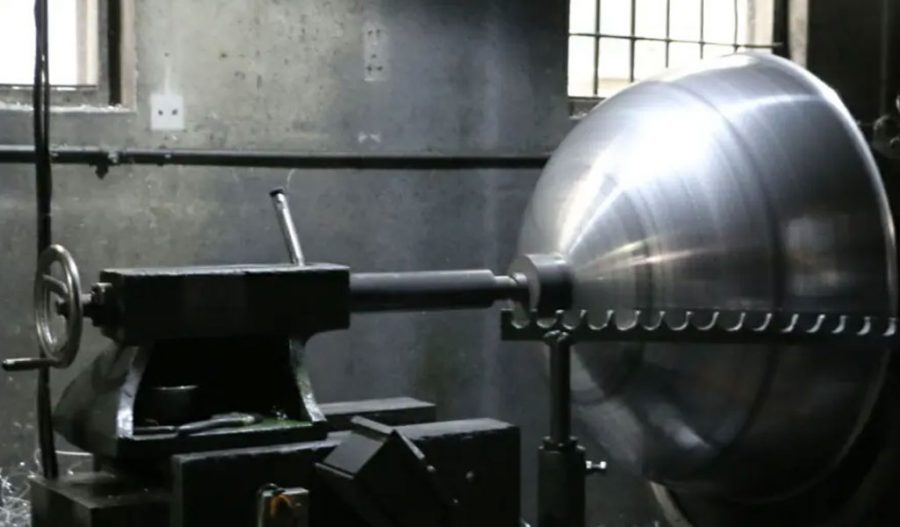
Metal spinning, also known as spin forming or spinning, is a metalworking process by which a disc or tube of metal is rotated at high speed and formed into an axially symmetric part. Traditionally, this process could be performed manually by skilled craftsmen or using advanced Computer Numerical Control (CNC) machines. This article delves into the nuances of CNC spinning and manual spinning, highlighting their respective methodologies, advantages, disadvantages, and applications in various industries.
The practice of metal spinning dates back several centuries, with early evidence suggesting its use in ancient Egypt. Historically, it was a manual process, requiring significant skill and dexterity. The industrial revolution marked a significant evolution in metal spinning techniques with the introduction of machinery, leading to more precise and efficient production methods. The advent of CNC technology in the late 20th century revolutionized metal spinning, providing unprecedented control, accuracy, and repeatability.
Metal spinning is critical in manufacturing because it allows for the production of strong, lightweight, and seamless metal parts. It is extensively used in industries such as aerospace, automotive, and consumer goods, where precision and durability are paramount. Understanding the differences between manual and CNC spinning helps in selecting the appropriate technique for specific applications, ultimately affecting production efficiency, cost, and quality.
Basics of Metal Spinning
Metal spinning involves mounting a metal blank onto a lathe and applying localized pressure with a tool to shape the metal over a pre-formed mold, or mandrel. The process can produce a wide range of symmetrical shapes, such as cones, cylinders, and hemispheres. The spinning action and the pressure applied cause the metal to flow and conform to the shape of the mandrel, achieving the desired geometry without significant thinning or loss of material integrity.
Types of Materials Used
Various metals can be spun, including aluminum, steel, copper, and brass. The choice of material depends on the application’s requirements, such as strength, weight, and corrosion resistance. Each material presents unique challenges and requires specific techniques and tools to ensure optimal results.
Common Applications
Metal spinning is used to manufacture components like satellite dishes, gas cylinders, kitchenware, musical instruments, and decorative items. Its ability to create complex shapes with high structural integrity makes it invaluable across many sectors.
Manual Spinning
Manual spinning is a traditional metalworking technique where a craftsman manually shapes a rotating metal blank using hand tools. This method relies heavily on the skill and experience of the operator to achieve the desired shape and finish.
