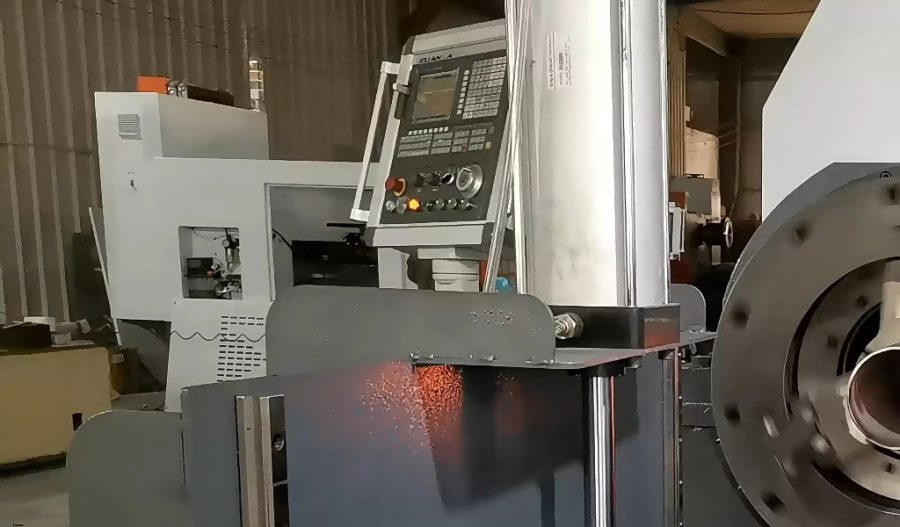
Metal spinning, a versatile sheet metal forming process, is widely employed in industries such as aerospace, automotive, and manufacturing to produce axisymmetric components with high precision and complex geometries. The process involves rotating a metal blank or preform at high speed while a forming tool, typically a roller, applies localized pressure to deform the material against a mandrel, shaping it into the desired form. Despite its advantages, including flexibility, low tooling costs, and the ability to form lightweight, high-strength components, metal spinning is challenged by the springback phenomenon—a critical issue that affects dimensional accuracy and product quality.
Springback refers to the elastic recovery of a material after the removal of forming forces, resulting in a deviation from the intended shape. In metal spinning, this phenomenon is particularly pronounced due to the complex stress states, non-uniform deformation, and material properties involved. Springback can lead to dimensional inaccuracies, compromising the functionality of components, especially in high-precision applications like turbine casings or satellite dishes. Controlling springback is thus a focal point of research and industrial practice, with various methods developed to predict, mitigate, and compensate for its effects.
This article provides a comprehensive exploration of the springback phenomenon in metal spinning, delving into its mechanics, influencing factors, and control methods. It includes detailed comparisons of recent approaches, supported by tables summarizing experimental and numerical results. The discussion is structured to cover theoretical foundations, material and process parameters, advanced control strategies, and emerging trends, offering a thorough resource for researchers, engineers, and practitioners in the field.
Mechanics of Springback in Metal Spinning
Definition and Fundamental Concepts
Springback is defined as the elastically driven change in shape of a formed part upon unloading, caused by the relaxation of residual stresses accumulated during deformation. In metal spinning, the process involves both plastic and elastic deformation, with the elastic component recovering partially when external forces are removed. This recovery alters the final geometry, leading to deviations such as increased radii of curvature, angular distortions, or shape inaccuracies.
The mechanics of springback can be expressed through the following equation, which describes the relationship between the loaded and unloaded shapes:
[ U_u = U_f – U_e ]
where:
- ( U_u ): Unloaded part shape
- ( U_f ): Fully loaded part shape (replica of the mandrel)
- ( U_e ): Elastic recovery
Recent studies suggest that unloading may exhibit non-linear behavior, introducing a small additional term, ( U_p ), representing non-linear elastic recovery. However, due to its minor contribution, ( U_p ) is often assumed to be zero for simplicity in most models.
