure that these systems operate smoothly, reducing the risk of breakdowns and increasing the reliability of non-profit activities.
Commercial Applications
In commercial settings, spun pulleys are used in various mechanical systems, including retail equipment and logistical systems. The precision and durability of spun pulleys ensure that these systems operate smoothly, reducing the risk of breakdowns and increasing the reliability of commercial operations.
Residential Applications
In residential settings, spun pulleys are used in various mechanical systems, including home appliances and security systems. The precision and durability of spun pulleys ensure that these systems operate smoothly, reducing the risk of breakdowns and increasing the reliability of residential services.
Technological Innovations
The integration of spinning technology in pulleys has led to several technological innovations. One of the most significant innovations is the development of self-lubricating pulleys. These pulleys are designed with built-in lubrication systems that ensure smooth operation and reduce the need for frequent maintenance. The self-lubricating feature is achieved through the precise shaping of the pulley wheel during the spinning process, which creates microscopic channels for lubricant distribution.
Another innovation is the development of variable-speed pulleys. These pulleys are designed to adjust their speed automatically based on the load and operating conditions. The spinning process allows for the creation of complex geometries within the pulley wheel, enabling it to adapt to different speeds and loads. This adaptability is crucial for optimizing the efficiency of mechanical systems and reducing energy consumption.
Environmental Impact
The application of spinning technology in pulleys has also had a positive environmental impact. Traditional pulleys often required frequent maintenance and replacement, leading to increased waste and resource consumption. Spun pulleys, with their enhanced durability and reduced maintenance requirements, contribute to sustainability by extending the lifespan of mechanical systems and reducing the need for frequent replacements.
Additionally, the efficiency of spun pulleys reduces energy consumption, leading to lower carbon emissions and a smaller environmental footprint. The precise shaping and uniform distribution of material during the spinning process ensure that spun pulleys operate with minimal friction, reducing the energy required to overcome resistance.
Economic Implications
The economic implications of spinning technology in pulleys are significant. The enhanced efficiency and durability of spun pulleys lead to reduced operational costs and increased productivity. The reduced need for maintenance and replacements translates to lower long-term costs, making spun pulleys a cost-effective solution for various industries.
Moreover, the precision and reliability of spun pulleys ensure that mechanical systems operate smoothly, reducing the risk of breakdowns and downtime. This reliability is crucial for maintaining productivity and meeting project deadlines, which is particularly important in industries with tight schedules and high stakes.
The future of spinning technology in pulleys holds immense potential. Advances in material science and manufacturing technologies are expected to further enhance the performance and durability of spun pulleys. The development of new composite materials and hybrid manufacturing processes will enable the creation of even more precise and durable pulley components.
Additionally, the integration of smart technologies, such as sensors and IoT devices, will allow for real-time monitoring and optimization of pulley systems. These technologies will enable predictive maintenance, where potential issues are identified and addressed before they cause breakdowns, further enhancing the reliability and efficiency of mechanical systems.
Research and Development
Research and development in spinning technology for pulleys are ongoing, with a focus on improving material properties, manufacturing processes, and system integration. Collaborations between academia, industry, and government agencies are driving innovation in this field, leading to the development of new materials, advanced manufacturing techniques, and integrated smart technologies.
One area of research is the development of nanocomposite materials for spun pulleys. These materials offer superior strength, durability, and resistance to wear and tear, making them ideal for high-performance applications. The integration of nanotechnology in the spinning process will enable the creation of pulley components with enhanced mechanical properties and reduced friction.
Another area of research is the development of additive manufacturing techniques for spun pulleys. Additive manufacturing, also known as 3D printing, allows for the creation of complex geometries and intricate designs that are difficult to achieve with traditional manufacturing methods. The integration of additive manufacturing with spinning technology will enable the creation of customized pulley components with optimized performance characteristics.
