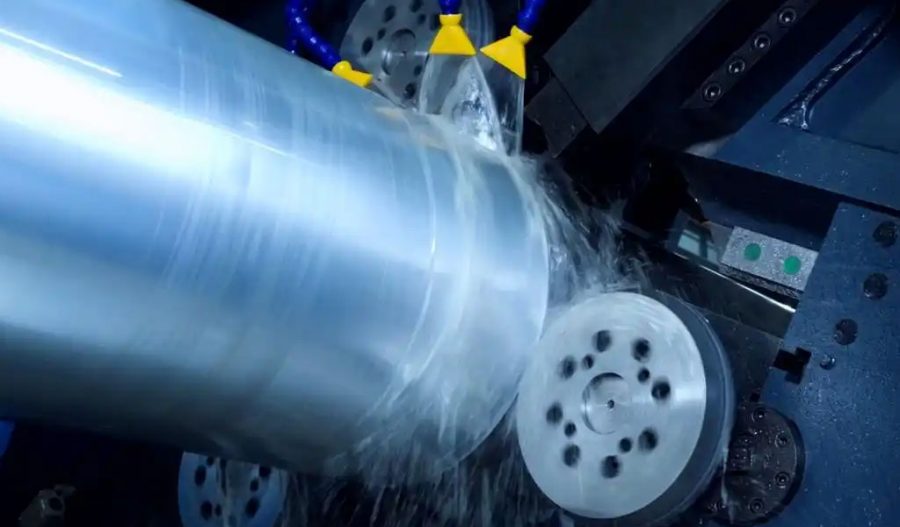
Metal spinning, a versatile sheet metal forming process, involves rotating a metal blank or tube at high speed while applying localized pressure to shape it over a mandrel or form. This technique, rooted in ancient craftsmanship, has evolved into a sophisticated manufacturing method used across industries such as aerospace, automotive, and consumer goods. Two primary approaches dominate modern metal spinning: conventional spinning and high-speed spinning. Conventional spinning relies on gradual, often manual or semi-automated deformation, while high-speed spinning leverages advanced machinery, higher rotational speeds, and optimized process parameters to enhance productivity and precision. This article provides a comprehensive comparative study of the forming quality of these two methods, analyzing their mechanics, process parameters, material behavior, and outcomes. Detailed tables and discussions draw on recent studies to highlight differences in dimensional accuracy, surface finish, material properties, and production efficiency.
The forming quality of spun parts is critical, as it determines their functionality, durability, and aesthetic appeal. Key quality metrics include wall thickness uniformity, surface roughness, dimensional accuracy, residual stresses, and material integrity (e.g., absence of wrinkles or fractures). High-speed spinning, characterized by rotational speeds often exceeding 10,000 RPM and automated control systems, promises improved efficiency and consistency compared to conventional spinning, which typically operates at lower speeds (300–1,400 RPM) and may involve manual intervention. However, the trade-offs between speed, quality, and cost remain a subject of ongoing research. This study synthesizes empirical data, numerical simulations, and experimental findings to elucidate how these methods compare across various dimensions of forming quality.
Historical Context and Evolution of Spinning Techniques
Metal spinning traces its origins to ancient Egypt, where artisans shaped metals using rudimentary lathes. By the Industrial Revolution, mechanized spinning lathes enabled mass production of symmetrical components like cookware and decorative items. Conventional spinning, as it developed in the 19th and 20th centuries, relied on skilled operators using hand tools or basic machinery to guide metal deformation. The process was labor-intensive, with quality heavily dependent on operator expertise. Typical materials included soft metals like aluminum, copper, and brass, spun at speeds of 300–1,200 RPM, depending on material thickness and part geometry.
The advent of computer numerical control (CNC) and high-speed spindles in the late 20th century marked the emergence of high-speed spinning. These advancements allowed for precise control of tool paths, feed rates, and spindle speeds, enabling the production of complex geometries with minimal human intervention. High-speed spinning systems, often operating at 10,000–100,000 RPM, integrate automated tooling and real-time monitoring, reducing cycle times and improving repeatability. Industries such as aerospace and automotive adopted high-speed spinning for components like turbine housings and wheel rims, where tight tolerances and high strength are paramount.
