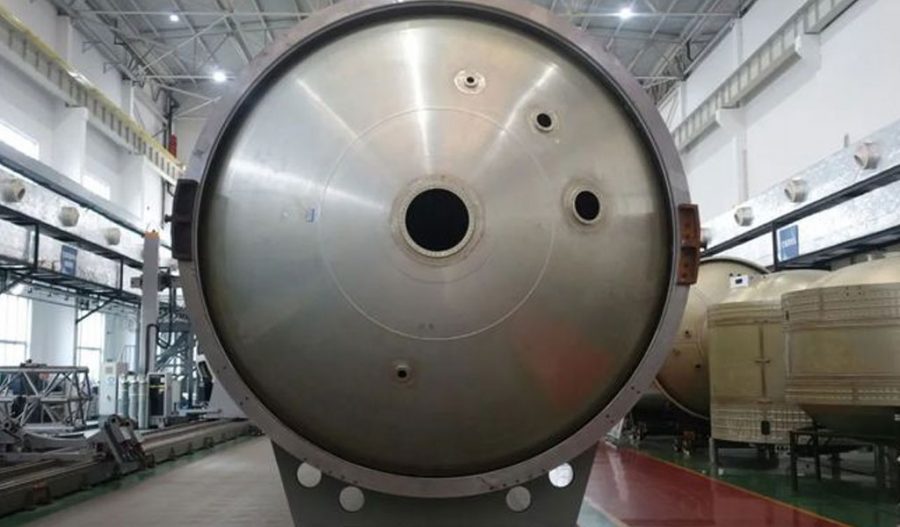
In the realm of manufacturing, the production of high-precision components is crucial for various industries, including aerospace, automotive, and defense. Two prominent methods for producing such components are precision spin-forming and cold extrusion. Both techniques are employed to create liners—thin, cylindrical structures used in various applications such as pressure vessels, pipelines, and engine components. This article delves into a comparative study of precision spin-formed and cold-extruded liners, examining their manufacturing processes, material properties, mechanical performance, cost-effectiveness, and applications.
Manufacturing Processes
Precision Spin-Forming
Precision spin-forming, also known as metal spinning, is a process where a flat metal disc is formed into a cylindrical shape by rotating it at high speeds and applying pressure using a spinning tool. The process involves several steps:
- Blank Preparation: A flat metal disc, known as a blank, is cut to the desired size and thickness.
- Clamping: The blank is clamped onto a spinning mandrel.
- Spinning: The mandrel rotates at high speeds, and a spinning tool applies pressure to the blank, gradually forming it into a cylindrical shape.
- Finishing: The spun part is trimmed and finished to achieve the desired dimensions and surface quality.
The precision spin-forming process is highly versatile and can produce complex shapes with varying wall thicknesses. It is particularly suitable for materials with good ductility, such as aluminum, copper, and stainless steel.
Cold Extrusion
Cold extrusion is a metalworking process where a billet (a solid cylinder of metal) is forced through a die at room temperature to create a desired shape. The process involves the following steps:
- Billet Preparation: A metal billet is prepared to the required size and shape.
- Lubrication: The billet and die are lubricated to reduce friction and wear.
- Extrusion: The billet is placed in the extrusion chamber and forced through the die using a hydraulic press.
- Finishing: The extruded part is trimmed and finished to achieve the desired dimensions and surface quality.
Cold extrusion is known for its ability to produce parts with high dimensional accuracy and excellent surface finish. It is commonly used for materials such as aluminum, brass, and low-carbon steels.
Material Properties
The material properties of spin-formed and cold-extruded liners are influenced by the manufacturing process and the type of material used. Table 1 compares the material properties of commonly used materials in both processes.