Educational Initiatives
Educational initiatives are also playing a crucial role in advancing the application of spinning technology in pulleys. Universities and research institutions are offering specialized programs and courses in material science, manufacturing engineering, and mechanical systems. These programs are equipping students with the knowledge and skills needed to innovate and advance the field of spinning technology for pulleys.
Moreover, industry partnerships and internships are providing students with hands-on experience and real-world applications of spinning technology. These initiatives are fostering a new generation of engineers and researchers who are well-versed in the latest technologies and innovations in the field.
Government and Policy Support
Government and policy support are essential for the continued advancement of spinning technology in pulleys. Policies that promote research and development, innovation, and sustainability are crucial for driving progress in this field. Government funding and grants for research projects, as well as incentives for industry collaborations, are fostering a supportive environment for innovation.
Additionally, regulations and standards that ensure the safety and reliability of spun pulleys are essential for their widespread adoption. Government agencies are working to establish guidelines and certifications that ensure the quality and performance of spun pulleys, providing confidence to industries and consumers.
Industry Collaborations
Industry collaborations are also playing a vital role in advancing the application of spinning technology in pulleys. Partnerships between manufacturers, suppliers, and end-users are driving innovation and improving the performance and reliability of spun pulleys. These collaborations are fostering a culture of continuous improvement and innovation, leading to the development of new materials, manufacturing techniques, and system integrations.
Moreover, industry consortiums and associations are providing platforms for knowledge sharing, best practices, and standardization. These organizations are working to establish industry-wide standards and guidelines that ensure the quality and performance of spun pulleys, promoting their widespread adoption and use.
Consumer Awareness and Adoption
Consumer awareness and adoption are crucial for the success of spinning technology in pulleys. Educating consumers about the benefits and advantages of spun pulleys is essential for driving demand and fostering widespread adoption. Marketing campaigns, educational materials, and demonstrations are playing a vital role in raising awareness and promoting the use of spun pulleys.
Moreover, consumer feedback and input are essential for continuous improvement and innovation. Listening to the needs and preferences of consumers is crucial for developing spun pulleys that meet their expectations and requirements, ensuring their satisfaction and loyalty.
Sustainability and Environmental Stewardship
Sustainability and environmental stewardship are core values in the application of spinning technology in pulleys. The focus on reducing waste, conserving resources, and minimizing environmental impact is driving innovation and improvement in this field. Sustainable manufacturing practices, eco-friendly materials, and energy-efficient designs are essential for promoting environmental stewardship and sustainability.
Moreover, the integration of renewable energy sources and sustainable practices in the manufacturing and operation of spun pulleys is crucial for reducing their environmental footprint. Initiatives that promote the use of renewable energy, recycling, and waste reduction are fostering a sustainable and environmentally responsible approach to the application of spinning technology in pulleys.
Global Impact and Collaboration
The global impact and collaboration in the application of spinning technology in pulleys are significant. International partnerships and collaborations are driving innovation and progress in this field. Sharing knowledge, best practices, and technologies across borders is fostering a global community of researchers, engineers, and industry professionals dedicated to advancing the application of spinning technology in pulleys.
Moreover, global initiatives and programs that promote sustainability, innovation, and collaboration are crucial for driving progress and addressing global challenges. International organizations, governments, and industry leaders are working together to establish guidelines, standards, and best practices that ensure the quality and performance of spun pulleys, promoting their widespread adoption and use.
Challenges and Opportunities
The application of spinning technology in pulleys presents both challenges and opportunities. One of the main challenges is the high initial cost of spun pulleys compared to traditional pulleys. However, the long-term benefits, including reduced maintenance, increased efficiency, and enhanced durability, outweigh the initial investment. Educating consumers and industries about these long-term benefits is crucial for driving adoption and overcoming the cost barrier.
Another challenge is the need for specialized knowledge and skills in the manufacturing and integration of spun pulleys. Addressing this challenge requires investment in education, training, and workforce development. Initiatives that promote STEM education, vocational training, and industry partnerships are essential for building a skilled workforce capable of advancing the application of spinning technology in pulleys.
