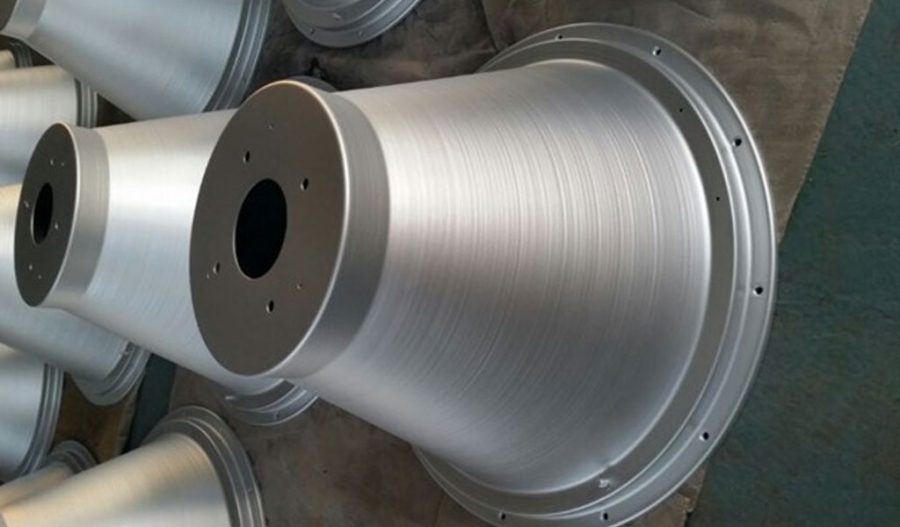
The ball spinning process is a specialized metalworking technique used to form thin-walled stainless steel tubes into complex shapes. This process is particularly valuable in industries where precision and durability are critical, such as aerospace, automotive, and medical device manufacturing. The following article provides an in-depth exploration of the ball spinning process, its applications, advantages, and the scientific principles behind its effectiveness.
Introduction to Ball Spinning
Ball spinning, also known as flow forming or shear forming, is a cold-working process that involves the use of a spinning mandrel and a set of rollers to shape thin-walled stainless steel tubes. The process begins with a pre-formed tube, which is placed over a mandrel. The mandrel is then rotated at high speeds while the rollers apply pressure to the tube, causing it to flow and conform to the shape of the mandrel. This results in a highly precise and uniformly shaped tube with enhanced mechanical properties.
Historical Background
The origins of ball spinning can be traced back to the early 20th century, when metalworking techniques were rapidly evolving. The process was initially used for forming simple cylindrical shapes but has since been refined and adapted for more complex geometries. The advent of computer-controlled machinery has further enhanced the precision and efficiency of the ball spinning process, making it a staple in modern manufacturing.
Scientific Principles
The ball spinning process relies on several key scientific principles, including plastic deformation, material flow, and stress-strain relationships. When the rollers apply pressure to the thin-walled stainless steel tube, the material undergoes plastic deformation, which is a permanent change in shape without fracture. This deformation is controlled by the mandrel’s shape and the rollers’ pressure, ensuring that the tube conforms precisely to the desired geometry.
Material flow is another critical aspect of the ball spinning process. As the tube is spun and compressed, the material flows in a controlled manner, redistributing itself to form the final shape. This flow is influenced by the material’s ductility, which is the ability to deform plastically without fracturing. Stainless steel, with its high ductility, is particularly well-suited for this process.
The stress-strain relationship is also crucial in understanding the ball spinning process. As the tube is deformed, it experiences both tensile and compressive stresses. The material’s response to these stresses, known as strain, determines the final shape and mechanical properties of the tube. Proper control of these stresses ensures that the tube retains its structural integrity and desired properties.
Advantages of Ball Spinning
The ball spinning process offers several advantages over traditional metalworking techniques:
- Precision: The process allows for highly precise and uniform shaping of thin-walled stainless steel tubes. This precision is essential in applications where dimensional accuracy is critical.
- Strength: The cold-working process enhances the mechanical properties of the material, resulting in a stronger and more durable final product.
- Efficiency: Ball spinning is a highly efficient process, capable of producing complex shapes in a single operation. This reduces the need for multiple forming steps and minimizes material waste.
- Versatility: The process can be adapted to form a wide range of shapes and sizes, making it suitable for various applications.
- Cost-Effectiveness: The reduced need for multiple forming steps and minimal material waste make ball spinning a cost-effective solution for manufacturing thin-walled stainless steel tubes.