The evolution from conventional to high-speed spinning reflects broader trends in manufacturing: automation, precision, and efficiency. However, both methods persist, as conventional spinning remains cost-effective for small batches and custom parts, while high-speed spinning dominates high-volume production. Understanding their comparative forming quality requires examining their mechanics, process parameters, and material interactions.
Mechanics of Conventional and High-Speed Spinning
Conventional Spinning Mechanics
Conventional spinning involves clamping a circular metal blank or tube against a rotating mandrel. A forming tool, typically a roller or hand-held instrument, applies localized pressure to deform the metal incrementally. The process can be single-pass or multi-pass, with the latter used for deep or complex shapes. The mechanics of conventional spinning are governed by plastic deformation under plane stress conditions, where the material undergoes radial and tangential stresses as it conforms to the mandrel.
Key mechanical features include:
- Incremental Deformation: The tool moves along predefined paths (e.g., linear, involute, or quadratic curves), gradually shaping the blank. This reduces forming forces but increases cycle time.
- Material Flow: The metal flows radially inward or axially along the mandrel, with thickness changes minimized in conventional spinning (unlike shear spinning, where thickness reduction is intentional).
- Stress and Strain Distribution: Radial and tangential stresses dominate, with compressive strains at the tool contact point and tensile strains elsewhere. Uneven strain distribution can lead to wrinkling or springback.
Conventional spinning typically operates at spindle speeds of 300–1,400 RPM, depending on material and thickness. For example, 1/32-inch iron is spun at 600 RPM, while zinc requires 1,000–1,400 RPM. The low speed minimizes heat generation but limits productivity.
High-Speed Spinning Mechanics
High-speed spinning builds on conventional principles but leverages higher rotational speeds and advanced control systems. The mechanics are similar, but the increased speed and automation introduce distinct characteristics:
- Higher Rotational Speeds: Spindle speeds often exceed 10,000 RPM, with some systems reaching 100,000 RPM for small-diameter tools. This accelerates material flow and reduces cycle time.
- Automated Tool Paths: CNC systems control roller paths with precision, using complex trajectories (e.g., Bessel curves) to optimize strain distribution and minimize defects.
- Thermal Effects: Higher speeds generate frictional heat, which can enhance material ductility but risks thermal softening or microstructural changes if not controlled.
- Vibration and Stability: High speeds increase the risk of chatter and vibration, necessitating balanced tooling and robust spindle designs.
The mechanics of high-speed spinning are influenced by centrifugal forces, gyroscopic effects, and bearing dynamics. These factors require sophisticated modeling, often using finite element analysis (FEA), to predict material behavior and optimize process parameters.
Comparative Mechanical Analysis
The primary mechanical difference between the two methods lies in speed and automation. High-speed spinning reduces forming time by accelerating material flow, but it introduces challenges like vibration and heat generation. Conventional spinning, while slower, offers greater control over deformation for skilled operators, reducing the risk of defects in low-volume production. Table 1 compares the mechanical characteristics of both methods.
Table 1: Mechanical Characteristics of Conventional and High-Speed Spinning
Parameter | Conventional Spinning | High-Speed Spinning |
---|---|---|
Spindle Speed (RPM) | 300–1,400 | 10,000–100,000 |
Tool Path Control | Manual or semi-automated | CNC-automated |
Forming Time | Longer (multi-pass often required) | Shorter (fewer passes due to higher speed) |
Primary Stresses | Radial, tangential (plane stress) | Radial, tangential, with thermal effects |
Vibration Risk | Low | High (requires balanced tooling) |
Thermal Effects | Minimal | Significant (frictional heat) |
Material Flow | Gradual, operator-dependent | Rapid, automated |
Process Parameters and Their Impact on Forming Quality
Process parameters significantly influence the forming quality of spun parts. These include spindle speed, feed rate, tool geometry, and mandrel design. This section examines how these parameters differ between conventional and high-speed spinning and their effects on quality metrics like wall thickness, surface finish, and dimensional accuracy.