Conclusion
The application of spinning technology in pulleys has revolutionized their efficiency, durability, and overall performance. From industrial and agricultural applications to aerospace and marine uses, spun pulleys have proven their value across various sectors. The integration of advanced materials, precise manufacturing techniques, and smart technologies is driving innovation and improvement in this field.
The future of spinning technology in pulleys holds immense potential, with ongoing research and development, industry collaborations, and government support fostering a supportive environment for innovation. Educational initiatives, consumer awareness, and global collaborations are also playing crucial roles in advancing the application of spinning technology in pulleys.
As we continue to innovate and improve, the application of spinning technology in pulleys will undoubtedly shape the future of mechanical engineering, promoting sustainability, efficiency, and reliability in various industries and applications. The journey of spinning technology in pulleys is a testament to human ingenuity and the power of innovation in driving progress and addressing global challenges.
Maximize Tooling and CNC Metal Spinning Capabilities.
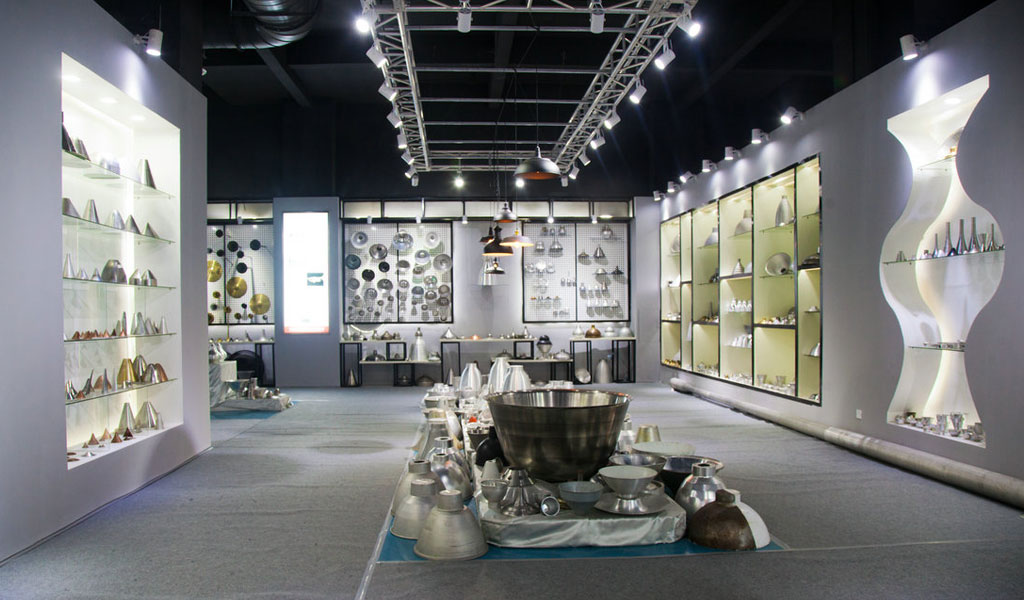
At BE-CU China Metal Spinning company, we make the most of our equipment while monitoring signs of excess wear and stress. In addition, we look into newer, modern equipment and invest in those that can support or increase our manufacturing capabilities. Our team is very mindful of our machines and tools, so we also routinely maintain them to ensure they don’t negatively impact your part’s quality and productivity.
Talk to us today about making a rapid prototype with our CNC metal spinning service. Get a direct quote by chatting with us here or request a free project review.
BE-CU China CNC Metal Spinning service include : CNC Metal Spinning,Metal Spinning Die,Laser Cutting, Tank Heads Spinning,Metal Hemispheres Spinning,Metal Cones Spinning,Metal Dish-Shaped Spinning,Metal Trumpet Spinning,Metal Venturi Spinning,Aluminum Spinning Products,Stainless Steel Spinning Products,Copper Spinning Products,Brass Spinning Products,Steel Spinning Product,Metal Spinnin LED Reflector,Metal Spinning Pressure Vessel,