Applications
The ball spinning process is used in a variety of industries, each with its unique requirements and challenges. Some of the key applications include:
- Aerospace: In the aerospace industry, precision and durability are paramount. Ball spinning is used to form components such as engine casings, exhaust systems, and structural supports. The enhanced mechanical properties of the spun tubes ensure that these components can withstand the extreme conditions of flight.
- Automotive: The automotive industry relies on ball spinning to produce components such as exhaust pipes, mufflers, and fuel tanks. The process ensures that these components are lightweight, durable, and meet stringent emissions standards.
- Medical Devices: Medical device manufacturing requires precision and biocompatibility. Ball spinning is used to form components such as stents, catheters, and implants. The process ensures that these devices are safe, effective, and meet regulatory standards.
- Industrial Equipment: In industrial applications, ball spinning is used to form components such as pipes, tanks, and pressure vessels. The process ensures that these components are robust, reliable, and meet industry standards.
Comparative Analysis
To better understand the advantages of the ball spinning process, it is helpful to compare it with other metalworking techniques. The following table provides a comparative analysis of ball spinning, hydroforming, and traditional stamping:
Feature | Ball Spinning | Hydroforming | Traditional Stamping |
---|---|---|---|
Precision | High | Moderate | Low to Moderate |
Strength | Enhanced | Moderate | Moderate |
Efficiency | High | Moderate | Low |
Versatility | High | Moderate | Low |
Cost-Effectiveness | High | Moderate | Low to Moderate |
Material Waste | Minimal | Moderate | High |
Complexity | Can handle complex shapes | Limited to simpler shapes | Limited to simpler shapes |
Tooling Costs | Moderate | High | Moderate |
Production Speed | Fast | Moderate | Slow |
Detailed Process Description
The ball spinning process involves several key steps, each critical to achieving the desired final shape and properties:
- Preparation: The process begins with the preparation of the thin-walled stainless steel tube. This includes cleaning the tube to remove any contaminants and ensuring that it is free of defects.
- Mandrel Selection: The mandrel is selected based on the desired final shape of the tube. The mandrel is a precision-machined component that serves as the template for the tube’s shape.
- Tube Placement: The tube is placed over the mandrel, ensuring that it is properly aligned and secured.
- Spinning: The mandrel is then rotated at high speeds, typically ranging from 500 to 2000 RPM, depending on the material and desired shape.
- Roller Application: As the mandrel spins, the rollers are applied to the tube, exerting pressure and causing the material to flow and conform to the mandrel’s shape. The rollers are carefully controlled to ensure uniform pressure and material flow.
- Cooling: During the spinning process, the tube may generate heat due to the friction and deformation. Cooling systems are often employed to maintain the tube’s temperature within an acceptable range, preventing thermal distortion.
- Finishing: Once the desired shape is achieved, the tube is removed from the mandrel and undergoes finishing operations such as polishing, deburring, and quality inspection.
Material Considerations
The choice of material is crucial in the ball spinning process. Thin-walled stainless steel tubes are particularly well-suited for this process due to their high ductility, corrosion resistance, and mechanical strength. Some of the commonly used stainless steel grades include:
- 304 Stainless Steel: Known for its excellent corrosion resistance and ductility, 304 stainless steel is widely used in applications requiring high durability and resistance to harsh environments.
- 316 Stainless Steel: This grade offers superior corrosion resistance, making it ideal for applications in marine and chemical industries.
- 410 Stainless Steel: A martensitic stainless steel, 410 is known for its high strength and hardness, making it suitable for applications requiring enhanced mechanical properties.
- Duplex Stainless Steel: Combining the properties of austenitic and ferritic stainless steels, duplex stainless steel offers a balance of strength, ductility, and corrosion resistance.
Quality Control
Quality control is essential in the ball spinning process to ensure that the final product meets the required specifications and standards. Some of the key quality control measures include:
- Dimensional Inspection: The final dimensions of the spun tube are carefully measured to ensure they meet the required tolerances.
- Surface Finish: The surface finish of the tube is inspected for any defects, such as scratches, dents, or burrs.
- Mechanical Testing: The mechanical properties of the spun tube, such as tensile strength, yield strength, and hardness, are tested to ensure they meet the required standards.
- Corrosion Testing: The tube is subjected to corrosion testing to ensure it meets the required corrosion resistance standards.
- Non-Destructive Testing (NDT): Techniques such as ultrasonic testing, radiographic testing, and magnetic particle testing are used to detect any internal defects or flaws in the spun tube.