Material | Spin-Forming | Cold Extrusion |
---|---|---|
Aluminum | High ductility, good formability | High strength, good surface finish |
Copper | Excellent formability, good conductivity | High strength, good dimensional accuracy |
Stainless Steel | Good corrosion resistance, moderate formability | High strength, good wear resistance |
Brass | Good formability, moderate strength | High strength, good dimensional accuracy |
Low-Carbon Steel | Moderate formability, good strength | High strength, good dimensional accuracy |
Mechanical Performance
The mechanical performance of spin-formed and cold-extruded liners is critical for their application in high-stress environments. Table 2 compares the mechanical properties of liners produced by both methods.
Property | Spin-Formed Liners | Cold-Extruded Liners |
---|---|---|
Tensile Strength | Moderate to high, depending on material | High, due to work hardening |
Yield Strength | Moderate to high, depending on material | High, due to work hardening |
Elongation | High, due to good ductility | Moderate, due to work hardening |
Hardness | Moderate to high, depending on material | High, due to work hardening |
Fatigue Strength | Moderate to high, depending on material | High, due to uniform grain structure |
Impact Strength | Moderate to high, depending on material | High, due to uniform grain structure |
Cost-Effectiveness
The cost-effectiveness of spin-formed and cold-extruded liners is influenced by various factors, including material costs, tooling costs, production rates, and finishing requirements. Table 3 compares the cost-effectiveness of both methods.
Factor | Spin-Forming | Cold Extrusion |
---|---|---|
Material Costs | Moderate, depending on material | Moderate to high, depending on material |
Tooling Costs | Low to moderate | High, due to complex die requirements |
Production Rates | Moderate to high | High, due to continuous process |
Finishing Requirements | Moderate, depending on surface quality | Low to moderate, due to good surface finish |
Overall Cost-Effectiveness | Moderate to high, depending on production volume | High, for large production volumes |
Applications
Spin-formed and cold-extruded liners find applications in various industries due to their unique properties and manufacturing capabilities. Table 4 compares the typical applications of both methods.
Industry | Spin-Formed Liners | Cold-Extruded Liners |
---|---|---|
Aerospace | Engine components, fuel tanks | Structural components, landing gear |
Automotive | Exhaust systems, fuel tanks | Drive shafts, suspension components |
Defense | Ammunition casings, pressure vessels | Armor components, weapon barrels |
Chemical | Pressure vessels, pipelines | Heat exchangers, reaction vessels |
Electronics | Heat sinks, enclosures | Connectors, housing components |
Advantages and Disadvantages
Both spin-forming and cold extrusion have their advantages and disadvantages, which influence their suitability for different applications. Table 5 summarizes the advantages and disadvantages of both methods.
Factor | Spin-Forming Advantages | Spin-Forming Disadvantages | Cold Extrusion Advantages | Cold Extrusion Disadvantages |
---|---|---|---|---|
Versatility | High, can produce complex shapes | Limited to ductile materials | High dimensional accuracy | Limited to certain materials |
Production Rates | Moderate to high | Requires skilled operators | High, continuous process | High tooling costs |
Surface Finish | Good, depending on finishing process | Requires finishing for high quality | Excellent, due to work hardening | Requires complex dies |
Material Utilization | High, minimal waste | Limited to thin-walled components | High, minimal waste | Limited to certain geometries |
Cost-Effectiveness | Moderate to high, depending on volume | High initial investment | High, for large production volumes | High initial investment |
Case Studies
To further illustrate the comparative study of spin-formed and cold-extruded liners, several case studies are presented below.
Case Study 1: Aerospace Engine Components
In the aerospace industry, engine components require high precision and strength to withstand extreme operating conditions. Spin-formed liners are often used for fuel tanks and exhaust systems due to their ability to produce complex shapes with varying wall thicknesses. Cold-extruded liners, on the other hand, are used for structural components and landing gear due to their high strength and dimensional accuracy.
Case Study 2: Automotive Exhaust Systems
Automotive exhaust systems require components that can withstand high temperatures and corrosive environments. Spin-formed liners are commonly used for exhaust pipes and mufflers due to their good formability and corrosion resistance. Cold-extruded liners are used for drive shafts and suspension components due to their high strength and dimensional accuracy.