Stress and Strain Distribution
In metal spinning, the deformation zone experiences a complex interplay of tensile, compressive, and shear stresses. The material undergoes localized bending, stretching, and thinning as the roller moves across the blank. The stress state varies through the thickness of the sheet, with tensile stresses on the outer surface and compressive stresses on the inner surface near the mandrel. Upon unloading, the redistribution of these residual stresses drives springback.
The strain history is equally critical, as metal spinning involves incremental deformation over multiple roller passes. The cumulative plastic strain, combined with elastic strain, influences the magnitude of springback. For instance, materials with higher yield strengths, such as advanced high-strength steels (AHSS), exhibit greater springback due to their increased elastic recovery.
Types of Metal Spinning Processes
Metal spinning encompasses several variants, each with distinct implications for springback:
- Conventional Spinning: Involves forming a flat blank into a conical or curved shape without significant thickness reduction. Springback is influenced by bending and stretching.
- Shear Spinning: Applies significant thickness reduction, following the sine law, leading to higher residual stresses and pronounced springback.
- Flow Forming: A specialized process for producing cylindrical components with controlled wall thickness, where springback is affected by axial and radial stresses.
Each process introduces unique stress and strain distributions, necessitating tailored springback control strategies.
Factors Influencing Springback
Material Properties
Material properties play a pivotal role in determining springback behavior. Key factors include:
- Young’s Modulus: A lower Young’s modulus increases springback due to greater elastic recovery. For example, aluminum alloys (Young’s modulus ~70 GPa) exhibit more springback than steels (~200 GPa).
- Yield Strength: Higher yield strength, as in AHSS, results in greater springback due to increased residual stresses.
- Strain Hardening Exponent: A lower strain hardening exponent increases springback by reducing plastic deformation relative to elastic recovery.
- Anisotropy: Rolling-induced anisotropy causes non-uniform deformation, affecting springback in different directions.
Process Parameters
Process parameters significantly influence springback in metal spinning:
- Roller Feed Rate: Higher feed rates increase springback by inducing greater residual stresses due to rapid deformation.
- Spindle Speed: Faster spindle speeds can reduce springback by promoting uniform deformation, though excessive speeds may cause material heating and altered properties.
- Roller Path and Geometry: Complex roller paths or smaller roller radii increase localized stresses, amplifying springback.
- Mandrel Design: The mandrel’s shape and surface finish affect contact conditions and stress distribution.
- Blank Thickness: Thicker blanks exhibit less springback due to lower elastic recovery relative to plastic deformation.
Environmental Factors
Temperature and lubrication also influence springback:
- Forming Temperature: Elevated temperatures reduce springback by lowering yield strength and enhancing plastic deformation, as observed in warm spinning of magnesium alloys.
- Friction: Higher friction between the blank and mandrel increases springback by restricting material flow, while optimized lubrication can mitigate this effect.
Traditional Springback Control Methods
Tooling Design Adjustments
One of the earliest approaches to controlling springback involves modifying the tooling geometry to compensate for anticipated elastic recovery. In metal spinning, this includes:
- Overbending: Designing the mandrel to slightly exaggerate the desired shape, allowing the part to spring back to the target geometry.
- Multi-Pass Strategies: Using multiple roller passes with incremental deformation to reduce residual stresses and control springback.
These methods rely heavily on trial-and-error, which is time-consuming and less effective for complex geometries or new materials.
Mechanical Restraining Techniques
Mechanical methods aim to increase tensile stresses during forming to minimize springback:
- Blank Holder Force (BHF): Applying a controlled force on the blank edge increases stretching, reducing residual stresses. Studies show that higher BHF can decrease springback by up to 20% in conventional spinning.
- Drawbeads: Used to control material flow, drawbeads enhance stretching and reduce springback, particularly in shear spinning.