Historical Development
Manual spinning has a long history, with roots tracing back to ancient metalworking practices. It became more refined during the industrial revolution, with advancements in lathe technology and tool materials. Despite the advent of automated techniques, manual spinning remains valued for its flexibility and the artisan’s touch it brings to the final product.
Tools and Equipment
The essential tools for manual spinning include the lathe, spinning tools, and mandrels. The lathe rotates the metal blank at high speeds, while the spinning tools, typically made from hardened steel, are used to apply pressure and shape the metal. Mandrels, which serve as the form around which the metal is shaped, are crucial for achieving precise geometries.
Techniques and Skills Required
Manual spinning requires a high degree of dexterity, hand-eye coordination, and an understanding of metal properties. The operator must skillfully control the pressure and movement of the tools to avoid defects like wrinkles or tears in the metal. Mastery of manual spinning is often acquired through years of practice and apprenticeship.
Advantages and Disadvantages
Advantages:
- Flexibility: Manual spinning allows for quick adjustments and customizations, making it ideal for small batches and prototypes.
- Low Initial Investment: The cost of setting up for manual spinning is relatively low compared to CNC machines.
- Artisanal Quality: Products created through manual spinning often have a unique, handcrafted quality that is difficult to replicate with machines.
Disadvantages:
- Labor-Intensive: Manual spinning is time-consuming and requires skilled labor, which can be costly.
- Inconsistency: The quality and precision of manually spun parts can vary based on the operator’s skill and experience.
- Limited Scalability: Manual spinning is less suitable for high-volume production due to its reliance on manual labor.
CNC Spinning
CNC (Computer Numerical Control) spinning is an advanced metalworking technique that uses computer-controlled machines to automate the metal spinning process. This technology allows for precise control over the shaping process, leading to consistent and high-quality results.
Technological Advancements
CNC spinning machines have evolved significantly since their introduction, incorporating advanced features like multi-axis control, real-time feedback systems, and sophisticated software for designing and simulating spinning processes. These advancements have expanded the capabilities of CNC spinning, enabling the production of more complex and precise components.
Tools and Equipment
CNC spinning involves specialized lathes equipped with computer control systems. These machines use various spinning tools and mandrels, similar to those in manual spinning, but their movement and pressure application are precisely controlled by the computer. The integration of sensors and feedback systems ensures optimal shaping conditions and consistent quality.
Techniques and Precision
CNC spinning techniques leverage the power of computer programming to define the exact path and pressure applied by the spinning tools. This precision allows for the production of parts with tight tolerances and complex geometries that would be challenging to achieve manually. Additionally, CNC machines can operate continuously with minimal human intervention, enhancing productivity and efficiency.
Advantages and Disadvantages
Advantages:
- High Precision: CNC spinning provides exceptional accuracy and repeatability, ensuring consistent quality across large production runs.
- Efficiency: Automated processes reduce production time and labor costs, making CNC spinning suitable for high-volume manufacturing.
- Complex Geometries: CNC technology allows for the creation of intricate shapes that are difficult or impossible to achieve manually.
Disadvantages:
- High Initial Investment: CNC spinning machines and associated software represent a significant capital expenditure.
- Limited Flexibility: While CNC machines are highly efficient for large batches, they may be less adaptable to small runs or frequent design changes.
- Technical Expertise: Operating and programming CNC machines require specialized knowledge and training.
Comparative Analysis
Manual spinning relies on the operator’s skill to achieve desired dimensions, which can result in variability. CNC spinning, on the other hand, offers superior accuracy and precision due to its computer-controlled nature, ensuring consistent quality.
Production Speed and Efficiency
CNC spinning is generally faster and more efficient than manual spinning, particularly for large production runs. The automation of CNC machines reduces the need for manual intervention, allowing for continuous operation and higher throughput.
Flexibility and Customization
Manual spinning excels in flexibility and customization, allowing for quick adjustments and unique, artisanal touches. CNC spinning, while highly precise, is better suited for standardized production but can struggle with frequent design changes.