Spindle Speed
- Conventional Spinning: Spindle speeds are material-specific and typically low. For example, soft steel is spun at 300–600 RPM, while aluminum requires 800–1,200 RPM. Low speeds reduce heat and vibration but increase cycle time, potentially leading to uneven deformation if operator skill varies.
- High-Speed Spinning: Speeds of 10,000–100,000 RPM enable rapid forming, reducing cycle time by up to 50% compared to conventional methods. However, high speeds increase vibration and frictional heat, which can cause surface imperfections or material softening if not managed.
Impact on Quality: Higher speeds in high-speed spinning improve productivity but risk chatter, which degrades surface finish. Conventional spinning’s lower speeds ensure smoother surfaces but may result in inconsistent wall thickness due to manual control.
Feed Rate
- Conventional Spinning: Feed rates are typically 0.5–2 mm/rev, adjusted manually or via basic CNC systems. Slow feed rates reduce wrinkling but prolong forming time.
- High-Speed Spinning: Feed rates range from 1–4 mm/rev, optimized by CNC systems to balance speed and stability. Higher feed rates can cause wrinkling or excessive thinning if not carefully controlled.
Impact on Quality: High feed rates in high-speed spinning increase productivity but may lead to wrinkling, as observed in experiments with feed rates of 4 mm/rev causing larger wrinkles compared to 3 mm/rev. Conventional spinning’s slower feed rates minimize defects but reduce efficiency.
Tool Geometry
- Conventional Spinning: Tools are often simple rollers or hand-held instruments with fillet radii of 2–6 mm. The choice depends on operator preference and part geometry.
- High-Speed Spinning: CNC-controlled rollers with optimized fillet radii (e.g., 6 mm) and attack angles (e.g., 35°) minimize spinning forces and improve surface quality.
Impact on Quality: Optimized tool geometry in high-speed spinning reduces radial and tangential forces, improving wall thickness uniformity. Conventional spinning’s simpler tools may lead to inconsistent deformation, especially for complex shapes.
Mandrel Design
- Conventional Spinning: Mandrels are typically wooden or steel, shaped to match the desired part geometry. They are cost-effective but may wear over time.
- High-Speed Spinning: Precision-engineered steel or composite mandrels withstand high speeds and ensure dimensional accuracy. They are more expensive but durable.
Impact on Quality: High-speed spinning’s robust mandrels maintain tight tolerances, while conventional spinning’s simpler mandrels may lead to dimensional deviations in high-volume production.
Table 2: Process Parameters and Their Effects on Forming Quality
| Parameter | Conventional Spinning | High-Speed Spinning | Quality Impact | |———————————–| Spindle Speed | 300–1,400 RPM | 10,000–100,000 RPM | High speeds improve productivity but risk chatter and thermal softening. || Feed Rate | 0.5–2 mm/rev | 1–4 mm/rev | Higher feed rates increase productivity but may cause wrinkling. || Tool Geometry | Simple rollers, 2–6 mm fillet | Optimized rollers, 6 mm fillet, 35° attack | Optimized geometry reduces forces, improving uniformity. || Mandrel Design | Wooden/steel, cost-effective | Precision steel/composite, durable | Robust mandrels ensure tight tolerances. |
Material Behavior and Forming Quality
Material behavior under spinning conditions is a critical determinant of forming quality. Common materials include aluminum, steel, copper, and titanium, each responding differently to the stresses and strains of spinning.
Aluminum
- Conventional Spinning: Aluminum’s high ductility makes it ideal for conventional spinning, producing smooth surfaces and uniform wall thickness. However, low speeds may lead to uneven strain distribution.
- High-Speed Spinning: High speeds enhance aluminum’s formability, increasing limiting spinning ratios (LSR) from 1.75 to 2.40 in deep spinning experiments. However, excessive heat can cause softening or microstructural changes.
Steel
- Conventional Spinning: Steel’s lower ductility requires careful control to avoid wrinkling or fracture. Soft steel spins well at 300–600 RPM, but thicker gauges need slower speeds.
- High-Speed Spinning: High speeds improve steel’s formability but increase the risk of chatter and surface defects. Optimized parameters (e.g., 500 RPM, 1 mm/rev) minimize these issues.