Empirical Models
Empirical equations, derived from experimental data, have been developed to predict springback for specific materials and processes. For example, Liu’s double-bend technique for U-channel forming has been adapted for spinning, using empirical correlations to adjust roller paths. However, these models are limited by their dependence on specific conditions and lack of generalizability.
Advanced Springback Control Methods
Finite Element Analysis (FEA)
Finite Element Analysis has revolutionized springback prediction and control by simulating the forming process and unloading phase. FEA models incorporate:
- Material Models: Anisotropic yield criteria (e.g., Hill’48, Barlat-89) and hardening laws (e.g., isotropic, kinematic) to capture complex material behavior.
- Process Parameters: Roller paths, feed rates, and friction conditions are modeled to optimize forming strategies.
- Springback Simulation: Explicit solvers simulate the forming phase, while implicit solvers analyze unloading to predict springback accurately.
Recent advancements include the integration of variable Young’s modulus and non-linear unloading behavior, improving prediction accuracy for AHSS and aluminum alloys. For instance, a study on shear spinning of DP780 steel using FEA reported a 95% correlation with experimental results.
Real-Time Control Systems
Real-time monitoring and control systems enhance springback management by adjusting process parameters during forming:
- Sensors: Linear displacement sensors and pressure sensors measure punch position and force, providing data on springback in real time.
- Closed-Loop Control: Feedback from sensors adjusts roller feed rates or BHF dynamically, minimizing deviations. A hydraulic press equipped with a 1 μm resolution optical scale achieved a 10% reduction in springback for aluminum alloys.
Laser-Assisted Spinning
Laser-assisted spinning uses localized heating to reduce springback:
- Mechanism: A high-power diode laser heats the deformation zone, lowering yield strength and enhancing plastic deformation.
- Results: Experimental studies on AA6082 aluminum alloy showed a 30% reduction in springback with laser post-treatment, attributed to stress relaxation.
Viscous Pressure Forming (VPF)
VPF employs a viscous medium to apply non-uniform pressure, reducing springback:
- Principle: The viscous medium increases tensile stresses and reduces stress gradients, minimizing elastic recovery.
- Application: Simulations of VPF in axisymmetric bulging showed a 15% reduction in springback compared to conventional spinning, validated by digital image correlation (DIC) experiments.
Optimization Algorithms
Optimization techniques, such as response surface methodology (RSM) and genetic algorithms, are used to minimize springback:
- RSM: Models the relationship between process parameters (e.g., feed rate, BHF) and springback, enabling optimal parameter selection.
- Multi-objective Genetic Algorithms: Simultaneously minimize springback and thickness variation, achieving up to 25% improvement in dimensional accuracy for complex parts.
Comparison of Control Methods
The following tables compare recent springback control methods in metal spinning, summarizing their mechanisms, advantages, limitations, and performance based on experimental and numerical studies.
