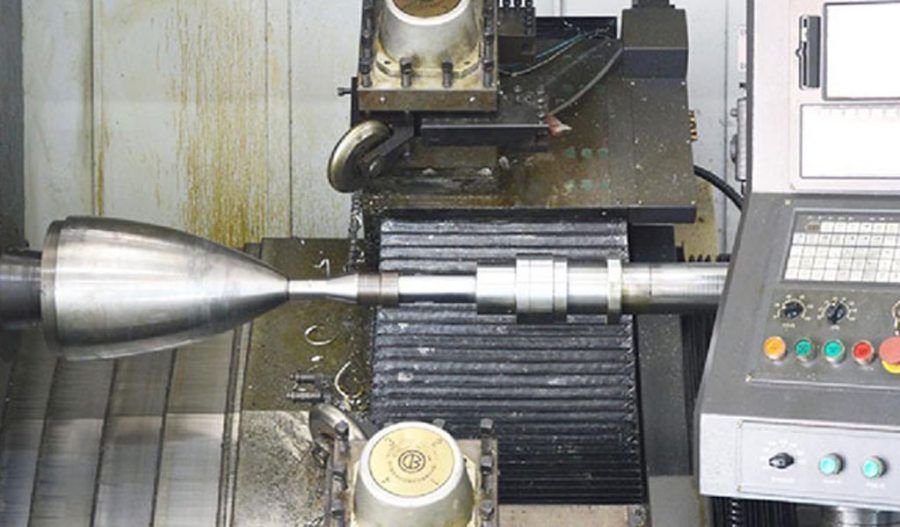
The spinning process typically involves clamping a metal sheet on a spinning machine, with the spindle driving the blank and the mold to rotate. A spinning wheel then applies pressure to the rotating blank. This localized plastic deformation gradually extends over the entire blank, forming various shapes of hollow rotational parts.
Classification and Characteristics of Spinning Processes
Spinning processes are usually divided into deep drawing spinning, shear spinning (conical thinning spinning), cylindrical thinning spinning, necking, bulging, trimming, flanging, reverse flanging, corrugating or ribbing, and surface finishing.
Spinning can be used to form rotational parts such as cylindrical, conical, parabolic shapes, or other shapes composed of various curves. It can also process relatively complex rotational parts.
Spinning is widely applicable, and most rotational workpieces can be formed using this process. However, the downside is lower productivity, making it more suitable for prototype and small batch production. Typically, if production exceeds 1000 pieces, the cost of spinning parts surpasses that of stamped parts.
Materials Used in Spinning
Carbon steel, aluminum, and stainless steel account for the largest share of materials used in spinning. Many metal materials are suitable for the process, including:
- Carbon steel
- Aluminum and aluminum alloys
- Stainless steel
- Copper and brass
- Silver
- Nickel alloys
- Titanium, molybdenum, tungsten, tantalum, niobium, and other hard-to-deform metals
Among these, carbon steel, aluminum, and stainless steel make up more than 80% of all materials used.
Production Principles and Lubrication Process
- Production Principles
- Lubrication and Cooling Process
Common lubricants include:
- Machine oil
- Soap
- Paraffin
- Grease
- Mixed oil
- Water-soluble oil
- Sprays
- Zinc gel
- Molybdenum disulfide
During regular spinning, the contact between the spinning wheel and the workpiece involves fluid lubrication, so the lubrication requirements are not very strict.
In thinning spinning, to reduce deformation resistance and improve surface quality, lubricants are often needed.
Points to Note:
When using fluid lubricants, the blank and the spinning wheel are in rolling contact, which allows the lubricant to easily enter the contact surface.
The higher the viscosity of the lubricant, the higher the blank’s rotational speed, the larger the spinning wheel diameter, and the smaller the wheel’s feed rate and pressure, the better the lubrication effect.
The lubricant should be applied evenly to avoid surface defects on the product.
Customer Production Case
The customer manufactures stainless steel products, with raw material thickness of 0.8mm, drawn to a depth of 160mm, and the lubricant is applied manually.