Case Study 3: Defense Ammunition Casings
In the defense industry, ammunition casings require high strength and precision to ensure reliable performance. Spin-formed liners are used for pressure vessels and ammunition casings due to their ability to produce complex shapes with high dimensional accuracy. Cold-extruded liners are used for armor components and weapon barrels due to their high strength and wear resistance.
Conclusion
The comparative study of precision spin-formed and cold-extruded liners reveals that both methods have their unique advantages and disadvantages. Spin-forming is highly versatile and suitable for producing complex shapes with varying wall thicknesses, making it ideal for applications requiring good formability and corrosion resistance. Cold extrusion, on the other hand, offers high dimensional accuracy and strength, making it suitable for applications requiring high strength and wear resistance.
The choice between spin-forming and cold extrusion depends on various factors, including material properties, mechanical performance requirements, cost-effectiveness, and specific application needs. By understanding the strengths and limitations of both methods, manufacturers can make informed decisions to produce high-quality liners for various industries.
Maximize Tooling and CNC Metal Spinning Capabilities.
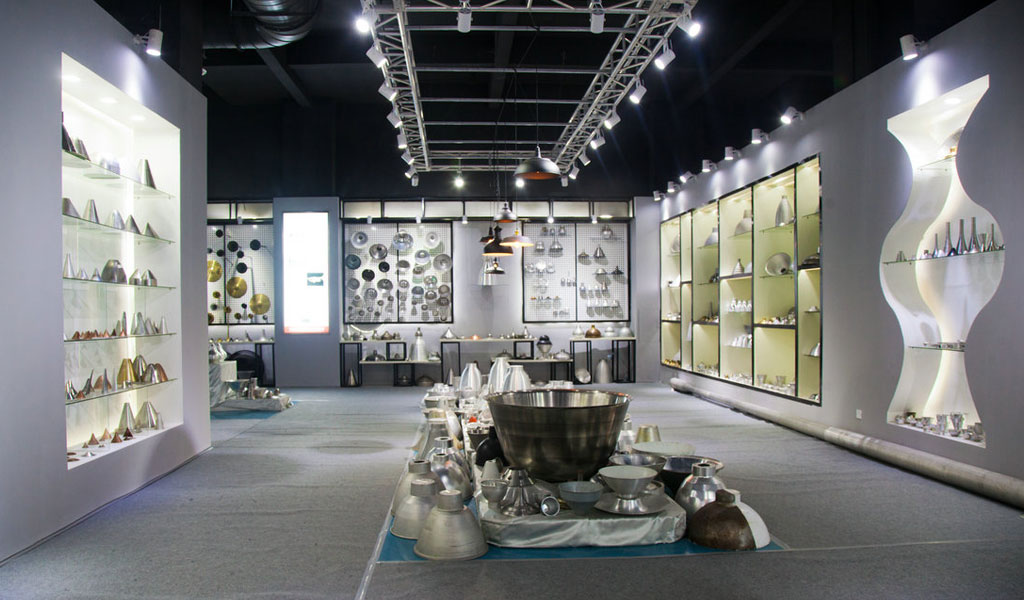
At BE-CU China Metal Spinning company, we make the most of our equipment while monitoring signs of excess wear and stress. In addition, we look into newer, modern equipment and invest in those that can support or increase our manufacturing capabilities. Our team is very mindful of our machines and tools, so we also routinely maintain them to ensure they don’t negatively impact your part’s quality and productivity.
Talk to us today about making a rapid prototype with our CNC metal spinning service. Get a direct quote by chatting with us here or request a free project review.
BE-CU China CNC Metal Spinning service include : CNC Metal Spinning,Metal Spinning Die,Laser Cutting, Tank Heads Spinning,Metal Hemispheres Spinning,Metal Cones Spinning,Metal Dish-Shaped Spinning,Metal Trumpet Spinning,Metal Venturi Spinning,Aluminum Spinning Products,Stainless Steel Spinning Products,Copper Spinning Products,Brass Spinning Products,Steel Spinning Product,Metal Spinnin LED Reflector,Metal Spinning Pressure Vessel,