Copper and Titanium
- Conventional Spinning: Copper spins easily at 800–1,000 RPM, producing excellent surface finish. Titanium, being less ductile, requires precise control to avoid cracking.
- High-Speed Spinning: Both materials benefit from high speeds, but titanium’s sensitivity to heat necessitates cooling systems to prevent embrittlement.
Table 3: Material Behavior and Forming Quality
Material | Conventional Spinning | High-Speed Spinning | Quality Impact |
---|---|---|---|
Aluminum | High ductility, smooth surfaces | Enhanced LSR (1.75 to 2.40) | High speeds improve formability but risk softening. |
Steel | Prone to wrinkling, needs slow speeds | Improved formability, risk of chatter | Optimized parameters reduce defects. |
Copper | Excellent surface finish | Benefits from high speeds | Minimal defects with proper cooling. |
Titanium | Requires precise control | Sensitive to heat, needs cooling | High speeds enhance formability but risk embrittlement. |
Dimensional Accuracy and Wall Thickness Uniformity
Dimensional accuracy and wall thickness uniformity are critical for functional parts. Both methods aim to minimize deviations from design specifications.
Conventional Spinning
- Dimensional Accuracy: Operator skill heavily influences accuracy. Manual adjustments can lead to deviations, especially for complex geometries. Studies report average deviations of 0.5–1 mm for simple shapes.
- Wall Thickness: Thickness remains relatively constant, with deviations of 0.1–0.3 mm. However, uneven strain distribution can cause localized thinning.
High-Speed Spinning
- Dimensional Accuracy: CNC control ensures tight tolerances, with deviations as low as 0.2 mm for deep cylinders. Automated tool paths reduce human error.
- Wall Thickness: Optimized parameters (e.g., 500 RPM, 1 mm/rev, 6 mm fillet) achieve deviations of 0.05–0.2 mm. However, high feed rates can cause thinning or thickening at the part mouth.
Table 4: Dimensional Accuracy and Wall Thickness Comparison
Metric | Conventional Spinning | High-Speed Spinning | Quality Impact |
---|---|---|---|
Dimensional Accuracy | 0.5–1 mm deviation | 0.2 mm deviation | CNC improves precision in high-speed spinning. |
Wall Thickness Deviation | 0.1–0.3 mm | 0.05–0.2 mm | Optimized parameters reduce thinning. |
Surface Finish and Defect Analysis
Surface finish affects aesthetics and performance, while defects like wrinkling, fracture, or chatter compromise part integrity.
Surface Finish
- Conventional Spinning: Produces smooth surfaces, especially for ductile materials like aluminum and copper. Surface roughness (Ra) ranges from 0.8–1.6 µm, but operator variability can lead to inconsistencies.
- High-Speed Spinning: High speeds can degrade surface finish due to chatter or thermal effects, with Ra of 1.2–2.0 µm. Optimized tool geometry and cooling systems mitigate this.
Defects
- Conventional Spinning: Common defects include wrinkling (due to excessive compressive strains) and springback (due to elastic recovery). These are minimized with slow feed rates and skilled operation.
- High-Speed Spinning: Risks include chatter (from vibration), wrinkling (from high feed rates), and fracture (from excessive thinning). Deep spinning with roller sets reduces wrinkling, increasing LSR from 1.67 to 2.24 for hard aluminum.
Table 5: Surface Finish and Defect Comparison
Metric | Conventional Spinning | High-Speed Spinning | Quality Impact |
---|---|---|---|
Surface Roughness (Ra) | 0.8–1.6 µm | 1.2–2.0 µm | High speeds increase roughness; cooling helps. |
Common Defects | Wrinkling, springback | Chatter, wrinkling, fracture | Optimized parameters reduce defects. |
Residual Stresses and Material Integrity
Residual stresses affect part durability and fatigue life, while material integrity ensures structural performance.
Residual Stresses
- Conventional Spinning: Multi-pass spinning induces moderate residual stresses due to incremental deformation. Stresses are typically compressive near the surface and tensile internally, with magnitudes of 50–100 MPa.
- High-Speed Spinning: Higher speeds and fewer passes reduce residual stresses, with magnitudes of 30–80 MPa. Optimized trajectories (e.g., Bessel curves) further minimize stress concentrations.