Table 1: Comparison of Springback Control Methods
Method | Mechanism | Advantages | Limitations | Springback Reduction |
---|---|---|---|---|
Tooling Design | Overbending, multi-pass strategies | Simple, cost-effective for simple geometries | Trial-and-error, limited for complex parts | 5–15% |
Mechanical Restraining | Increased BHF, drawbeads | Effective for high-strength materials | Requires precise force calibration | 10–20% |
Empirical Models | Data-driven predictions | Quick for specific conditions | Lack of generalizability | 5–10% |
Finite Element Analysis | Numerical simulation of forming and unloading | High accuracy, versatile for complex geometries | Computationally intensive, requires expertise | 20–30% |
Real-Time Control | Sensor-based feedback and dynamic adjustments | Adapts to material variations | High setup costs, complex integration | 10–15% |
Laser-Assisted Spinning | Localized heating to reduce yield strength | Significant springback reduction, suitable for aluminum alloys | Limited to heat-tolerant materials, high energy costs | 25–30% |
Viscous Pressure Forming | Non-uniform pressure to reduce stress gradients | Effective for complex surfaces | Limited research, requires specialized equipment | 15–20% |
Optimization Algorithms | Parameter optimization using RSM or genetic algorithms | Balances multiple objectives, high precision | Requires extensive data, complex implementation | 20–25% |
Table 2: Experimental Results for Springback Control
Study | Material | Process | Control Method | Springback Rate (%) | Reduction Achieved (%) | Source |
---|---|---|---|---|---|---|
Shear Spinning of DP780 | DP780 Steel | Shear Spinning | FEA with Barlat-89 | 8–12 | 25 | |
Conventional Spinning | AA6082 Aluminum | Conventional Spinning | Laser-Assisted | 5–10 | 30 | |
Axisymmetric Bulging | Aluminum Alloy | VPF | Viscous Medium | 6–15 | 15 | |
Four-Axis Roll Bending | Aluminum Alloy | Roll Bending | RSM Optimization | 5–15 | 20 | |
Real-Time Control | HSLA360 Steel | Conventional Spinning | Sensor-Based Control | 7–13 | 12 |
Table 3: Numerical vs. Experimental Correlation
Method | Material | Correlation (%) | Key Parameters Modeled | Source |
---|---|---|---|---|
FEA | DP780 Steel | 95 | Anisotropy, variable Young’s modulus | |
FEA | AA5083 Aluminum | 92 | Kinematic hardening, roller path | |
VPF Simulation | Aluminum Alloy | 90 | Viscous pressure, stress gradients | |
RSM Optimization | Aluminum Alloy | 88 | Feed rate, BHF, roller speed | |
Neural Network | HSLA360 Steel | 85 | Hole geometry, die radius, pad force |
Emerging Trends and Future Directions
Machine Learning and Artificial Intelligence
Machine learning (ML) and artificial intelligence (AI) are transforming springback control by enabling predictive modeling and real-time optimization:
- Neural Networks: Trained on experimental and FEA data, neural networks predict springback for complex geometries, achieving up to 85% accuracy for perforated components.
- Reinforcement Learning: Adjusts process parameters dynamically, optimizing roller paths and feed rates to minimize springback in real time.
Advanced Material Models
Developing accurate material models is critical for improving springback predictions:
- Non-Linear Unloading Models: Account for variable Young’s modulus and non-linear elastic recovery, enhancing FEA accuracy.
- Microstructure-Based Models: Incorporate grain size, texture, and residual stress evolution to predict springback in novel alloys.
Hybrid Forming Processes
Hybrid processes, combining spinning with other techniques, offer new avenues for springback control:
- Incremental Forming with Spinning: Combines incremental sheet forming with spinning to reduce residual stresses.
- Electromagnetic-Assisted Spinning: Uses electromagnetic pulses to induce high-rate deformation, minimizing springback in conductive materials.
Sustainable Manufacturing
Sustainability considerations are driving innovations in springback control:
- Energy-Efficient Processes: Laser-assisted and VPF methods are being optimized to reduce energy consumption while maintaining springback control.
- Recyclable Materials: Research focuses on controlling springback in recycled aluminum and magnesium alloys, supporting circular manufacturing.
Challenges and Limitations
Despite advancements, several challenges persist:
- Computational Complexity: FEA and optimization algorithms require significant computational resources, limiting their adoption in small-scale industries.
- Material Variability: Variations in material properties, such as batch-to-batch differences, complicate springback predictions.
- Process Scalability: Real-time control and hybrid processes are challenging to scale for high-volume production.
- Knowledge Gaps: The evolution of microstructure, residual stresses, and failure mechanisms in spinning remains poorly understood, hindering predictive accuracy.