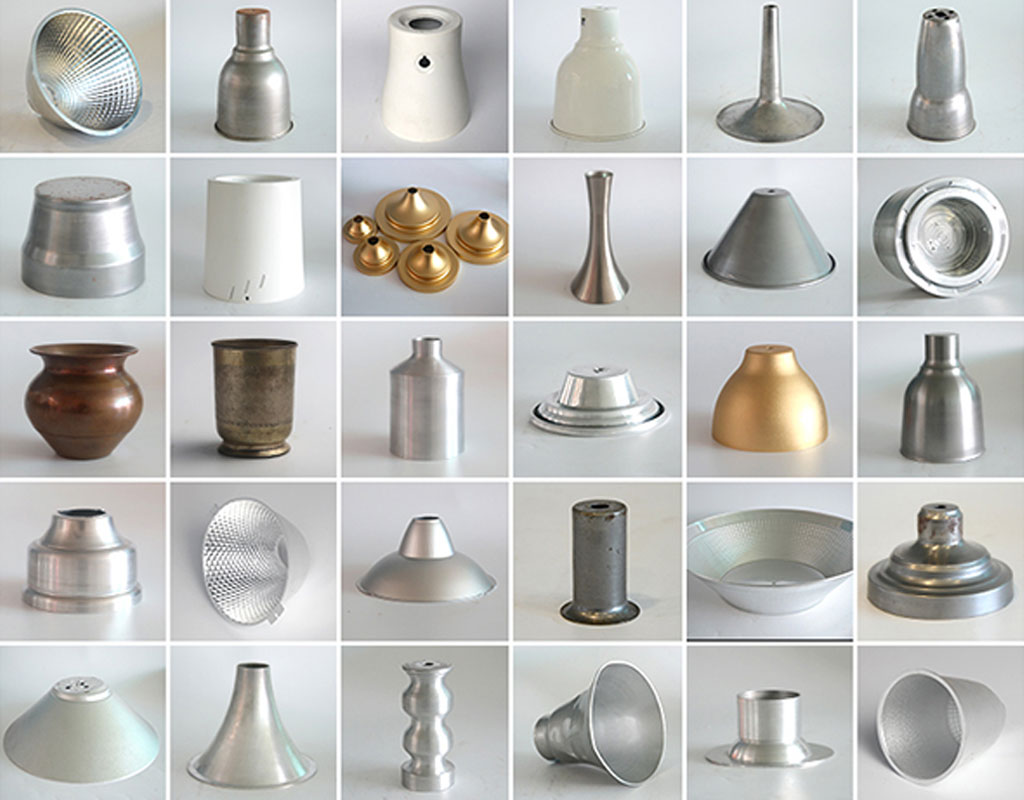
Production Issues:
- Ordinary machine oil provides limited lubrication, causing surface scratches.
- Some oils have low viscosity and are thrown off during high-speed rotation of the core mold.
- Some oils are too viscous, leading to uneven application and affecting product quality.
Solution:
The customer originally used a lubricant with low viscosity, providing limited lubrication and requiring six applications throughout the process. Based on their feedback, the company recommended a product with appropriate viscosity and lubricating properties (Stainless Steel Deep Drawing Oil Form DP 60).
Maximize Tooling and CNC Metal Spinning Capabilities.
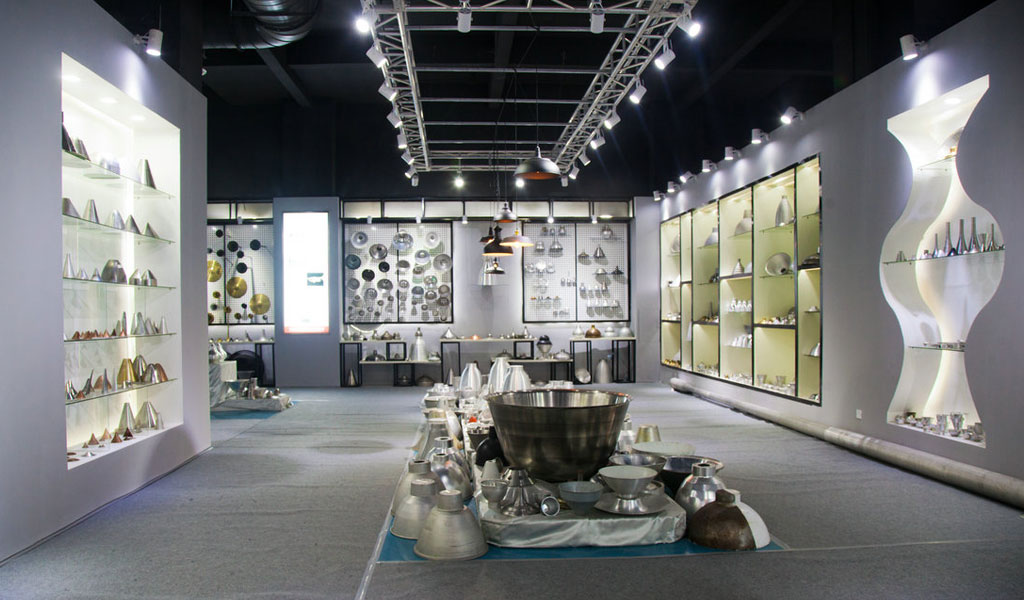
At BE-CU China Metal Spinning company, we make the most of our equipment while monitoring signs of excess wear and stress. In addition, we look into newer, modern equipment and invest in those that can support or increase our manufacturing capabilities. Our team is very mindful of our machines and tools, so we also routinely maintain them to ensure they don’t negatively impact your part’s quality and productivity.
Talk to us today about making a rapid prototype with our CNC metal spinning service. Get a direct quote by chatting with us here or request a free project review.
BE-CU China CNC Metal Spinning service include : CNC Metal Spinning,Metal Spinning Die,Laser Cutting, Tank Heads Spinning,Metal Hemispheres Spinning,Metal Cones Spinning,Metal Dish-Shaped Spinning,Metal Trumpet Spinning,Metal Venturi Spinning,Aluminum Spinning Products,Stainless Steel Spinning Products,Copper Spinning Products,Brass Spinning Products,Steel Spinning Product,Metal Spinnin LED Reflector,Metal Spinning Pressure Vessel,