Material Integrity
- Conventional Spinning: Gradual deformation preserves material integrity, with minimal risk of micro-cracks or voids. However, uneven strain distribution can cause localized damage.
- High-Speed Spinning: High speeds risk microstructural changes (e.g., grain refinement or recrystallization) due to heat. Cooling and parameter optimization maintain integrity.
Table 6: Residual Stresses and Material Integrity Comparison
Metric | Conventional Spinning | High-Speed Spinning | Quality Impact |
---|---|---|---|
Residual Stresses | 50–100 MPa | 30–80 MPa | High speeds reduce stresses with optimization. |
Material Integrity | Minimal micro-cracks | Risk of microstructural changes | Cooling preserves integrity. |
Production Efficiency and Cost Analysis
Production efficiency and cost are critical for industrial applications, balancing quality with economic viability.
Production Efficiency
- Conventional Spinning: Suitable for small batches and custom parts, with cycle times of 5–15 minutes per part. Manual operation limits throughput.
- High-Speed Spinning: Ideal for high-volume production, with cycle times of 1–5 minutes per part. Automation and high speeds increase throughput by up to 50%.
Cost Analysis
- Conventional Spinning: Low tooling costs (e.g., wooden mandrels) and minimal setup make it cost-effective for prototypes or small runs. Labor costs are high due to skilled operator requirements.
- High-Speed Spinning: Higher initial costs for CNC machines and precision mandrels are offset by reduced labor and cycle times. Cost-effective for large-scale production.
Table 7: Production Efficiency and Cost Comparison
Metric | Conventional Spinning | High-Speed Spinning | Quality Impact |
---|---|---|---|
Cycle Time | 5–15 min/part | 1–5 min/part | High speeds increase throughput. |
Cost | Low tooling, high labor | High initial, low labor | Cost-effective for large-scale production. |
Case Studies and Recent Research
Recent studies provide empirical data on forming quality, highlighting the strengths and limitations of both methods.
Case Study 1: Deep Cylinder Spinning
A 2021 study explored multi-pass spinning of deep cylinders (500 mm diameter, 2 mm thick, 700 mm deep) using both methods. High-speed spinning (500 RPM, 1 mm/rev, 6 mm fillet, 35° attack) achieved a wall thickness deviation of 0.05 mm and dimensional accuracy of 0.2 mm, compared to 0.3 mm and 0.5 mm for conventional spinning. However, high feed rates (4 mm/rev) caused wrinkling, underscoring the need for optimization.
Case Study 2: Asymmetric Spinning
A 2020 study on asymmetric spinning of octagonal blanks found high-speed spinning reduced springback and strain deviations compared to conventional methods. Numerical simulations showed shell elements predicted springback better than solid elements, guiding parameter selection.
Case Study 3: Aluminum Dome Forming
A 2019 study on Al 6061-O dome forming reported high-speed spinning’s two-step process increased boss thickness by 20% compared to conventional spinning, improving structural integrity for pressure vessels.
Environmental and Sustainability Considerations
Sustainability is increasingly important in manufacturing. Both methods have environmental implications:
- Conventional Spinning: Lower energy consumption due to slower speeds but higher material waste from trimming and defects. Manual processes limit scalability.
- High-Speed Spinning: Higher energy use from fast spindles but reduced waste due to precision and fewer defects. Automation supports sustainable, high-volume production.
Table 8: Environmental Impact Comparison
Metric | Conventional Spinning | High-Speed Spinning | Quality Impact |
---|---|---|---|
Energy Consumption | Lower | Higher | High speeds increase energy use. |
Material Waste | Higher (trimming, defects) | Lower (precision, fewer defects) | Precision reduces waste. |
Future Trends and Innovations
The future of spinning lies in hybrid processes, advanced materials, and digital integration:
- Hybrid Processes: Combining spinning with electromagnetic forming or incremental sheet forming to enhance formability and reduce defects.
- Advanced Materials: Spinning high-strength alloys and composites, requiring adaptive control systems to manage complex deformation.
- Digital Twins and AI: Real-time monitoring and AI-driven optimization to predict defects and adjust parameters dynamically.