Cost and Economic Considerations
The initial cost of CNC spinning equipment is significantly higher than that of manual spinning tools. However, the long-term benefits of reduced labor costs and higher production efficiency can offset the initial investment, particularly for large-scale manufacturing. Manual spinning, with its lower setup costs, may be more economical for small-scale or custom production.
Skills and Labor Requirements
Manual spinning requires highly skilled labor, with expertise built over years of practice. CNC spinning reduces the dependency on manual skills but requires technical proficiency in operating and programming CNC machines.
Material Waste and Sustainability
CNC spinning generally results in less material waste due to its precision and control, contributing to more sustainable manufacturing practices. Manual spinning, while potentially more wasteful due to human error, can also be more adaptable in using recycled or scrap materials.
Maximize Tooling and CNC Metal Spinning Capabilities.
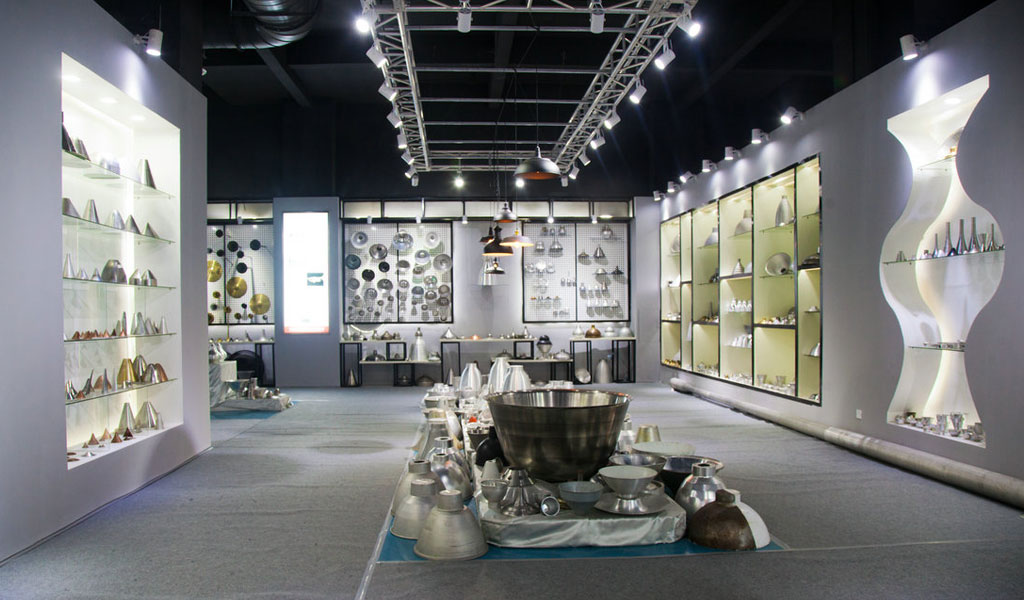
At BE-CU China Metal Spinning company, we make the most of our equipment while monitoring signs of excess wear and stress. In addition, we look into newer, modern equipment and invest in those that can support or increase our manufacturing capabilities. Our team is very mindful of our machines and tools, so we also routinely maintain them to ensure they don’t negatively impact your part’s quality and productivity.
Talk to us today about making a rapid prototype with our CNC metal spinning service. Get a direct quote by chatting with us here or request a free project review.
BE-CU China CNC Metal Spinning service include : CNC Metal Spinning,Metal Spinning Die,Laser Cutting, Tank Heads Spinning,Metal Hemispheres Spinning,Metal Cones Spinning,Metal Dish-Shaped Spinning,Metal Trumpet Spinning,Metal Venturi Spinning,Aluminum Spinning Products,Stainless Steel Spinning Products,Copper Spinning Products,Brass Spinning Products,Steel Spinning Product,Metal Spinnin LED Reflector,Metal Spinning Pressure Vessel,