Environmental Considerations
The ball spinning process is not only efficient and cost-effective but also environmentally friendly. The minimal material waste and reduced need for multiple forming steps contribute to a lower environmental impact. Additionally, the use of stainless steel, which is recyclable, further enhances the sustainability of the process.
The ball spinning process continues to evolve with advancements in technology and material science. Some of the future trends in this field include:
- Advanced Materials: The development of new stainless steel grades with enhanced properties, such as higher strength, ductility, and corrosion resistance, will further expand the applications of the ball spinning process.
- Automation: The integration of advanced automation and robotics will enhance the precision, efficiency, and consistency of the ball spinning process.
- Simulation and Modeling: The use of advanced simulation and modeling tools will enable better prediction and optimization of the ball spinning process, leading to improved quality and reduced costs.
- Sustainability: The focus on sustainability will drive the development of more environmentally friendly ball spinning processes, including the use of recycled materials and energy-efficient machinery.
Conclusion
The ball spinning process is a highly specialized and effective metalworking technique for forming thin-walled stainless steel tubes. Its precision, efficiency, and versatility make it a valuable tool in various industries, from aerospace to medical devices. The scientific principles behind the process, including plastic deformation, material flow, and stress-strain relationships, ensure that the final product meets the required specifications and standards. As technology and material science continue to advance, the ball spinning process will remain a critical component of modern manufacturing, driving innovation and sustainability.
Maximize Tooling and CNC Metal Spinning Capabilities.
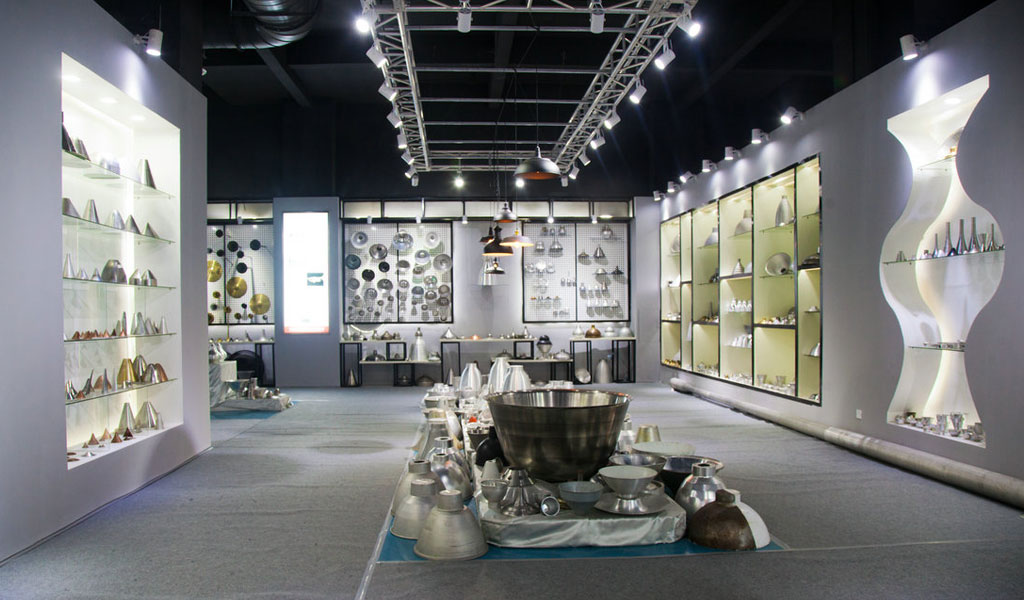
At BE-CU China Metal Spinning company, we make the most of our equipment while monitoring signs of excess wear and stress. In addition, we look into newer, modern equipment and invest in those that can support or increase our manufacturing capabilities. Our team is very mindful of our machines and tools, so we also routinely maintain them to ensure they don’t negatively impact your part’s quality and productivity.
Talk to us today about making a rapid prototype with our CNC metal spinning service. Get a direct quote by chatting with us here or request a free project review.
BE-CU China CNC Metal Spinning service include : CNC Metal Spinning,Metal Spinning Die,Laser Cutting, Tank Heads Spinning,Metal Hemispheres Spinning,Metal Cones Spinning,Metal Dish-Shaped Spinning,Metal Trumpet Spinning,Metal Venturi Spinning,Aluminum Spinning Products,Stainless Steel Spinning Products,Copper Spinning Products,Brass Spinning Products,Steel Spinning Product,Metal Spinnin LED Reflector,Metal Spinning Pressure Vessel,