Conclusion
High-speed spinning and conventional spinning offer distinct advantages in forming quality, driven by differences in mechanics, process parameters, and automation. High-speed spinning excels in dimensional accuracy, wall thickness uniformity, and production efficiency, making it ideal for high-volume, precision applications. Conventional spinning remains valuable for small batches and custom parts, leveraging operator skill to achieve smooth surfaces and minimal defects. Material behavior, tool geometry, and process optimization are critical to both methods, with recent studies highlighting the importance of CNC control and advanced modeling.
Tables 1–8 summarize key comparisons, showing high-speed spinning’s edge in precision and throughput, tempered by challenges like chatter and thermal effects. Conventional spinning’s simplicity and low tooling costs ensure its relevance for niche applications. Future innovations, from hybrid processes to AI integration, promise to further enhance forming quality, aligning with industry demands for sustainability and performance.
This comparative study underscores the need for tailored process design, balancing quality, cost, and environmental impact. As manufacturing evolves, both methods will continue to shape the production of high-quality, complex components across diverse industries.
Maximize Tooling and CNC Metal Spinning Capabilities.
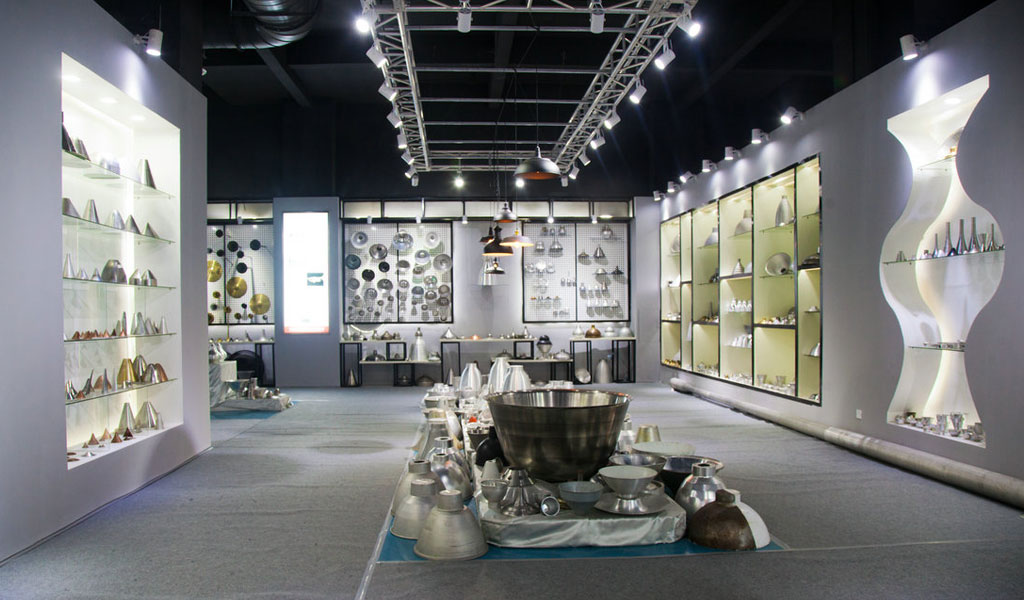
At BE-CU China Metal Spinning company, we make the most of our equipment while monitoring signs of excess wear and stress. In addition, we look into newer, modern equipment and invest in those that can support or increase our manufacturing capabilities. Our team is very mindful of our machines and tools, so we also routinely maintain them to ensure they don’t negatively impact your part’s quality and productivity.
Talk to us today about making a rapid prototype with our CNC metal spinning service. Get a direct quote by chatting with us here or request a free project review.
BE-CU China CNC Metal Spinning service include : CNC Metal Spinning,Metal Spinning Die,Laser Cutting, Tank Heads Spinning,Metal Hemispheres Spinning,Metal Cones Spinning,Metal Dish-Shaped Spinning,Metal Trumpet Spinning,Metal Venturi Spinning,Aluminum Spinning Products,Stainless Steel Spinning Products,Copper Spinning Products,Brass Spinning Products,Steel Spinning Product,Metal Spinnin LED Reflector,Metal Spinning Pressure Vessel,