CNC Metal Spinning
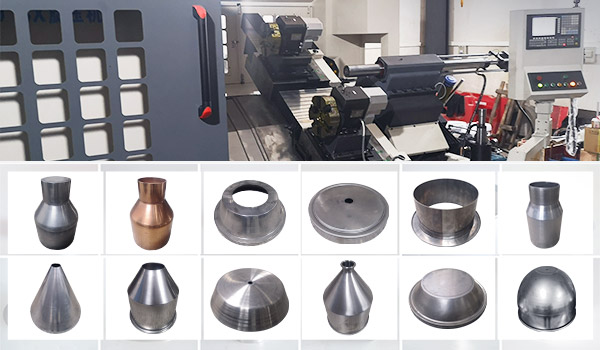
Metal Spinning technology has evolved over the last couple of years from simple machine tools to more sophisticated ones. CNC Metal Spinning is one of the most advanced spun metal processes available today. It implements lathe spinning technology to provide infinite possibilities in part creation. This technique uses spun tools that work on 2-3 directions to rotate workpieces into desired shapes and sizes.
CNC Metal Spinning offers increased accuracy and precision, efficiency, and reliability. Moreover, the process allows complete automation and management with Computer Numerical Control (CNC). As a result, many reliable metal spinning machine shops rely on this technology for precision CNC spinning services.
Combining advanced technology with skilled craftsmanship, CNC Metal Spinning has become a cornerstone in the production of intricate metal components across diverse industries. From aerospace to automotive, from household appliances to decorative arts, the applications of CNC Metal Spinning are vast and ever-expanding.
History of Metal Spinning
The art of metal spinning dates back centuries, with early evidence found in ancient civilizations such as Egypt and China. However, it wasn’t until the Industrial Revolution that metal spinning evolved into a mechanized process. Traditional metal spinning involved manually shaping metal discs or tubes over a form or mandrel using hand tools. While effective, this method was labor-intensive and limited in precision.
The advent of the Industrial Revolution brought about significant advancements in metalworking technology. With the introduction of lathes and other machinery, metal spinning underwent a transformation, becoming more efficient and precise. As technology continued to evolve, CNC Metal Spinning emerged as the pinnacle of this age-old craft, combining the precision of computer control with the versatility of traditional spinning techniques.If you want to know more about the history of spinning, please click: The History of Metal Spinning: From Ancient Craft to Modern Art
Technology Behind CNC Metal Spinning – How Does CNC Spinning Work?
At the heart of CNC Metal Spinning is computer numerical control, which enables precise control of the spinning process. CNC Metal Spinning machines are equipped with computer-controlled axes that dictate the movement of the spinning tool, allowing for intricate and complex shapes to be formed with unparalleled accuracy.
The process begins with the design of a CAD (Computer-Aided Design) model, which serves as the blueprint for the final product. The CAD model is then translated into machine code using CAM (Computer-Aided Manufacturing) software, which generates instructions for the CNC Metal Spinning machine. These instructions dictate the movements of the spinning tool, including rotation, translation, and shaping, ensuring that the desired shape is achieved with precision.
One of the key components of CNC Metal Spinning is the spinning lathe, which holds the metal workpiece and rotates it at high speeds. A spinning tool, typically in the form of a roller or mandrel, is then brought into contact with the rotating workpiece, gradually shaping it into the desired form. The CNC control system precisely coordinates the movements of the spinning tool and the workpiece, ensuring uniformity and accuracy throughout the spinning process.
CNC (Computer Numerical Control) spinning is a highly advanced manufacturing process that utilizes computer-controlled machinery to shape metal workpieces into desired forms. The process involves several key steps, each meticulously coordinated by CNC software and machinery to achieve precise results. Here’s a breakdown of how CNC spinning works:
The process begins with the creation of a digital design for the desired metal component using CAD (Computer-Aided Design) software. This design serves as a blueprint, detailing the dimensions, contours, and specifications of the final product.
Once the design is complete, it is translated into machine-readable instructions using CAM (Computer-Aided Manufacturing) software. These instructions, often referred to as G-code, contain commands that dictate the movements and operations of the CNC spinning machine.
The metal workpiece, typically in the form of a flat sheet or a cylindrical blank, is selected based on the material and dimensions required for the final component.
Prior to spinning, the workpiece may undergo pre-forming operations such as cutting, shearing, or punching to achieve the initial shape and size required for the spinning process.
The workpiece is securely mounted onto the spinning lathe, a specialized machine equipped with computer-controlled axes and spinning tools.