Conclusion
The control of springback in metal spinning is a multifaceted challenge that requires a deep understanding of material behavior, process dynamics, and advanced technologies. Traditional methods, such as tooling design and mechanical restraining, have been largely supplemented by sophisticated approaches like FEA, real-time control, laser-assisted spinning, and optimization algorithms. These methods, supported by experimental and numerical studies, have achieved significant reductions in springback, enhancing the dimensional accuracy of spun components.
Tables comparing control methods, experimental results, and numerical correlations highlight the strengths and limitations of each approach, guiding practitioners in selecting appropriate strategies. Emerging trends, including machine learning, advanced material models, and hybrid processes, promise further improvements, while sustainability considerations underscore the need for energy-efficient solutions.
As metal spinning continues to evolve, addressing challenges such as computational complexity, material variability, and knowledge gaps will be critical. By integrating theoretical insights, experimental validation, and technological innovations, the industry can achieve precise control over springback, ensuring high-quality components for demanding applications.
Maximize Tooling and CNC Metal Spinning Capabilities.
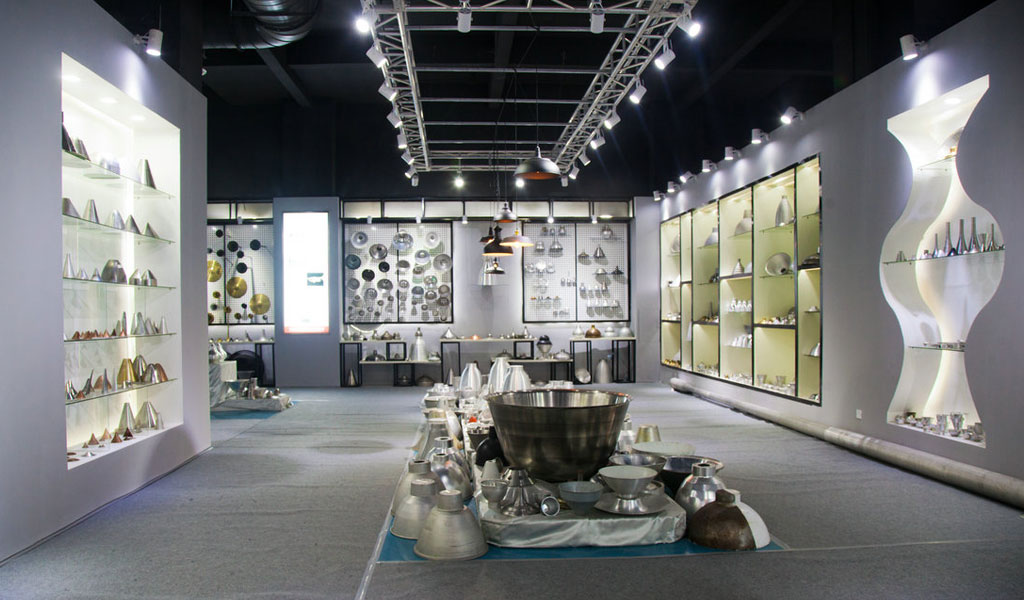
At BE-CU China Metal Spinning company, we make the most of our equipment while monitoring signs of excess wear and stress. In addition, we look into newer, modern equipment and invest in those that can support or increase our manufacturing capabilities. Our team is very mindful of our machines and tools, so we also routinely maintain them to ensure they don’t negatively impact your part’s quality and productivity.
Talk to us today about making a rapid prototype with our CNC metal spinning service. Get a direct quote by chatting with us here or request a free project review.
BE-CU China CNC Metal Spinning service include : CNC Metal Spinning,Metal Spinning Die,Laser Cutting, Tank Heads Spinning,Metal Hemispheres Spinning,Metal Cones Spinning,Metal Dish-Shaped Spinning,Metal Trumpet Spinning,Metal Venturi Spinning,Aluminum Spinning Products,Stainless Steel Spinning Products,Copper Spinning Products,Brass Spinning Products,Steel Spinning Product,Metal Spinnin LED Reflector,Metal Spinning Pressure Vessel,