Proper setup is crucial for ensuring accuracy and repeatability in the spinning process. This may involve aligning the workpiece with the spinning axis, selecting appropriate tooling, and configuring machine parameters such as speed and feed rates.
Once the setup is complete, the CNC spinning machine initiates the spinning operation according to the programmed instructions.
A spinning tool, such as a roller or mandrel, is brought into contact with the rotating workpiece. The tool applies pressure to the metal surface, gradually shaping it into the desired form.
The CNC control system coordinates the movements of the spinning tool and the workpiece, precisely controlling parameters such as rotational speed, tool path, and pressure application.
As the spinning tool moves along the surface of the workpiece, it gradually forms the metal into the desired shape, smoothing out wrinkles and eliminating imperfections.
Depending on the complexity of the design, multiple passes may be required to achieve the desired shape and surface finish.
Additional finishing operations, such as trimming, cutting, or polishing, may be performed to refine the final appearance and dimensions of the component.
Throughout the spinning process, sensors and monitoring systems may be employed to ensure dimensional accuracy, surface quality, and consistency of the finished component.
Inspection techniques such as laser scanning, coordinate measuring, and visual inspection may be used to verify compliance with design specifications and quality standards.
Once the spinning operation is complete, the finished component is carefully removed from the spinning lathe.
Any remaining burrs, sharp edges, or surface imperfections may be removed through post-processing techniques such as deburring, sanding, or machining.
The finished component is then ready for further assembly, coating, or installation as required by the specific application.
CNC spinning is a sophisticated manufacturing process that combines advanced technology with skilled craftsmanship to produce precise and intricate metal components. By leveraging computer-controlled machinery and precise programming, CNC spinning offers unparalleled accuracy, efficiency, and versatility in the production of a wide range of metal parts and products.
CNC Metal Spinning Company – Quality Metal CNC Spinning Service
At Be-Cu spinning company, we have a team of skilled CNC spinning machinists and EDM experts who use our state-of-the-art CNC spinning machine and tooling team to produce complex metal spun parts & spun die with the highest levels of precision and accuracy. These spun die are specially calibrated to deliver the best results, setting us apart from the competition.
We can offer 0.187 to 0.250 in. thickness, 0.250 to 72 in. dia. with +/-0.002 in. tolerance. With our precision spinning capabilities, we are able to deliver superior products and make spun-manufacturing more efficient.
At Be-Cu spinning company, we are committed to providing our clients with the highest level of satisfaction. Whether you have a simple or complex cnc metal spinning project, we have the expertise and equipment to deliver the perfect solution. We have helped clients throughout the nation with their cnc metal spinning challenges, including parts that other spun metal machine shops were unable to produce to their exact specifications. Trust us with all of your cnc metal spinning needs and we will guarantee your satisfaction.
Common Applications of CNC Metal Spinning – CNC Spun Parts Gallery
This manufacturing process is suitable for applications in several industries requiring high precision, complex shapes, and tight tolerances.
Work Material With CNC Metal Spinning
The materials used in CNC metal spinning can vary depending on the specific requirements of the part being produced.BE-CU spinning company has extensive experience manufacturing component parts from different materials using cnc metal spinning:
- Aluminum: Aluminum is a lightweight metal with good strength-to-weight ratio and excellent corrosion resistance. It is commonly used in CNC metal spinning for parts where weight reduction is important, such as aerospace components and automotive parts.
- Stainless Steel: Stainless steel is known for its corrosion resistance and durability, making it suitable for a wide range of applications, including kitchenware, automotive parts, and industrial equipment. It comes in various grades, each with its own properties suited for different applications.
- Copper: Copper is a highly conductive metal that is often used in electrical components and wiring. It is also valued for its aesthetic appeal, making it suitable for decorative pieces and architectural elements.
- Brass: Brass is an alloy of copper and zinc, known for its yellowish color and malleability. It is commonly used in CNC metal spinning for decorative items, musical instruments, and plumbing fixtures.
- Mild Steel: Mild steel, also known as carbon steel, is a versatile material with good machinability and weldability. It is used in a wide range of applications, including automotive parts, structural components, and machinery.
- Titanium: Titanium is a lightweight and strong metal with excellent corrosion resistance. It is commonly used in aerospace, medical implants, and high-performance automotive parts.
- Nickel Alloys: Nickel alloys offer high temperature and corrosion resistance, making them suitable for demanding applications such as aerospace, chemical processing, and marine environments.
Determining which spinning material will work best for your component or prototype can be difficult. BE-CU spinning company is experienced in cnc metal spinning a wide variety of components from hundreds of different materials. It’s important you pick a material that will work efficiently in your application’s typical environment. Not sure what material to use? Contact us today.